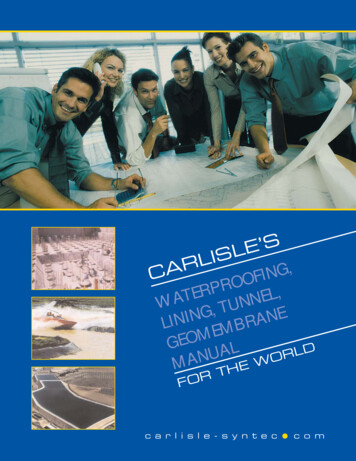
Transcription
’SELSILR,AGNCIOOFRPR,ELTEANW G, TUN ELININMEMBRANGEO UALLDRMANR THE WOFOc a r l i s l e - s y n t e c c o m
Carlisle InternationalOperations HeadquartersTheCarlisleStoryFor more than 40 years, Carlisle hasled the single-ply industry in productinnovation, customer enthusiasm andsystem integrity.1960s1970s1980sUSA: 717.245.7000fax: 717.245.7115email: 45.7000 x 7016fax 717.245.7115email: thomas@syntec.carlisle.comBeijing86.10.6796.6326 x 611fax: 86.10.6796.5004email: billqiu@carlisle.com.cnEurope32.2.732.2420fax: 32.2.733.2384email: jm.petit@skynet.beMiddle East961.1.353.171fax: 961.1.738.731email: : 7.095.200.4498email: krovtex@awax.ru1990s2000s
temssytSgnnikneaTmtdetnsunyoSrgtorneedC n I Un r Containm fing Secti IIInoCnoniositorcEeSIVnoitSec
IMETnSYoSiGtNIcKNSe ROUND TAGREDUN
Table of ContentsAugust 2002PagePart I General1.011.021.031.041.051.06Description .3Quality Assurance .3Submittals.4Product Delivery, Storage and Handling.4Job Conditions.4Warranty.5Part II Products2.012.022.032.042.052.06General .5Membrane.5Flashing .8Cleaners, Primers, Adhesives and Sealants .8Fastening Components .9Other Products.9Part III eneral .10Substrate Preparation.10Application of Liquid Waterproofing Membrane (Where Applicable).10Application of Separation Layer .11Application of Sure-Seal 1.5 mm Thick Non-Reinforced EPDM Membrane.11Application of FleeceBACK AFX Membrane (Optional).12EPDM Membrane Splicing .12Membrane Flashing .13Flashing Terminations .14Application of Protection Layer .14600427 – Underground Tanking – 8/2002
August 2002This specification outlines Carlisle's Sure-Seal Underground Tanking System requirements and is intended for use as a guidelinefor architects/engineers when specifying an underground/tanking waterproofing assembly. While the specification containsspecific installation details pertaining to various methods of membrane termination, contractors may reference other Carlisletechnical publications for in-depth application procedures. Additional information pertaining to field splicing, membrane bondingand flashing of various penetrations can be found in the “Application” Section of the Carlisle Sure-Seal Adhered Roofing SystemSpecification.PART IGENERAL1.01 DESCRIPTIONThe Sure-Seal Underground Tanking System incorporates 1.5 mm (.060 inch) thick Sure-Seal, black, non-reinforced or reinforcedEPDM membrane. The membrane is loose laid over a geotextile separator sheet on the horizontal grade. On the vertical gradeand over the geotextile separator sheet, the membrane can be mechanically fastened to a peripheral wall or directly adhered. Insome applications, FleeceBACK AFX membrane can be installed horizontally and vertically in conjunction with CCW 500 HotRubberized Asphalt or CCW 525 Cold Applied Liquid Waterproofing Membrane. (As an option the Sure-Seal EPDM membranecan be installed on top of the CCW membranes).All membrane splices shall be a minimum of 150 mm (6 inches) wide and assembled with Sure-Seal EP-95 Splicing Cement, InSeam Sealant and Lap Sealant. As an option, Sure-Seal Pressure-Sensitive Flashing (150 mm in width) can be used as anoverlayment to membrane splices.1.02 QUALITY ASSURANCEA. The Sure-Seal 1.5 mm (.060”) thick, non-reinforced EPDM membrane meets ASTM D6134-97, Standard Specification forVulcanized Rubber Sheets Used in Waterproofing Systems.Tensile StrengthElongation, UltimateTensile SetTear ResistanceBrittleness TemperatureLinear Dimensional ChangeWater AbsorptionFactory Seam StrengthWater Vapor PermeanceHardness Durometer AResistance to Soil BurialResistance to Heat AgingTest Resistance to PunctureASTM D412, Die CASTM D412, Die CASTM D412, Method A, Die C, % ElongationASTM D624, Die CASTM D746ASTM D1204, 166 h @ 240º F 4º FASTM D471, @ 70º C 2º C (158º F 4º F) for 166 