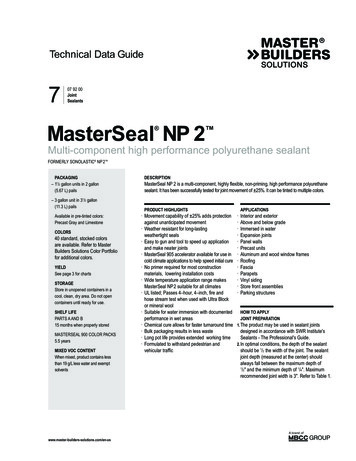
Transcription
Technical Data Guide707 92 00JointSealantsMasterSeal NP 2 Multi-component high performance polyurethane sealantFORMERLY SONOLASTIC NP 2 PACKAGING– 11/2 gallon units in 2 gallon(5.67 L) pails– 3 gallon unit in 31/2 gallon(11.3 L) pailsAvailable in pre-tinted colors:Precast Gray and LimestoneCOLORS40 standard, stocked colorsare available. Refer to MasterBuilders Solutions Color Portfoliofor additional colors.YIELDSee page 3 for chartsSTORAGEStore in unopened containers in acool, clean, dry area. Do not opencontainers until ready for use.SHELF LIFEPARTS A AND B15 months when properly storedMASTERSEAL 900 COLOR PACKS5.5 yearsMIXED VOC CONTENTWhen mixed, product contains lessthan 19 g/L less water and exemptsolventsDESCRIPTIONMasterSeal NP 2 is a multi-component, highly flexible, non-priming, high performance polyurethanesealant. It has been successfully tested for joint movement of 25%. It can be tinted to multiple colors.PRODUCT HIGHLIGHTS Movement capability of 25% adds protection against unanticipated movement Weather resistant for long-lasting weathertight seals Easy to gun and tool to speed up application and make neater jointsMasterSeal 905 accelerator available for use in cold climate applications to help speed initial cure No primer required for most construction materials, lowering installation costs Wide temperature application range makes MasterSeal NP 2 suitable for all climates UL listed; Passes 4–hour, 4–inch, fire andAPPLICATIONSInterior and exteriorAbove and below gradeImmersed in waterExpansion jointsPanel wallsPrecast unitsAluminum and wood window framesRoofingFasciaParapetsVinyl sidingStore front assembliesParking structureshose stream test when used with Ultra Blockor mineral woolSuitable for water immersion with documentedHOW TO APPLYperformance in wet areasJOINT PREPARATIONChemical cure allows for faster turnaround time 1. The product may be used in sealant jointsBulk packaging results in less wastedesigned in accordance with SWR Institute'sLong pot life provides extended working timeSealants - The Professional's Guide.Formulated to withstand pedestrian and2. In optimal conditions, the depth of the sealantvehicular trafficshould be 1/2 the width of the joint. The sealantjoint depth (measured at the center) shouldalways fall between the maximum depth of1/2" and the minimum depth of 1/4". Maximumrecommended joint width is 3". Refer to Table 1.A brand ofwww.master-builders-solutions.com/en-us
Technical Data GuideMasterSeal NP 2 Technical DataCompositionMasterSeal NP 2 is a multi-componentpolyurethane product.CompliancesASTM C 920, Type M, Grade NS, Class 25, use NT,T, A, M, O* and IFederal Specification TT-S-00227E, Type II, Class ACorps of Engineers CRD-C-506Canadian Standards Board CAN/CGSB-19.24-M90,Classification MCG-2-40-A-N, No. 81029CFI acceptedUnderwriters Laboratories Inc. classified(fire resistance only).* Refer to substrates in Where to Use.Test DataPROPERTYRESULTSTEST METHODMovement capability, % 25%ASTM C 719Tensile strength, psi (MPa)160 (1.1)ASTM D 412Ultimate elongation at break, %280ASTM D 412Stain and color changePasses(no visible stain)ASTM C 510Extrusion rate, sec,3 hrs after mixing6PassesASTM C 603Rheological (flow),at 120 F (49 C)NonsagASTM C 639Hardness, Shore AASTM C 661At standard conditions25After heat aging (max Shore A:50)22Typical PropertiesPROPERTYVALUETemperature range, F ( C)-40 to 180(-40 to 82)ShrinkageNoneTack-free time, hrs,(maximum 72 hrs) 48 hoursASTM C 679Bond durability*, %,on aluminum and concretePassesASTM C 719Weight loss, after heat aging, %4.7ASTM C 792Cracking and chalking,after heat agingNoneASTM C 792Artificial weathering,Xenon arc, 250 hoursPassesASTM C 793Artificial weathering,Xenon arc, 2,000 hoursNo surface crackingASTM G 26Adhesion in peel, on aluminumand concrete*, pli 10ASTM C 794Water immersion, 122 F (50 C)Passes 10 weeks withmovement cycleASTM C 1247*Primed for water immersion dictated by ASTM C 920. Concrete and aluminum primed with MasterSeal P 173; glass primedwith MasterSeal P 176Test results are typical values obtained under laboratory conditions. Reasonable variations can be expected.TABLE 1Joint Width and Sealant DepthJOINT WIDTH,IN (MM)1 4– 1 21 2– 3 43 4–1TABLE 2Working Time, hoursSEALANT DEPTHAT MIDPOINT, IN (MM)HIGHER TEMPERATURE95 F (35 C), 5 – 90% RHCOLDER TEMPERATURE40 F (4 C)(6–13)1 4No accelerator2–31–24–6(13–19)1 4– 3 8(6–10)1 accelerator1–2 12–33 8– 1 2(10–13)2 accelerators 1—1.5 – 2.5(19–25)1–3 (25–75)1 2(6)STANDARD CONDITIONS73 F (23 C) 50% RH(13)
