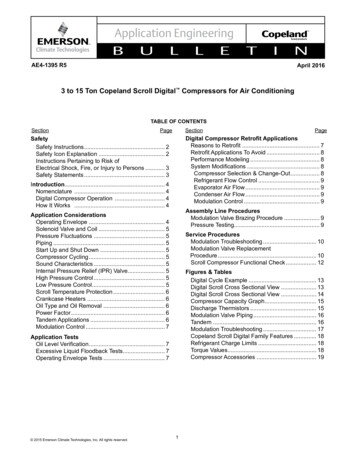
Transcription
AE4-1395 R5AE4-1395 R5April 20163 to 15 Ton Copeland Scroll Digital Compressors for Air ConditioningTABLE OF CONTENTSSectionPageSectionDigital Compressor Retrofit ApplicationsReasons to Retrofit. 7Retrofit Applications To Avoid. 8Performance Modeling. 8System Modifications. 8Compressor Selection & Change-Out. 8Refrigerant Flow Control. 9Evaporator Air Flow. 9Condenser Air Flow. 9Modulation Control. 9SafetySafety Instructions. 2Safety Icon Explanation. 2Instructions Pertaining to Risk ofElectrical Shock, Fire, or Injury to Persons. 3Safety Statements. 3Introduction. 4Nomenclature . 4Digital Compressor Operation . 4How It Works . 4Assembly Line ProceduresModulation Valve Brazing Procedure. 9Pressure Testing. 9Application ConsiderationsOperating Envelope. 4Solenoid Valve and Coil. 5Pressure Fluctuations. 5Piping. 5Start Up and Shut Down. 5Compressor Cycling. 5Sound Characteristics. 5Internal Pressure Relief (IPR) Valve. 5High Pressure Control. 5Low Pressure Control. 5Scroll Temperature Protection. 6Crankcase Heaters. 6Oil Type and Oil Removal . 6Power Factor. 6Tandem Applications. 6Modulation Control. 7Service ProceduresModulation Troubleshooting. 10Modulation Valve ReplacementProcedure. 10Scroll Compressor Functional Check. 12Figures & TablesDigital Cycle Example. 13Digital Scroll Cross Sectional View. 13Digital Scroll Cross Sectional View. 14Compressor Capacity Graph. 15Discharge Thermistors. 15Modulation Valve Piping. 16Tandem. 16Modulation Troubleshooting. 17Copeland Scroll Digital Family Features. 18Refrigerant Charge Limits. 18Torque Values. 18Compressor Accessories. 19Application TestsOil Level Verification. 7Excessive Liquid Floodback Tests. 7Operating Envelope Tests. 7 2015 Emerson Climate Technologies, Inc. All rights reserved.Page1
AE4-1395 R5Safety InstructionsSafety Instructions CopelandCopeland ScrollScroll compressorscompressors areare manufacturedmanufactured accordingaccording toto thethe latestlatest U.S.U.S. andand EuropeanEuropean SafetySafety wParticular emphasis has been placed on the user's safety. Safey icons are explainedand inthisbulletinaregroupedonPage3.Theseinstructions applicable to the products in this bulletin are grouped on page 3. These instructions shouldinstructions should be retained throughout the lifetime of the compessor. You are strongly advisedbe retained throughout the lifetime of the compressor. You are strongly advised to follow these safetyto follow these safety instructions.instructions.Safety Icon ExplanationDANGERDANGER indicates a hazardous situation which, if not avoided, will resultin death or serious injury.WARNINGWARNING indicates a hazardous situation which, if not avoided, couldresult in death or serious injury.CAUTIONCAUTION, used with the safety alert symbol, indicates a hazardoussituation which, if not avoided, could result in minor or moderate injury.NOTICECAUTIONNOTICE is used to address practices not related to personal injury.CAUTION, without the safety alert symbol, is used to address practicesnot related to personal injury. 2015 Emerson Climate Technologies, Inc. All rights reserved.2
AE4-1395 R5Instructions Pertaining to Risk of Electrical Shock, Fire, or Injury to PersonsWARNINGELECTRICAL SHOCK HAZARD Disconnect and lock out power before servicing. Discharge all capacitors before servicing. Use compressor with grounded system only. Molded electrical plug must be used when required. Refer to original equipment wiring diagrams. Failure to follow these warnings could result in serious personal injury.WARNINGPRESSURIZED SYSTEM HAZARD System contains refrigerant and oil under pressure. Remove refrigerant from both the high and low compressor side beforeremoving compressor. Never install a system and leave it unattended when it has no charge,a holding charge, or with the service valves closed without electricallylocking out the system. Use only approved refrigerants and refrigeration oils. Personal safety equipment must be used. Failure to follow these warnings could result in serious personal injury.WARNINGBURN HAZARD Do not touch the compressor until it has cooled down. Ensure that materials and wiring do not touch high temperature areas ofthe compressor. Use caution when brazing system components. Personal safety equipment must be used. Failure to follow these warnings could result in serious personal injury orproperty damage.CAUTIONCOMPRESSOR HANDLING Use the appropriate lifting devices to move compressors. Personal safety equipment must be used. Failure to follow these warnings could result in personal injury orproperty damage.Safety Statements Refrigerant compressors must be employed only for their intended use. install, commission and maintain this equipment. All valid standards and codes for installing, servicing, and maintaining electrical andrefrigeration equipment must be observed. 2015 Emerson Climate Technologies, Inc. All rights reserved.3
