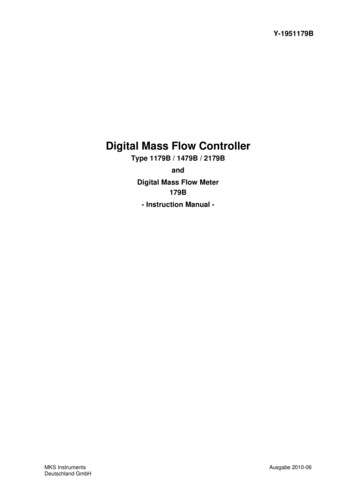
Transcription
Y-1951179BDigital Mass Flow ControllerType 1179B / 1479B / 2179BandDigital Mass Flow Meter179B- Instruction Manual -MKS InstrumentsDeutschland GmbHAusgabe 2010-06
Copyright 2003 by MKS Instruments Deutschland GmbH.All rights reserved. No part of this work may be reproduced or transmitted in any form or by any means, electronicor mechanical, including photocopying and recording, or by any information storage or retrieval system, except asmay be expressly permitted in writing by MKS Instruments.Printed in the Federal Republic of GermanySwagelok , VCR , and VCO are registered trademarks of Swagelok Marketing Company, Solon, OHKalrez and Viton are registered trademarks of DuPont Dow Elastomers Inc., Wilmington, DENUPRO is a registered trademark of Crawford Fitting Company, Solon, OHKel-F is a registered trademark of 3M, Minneapolis, MN
1179B/1479B/2179B/179BTable of ContentsTable of ContentsMass Flow Controller Safety Information . 9Symbols Used in This Instruction Manual.9Symbols Found on the Unit.10Safety Procedures and Precautions.11Chapter 1: General Information. 13Introduction.13Overview of Versions .13Options .14Special versions .14Power Supply and Readout Units .14Profibus Version .14Reliability .15Instruction Manual .15Contents .15Conventions .15Designations and Names .16Chapter 2: Shipment . 17General.17Unpacking .17Unpacking Checklist.17Analog Units .17Profibus Units .18Optional Accessories: .18Label.19Clean Room Packaging .19Chapter 3: Connectors and Control Elements . 21Analog Units .21Potentiometer ZERO .22RESET Switch.22Electrical Connector .231179B, Analog Unit .23iii
Table of Contents1179B/1479B/2179B/179BProfibus Units . 24RESET Switch . 25Address and Mode switch A/B . 25Status LED STS . 25Electrical Connectors . 261179B, Profibus Units, Connector ANALOG. 261179B, Profibus Units, Connector PROFIBUS . 27Chapter 4: Installation. 29General Requirements . 29Environmental. 29Location and Orientation . 30Protection against Dust and Water . 31Use of a Positive Shutoff Valve, e.g. Type 2179B . 31Leak Integrity . 31Pressure Drop Test . 31Dimensions. 32Type 179, 1179 and 1479, Analog and Profibus Units . 32Mounting Holes on 179, 1179, 1479 Analog and Profibus Units . 33Type 2179B, Analog and Profibus Units . 34Mounting Holes . 35Electrical Connections and Cables . 36Cables and Controllers by MKS . 36Power Supply / Readout Units of other Manufacturers. 36Non MKS Cables . 37Finishing the Installation. 37Chapter 5: Operation (Analog Units) . 39Start Up the Mass Flow Controller/Meter . 39Zero Adjust . 40Override the Control Valve . 41Priority of Commands . 41iv
1179B/1479B/2179B/179BTable of ContentsChapter 6: Operation (Profibus Units). 43Functions .43Overview .43Valve Override.44Auto Zero.44Alarm Limits.44Temperature Measurement.44Valve Drive Level .44User Span / Gas Correction .45User Zero .45Filter.45Gas Tables .45Soft Start Rate.45Start Up the Mass Flow Controller .46Zeroing the Flow Controller.47Zero Offset .47Status LED STS .48Adress and Mode Switch A/B.48Switch Assignment .48Mode B .48Setting an Address .49Mode A .49Zero Modes .49PROFIBUS Protocol.50Data Interface.50Send Data .51Small Receive Data.52Full Receive Data .53Small Setup .54Full Setup .55Small Diagnostics.57Full Diagnostics .58Calibration Table .60PROFIBUS Setup.61GSD Files Usage.61Standard GSD File .62v
Table of Contents1179B/1479B/2179B/179BChapter 7: Theory of Operation. 63Technique of Measurement and Control, Electronics . 63Flow Path. 64Measurement Technique. 64Control Circuitry. 64Control Valve . 65Chapter 8: Gas Correction Factor (GCF) . 67The Gas Correction Factor (GCF):. 67How To Calculate the GCF for Pure Gases . 67How To Calculate the GCF for Gas Mixtures. 68Example. 69Mass Flow Rate at a Different Reference Temperature . 69Direct Reading of the Analog Output Signal . 70Chapter 9: MFC Sizing Guidelines . 71General. 71Determining the Flow Controller Range . 72Configurations for Low or High Differential Pressure. 72Chapter 10: Maintenance . 73General. 73Zero Adjustment . 73Checks and Recalibration . 73Profibus Support Kit . 74Customer Support . 74Troubleshooting. 75Chapter 11: Type 179B, 1179B, 1479B, 2179B (Comparison). 77Type 179B . 77Type 1179B . 77Type 1479B . 77Type 2179B . 77Pneumatic Positive Shutoff Valve . 78Appendix A: Product Specifications . 79Specifications . 79Environmental Specifications . 80Electrical Specifications. 80Physical Specifications. 81vi
1179B/1479B/2179B/179BTable of ContentsAppendix B: Model Codes. 83Model Code .83Appendix C: Gas Correction Factors . 87Appendix D: Binary Code . 91MKS Worldwide Calibration & Service Centers . 93There is a declaration of contamination on the last page of this instruction manual.vii