Master Builders eldLINEAR FEET PER GALLON*JOINT DEPTH, JOINT WIDTH (INCHES)(INCHES) 3 81 21414 38 12 58 34 78 11 1 –––––––514438261912METERS PER LITERJOINT DEPTH, JOINT WIDTH –4.13.53.02.21.50.7(MM)3. In deep joints, the sealant depth must beWOODcontrolled by closed cell backer rod or softNew and weathered wood must be clean, drybacker rod. Where the joint depth does notand sound. Scrape away loose paint to barepermit the use of backer rod, a bond breakerwood.(polyethylene strip) must be used to preventAny coatings on wood must be tested tothree-point bonding.verify adhesion of sealant or to determine an4. To maintain the recommended sealant depth,appropriate primer.install backer rod by compressing and rollingMETALit into the joint channel without stretching itRemove scale, rust and loose coatings fromlengthwise. Closed cell backer rod should bemetal to expose a bright white surface. Any1about 8" (3 mm) larger in diameter than thecoatings on metal must be tested to verifywidth of the joint to allow for compression.adhesion of sealant or to determine anSoft backer rod should be approximately 25%appropriate primer.larger in diameter than the joint width. Thesealant does not adhere to it, and no separatePRIMINGbond breaker is required. Do not prime or1. MasterSeal NP 2 is considered a nonpuncture the backer rod.priming sealant, but special circumstancesor substrates may require a primer. It is theSURFACE PREPARATIONuser’s responsibility to check the adhesionSubstrates must be structurally sound, fullyof the cured sealant on typical test joints atcured, dry and clean. Substrates shouldthe project site before and during application.always be free of the following: dirt, looseRefer to product data sheet on MasterSealparticles, oil, grease, asphalt, tar, paint, wax,P 173 and MasterSeal P 176, and consultrust, waterproofing or curing and partingTechnical Service for additional information.compounds, membrane materials and sealant2. For immersion applications, MasterSeal P 173residue.must be used.CONCRETE, STONE, AND OTHER MASONRY3. Apply primer full strength with a brush or cleanClean by grinding, sandblasting or wirecloth. A light, uniform coating is sufficient forbrushing to expose a sound surface free ofmost surfaces. Porous surfaces require morecontamination and laitance.primer; however, do not over-apply.4. Allow primer to dry before applying MasterSealNP 2. Depending on temperature and humidity,primer will be tack-free in 15–20 minutes. Primingand sealing must be done on the same day.MIXING1. MasterSeal NP 2 is a multi-component systemwith a configuration of Part A, Part B and acolor pack.2. Transfer entire contents of Part B to Part Acontainer using a spatula or margin trowel.3. Part B must be mixed thoroughly with Part A.Before adding pigment, scrape sides of containerto ensure complete mixing of Parts A and B. Witha slow-speed drill and a sealant mixing paddle,mix 4–6 minutes. Keep the paddle blade belowthe surface of the sealant to avoid whipping airinto the sealant.4. Transfer the entire contents of one MasterSeal900 pigment can into the mixed Part A and B.Use a spatula or knife to remove all the pigmentfrom the container. Continue mixing with aslow-speed drill and slotted paddle until color isuniform. During the process, scrape the sidesand bottom of the mixing container severaltimes to obtain a complete mix.5. The pot life of mixed MasterSeal 905accelerator is influenced by temperature. SeeTable 2 for specific data. MasterSeal 905accelerator may be added to adjust the initialcure rate.
