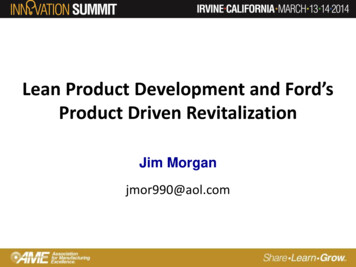
Transcription
Lean Product Development and Ford’sProduct Driven RevitalizationJim Morganjmor990@aol.com
Innovation – the heart of lean TPS (the genesis of lean) evolves, adapts and continually improves – ithas human ingenuity and innovation at its very core JIT or Kanban are “counter measures” with an implicit expectationthat a better method will be developed Lean at it’s heart is a powerful system of continuous innovation successful in a variety of environments This is the essence of lean product development. It is a powerful andprofound system to focus the creative power of people across theenterprise on delivering truly great products and its not new
Event Sequence of LPPD Research Al Ward develops concept of “Set-based RecursiveDesign” @MIT (Late 1980s) MIT Studies and “The Machine That Changed theWorld” Womack, Jones & Roos (1990) ProductDevelopment “ Product Development Performance” Clark &Fujimoto (1991) University of Michigan Japan Auto Studies (199198) (Liker/Ward/Sobek/Hammett) High Performance Product Development U of MResearch (J. Morgan 1999 to 2003)
Research Results: High PerformanceProduct Development at ToyotaBest Quality First place in seven of sixteen J.D. Powers categories forinitial quality in 2001, nine in 2002, six in 2003, seven in2004, and ten in 2005 (Total of 39 to 29 total for all ofN.A. since 2001) Lexus capturing three of the four luxurycategories as well as being rated as the highest qualitybrand in JD Powers) Industries lowest TGW/1000 andhighest over all customer sat (80). The highest qualityassembly plants worldwide and first place in five of tencategories of Consumer Reports Top Autos.Sales and Profit AVG Profit/Rev: Toyota 7.5B / 135.7B vs. NA Avg.( 45)mil / 171.8B
Research Results: High PerformanceProduct Development at ToyotaSpeed to Market Product development lead times that were half of theircompetitorsMost Efficient Process Best in industry engineering efficiencies and fraction ofthe engineering changes than competitors. Designs thatdrive the worlds most efficient plants, T.P.S. andsmoothest launches
Toyota Product DevelopmentWe found that Toyota’s product developmentsystem is as powerful and profound as theirmanufacturing system and may be even more important
Framework for a Lean ProductDevelopment Systempeoplelean productdevelopmentsystemprocesstools
Transforming An American IconIt’s nearly impossible to describe ( 17B) in losses20yr market share decline 1.90 stock priceSudden supplier bankruptcies“Cage fighting” cultureMassive layoffsBetting the company on a 23B loan“I was right – Ford’s problems weren’t as bad as Boeing’s. They were much, much worse”- Alan Mulally
Transforming An American IconIt’s nearly impossible to describe 8B profit (even with a European recession)2-yr market share increase 17 stock priceStronger global supply base“ONE FORD”Hiring thousands
Product Led Revolution“All in for product”New globaldevelopment processGlobal developmentorganizationCompletely newproduct portfolio
peoplelean productdevelopmentsystemprocesstoolsThe best people create the best productsSo we develop people & products simultaneously
People Create a Chief Engineer System to LeadDevelopment from Start to Finish Organize to Balance Functional Expertise andCross-Functional Integration Develop Towering Technical Competence –Mastery in All Engineers and Create Leaders WhoAre Technically Competent Fully Integrate the Enterprise IncludingSuppliers into the Product Development System Build in Learning and Passion for the Product Build a Culture to Drive Excellence and RelentlessContinuous Improvement
The Chief Engineer Fundamental. . .but difficult to develop Groomed as super engineers and superb leaders withstrategic assignments Responsibility without commensurate authority. Strong personalities. . .unreasonable and demanding – butfocused The voice of the customer - intuition and technicalunderstanding. Success depends on Functional organizations.
