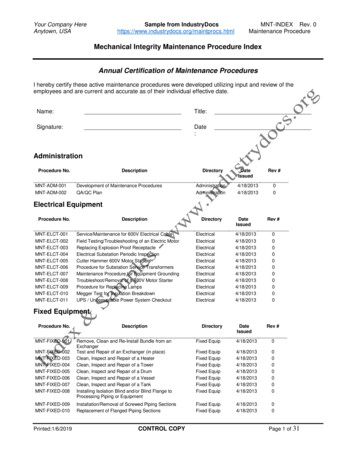
Transcription
Your Company HereAnytown, USASample from s.htmlMNT-INDEX Rev. 0Maintenance ProcedureMechanical Integrity Maintenance Procedure IndexAnnual Certification of Maintenance ProceduresI hereby certify these active maintenance procedures were developed utilizing input and review of theemployees and are current and accurate as of their individual effective dure No.MNT-ADM-001MNT-ADM-002DescriptionDevelopment of Maintenance ProceduresQA/QC d4/18/20134/18/2013Rev #00Electrical EquipmentProcedure ice/Maintenance for 600V Electrical CableField Testing/Troubleshooting of an Electric MotorReplacing Explosion Proof ReceptacleElectrical Substation Periodic InspectionCutler Hammer 600V Motor StartersProcedure for Substation Service TransformersMaintenance Procedure for Equipment GroundingTroubleshoot/Removal of a 480V Motor StarterProcedure for Replacing LampsMegger Test for Insulation BreakdownUPS / Uniterruptable Power System 4/18/20134/18/20134/18/20134/18/2013Rev #00000000000Fixed EquipmentProcedure escriptionDirectoryDateIssuedRev #Remove, Clean and Re-Install Bundle from anExchangerTest and Repair of an Exchanger (in place)Clean, Inspect and Repair of a HeaterClean, Inspect and Repair of a TowerClean, Inspect and Repair of a DrumClean, Inspect and Repair of a VesselClean, Inspect and Repair of a TankInstalling Isolation Blind and/or Blind Flange toProcessing Piping or EquipmentFixed Equip4/18/20130Fixed EquipFixed EquipFixed EquipFixed EquipFixed EquipFixed EquipFixed 4/18/20134/18/20130000000Installation/Removal of Screwed Piping SectionsReplacement of Flanged Piping SectionsFixed EquipFixed Equip4/18/20134/18/201300CONTROL COPYPage 1 of 31
Your Company HereAnytown, USASample from s.htmlMNT-INDEX Rev. 0Maintenance e a PlugReplacement of a Screwed ValveReplacement of a Flanged ValveRepack a ValveRepair or Replace Steam Traps“Hot Bolting” of a FlangeFixed EquipFixed EquipFixed EquipFixed EquipFixed EquipFixed 4/18/2013000000MNT-FIXED-017MNT-FIXED-018Fixed EquipFixed Equip4/18/20134/18/201300MNT-FIXED-019Hydrostatic Pressure Test for Shop Fabricated PipeReplacement of Butt or Socket Weld Piping Sectionsand Associated ComponentsWelding on Towers/Vessels or ExchangersFixed Equip4/18/20130MNT-FIXED-020Install, Remove, or Modify Structure and PlatformsFixed Equip4/18/20130InspectionProcedure escriptionInspection Procedure for Shell and Tube HeatExchangersInspection Procedure for Active Non-Trayed PressureVesselsInspection Procedure for Active Trayed PressureVesselsInspection Procedure for Air Cooled Heat ExchangersInspection Procedure for Leak TestingInspection Procedure for Fired HeatersInspection Procedure for Liquid Penetrant ExaminationInspection Procedures for Pressure Relieving DevicesDirectoryDateIssuedRev 8/201300000InstrumentationProcedure 4DescriptionDirectoryDateIssuedRev #High Risk Equipment CalibrationAnalytical EquipmentTesting Alarm Devices & ShutdownsFunction Check/Removal/Installation of aHoneywell Smart Pressure TransmitterShop Checkout Procedure for theRosemount Model 1151 Pressure uments4/18/20130Shop Checkout Procedure for theRosemount Model 1151 Differential Pressure (D/P)TransmitterShop Checkout ProcedureMoore Industries MVX Millivolt 130MNT-INST-008Shop Checkout ProcedureAshcroft (Duragauge) Standard Pressure GaugeInstruments4/18/20130MNT-INST-009Functional Check of a Teledyne AnalyticalPortable Flue Gas Analyzer (Model 980)Instruments4/18/20130MNT-INST-010Shop Checkout Procedure for the Fisher PneumaticLevel Controller/Indicator Transmitters with Cage(External Float) or Cageless (Internal Float) DisplacerSensorsShop Checkout Procedure for the Fisher Type 546Electro-Pneumatic Transducer -INST-012Shop Transmitter Checkout Procedure for theHoneywell Smart TransmitterInstruments4/18/20130MNT-INST-013Shop Testing/Repair of Single and Double Ported, PlugType, & Diaphragm Actuated Control 6MNT-INST-007MNT-INST-011Printed:1/6/2019CONTROL COPYPage 2 of 31