AE4-1395 R5IntroductionDigital Compressor OperationThe 3 to 15 ton Copeland Scroll Digital compressorsdescribed in this bulletin include the follow compressormodel numbers:The digital scroll is capable of seamlessly modulatingits capacity from 10% to 100%. A normally closed(de-energized) solenoid valve is a key component forachieving modulation. When the solenoid valve is in itsnormally closed position, the compressor operates atfull capacity, or loaded state. When the solenoid valveis energized, the two scroll elements move apart axially,or into the unloaded state. During the unloaded state,the compressor motor continues running, but sincethe scrolls are separated, there is no compression.During the loaded state, the compressor delivers 100%capacity and during the unloaded state, the compressordelivers 0% capacity. A cycle consists of one loadedstate and one unloaded state. By varying the time ofthe loaded state and the unloaded state, an averagecapacity is obtained. The lowest achievable capacity is10% which equates to 1.5 seconds of pumping duringone 15 second cycle.R-410AR-22 & R-407CZPD34 to ZPD54K5ZRD36 to ZRD81KCZPD61-ZPD83, ZPD91,ZPD104, ZPD122KCZRD94 to ZRD125KCZPD103, ZPD120,ZPD137-182KCZPD and ZRD digital scroll compressors are variablecapacity compressors that can modulate down to 10%of full load. Digital scrolls are suitable for a variety ofapplications where a variable capacity compressor isuseful, such as VAV applications, dedicated outsideair units, units that typically used hot gas bypass forcapacity control, and applications that require accuratecontrol of temperature and humidity. Other applicationsinclude multiple compressor systems where modulationis required over the entire operating range of the systemand in applications where compressor starting andstopping is unacceptable. Typical digital scroll modelnumbers are ZRD94KCE-TF5 and ZPD182KCE-TWD.This bulletin describes the operating and applicationdifferences with respect to the equivalent fixedcapacity Copeland Scroll compressors. The followingApplication Engineering bulletins should be consultedfor non-modulating scroll application guidelines:An example for the 15 second controller cycle: In any15 second cycle, if the loaded time is 10 seconds andthe unloaded time is 5 seconds, the average capacityis 66% or if the loaded time is 5 seconds and theunloaded time is 10 seconds the capacity during that15 second period is 33%. See Figure 1 for a graphicalrepresentation of the digital cycle, and Figure 4 fora graph showing solenoid on-time vs. compressorcapacity.How it WorksAE4-1331 ZPD34-ZPD54K5The digital scroll compressor unloads by takingadvantage of the Copeland Scroll compressor's axialcompliance. All Copeland Scroll compressors aredesigned so that the compression elements canseparate axially a few thousands of an inch. TheZPD34-ZPD54K5, ZPD61-ZPD83KC, ZPD91KC,ZPD104KCE, ZPD122KCE, and ZRD36-81KCcompressors described in this bulletin use a lift pistonmechanism to separate the scrolls during the unloadedstate. When the solenoid is energized the volume on topof the piston is vented to the low side allowing the pistonand fixed scroll assembly to move axial away from theorbiting scroll. When the solenoid is de-energized thepiston is forced down and the scrolls are loaded axially.AE4-1365 ZPD61-ZPD83KC, ZPD91KC,ZPD104KCE, ZPD122KCEAE4-1303 ZPD103KC, ZPD120KC,ZPD137-182KC, ZRD94-125KCAE4-1312 ZRD36-81KCNomenclatureThe model number of the Copeland Scroll Digitalcompressors includes the approximate nominal60 Hz capacity at the AHRI high temperature fullload air conditioning rating point. An example is theZPD120KCE-TFD, which has approximately 120,000Btu/hr cooling capacity at the air conditioning ratingpoint when operated on 60 Hz. Note that the samecompressor will have approximately 5/6 of thiscapacity or 100,000 Btu/hr when operated on 50 Hzpower. Please refer to the Online Product Informationat EmersonClimate.com for more information onperformance at part load. 2015 Emerson Climate Technologies, Inc. All rights reserved.The ZPD103KC, ZPD120KC, ZPD137-182KC andZRD94-125KC digital scroll compressors employa solenoid valve that is mounted on the side of thecompressor that vents the intermediate cavity to thelow side of the compressor during the unloaded state.During the loaded state the solenoid valve is de4