Organize around the value streamNorth AmericaJim MorganDirector Global Body Exterior, Safety& SBU EngineeringBody StructuresExterior SystemsStamping Program MgtGlobal Functional Skill TeamsStampingBusiness OfficeCraftsmanshipSafetyTDMEuropeFAPAFSA
Skilled PeopleE MC2How do you transformA brand new college graduateinto a Technically Mature, HighlySkilled and Efficient Employee?SLIDE 15
Create Towering TechnicalCompetenceHonor technical excellence and value creationDeveloping Engineers as a Priority TMMITDPMentoring & targeted assignmentsDesign reviews – for developing people and productsTechnical masteryStrong Functional Organizations Foster deep technical knowledge – continually advance yourproduct Provide an infrastructure for learning & continuous improvement Organize around the value stream Create a true competitive advantage
Technical Maturity Model @Ford Technical Maturity Models (TMM) around Critical Functions Skills required for Every Phaseof PD mapped to the Function Mixture of Industry/SpecializedTraining/On-Job ExperiencesDefined to meet requirements of“Novice”, “User”, “Expert” System must teach Employeeswhat they do not learn in school.“Body Structures 101” Mentoring role of Functionalleaders
Design Reviews Great for developing products and peopleCross-functional participationRigorous, candid and difficultPrep work part of learningCritical questions Did you consider? .How did youarrive at that?.What’s the data say?.Have youthought of?.What are your benchmarks?Scientific Method: Go and see, develop a hypothesis,execute tests, analyze, action planBring it back to foundation documents – captureknowledge
Learning At The “GEMBA” “Go and See” what is really happening – graspthe situation for yourself Ask questions – deep understanding for all. Show Respect Coach and set clear expectations Come back and do it again – CADENCE. Makelearning part of the process
Include The Extended Enterprise“Fully integrate and align around delivering great products”
The Matched Pair Process “Matched pairs” at Director, Chief & Managerlevels in Engineering & Purchasing Speak with one voice of Ford Motor Company Align processes, tools & objectives arounddelivering great products Improved quality & speed decision making ABF (Aligned Business Framework) for majorsuppliers
L λωLeadTime0peopleCapacity100%CAPACITY UTILIZATIONSTANDARD PROCESS &ARCHITECTURElean productdevelopmentsystemprocessPERFECT DRAWING PLANtoolsSTANDARDIZATION Ca 2 Ce 2 u CTq te 2 1 u REDUCEVARIABILITYPDVSM
ProcessLeadTimeL λωSTUDY/KENTOU (Front Loaded process to create the right0Capacity100%product)CAPACITY UTILIZATION Product immersionpeople Chief engineer concept paper Set-basedcollaborationSTANDARDPROCESS &ARCHITECTUREEXECUTION (to deliver the product right)lean product Capacity/CapabilitydevelopmentPERFECT DRAWING PLAN Enabling process logicsystem Create Flow/Synchronizecross functionallytoolsprocess Compatibility before completion/minimum feasible maturitySTANDARDIZATION System of standards (fixed and flexible / C.I.)REFLECTION/LEARNING Ca 2 Ce 2 u GEMBACT q Learning teat 2 1 u Reflection/HanseiREDUCEVARIABILITYPDVSM
Study: Create the Right ProductCreate mechanisms toalign the enterprisearound delivering thegreatest value to thecustomer Mono-sukuri – Bringsenterprise together todeliver value to thecustomer Kara-kuri – teardownlink to attributes Bundled Planning
Study: Create the Right Product“Set Based” Enablers: Utilize mechanisms toexamine multipledesigns/solution sets Early Design Reviews 3x Internal 3x Competition R&D Supplier Tech Design Efficiency
Creating Flow Capacity/Capability– Linked– Dynamic– Capability study Enabling Process Logic– Clear quality of event criteria– Scalable– Built in C.I. mechanism– Synchronize cross-functionally Create Flow– CbC (Compatibility before Completion)– MFM (Minimum Feasible Maturity)– Virtual / Physical Detailed Scheduling / Execution Discipline– Block timing “traveling hopefully”Powerful Standards Underpin the ProcessFixed and flexible
Capability & Capacity Tough to know one withoutreally understanding the other Task and inter-arrival variabilityand system capacity effects Numerous dynamic contributing variables toconsider Process capability studies Create flexible capacity where possible Understand and monitor critical milestones27
Compatibility Before CompletionCompletenessEngineering thoroughness ofgiven design includingdesign analysis for failuremode avoidance, testing andverificationCONCLUSIONEarly focus on completioncreates more CAD work andlate engineering changes .LPPD synchronizes theprocesses of compatibilityand completeness minimizingrework workload andshortening lead time28TraditionalRelease PointPart DetailVerify AttributesResolve PackageLean PPDProcessIdentify PartsProgram StartCompatibilityShould be a subset of completeness, virtual (CAD/CAD)checks done prior to CAD freeze for robust release.DPA work streams ensure critical interdependencies arechecked. SynchronizationSequencing value-added work acrossFunctions to eliminate rework loops (gives &gets)