Technical Data GuideMasterSeal NP 2 APPLICATION1. Except when unusual job conditions dictatethe use of knife or spatula, apply MasterSealNP 2 by professional bulk gun loaded at thejobsite. Fill joints from the bottom up to theexterior face by holding a properly sizednozzle against the joint bottom.2. Dry tooling is recommended. Proper toolingresults in the correct bead shape, neat joints,and optimal adhesion.3. Best practices dictate that all caulking andsealing be done when temperatures are above40 F (4 C) to avoid application to moistureladen surfaces. Moisture on substrates willadversely affect adhesion.4. Application may proceed as low as 40 F(4 C) if there is certainty that substrates arecompletely dry, free of moisture and clean asdescribed under Surface Preparation.CURINGThe cure of MasterSeal NP 2 varies withtemperature and humidity. The followingtimes assume 75 F (24 C), 50% relativehumidity, and a joint 1/2" (13 mm) in widthby 1/4" (6 mm) in depth.– Skins: within 3–4 hours– Full cure: approximately 1 weekSee Table 2 for use of MasterSeal 905accelerator.CLEAN UPImmediately after use and before sealant hascured, clean equipment with MasterSeal 990or xylene. Cured sealant may be removed bycutting with a sharp-edged tool. Remove thinfilms by abrading. Do not allow uncured MasterSeal NP 2 FOR BEST PERFORMANCE Pursuant to accepted industry standards andpractices, using rigid paints and/or coatingsover flexible sealants can result in a loss ofadhesion of the applied paint and/or coating,due to the potential movement of the sealant.However, should painting and/or coating bedesired, it is required that the applicator of thepaint and/or coating conduct on-site testing todetermine compatibility and adhesion. to come into contact with alcohol-basedmaterials or solvents.Do not use as a cap, heel or toe bead forexterior glazing.Do not apply polyurethane sealants in thevicinity of uncured silicone sealants or uncuredMasterSeal NP 150 .MasterSeal NP 2 should not come in contactwith oil-based caulking, silicone sealants,polysulfides or fillers impregnated with oil,asphalt or tar.Do not apply epoxy-based coatings in thevicinity of uncured MasterSeal NP 2.Do not apply to freshly treated wood; treatedwood must have weathered for at least 6months.Do not open containers until ready for use.Units are premeasured; do not use partialunits.MasterSeal NP 2 may yellow in thepresence of unvented artificial heat; this isa surface phenomenon that does not affectsealant performance.When MasterSeal NP 2 is used in areas subjectto continuous water immersion, cure for 14 daysat 70 F (23 C). Allow longer cure times at lowertemperatures. Always use Master Seal P 173.Do not use in swimming pools, or onother submerged conditions where thesealant will be exposed to strong oxidizers.Avoid submerged conditions where watertemperatures will exceed 120 F (50 C).Horizontal joints subject to traffic or intermittentponding of water require the use of primer. CallTechnical Service for details.Substrates such as copper, stainless andgalvanized steel typically require the use ofa primer; MasterSeal P 173 or MasterSealP 176 are acceptable. For Kynar coatings,use MasterSeal P 173 only. An adhesion testis recommended for any other questionablesubstrate.Use only MasterSeal 900 color packs designedfor use with MasterSeal NP 2.Proper application is the responsibility of theuser. Field visits by Master Builders Solutionspersonnel are for the purpose of makingtechnical recommendations only and not forsupervising or providing quality control on thejobsite.HEALTH, SAFETY AND ENVIRONMENTALRead, understand and follow all Safety DataSheets and product label information for thisproduct prior to use. The SDS can be obtainedby visiting www.master-builders-solutions.com/en-us, e-mailing your request to mbsbscst@mbcc-group.com or calling 1(800)433-9517.Use only as directed.IN CASE OF EMERGENCY: Call CHEMTEL 1 (800) 255-3924 or if outside the US orCanada, 1 (813) 248-0585.