hASTM D816, Modified Method B, 1” wide, 2”/min.ASTM E96, Procedure B W relative humidity of 45% @ 70º F 4º FASTM D2240ASTM D3083ASTM D573, Properties after 166 h @ 240º F 4º FASTM E154Refer to the physical property chart included in the “Product Section” for actual values achieved.B. This Underground Tanking System must be installed by an Authorized Applicator and in compliance with Carlisle’sinstallation details and project specification as approved by Carlisle. Deviations from Carlisle's details or approvedspecification shall be secured in writing prior to commencement of workC. Prior to installation, project shop drawings may be submitted to the manufacturer for review and approval. Copies of theapproved shop drawing should be made available to the project architect/engineer upon request.D. Comply with applicable regulatory requirements and applicable codes, ordinances, regulations and laws.600427 – Underground Tanking – 8/20023
E. On-site technical assistance is available for a charge. Projects where technical assistance is required must have amanufacturer’s approved drawing.1.03SUBMITTALSA. To ensure compliance with the applicable design criteria, project drawings, specification and pertinent details may besubmitted for Carlisle’s review.B. Requests for certification and/or formal drawing approval must be accompanied by a copy of the project specification anddetails. Shop drawings of maximum size 43 cm x 56 cm (17” x 22”) are preferred.C. Substitution of a non-Carlisle supplied product is permitted upon review and approval. Samples of the product along withtechnical literature may be forwarded to Carlisle for consideration.1.04PRODUCT DELIVERY, STORAGE AND HANDLINGA. Deliver materials to the job site in the original, unopened containers labeled with the manufacturer's name, brand name andinstallation instructions.B. Job site storage temperatures in excess of 32 C (90 F) may affect shelf life of curable materials (i.e., adhesive, sealants andcleaners).C. When sealants or cleaners are exposed to lower temperatures, restore to minimum 16 C (60 F) before use.1.05JOB CONDITIONSA. The EPDM membrane resists a wide variety of chemicals. Depending upon level of concentration and temperature, themembrane performance will vary. The chemical resistance chart of Sure-Seal EPDM shows compatibility of the membranewith various chemicals that normally exist in the soil. Should there be severe soil conditions not shown in the chart, a soil testshall be reviewed by Carlisle for compatibility.B. Comply with applicable codes and regulations pertaining to the operation and storage of heavy equipment.C. Coordination between various trades is essential to avoid unnecessary traffic over sections of already installed membrane toprevent damage to the waterproofing membrane.D. Do not install membrane onto low melting point asphalt (ASTM D 312 Type I and II) with a softening point below 85 C(185 F).E. Do not allow waste products (i.e., petroleum, grease, oil, solvents, vegetable or mineral oil, animal fat) or direct steam ventingto come in contact with the waterproofing membrane.F.Do not expose membrane and accessories to constant temperatures in excess of 82 C (180 F).G. Prior to the use of any product, consult the Material Safety Data Sheet and Technical Data Bulletin for cautions and warnings.Store adhesives, sealants and cleaners away from all sources of heat, flame or sparks. Do not use in confined or unventilatedareas.H. Cold temperatures will not restrict installation of the Sure-Seal Underground Tanking System. Follow specified precautionsfor storage of materials. Expose only enough cements/adhesives to be used within a 4 hour period.I.Splicing and bonding surfaces should be dry and clean.J.Substrate shall be free of ponded water, ice or snow.K. Coordinate waterproofing work with other trades. The applicator shall have sole right of access to the specified areas for thetime needed to complete the application and allow the membrane to cure adequately.600427 – Underground Tanking – 8/20024