Your Company HereAnytown, 7MNT-INST-018MNT-INST-019MNT-INST-020Sample from s.htmlFunction Check/Removal/Installation of aFlow Transmitter (Honeywell Smart)Function Check/Removal/Installation of a PressureTransmitter (Honeywell Smart)Function Check/Removal of a Cage TypeDisplacer Level TransmitterFunction Check/Removal of a Control ValveFunction Check of a Precision Continuous ViscometerReplacement of a Butterfly ValveInstallation/Removal/Function Check of a PressureSwitchMNT-INDEX Rev. 0Maintenance 130000Rotating EquipmentProcedure onShop Repairs to a Horizontal Barrel Centrifugal PumpRebuild & Certify Relief Valves Per State CodeShop Repairs to a Horizontal Split Case PumpShop Repairs to a Vertical In-Line PumpShop Repairs to a Vertical Sump PumpShop Repairs to a TurbineShop Repairs to a Reciprocating Chemical InjectionPumpShop Repairs to a GearboxShop Repairs to a Centrifugal CompressorShop Repairs to a MixerShop Repairs to a Fan or BlowerShop Repairs to a Gear PumpRemove, Repair, and Reinstall a Horizontal PumpRemove, Repair, and Reinstall a Reciprocating PumpRemove, Repair, and Reinstall a TurbineRemove and Reinstall an Electric MotorRemove, Repair, and Reinstall a FanRemove, Repair, Reinstallation of a GearboxReplacement of Valves on a Reciprocating CompressorRemove, Repair and Reinstall a Horizontal Split CasePump Motor DrivenRemove, Repair and Reinstall a Horizontal Gear PumpMotor DrivenRemove, Repair and Reinstall a Vertical Sump PumpMotor DrivenRemove, Repair and Reinstall a Vertical In-Line PumpMotor DrivenRemove, Repair and Reinstall a Reciprocating PumpMotor DrivenRemove, Repair and Reinstall a Horizontal Split CasePump Turbine DrivenRemove, Repair and Reinstall a Mixer on a TankRepack a Centrifugal PumpRepairs to API Separator (Skimmer)Remove, Repair and Reinstall a Vertical Water WellMotor DrivenRemoval, Repair, Install a Cooling Tower Fan and GearBoxTurbine Overspeed Test ProcedureCONTROL COPYDirectoryDateIssuedRev 0Machinists4/18/20130Page 3 of 31
Your Company HereAnytown, USASample from s.htmlMNT-INDEX Rev. 0Maintenance ProcedureRiggingProcedure suedRev #Choker, Wire Rope Sling, Metal Mesh Sling, SyntheticWebbing Slings, & Natural/ Synthetic Fiber RopeInspectionHand Operated, Electrical or Air-Powered Chain Hoists& Hook InspectionRigging4/18/20130Rigging4/18/20130Mobile Crane & Standing Wire Rope InspectionMobile Crane Lifting ProceduresTackle Blocks, Eye Bolts, & Shackles /18/2013000CONTROL COPYPage 4 of 31
Your Company HereAnytown, USASample from procs.htmlMNT-ADM-001 Rev. 0Administrative ProcedureDevelopment of Maintenance ProceduresAPPROVED: DATE APPROVED: DATE EFFECTIVE:Maintenance ManagerPURPOSEThis procedure defines the Y O U R C O M P A N Y N A M E H E R E Maintenanceprocedures. The process for procedure, development, review, approval, documentcontrol and formatting standards are described.REFERENCESDepartment of Labor (OSHA), 29 CFR part 1910.119, Process Safety Management ofHighly Hazardous Chemicals, Final Rule, February 24, 1992.American Petroleum institute, API Recommended Practice 750, "Management ofProcess Hazards", January 1990.DEFINITIONSAPPROVAL -- Authorization granted by the Maintenance Manager to issue a newprocedure or revision, delete an approved procedure, or implement a field change.Approval authority shall not be delegated, except in the absence of the MaintenanceManager.CONTROL COPY -- A control copy is the only version of a procedure which isconsidered up-to-date at all times. Working copies shall be reproduced from a controlcopy.DATE APPROVED -- The date a procedure is approved by the Maintenance Managerand becomes authorized