AE4-1395 R5energized and the intermediate cavity is pressurizedto load the floating seal and scrolls axially.velocity remains above 1500 fpm when only the digitalscroll is running.Please refer to Figures 2 and 3 for cross sectionalpictures of the two digital modulation mechanisms.Start Up and Shut DownTo improve the starting characteristics of the digitalscroll compressor, the the Emerson controllers delayloading the compressor for 0.1 seconds. Likewise, toeliminate the reverse rotation sound at shut down thecompressor is unloaded 0.5 seconds before shut down.APPLICATION CONSIDERATIONSOperating EnvelopeRefer to the fixed capacity compressor model familyapplication bulletin for approved operating range.System testing is highly recommended to verifyadequate oil return during fully loaded and modulatedoperation.Compressor CyclingBecause of the digital scroll's seamless capacitymodulation from 10% to 100%, capacity short cyclingshould not be a problem for single compressors.Modulating below 10% is not recommended due topossible motor overheat and inadequate oil return.However, if the digital compressor is in tandem with anon modulated scroll, short cycling of the non modulatedcompressor may be a problem if the system control isnot designed and set correctly. The Emerson digitalcontrollers have a built in two minute anti-short cycletimer to prevent short cycling.Solenoid Valve and CoilThe external solenoid valve and coil specified byEmerson must be used since this is a critical componentfor the proper functioning of this compressor. Thesolenoid valve and coil are designed for approximately32 million cycles. Do not attempt to substitutereplacement coils or valves; use only the replacementparts specified in Table 4. Refer to the ServiceProcedures section for information on changing themodulation valves.Sound CharacteristicsThe sound spectrum of the loaded state and theunloaded state are different. Special considerationshould be given to the transition sound between theloaded and unloaded states. If the transition soundis unacceptable, a heavy sound blanket shouldbe applied to the compressor. Fabricating Services(www.fabsrv.com) is one source for scroll compressorsound blankets.Pressure FluctuationsDuring scroll modulation the suction and the dischargepressure will fluctuate. This fluctuation should beobserved during unit testing. The installation and settingof pressure controls should take this into account.During the unloaded state, the discharge pressure willdecrease and the suction pressure will increase. Thisnormal pressure fluctuation has no observable effect onthe reliability of the compressor or system components.System component manufacturers should be consultedto ensure the proper application of their products.The transition sound between the loaded and unloadedstates has no observable effect on compressorcomponents or reliability.The Emerson controllers unload the compressor afraction of a second before shut down allowing the scrollset to unload, ensuring a relatively quiet shutdown.PipingUnlike a variable speed compressor whose mass flowand gas velocity changes with its speed, the digitalscroll’s pumping capacity is equal to its 100% capacitywhile it is pumping. For this reason the gas velocityremains high even during periods when the capacitydemand is low. Because the mass flow and gas velocityremain high, piping may be designed as if it weredesigned for a non capacity controlled compressor. Forvertical piping a trap every 20 feet should be sufficientto ensure proper oil return. This recommendation isbased upon a minimum 1500 fpm velocity or higher.When the digital scroll compressor is part of a tandem,a double riser should be considered to assure that the 2015 Emerson Climate Technologies, Inc. All rights reserved.Internal Pressure Relief (IPR) ValveWARNINGA high pressure control must be used in allZRD94-125KC and ZPD103, ZPD120, ZPD137182KC applications because these compressorsdo not have internal pressure relief (IPR) valves.High Pressure ControlAs mentioned above, not all digital scrolls have IPR5