Master Builders MITED WARRANTY NOTICEMaster Builders Solutions ConstructionSystems US, LLC (“Master Builders”) warrantsthis product to be free from manufacturingdefects and to meet the technical propertieson the current Technical Data Guide, if usedas directed within shelf life. Satisfactoryresults depend not only on quality productsbut also upon many factors beyond ourcontrol. MASTER BUILDERS MAKES NOOTHER WARRANTY OR GUARANTEE,EXPRESS OR IMPLIED, INCLUDINGWARRANTIES OF MERCHANTABILITY ORFITNESS FOR A PARTICULAR PURPOSEWITH RESPECT TO ITS PRODUCTS. Thesole and exclusive remedy of Purchaser forany claim concerning this product, includingbut not limited to, claims alleging breachof warranty, negligence, strict liability orotherwise, is shipment to purchaser ofproduct equal to the amount of product thatfails to meet this warranty or refund of theoriginal purchase price of product that failsto meet this warranty, at the sole option ofMaster Builders. Any claims concerning thisproduct must be received in writing within one(1) year from the date of shipment and anyclaims not presented within that period arewaived by Purchaser. MASTER BUILDERSWILL NOT BE RESPONSIBLE FOR ANYSPECIAL, INCIDENTAL, CONSEQUENTIAL(INCLUDING LOST PROFITS) OR PUNITIVEDAMAGES OF ANY KIND.Master Builders Solutions Construction Systems US, LLC MBCC Group, Form No.1017911 rev 05/2022 registered trademark of a MBCC Group member in many countries of the worldPurchaser must determine the suitability of theproducts for the intended use and assumesall risks and liabilities in connection therewith.This information and all further technicaladvice are based on Master Builders’ presentknowledge and experience. However, MasterBuilders assumes no liability for providing suchinformation and advice including the extent towhich such information and advice may relateto existing third party intellectual propertyrights, especially patent rights, nor shall anylegal relationship be created by or arise fromthe provision of such information and advice.Master Builders reserves the right to make anychanges according to technological progressor further developments. The Purchaserof the Product(s) must test the product(s)for suitability for the intended applicationand purpose before proceeding with a fullapplication of the product(s). Performance ofthe product described herein should be verifiedby testing and carried out by qualified experts.FOR PROFESSIONAL USE ONLY. NOT FORSALE TO OR USE BY THE GENERAL PUBLIC.889 Valley Park Drive, Shakopee, MN er Service 1 (800) 433-9517Technical Service 1 (800) 243-6739
IN CASE OF EMERGENCY: Call CHEMTEL 1 (800) 255-3924 or if outside the US or Canada, 1 (813) 248-0585. Do not allow uncured MasterSeal NP 2 to come into contact with alcohol-based materials or solvents. Do not use as a cap, heel or toe bead for exterior glazing. Do not apply polyurethane sealants in the