for use. This means the content of the procedure issatisfactory and the procedure is to be implemented.DELETED PROCEDURE -- A procedure rescinded and not replaced by a later revision.The procedure's number will not be reused.EXPIRATION DATE -- The date or condition after which a TEMPORARYPROCEDURE will no longer be used.INTENT CHANGE -- A change to the content of a control copy which: Changes the purpose or outcomeCreates new process safety issuesChanges any operating parameter or limitCauses other Departments to perform tasks not previously required.NON-INTENT CHANGE -- A change to a procedure which does not change thepurpose, safety concerns, parameters, flow paths or the validity of any data taken.Such changes may include the following: Clearly identifiable typographical errors, misspelled words and correction topunctuationInadvertently omitted information or clearly erroneous dataReferences to other documents which must be corrected due to the referencedocument title, number, or revision number changingMAINTENANCE MANAGER -- The Manager who is responsible for the equipment oroperation will sponsor applicable procedures and has the approval authority.Printed:1/6/2019CONTROL COPYPage 5 of 31
Your Company HereAnytown, USASample from procs.htmlMNT-ADM-001 Rev. 0Administrative ProcedureMAINTENANCE PROCEDURE - identifies hazards associated with employees jobtask. Field procedures will contain information to assure that the employee can performthe job task in a safe manner. A Maintenance Procedure shall include, whereapplicable, specific instructions and values as needed to execute the job correctly, e.g.,manufacturer's "bolt torque" specifications.REVISION -- The process of incorporating approved changes into a control copy whichresults in a change in the procedure's revision number.TEMPORARY PROCEDURE -- A procedure intended for one use that has a finite life(that is, a specified effective date and expiration date or predefined condition.)USE OF SHALL, SHOULD AND MAY -- These words have definite meanings: SHALL denotes a requirementSHOULD denotes a recommendationMAY denotes permission (that is, neither a requirement nor a recommendation)WORKING COPY -- A procedure either under development or revision.PROCEDURE USAGEPROCEDURE AVAILABILITY -- Plant procedures shall be readily accessible to allworkers who perform Maintenance activities. The procedures shall be written toprovide clear instructions for safely performing work activities.USER RESPONSIBILITY -- Each worker is responsible for reviewing the proceduresfor their area of responsibility as often as necessary to ensure adherence to currentoperating and maintenance practices.MAINTENANCE PROCEDURESMaintenance Procedures will identify any specific hazards associated with the job, alongwith any exposure effects and references to Material Safety Data Sheets for treatmentrequired.Maintenance Procedures need to be specific to the type of equipment. Identical or verysimilar items of equipment in similar service need not have individualized procedures.Each procedure must clearly identify the equipment to which it applies.These procedures will contain specific job instructions on "how to do the job correctly".When tasks have to be done in a fixed, specific sequence and special instructions needto be followed, these will be included as part of the procedure.Maintenance Procedures will also identify any initial conditions (prerequisites) that mustbe satisfied or actions that should be performed prior to starting the procedure (i.e., Lockand Tag, obtain Work Permit, etc.).Procedures will reference other guidelines, such as ISA, NEC, ASME, or API, as theyapply to each individual procedure. Manufacturer's manuals and/or drawings will also bereferenced as applicable.PROCEDURE DEVELOPMENTThe need for new procedures or procedure revisions may be identified or initiated byanyone.Printed:1/6/2019CONTROL COPYPage 6 of 31