AE4-1395 R5valves, therefore high pressure controls are requiredin some applications. The recommended maximum cutout setting is 425 psig (30 bar) for R-407C & R-22 and650 psig (45 bar) for R-410A. The high pressure controlshould have a manual reset feature for the highestlevel of system protection. This pressure control mustact independently of the digital compressor controller.Oil Type and Oil RemovalMineral oil is used in the ZRD*KC compressors forR-22 applications. Polyolester (POE) oil is used inthe ZRD*KCE and ZPD*KCE compressors for R-22& R-407C and R-410A applications respectively. Seethe compressor nameplate for the original oil charge. Acomplete recharge should be approximately four fluidounces (118 ml) less than the nameplate.Low Pressure ControlAir-conditioning units can be protected against highdischarge temperatures through a low pressure control inthe suction line. Testing has shown that a cut out settingof not lower than 55 psig (3.8 bar) for R-410A and 25psig (1.7 bar) for R-407C & R-22 will adequately protectthe compressor against overheating from loss of charge,blower failure in a TXV system, etc. A higher level ofprotection is achieved if the low pressure control is set tocut out at 95 psig (6.7 bar) for R-410A and 55 psig (3.8bar) for R-407C & R-22 to prevent evaporator coil icing.The cut in setting can be as high as 180 psig (12.5 bar)for R-410A and 105 psig (7.2 bar) for R-407C & R-22 toprevent rapid recycling in case of refrigerant loss.It is an approved practice to use ZRD*KCE compressorswith POE to replace ZRD*KC compressors with mineraloil in R-22 service applications. R-22 has been approvedfor use with both mineral and POE and some mixing ofthese oil in the system is acceptable.For heat pumps, a cut out setting no lower than 20 psig(1.4 bar) is recommended for R-410A and 10 psig (0.7bar) for R-407C & R-22.If additional oil is needed in the field for mineral oilapplications, Sonneborn Suniso 3GS or ChevronTexaco Capella WF32 should be used.If additional oil is needed in the field for POEapplications, Copeland Ultra 32-3MAF, LubrizolEmkarate RL32-3MAF, Parker Emkarate RL32-3MAF/Virginia LE32-3MAF, or Nu Calgon 4314-66 (EmkarateRL32-3MAF) should be used. Copeland Ultra 22 CC,Hatcol EAL 22CC, and Mobil EAL Arctic 22 CC areacceptable alternatives.CAUTIONScroll Temperature ProtectionMost digital scrolls do not have internal dischargegas temperature protection. In order for the Emersoncontrollers to operate properly an NTC sensor must beattached to the compressor discharge line as close aspossible to the compressor discharge fitting. For bestresponse the sensor should be insulated. See Table 6of AE8-1328 for thermistor temperature vs. resistancevalues. Refer to Table 4 for part numbers of dischargeline thermistors. Figure 5 illustrates the two differenttypes of discharge thermistors.POE must be handled carefully and the properprotective equipment (gloves, eye protection, etc.)must be used when handling POE lubricant. POEmust not come into contact with any surface ormaterial that might be harmed by POE, includingwithout limitation, certain polymers (e.g. PVC/CPVCand polycarbonate).Power FactorDuring the loaded state the digital scroll compressoroperates at full capacity and the power factor is thesame as a standard scroll. However, when the scrolls areunloaded, the power factor is much lower. If power factoris an important consideration, the correcting capacitorsshould be calculated using the full capacity data to avoidproblems associated with over correction. See AE9-1249for more information on power factor correction.The ZRD61 through ZRD81KC compressors have adischarge thermistor that is inside of a well in the topcap of the compressor. If this thermistor ever needs tobe replaced, it should be replaced with either 985-019900 or 085-0204-00 as listed in Table 4.Crankcase HeatersA crankcase heater is required if the system chargeexceeds the system charge limits listed in Table 2.For more information regarding regarding heater partnumbers and installation location please refer to theequivalent non-digital scroll Application Engineeringbulletin listed on Page 4. 2015 Emerson Climate Technologies, Inc. All rights reserved.Tandem ApplicationsTandem compressors follow the same applicationguidelines as single compressors outlined in this bulletin.The refrigerant charge limit for tandem compressors is6
AE4-1395 R5shown in Table 2. A tandem circuit with a charge overthis limit must have crankcase heaters applied to bothcompressors.NOTICEFor OEMs that choose their own controlspackage, the controls must include the protectionfeatures incorporated into the Copeland ScrollDigital Compressor Controller. Please consultwith Application Engineering for a list of theserequirements.Tandem compressor assemblies are available forpurchase from Emerson. In lieu of purchasing theassembled tandem, the OEM has the option topurchase the tandem-ready compressors to assemblethe compressors into a tandem configuration intheir manufacturing plant. Drawings of the tandemmanifolds are available by contacting your applicationengineer. Figure 7 illustrates a typical tandemcompressor assembly using ZPD34-ZPD54K5, ZPD61ZPD83KC, ZPD91KC, ZPD104KCE, ZPD122KCE,and ZRD36-81KC scroll compressors. Note