Powerful Global StandardsProcess Driven Product Design (PDPD)Standard ArchitecturePerfect Drawing Plan (PDP)Global Standard Press Equipment“Today's standardization is the necessary foundation on which tomorrow's improvements will be based the best you know today to be improved tomorrow. But if you think of standards as confining, thenprogress stops”Henry Ford29
A Plan for Every PartPDP Overview – “Recipe for Success” Commodity Specific Development Timing Defines Engineering Needs and Deliverables ByMilestone To Enable Success – Clear Quality of EventCriteria and linked to high level process Highlights Any Disconnects Between Program Timing,and Commodity Timing Consistent Program to Program Template for Engineers and basis for CI30Commodity Business Plan Medium range plan for platformarchitecture and materials Supplier strategy development Manufacturing footprintdevelopment Value chain analysis
Enabling Standards & InnovationHydroforming Enabling standards andstrong foundationalknowledge allow innovationin complex systems A challenging environment Enabling process Skilled, creative, motivatedpeople workingcollaboratively.Opportunities often crossFunctionsPSH ProcessHydro-Forming Process:1.Rolled tube2.Pre-bend part to approximate configuration3.Pre-crush the bent tube with an internalpressure in the tube of approximately 1000 psito control the deformed shape4.Pressurize tube to achieve final geometry5.Final Trim and Pierce1,000 psi10,000 psiMagnesium Liftgate
Enabling Standards & Innovation Often a response tocomplex and conflictingmarket/regulatorydemands. Front endchallenge: designleadership/pedpro/LSD/crash/aero & CO2emissions Or “adjacentinnovation” to changean entire industry Prog Die vs. In-Die AutomationScallop BlanksBIW TopologyOptimizationLaser Welding
Aluminum F150
peoplelean productdevelopmentsystemprocesstoolsTools That Enable People & Processes
TOOLS and TECHNOLOGYpeople Adapt Powerful Technologyto Fit YourPeople and Process to Fully Leverage TheirCapabilitieslean productdevelopment Align Your OrganizationThrough Simple,systemVisual Communicationprocesstools Use Powerful Tools for Standardization,Alignment and Organizational Learning
Powerful Technology: The DigitalValue Stream Common language from studio to shop floor Eliminate data conversion steps, errors &other waste Enabler for global PD strategy and reusabilityAnalytical PrototypesLighting SimulationCAD/Engineering TemplatesVirtual ManufacturingStage 3 : Parameter Y SD OTR 27846 MATL THKCD338DimD219/D258200 AL - ParametersA PLR REINF 513A12 MATL THKmm1.891.47A PLR INR 202A66 MATL THKmm1.891.47EStandard Design GapmmFA Line OffsetmmGTangent Offset (from radii on flange)mmHA66 - AB WELD FLATmmJA66 - ANGLE OFF AB FLANGEdeg0.0MaxEngineering Requirement Program Specific Engineering Target2NomTol ( /-)MaxMinEngineering Requirement1Min0.70Dent & Ding: 6 - INSIDE SURF FLAT LENGTHmm15.6N/AA66 - W/S WELD FLATmm15.418.9A66 - ANGLE OFF W/S alParameter IDbs test 1Unitslength1.40200albs test 2length1.40200albs test 3length200albs test 5lengthDynamic Seal200albs test 6length200albs test 7length12.2Welding: ES-4G13-1N261-AC200albs test 8length200albs test 9length12.2Welding: ES-4G13-1N261-ACE Coat DrainageSqueak & Rattle3.013.4A66 - FIRST SWEEP OFF AB THEO LENGTHLNTol ( /-)1.53.0KMBaseline Engineering GuidelineNom0.84BC200albs test 10length200albs test 11length200albs test 12length200albs test 13lengthPA66 - FIRST RADIUS OFF ABmm5.07.06.03.03.0200albs test 14lengthRA66 - SECOND RADIUS OFF ABmm5.05.06.04.04.0200albs test 15lengthSA66 - FIRST RADIUS OFF W/S FLANGEmm5.07.06.06.05.0200albs test 16lengthTA66 - SECOND RADIUS OFF W/S FLANGEmm5.05.06.06.06.0200albs test 17lengthUA66 - FLAT FIRST SWEEP OFF W/S FLANGE25.831.0200albs test 18lengthV60.676.0200albs test 19lengthmm23.433.341.5A66- DRAW OPEN ANGLEdeg59.090.5124.5WA12 - RADIUS BETWEEN AB & BC OFFSETmmXA12 - OUTSIDE RADIUS ON BODYSIDE OFFSET mm6.08.05.06.05.06.05.06.05.010.07.0200albs test 20length7.0200albs test 21lengthYA12 - FIRST RADIUS OFF W/S FLANGEmm7.0200albs test 22lengthZA12 - INSIDE RADIUS ON BODYSIDE OFFSETmm8.05.05.08.07.0200albs test 23lengthA12 - DRAW OPEN ANGLEdeg14.311.915.134.650.0200albs test 24lengthbs test 25lengthbs test 26lengthAA6.05.0BB846 - FIRST RADIUS OFF CLASS 1 W/S SIDEmm3.02.52.62.02.01.8Stamping - PDPD200alCC846 - FIRST RADIUS OFF CLASS 1 DOOR SIDE mm5.02.52.53.02.82.5Stamping - PDPD200al200albs test 27lengthStamping - PDPD200albs test 28length200albs test 29leng
progress stops” Henry Ford Process Driven Product Design (PDPD) Standard Architecture Perfect Drawing Plan (PDP) Global Standard Press Equipment