Your Company HereAnytown, USASample from procs.htmlMNT-ADM-001 Rev. 0Administrative ProcedureThe Maintenance Manager is responsible for arranging for procedure(s) be writtenaccording to the format and writing standards described in this document. Capitalprojects and other process engineering changes should automatically initiatedevelopment of procedures or revisions to procedures as part of the Management ofChange (MOC) process.REVIEW AND APPROVALPrior to approval, each new procedure or procedure revised for an intent change or dueto periodic review comments will be reviewed to ensure that it addresses the following: SafetyTechnical accuracyRegulatory requirementsSound operating and maintenance practicesQualityPROCEDURE CONTROLThe master document shall be titled as a “Control copy”. A Control copy is the onlyversion considered up-to-date at all times. All other copies of procedures are "ForInformation Only" and should be compared with the Control copy prior to use to ensurethat they are current and to include all field changes.WORKING COPIES – Procedures titled as “Working Copy” will not be considered ascurrent.NON-INTENT CHANGES - should be written in ink on a Controlled Copy, signed anddated by the person making the change and submitted for correction.PROCEDURE REVIEWProcedures will be reviewed as often as necessary to ensure that they reflect currentoperating practice, including changes that result from changes to process chemicals,technology, and equipment, and changes to facilities.The Maintenance Managers will certify annually that the procedures are current andaccurate. Each procedure's 12 month review cycle will restart immediately following theapproval of a revision to the procedure. Procedure revisions identified as a part of theMOC review of other process safety information changes must be reviewed andapproved in accordance with this procedure.When a procedure is formally revised the Maintenance Manager will ensure that theearlier versions are removed and the latest revision inserted in its place. Revisedprocedures will be published and distributed in their entirety.The Maintenance Managershall ensure all employees affected by the new or revised procedure will be informed ofor trained in the change prior to the effective date.Printed:1/6/2019CONTROL COPYPage 7 of 31
Your Company HereAnytown, USASample from procs.htmlMNT-ADM-001 Rev. 0Administrative ProcedureTEMPORARY PROCEDURESTemporary procedures are written for a temporary situation or condition. Eachtemporary procedure has a an effective date and an end date or when a predefinedcondition is satisfied. Temporary procedures will be centrally archived after theirexpiration date.Temporary procedures shall be marked "TEMPORARY" after the title. They willinclude an expiration date or terminating condition in the Purpose section. Temporaryprocedures may be hand written if the writing is clear and legible.PROCEDURE FORMATProcedure pages will include a header and footer containing the following information:PROCEDURE NUMBER -- An alphanumeric code consisting of:1. Procedure Type Indicator – e.g. MNT2. Craft prefix number - e.g. FIXED, INST3. Sequential number - e.g. 001, 0024. Revision Number - e.g. 0, 1 (The first revision is Rev. 1)PROCEDURE TITLE -- A summary of the major goal of the procedure, usually a majorjob or task description. For example: "Unit #1 Startup" or "Loading Product Tank Cars"APPROVED BY -- Signature of approval authority by the Maintenance Manager. Thisline appears on the top of the first page only.DATE -- Month and year when the current revision of the procedure was approved andpublished.PAGE NUMBER -- Each procedure begins on page one and