Table of Contents1179B/1479B/2179B/179BList of FiguresFigure 1: Model Code Label . 19Figure 2: 1179B /1479B / 179B Side View . 21Figure 3: 1179B /1479B / 179B Connector Side . 21Figure 4: 1179B / 1479B / 179B Gas Inlet Side . 22Figure 5: 15-pol. connector . 23Figure 6: 1179B / 1479B / 179B Side View . 24Figure 7: 1179B / 1479B / 179B Connector Side . 24Figure 8: 1179B / 1479B / 179B Gas Inlet Side . 25Figure 9: 9-pol. Connector. 26Figure 10: Profibus Connector . 27Figure 11: 1179B 1479B / 179B Dimensions (Side) . 32Figure 12: Dimensions (Inlet/Outlet side). 33Figure 13: Mounting Holes on 1179B, 1479B, 179B. 33Figure 14: Type 2179B, Side. 34Figure 15: Type 2179B, Connector Side. 35Figure 16: Base Plate, Dimensions and Mounting Holes. 35Figure 17: Adress and Mode Switch Map A/B . 48Figure 18: Assembly. 63Figure 19: Voltage Divider. 70List of TablesTable 1: Definition of Symbols Found on the Unit. 10Table 2: MKS Cables. 36Table 3: Troubleshooting. 76Table 4: Ordering Code - Ranges . 84Table 5: Ordering Code - Fittings . 84Table 6: Ordering Code - Valves. 85Table 7: Ordering Code - Connectors . 85Table 8: Ordering Code - Seals. 85Table 9: Binary Code. 91viii
1179B/1479B/2179B/179BMass Flow Controller Safety InformationMass Flow Controller Safety InformationSymbols Used in This Instruction ManualDefinitions of WARNING, CAUTION, and NOTE messages used throughout the manual.WarningThe WARNING sign denotes a hazard to personnel. It callsattention to a procedure, practice, condition, or the like, which, ifnot correctly performed or adhered to, could result in injury topersonnel.CautionThe CAUTION sign denotes a hazard to equipment. It callsattention to an operating procedure, practice, or the like, which, ifnot correctly performed or adhered to, could result in damage to ordestruction of all or part of the product.NoteThe NOTE sign denotes important information. It calls attention to aprocedure, practice, condition, or the like, which is essential to highlight.9
Mass Flow Controller Safety Information1179B/1479B/2179B/179BSymbols Found on the UnitThe following table describes symbols that may be found on the unit.Definition of Symbols Found on the Unit Earth (ground)IEC 417, No.5017Protective earth(ground)IEC 417, No.5019EquipotentialityIEC 417, No.5021Direct currentIEC 417, No.5031Alternating currentIEC 417, No.5032Both direct andalternating currentIEC 417, No.5033-aClass ll equipmentIEC 417, No.5172-aThree phasealternating currentIEC 617-2 No.020206Caution, refer toaccompanyingdocumentsISO 3864, No.B.3.1Caution, risk ofelectric shockISO 3864, No.B.3.6Caution, hot surfaceIEC 417, No.5041On (Supply)IEC 417, No.5007Frame or chassisIEC 417, No.5020Off (Supply)IEC 417, No.5008Table 1: Definition of Symbols Found on the Unit10
1179B/1479B/2179B/179BMass Flow Controller Safety InformationSafety Procedures and PrecautionsThe following general safety precautions must be observed during all phases of operation ofthis instrument. Failure to comply with these precautions or with specific warnings elsewhere inthis manual violates safety standards of intended use of the instrument and may impair theprotection provided by the equipment. MKS Instruments, Inc. assumes no liability for thecustomer’s failure to comply with these requirements.DO NOT SUBSTITUTE PARTS OR MODIFY INSTRUMENTDo not install substitute parts or perform any unauthorized modification to the instrument. Returnthe instrument to an MKS Calibration and Service Center for service and repair to ensure that allsafety features are maintained.SERVICE BY QUALIFIED PERSONNEL ONLYOperating personnel must not attempt component replacement and internal adjustments. Anyservice must be made by qualified service personnel only.USE CAUTION WHEN OPERATING WITH HAZARDOUS MATERIALSIf hazardous materials are used, observe the proper safety precautions, completely purge theinstrument when necessary, and ensure that the material used is compatible with the wettedmaterials in this product, including any sealing materials.PURGE THE INSTRUMENTAfter installing the unit, or before removing it from a system, purge the unit completely with a clean,dry gas to eliminate all traces of the previously used flow material.USE PROPER PROCEDURES WHEN PURGINGThis instrument must be purged under a ventilation hood, and gloves must be worn for protection.DO NOT OPERATE IN AN EXPLOSIVE ENVIRONMENTTo avoid explosion, do not operate this product in an explosive environment unless it has beenspecifically certified for such operation.USE PROPER FITTINGS AND TIGHTENING PROCEDURESAll instrument fittings must be consistent with instrument specifications, and compatible with theintended use of the instrument. Assemble and tighten fittings according to manufacturer’sdirections.CHECK FOR LEAK-TIGHT FITTINGSCarefully check all vacuum component connections to ensure leak-tight installation.OPERATE AT SAFE INLET PRESSURESNever operate at pressures higher than the rated maximum pressure (refer to the productspecifications for the maximum allowable pressure).11