that onlyone compressor in the tandem assembly is a digitalscroll compressor. Customers that choose to designand build their own manifolds for tandem and triocompressor assemblies are ultimately responsiblefor the reliability of those manifold sets.APPLICATION TESTSOil Level VerificationIf the system configuration is more complex than asingle circuit packaged system with one compressor,evaporator, and condenser, an oil return test is highlyrecommended during system development testing.For this test a sample compressor with a sight-tubeshould be used to observe the oil level over theentire operating range of the system at the expectedcompressor modulation rates, to ensure an adequateoil level in the compressor at all times. The oil levelshould not go below the weld points of the lower bearingbracket for the ZPD34-ZPD54K5, ZPD61-ZPD83KC,ZPD91KC, ZPD104KCE, ZPD122KCE, and ZRD3681KC compressors. For the ZPD103KC, ZPD120KC,ZPD137-182KC and ZRD94-125KC digital scrolls theminimum oil level is 1.5" (40 mm) below the center ofthe standard oil sight-glass on the compressor. If theoil level falls below the prescribed level for more than afew minutes either more oil is required in the system oran oil recovery cycle is needed. For more informationon what an oil recovery cycle is, please consult withApplication Engineering.For more information on tandems, please refer to thenon-modulating compressor Application Engineeringbulletins listed on Page 4.Modulation ControlTwo different controls are available from Emerson toprovide digital scroll modulation control, the CopelandScroll Digital Compressor Controller and the EmersonCommercial Comfort Controller.The Copeland Scroll Digital Compressor Controller isan open loop controller that provides control, protection,and diagnostics for the digital scroll and is suited forOEM applications. The system controller supplied by theOEM calculates the required compressor capacity andcommunicates that capacity to the digital scroll controllervia a 1-5 VDC analog signal. For more information onthe Copeland Scroll Digital Compressor Controller pleaserefer to AE8-1328.If the system contains more than 20 pounds (9 kg) ofrefrigerant, it is our recommendation to add one fluidounce of additional oil for every 5 pounds (15 ml/kg)of refrigerant over this amount. This is a starting pointand oil should be added as determined through systemtesting or as required by the end use application in thefield.The Emerson Commercial Comfort Controller is a closedloop controller that provides modulation control basedon space temperature and is suited for both OEM andretrofit applications. This controller is typically located inthe conditioned space and controls the modulation cycleof the compressor without the need for an additionalsystem controller. For more information on the EmersonCommercial Comfort Controller, please refer to AE8-1393.The compressor oil level should be checked with thecompressor 'off' to avoid the sump turbulence whenthe compressor is running. Manifolded compressorsshould have their oil levels checked after 20 to 30seconds of off time, to allow oil balancing betweenthe manifolded compressors.Excessive Liquid Flood Back TestsIt is expected that the design will not flood duringoperation at all of the varying loaded and modulation 2015 Emerson Climate Technologies, Inc. All rights reserved.7
AE4-1395 R5conditions. This places demanding requirementson the flow control device to control refrigerant flowand superheat all the way down to 10% of full load.Throughout the operating range of the unit, thesuction superheat must remain positive. If theflow control device is unable to maintain superheat,an electronic expansion valve, accumulator, or othermeans must be taken to maintain at least 20 F ofcompressor sump superheat.constant cooling are all applications that would benefitfrom a modulating digital scroll. Many of these arecritical cooling applications and require equipment thatis designed specifically for these applications. Don’tattempt to retrofit a non-modulating HVAC unit, in acritical application, to one with a digital scroll in an attemptto make the unit perform well beyond its intended use.Applications that have complex refrigeration circuits(modulating reheat, heat recovery for water heating,etc.) should not be considered for a digital scroll retrofit.Operating Envelope TestSystem testing should consist of unit/system operationat abnormal operating conditions to verify that suctionsuperheat and compressor discharge temperatures stayin a range that is healthy for the compressor and trippingof the compressor overload is avoided. Please consultwith