is numbered consecutivelythrough the last page of the procedure. Each page shows the page number and thetotal number of pages in the procedure (including attachments). For example, the lastpage of a three-page procedure is Page 3 of 3.TABLES AND FIGURESTables, simple drawings, exploded drawings, figures, diagrams, and charts serve toclarify confusing or difficult ideas. Locate them close to the point in the procedurewhere they are referenced. If complicated drawings are necessary for understandingthe procedure they may be included as attachments. If this is not practical (as withvendor manuals or numerous detailed PFDs) the procedure user should be directed tothe appropriate document.PROCEDURE SECTIONMaintenance procedures contain the following sections, identified in the left margin ofeach procedure:1. PURPOSE -- A brief description of summary of the use and goal of the procedure.2. REFERENCES -- Documents that support the maintenance work being performed.In case of possible chemical exposure, include references to appropriate MSDS,using the actual chemical name(s).Printed:1/6/2019CONTROL COPYPage 8 of 31
Your Company HereAnytown, USASample from procs.htmlMNT-ADM-001 Rev. 0Administrative Procedure3. PRECAUTIONS -- A brief description of any dangerous conditions that exist orcould be encountered while performing the procedure as identified by a Job HazardAnalysis.4. SPECIAL TOOLS AND EQUIPMENT -- A list of equipment or materials unique tothe procedure or which should be in place before beginning the procedure. Thissection would not include normal Personal Protection Equipment (PPE) worn tomeet general plant safety requirements.5. PREREQUISITES -- Actions or conditions which shall be performed or verifiedbefore starting the procedure. The technician skill level that the work requires willbe stated here. Other job planning information is identified here as well as specialtraining and regulatory requirements.6. PROCEDURE -- The step-by-step instructions for achieving the purpose of theprocedure.Procedural steps will consist of an action and the object of the action. For example:Mechanic 1. VISUALLY INSPECT gasket seat for signs of rusting or pitting.2. WIPE the gasket seat area with a cloth soaked in machine oil.NOTES contain information that will help in the performance or understanding of aprocedural step. Notes will precede the procedural step to which they refer. It isadvisable to limit the use of "nice to know information" in notes as well as inprocedural steps. Notes do not normally contain actions. Notes will be designatedas shown below:CAUTIONS are placed before a step to identify potential or actual hazards thatcould injure personnel, damage equipment or reduce a component's mechanicalintegrity.END OF PROCEDUREThe centered word { END }, in bold type, shall appear after the last step or paragraph ofa procedure.ENDPrinted:1/6/2019CONTROL COPYPage 9 of 31
Your Company HereAnytown, USASample from procs.htmlMNT-ELCT-001 Rev. 0Maintenance ProcedureService/Maintenance Procedure for 600V Electrical CableAPPROVED: DATE APPROVED: DATE EFFECTIVE:Maintenance ManagerPURPOSEThis procedure describes the service and maintenance of 600V electrical cableThis procedure applies to all electrical personnel that perform or assist in thiswork. All Maintenance Electrical Personnel that perform or assist inaccomplishing this work will follow all procedures.REFERENCES SPECIALEQUIPMENTMinimum 5KV Megger with 20,000 Mohm scale.PREREQUISITEThis procedure requires qualified craftsmen.MATERIAL SAFETY DATA SHEETSSafe Work Permit ProcedureLock Out/ Tag Out ProcedureSafety Manual1. REVIEW this procedure with the electrical personnel to ENSURE all stepsand cautions are CLEAR and all hazards have been DEFINED.2. Electrical personnel shall VERIFY that all safety equipment