Mass Flow Controller Safety Information1179B/1479B/2179B/179BINSTALL A SUITABLE BURST DISCWhen operating from a pressurized gas source, install a suitable burst disc in the vacuum systemto prevent system explosion should the system pressure rise.KEEP THE UNIT FREE OF CONTAMINANTSDo not allow contaminants to enter the unit before or during use. Contamination such as dust, dirt,lint, glass chips, and metal chips may permanently damage the unit or contaminate the process.ALLOW THE UNIT TO WARM UPIf the unit is used to control dangerous gases, they should not be applied before the unit hascompletely warmed up. Use a positive shutoff valve to ensure that no erroneous flow can occurduring warm up.12
1179B/1479B/2179B/179BChapter 1: General InformationChapter 1: General InformationIntroductionThe digital mass flow controllers of the 1179B series accurately measure and control the mass flowrate of gases. The type 179B of this series is a mass flow meter for mass flow measurement onlyand is completely metal sealed.Based upon an patented * MKS measurement technique, these instruments use a laminar flowdevice whose precise indication of mass flow is achieved through the use of a laminar bypasselement in parallel with a sensor tube. The 1179, 1479 and 2179 digital controllers use a PIDalgorithm which compares the flow signal with an external setpoint command, thus creating acontrol signal which is applied to a solenoid driven control valve to set the desired flow rate. Thecontrollers also feature in the analog mode the ability to accept TTL level commands to remotelyopen and close the control valve. The control valve is located at the outlet of the meter section,also inside the metal instrument housing. The metal cover plus the RF bypass capacitors virtuallyeliminate RFI and EMI interference.The flow signal as derived from the sensor and also an analog setpoint signal are digitalized.Therefore linearization, flow control and handling of all other signals and commands is operated bythe microcomputer, in both digital and analog versions of the B series. This provides best accuracyand optimizes the controller’s response and stability.The 1179,1479 controller and 179 meter have a three-inch footprint. The type 2179 has a positiveshutoff valve, pneumatically driven and close coupled to the controller outlet.Overview of VersionsTypeFunctionFeatures179BMass Flow MeterStandard unit, all metal sealed, full scale ranges from 5 to20 000 sccm1179BMass FlowControllerStandard unit, one elastomer seal, all other sealing metal, fullscale ranges same as Type 179B, fully closing control valve,override function1479BMass FlowControllerSame as 1179B but all metal sealed2179BMass FlowControllerSame as 1179B but with positive shutoff valve at outlet side*US Patent No 546191313
Chapter 1: General Information1179B/1479B/2179B/179BOptions Analog version (digital electronic with analog interfacing) Profibus version Full scale range: 10, 20, 50, 100, 200, 500, 1000, 2000, 5000, 10.000, 20.000 sccm(N2-equivalent); Fittings: Cajon 4-VCR male, Cajon 4-VCO male, 6 mm and 1/4“ Swagelok , DN16KFFor other fittings and ranges contact MKS please.Special versionsThere are many variations of the above listed versions and options possible, for example with filter mounted at inlet with all metal valve plug low pressure drop versions for low inlet pressure or small differential pressure applications,e.g. combination with vaporizers or use with air sampling pumps etc. combinations (Gas Sticks) with filters, pneumatic shutoff valves at inlet and/or outlet, purgefitting, mini-pressure transducers etc.The control valve of all mass flow controllers is a normally closed (NC) valve.Power Supply and Readout UnitsThe analog versions of the 1179B series can interface to complementary MKS equipment whichare available as single channel, dual channel, four and eight channel units to display the flowsignal and to provide the power and set point commands. Almost all control units are equipped withserial interface. Refer to the corresponding manuals for requirements and instructions.Profibus VersionThe particular features of units with Profibus interface, setup and control are described inChapter 6, Operation.Note: All Profibus
Y-1951179B . Digital Mass Flow Controller . Type 1179B / 1479B / 2179B . and . Digital Mass Flow Meter . 179B - Instruction Manual - MKS Instruments Deutschland GmbH