application engineering for recommended tests andanalysis of test data.Performance ModelingDIGITAL COMPRESSOR RETROFIT APPLICATIONSSuccessful digital scroll retrofit projects, and resultantenergy savings, have been documented by severalindustry energy groups. Predicting the energy usageand calculating a return on investment before theproject is undertaken is not trivial and is best done byexperienced companies that use advanced softwareprograms to predict energy use. Before large retrofitprojects are considered, as much front-end analysisas possible should be done to better predict how muchenergy might be saved. Tabular performance data andthe ten coefficients for the AHRI polynomial equation forperformance at 50% and 100% load are available formodeling purposes in the Online Product Information(OPI) section at EmersonClimate.com.NOTICEEmerson Climate Technologies, Inc. is notresponsible or liable for incorrect energy usepredictions.Reasons To RetrofitThere are a number of reasons why retrofitting a nonmodulating system to one that modulates will benefitthe building owner and its occupants. Some of thesereasons include:1. Reduced indoor temperature and humidity swings2. Reduced power consumption and operating costs3. Reduced cyclic losses4. Qualification for special utility rebatesApplications that have excess cooling capacity and aresingle zone, constant or variable air-flow are certainlyin the scope of retrofit opportunities. Units that employhot-gas-bypass for capacity control are also ideal unitsfor a digital scroll retrofit.System ModificationsNOTICEAlways check with the OEM of the equipment beingconsidered for the digital scroll retrofit, before theretrofit is undertaken. The OEM may have specificinstructions developed that offer step by stepguidance.Retrofit Applications To AvoidNOTICEAlways check with the original equipmentmanufacturer, before modifying the equipment,to understand their warranty policies regardingequipment modifications.Before beginning the retrofit, the system should beoperable and system operating conditions should belogged for future reference. The compressor suctionand discharge pressures, suction superheat, subcooling,volts, amps, evaporator air flow and leaving temperature,and system charge should all be measured and recordedprior to any system modifications.The success of the retrofit will depend on the amountof planning and evaluation done before the retrofit.Applications such as clean rooms for manufacturingsensitive components, laboratories, hospital operatingand recovery rooms, and equipment rooms that require 2015 Emerson Climate Technologies, Inc. All rights reserved.8
AE4-1395 R5Compressor Selection & Change-Outcompressor in the unit on the mounting grommetsusing the appropriate lifting devices.The replacement digital scroll compressor should becompared to the non-modulating compressor in at leastthese three areas:2. Install the compressor mounting bolts.3. Connect the suction and discharge lines usingstandard brazing practices.1. Performance – the full load capacity of the digitalscroll should be approximately equal to the capacityof the compressor being replaced. In some casesin might make sense to 'right size' the compressorcapacity for the load if the compressor is grosslyoversized.4. If the compressor has an external modulation valveand tubing (ZPD34-ZPD54K5, ZPD61-ZPD83KC,ZPD91KC, ZPD104KCE, ZPD122KCE, andZRD36-81KC only) refer to Figure 6 for the correctvalve orientation and position. Wrap a wet ragaround the valve and complete the assembly bybrazing the valve and tubing into place.2. Electrical – the digital scroll compressor RLA andLRA should be compared to the compressor beingreplaced. Contactor, wire, breaker/fuse, and runcapacitor sizes should be evaluated.5. Check for leaks using nitrogen with a properly sizedregulating and relief valve.6. Connect conduits and wiring to the compressor.Inspect and/or replace the contactor. If thecompressor is 1-phase, install the correct runcapacitor.3. Mechanical – in most cases the compressormounting will be identical for the non-modulatingand the digital scroll. There could be minordifferences in the suction and discharge tubinglocations, as well as the height of the compressor.NOTICEThe following steps should be followed to remove thenon-modulating compress
instructions applicable to the products in this bulletin are grouped on page 3. These instructions should be retained throughout the lifetime of the compressor. You are strongly advised to follow these safety instructions. Safety Instructions Copeland Scroll compressors are manufactured according to the latest U.S. and European Safety Standards.