in the substation is in good working order.3. If electrical lockout is required, REFER to Lock Out/ Tag Out Procedure.4. When involving electrical distribution, NOTIFY central control operatorsthat a power distribution system will be out of service, and what will beaffected.5. Refer to Electrical Switching Orders Procedure.PRECAUTIONPrinted: 1/6/2019Personnel will be exposed to low or high voltages. The following hazards areassociated with electrical energy and safety precautions must be exercised:1. Shock2. Arc (Flash)3. BlastExposure or contact with any of these hazards will result in burns, severeand/or possibly fatal injuries. Wear proper protective gear, barricade area to betested.CONTROL COPYPage 10 of 31
Your Company HereAnytown, USAPROCEDURESample from procs.htmlMNT-ELCT-001 Rev. 0Maintenance ProcedureSERVICE/MAINTENANCE FOR 600V POWER CABLES1. The circuit must be DE-ENERGIZED and ISOLATED before beginningwork.2. Visually inspect grounding, cable support and termination.3. Perform Testing Procedure for 600V cable, per industry practices.4. TEST leads must be in good shape, CLEAN and having no broken orcracked insulation.CAUTIONDO NOT TOUCH CABLE DURING TEST.CAUTION5. DOCUMENT all test results and work done in proper files. All test resultsare to be reviewed and kept by the electrical supervisor.DURATIONInterval for testing and maintenance: Testing and maintenance as outlinedabove shall be done on the cable covered by this procedure at an interval NOTTO EXCEED 5 YEARS. The electrical supervisor or his designee willimplement the timing based on schedules and maintenance work.ENDPrinted: 1/6/2019CONTROL COPYPage 11 of 31
Your Company HereAnytown, USASample from procs.htmlMNT-ELCT-001Rev. 0Maintenance Procedure600V CABLE TESTCABLE SERVICELOCATION(Project Name)(Area in Plant)DATE OF TESTWEATHER COND.AMBIENT TEMP.FREE AIR PROBE(Degree F)TEST RESULTSPERSON(S) PERFORMINGTEST & COMPANY AFFILIATION123Cable TypeDescription(XHHW orApprox.CircuitRHH/RHW/USELengthNo., Ect.and Size)(Ft.)Printed: 1/6/201945Temperature Megohms-1000 Ft.Megohms Megohms-1000 Ft(For Run)(2)x(1)/1000 Ft6Megohms-1000 Ft.CorrectionCorrected(MinimumFactorto 60 deg. FAcceptable)Comments(From Table)(3)x(4)(From Table)Acceptable(?)CONTROL COPYPage 12 of 31
Your Company HereAnytown, USASample from procs.htmlMNT-FIXED-001 Rev. 0Maintenance ProcedureRemove, Clean, and Re-Install Bundle from an ExchangerAPPROVED: DATE APPROVED: DATE EFFECTIVE:Maintenance ManagerPURPOSEThis Procedure describes the steps required to remove the tube bundle from anexchanger. This procedure applies to all Maintenance personnel that performor assist in this work.REFERENCES SPECIALEQUIPMENTRefer to proper MATERIAL SAFETY DATA SHEETSPREREQUISITEThis procedure requires qualified craftsmen.MATERIAL SAFETY DATA SHEETSHazardous Energy Control ProcedureSafe Work Permit ProcedureLock Out/ Tag Out ProcedureLifting ProcedureSafe Work Program for Handling Inorganic Metals in Process ScalesWelding on Towers/Vessels or Exchangers Procedure1. REVIEW this procedure with the Operations and Maintenance crews toENSURE all steps and cautions are clear and all hazards have beenDEFINED. Match the proper MATERIAL SAFETY DATA SHEETS with theequipment service.2. Use special precautions defined on MATERIAL SAFETY DATA SHEETSand verify operation of all safety showers and eyewashes near the workarea to ENSURE they are in good working order.3. Field VERIFY with Operations that the equipment has been BLOCKED IN,DE PRESSURIZED, and BLED DOWN. VERIFY that block valves areHOLDING satisfactorily.4. INSTALL locks and tags where required per the Lock Out/ Tag OutProcedure.5. Maintenance personnel shall VERIFY with the unit operator that allapplicable equipment is LOCKED and TAGGED OUT and is NONOPERABLE (Lock, Tag, Test, Try).6. REVIEW and OBTAIN Work Permit at this time.PROCEDUREPrinted: 1/6/2019REMOVE, CLEAN, AND RE-INSTALL TUBE BUNDLE FROM ANEXCHANGER IN THE VACUUM-I UNIT.CONTROL COPYPage 13 of 31