L. Maintain work area neat and orderly condition, removing empty containers, rags and debris daily from the site.1.06WARRANTYA 20 year Membrane Material Warranty is available for a charge. The Material Warranty will cover normal deterioration and ispro-rated.PART IIPRODUCTS2.01GENERALThe components of this Underground Tanking System are to be products of Carlisle or accepted by Carlisle as compatible. Theinstallation, performance or integrity of products by others, when selected by the specifier and accepted as compatible byCarlisle, is not the responsibility of Carlisle.2.02MEMBRANEA. Sure-Seal (black) 1.5 mm (.060”) thick non-reinforced EPDM (Ethylene, Propylene, Diene Terpolymer) membrane;maximum 15.2 m (50') wide, maximum 30.5 m (100') long which meets ASTM D6134-97. Sure-Seal 1.1 mm (.045”) thicknon-reinforced membrane is also available in 61 m (200’) lengths.060" THICK NON-REINFORCED EPDM MEMBRANEPhysical PropertyTolerance on Nominal Thickness, %Tensile Strength, min, psi (MPa)Test MethodASTM D 412ASTM D 412SPEC. (Pass) 101305 (9)Typical 101630 (11.2)Elongation, Ultimate, min, %Tear Resistance, min, lbf/in (kN/m)ASTM D 412ASTM D 624(Die C)ModifiedASTM D 816ASTM D 573350520175 (30.6)230 (40.3)MembraneRuptureMembraneRuptureASTM D 412ASTM D 412ASTM D 624ASTM D 12041205 (8.3)225150 (26.3) 1.01500 (10.3)310215 (37.6)-0.4ASTM D 1149No CracksNo CracksASTM D 746-75 (-59)-85 (-65)ASTM D 471 4.0 2.0ASTM E 96(Proc. B or BW)0.1.05ASTM D G-26No CracksNo CrazingNo CracksNo CrazingFactory Seam Strength, min.Resistance to Heat Aging*Properties after 4 weeks @ 240 F (116 C)Tensile Strength, min, psi (MPa)Elongation, Ultimate, min, %Tear Resistance, min, lbf/in (kN/m)Linear Dimensional Change, max, %Ozone Resistance*Condition after exposure to 100 pphmOzone in air for 168 hours @ 104 F (40 C)Specimen is at 50% strainBrittleness Temp., max, deg. F (deg. C)*Resistance to Water Absorption*After 7 days immersion @ 158 F (70 C)Change in mass, max, %Water Vapor Permeance*max, permResistance to Outdoor (Ultraviolet) Weathering*Xenon-Arc, 7560 kJ/m2 total radiant exposure at .70 W/mirradiance, 176 F (80º C) black panel temp.*Not a Quality Control Test due to the time required for the test or the complexity of the test. However, all tests are run on a statistical basis toensure overall long-term performance of the sheeting.600427 – Underground Tanking – 8/20025
B. Sure-Seal (black) 1.5 mm (.060”) thick reinforced EPDM (Ethylene, Propylene, Diene Terpolymer) membrane;maximum 3.1 m (10') wide, maximum 30.5 m (100') long that meets ASTM D4637-96.060" THICK REINFORCED EPDM MEMBRANEPhysical PropertyTolerance on Nominal Thickness, %Thickness Over Scrim, min, in. (mm)Breaking Strength, min, lbf (N)Elongation, Ultimate, min, %Tear Strength, min, lbf(N)Test MethodASTM D 751ASTM D 4637AnnexASTM D 751Grab MethodASTM D 751Grab MethodASTM D 751B Tongue TearASTM D 2137ASTM D 573SPEC.(Pass) 10.015 (.381)90 (400)Typical 10.045"-.016 (.406).060"-.020 (.508)180 (800)250 **500 **10 (45)30 (132)Brittleness point, max, deg. F (deg. C) *-49 (-45)-75 (-59)Resistance to Heat Aging *Properties after 4 weeks @ 240 FASTM D 75180 (355)175 (780)Breaking Strength, min, lbf (N)ASTM D 751200 **250 **Elon
ASTM D 412 ASTM D 624 ASTM D 1204 1205 (8.3) 225 150 (26.3) 1.0 1500 (10.3) 310 215 (37.6) -0.4 Ozone Resistance* Condition after exposure to 100 pphm Ozone in air for 168 hours @ 104 F (40 C) Specimen is at 50% strain ASTM D 1149 No Cracks No Cracks Brittleness Temp., max, deg. F (deg. C)* ASTM D 746 -75 (-59) -85 (-65) Resistance to Water Absorption* After 7 days immersion @ 158 F .