Your Company HereAnytown, USASample from procs.htmlMNT-FIXED-001 Rev. 0Maintenance ProcedureCAUTION"First Flange Break" - Personnel must stand upwind of flange being brokento lessen exposure to hazard. Personnel shall loosen and remove boltson far side of flange first to lessen chances of exposure.CAUTION1. INSTALL blinds on the shell side inlet and outlet nozzles if required.2. REMOVE channel cover and channel head.3. INSTALL blind flanges on the tube side inlet and outlet piping if required.4. PULL bundle.5. Hydro-blasters to CLEAN tubes, bundle and heads if required.6. Inspection Department to INSPECT all parts.7. REPAIR as needed per Inspection Memo.8. RE-ASSEMBLE exchanger, except for channel cover.9. OBTAIN test pressures from Operations.10. HYDROTEST shell side and complete hydrotest forms. Cold gas oil mustbe used to test.11. RE-INSTALL channel cover, Hydrotest tubes, complete Hydrotest forms.Cold gas oil must be used to test.CAUTION"First Flange Break" - Personnel must stand upwind of flange being brokento lessen exposure to hazard. Personnel shall loosen and remove boltson far side of flange first to lessen chances of exposure.CAUTION12. REMOVE all blinds.13. NOTIFY Operations that work is complete.14. REMOVE all locks and tags.15. After system is back in service, Operations will SIGN OFF the WorkOrder/Work Permit as completed.* Note: During turnaround or complete unit shutdown with all isolation blinds inplace, water may be used to Hydrotest exchangers if there is sufficientsteam in the unit to effectively steam out exchangers after testing.END OF PROCEDUREPrinted: 1/6/2019CONTROL COPYPage 14 of 31
Your Company HereAnytown, USASample from procs.htmlMNT-INSP-001 Rev. 0Inspection ProcedureINSPECTION PROCEDURE FOR SHELL AND TUBE HEAT EXCHANGERSAPPROVED: DATE APPROVED: DATE EFFECTIVE:Technical Writer:Content Expert:PurposeEstablish inspection guidelines to ensure mechanical integrity and continuedreliable operation of shell and tube heat exchangers. This procedure applies tothe pressure containing parts of the exchanger alone with supporting structures.ReferencesMaterial Safety Data Sheets (MSDS) are electronically stored and can bereferred to in the MSDS program by equipment number, MSDS can also befound by searching by manufacturer, product name, or chemical. Theprocedure user is responsible for referring to the appropriate MSDS.Corporate Safety Procedures shall be referred to for all safety related issues.They are accessible electronically plant wide by going to the Health and SafetyServices tab on the Intranet. Personnel are responsible for referring lo theappropriate safety procedures.National Board Inspection Code ANSI-NB-23, Latest EditionAPl-510 Pressure Vessel Inspection Code: Maintenance Inspection, Rating,Repair, and Alteration; Latest EditionAmerican Society of Mechanical Engineers (ASME), Section VIII, Division 1American Society of Mechanical Engineers (ASME), Section IX, Latest EditionApplicable Local, Stale and Federal RegulationsApplicable Engineering Standards and Practices APIRP571 Conditions Causing Deterioration and FailureAPI RP572 Inspection of Pressure VesselsAPI RP750 Management of Process HazardsApplicable Maintenance Inspection ProceduresVendor Drawing for the vessel being inspected.Printed: 1/6/2019CONTROL COPYPage 15 of 31
Your Company HereAnytown, USASample from
Mechanical Integrity Maintenance Procedure Index Annual Certification of Maintenance Procedures I hereby certify these active maintenance procedures were developed utilizing input and review of the employees and are current and accurate as of their individual effective date.