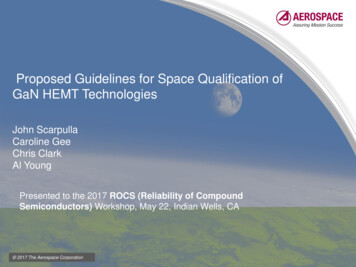
Transcription
Proposed Guidelines for Space Qualification ofGaN HEMT TechnologiesJohn ScarpullaCaroline GeeChris ClarkAl YoungPresented to the 2017 ROCS (Reliability of CompoundSemiconductors) Workshop, May 22, Indian Wells, CA 20172016 The Aerospace Corporation
GaN based Microwave HEMT technologyA “natural” for medium and high power microwaveapplications Dramatically Higher–––– RF output PowerDC breakdown voltageEfficiencyBandwidth Dramatically Lower––––SizeWeightDissipated PowerRadiation degradationCommercial applications abound:– Cell phone towers– Base stations– EMI testing Yet there are no Class A or Class B Missions currently flying GaN– No proven designs?– No flight history?– No qualified devices yet !Need exists for GaN qualification guidelines specifically for space2
GaN space qual guidelines documentis currently “in press” Objective of this presentation:– To inform the space community about our new document– To provide some highlights of the GaN issues– To invite participation––––Some History:1994 first GaN HEMTs reported2000’s AFRL HiReV program focusing on GaN reliability2013 ESA launches Proba V satellite Contains a small experimental X-band telemetry transmitter– 2014 JAXA launches Hodoyoshi-4 satellite Small X-band 2W Class AB 16QAM downlinkCurrent Assessment: GaN HEMT technology at TRL-53
Key GaN Reliability IssuesNew things to worry about GaN is “different”––––– Unlike GaAs technologyNo one single dominant failure mechanism (to date)Failure modes depend upon usageCannot assume a single activation energyCannot project failure using simple DC elevated temperature stressesMultiple (competing) failure modes have been identified–––––Calls for a more exhaustive qualificationTargeted to subset of failure mechanismsDC – multiple Q points (2-10 weeks qual, each)RF – accelerated temperature/compression (2-4 months qual)Long term –TLYF – RF operational lifetest (1 year qual)We need to rethink the single EA model4
Some Failure Mechanisms in GaN Power HEMTsGateSi3N4 passivationSCFP*DrainSourceViaGaNSiCReliability Concerns:Gate diffusion, chemical reactionsSource/drain ohmic metal-semiconductor reactionsPits/cracks – mechanical stress (IPE*)Charging/traps—virtual gate (VG)Dislocation defects (throughout)Point defects (esp. at gate-drain edge5*Source Connected Field Plate*Inverse Piezoelectric Effect*Two Dimensional Electron GasAlGaN2DEG*
DC Qual ProposalDC stressing at four operating points (Q-points)OhmicQ1 hi powerQ2 hi current lo voltageQ3 hi voltage lo currentQ4 off stateReactions/defectsVirtual gateIPE 6Depending upon the RF load figure different failure modes are manifestedDevote at least two temperatures to each Q-point
Problem with accelerated testing at Q1 onlyPossible lower EA mechanisms could be missedSatellite missions7
RF qualification proposal RF reliability testing is 10X harder than DC only testing But it is necessary until proven otherwise Choose a test vehicle (transistor, MMIC) that represents the productPerform one temperature-accelerated RF-driven lifetest––––– Maximum drive/compressionWorst case output mismatchWorst case duty cycle (or CW)Moderate temperature accelerationPicked based upon the failure times observed in DC testingPerform TLYF (test like you fly)– Operational lifetest, with realistic RF drive and compression level,waveforms– Realistic load and duty cycle– At worst case usage temperature– Purpose is to exonerate against any unknown sneak low EA failuremodes not caught by the previous qual tests8
GaN SSPA Reliability Test Fixture Accel-RF fixture with isolated heating block and airgap - 250 C max Simulates the high efficiency amp environment – TLYF 10X harder than DC testing9
Other Qual items covered in our guidelines Safe Operating Area– Gate/drain pulsed and DC absolute max. ratings– RF burnout ESDTemperature cycling– Mainly for packaging related issues, possibly a die mechanical stress effect Power cycling (still in discussion)Metallization (electromigration) and thin film resistors (stability)Back metal adhesion / Bond pull/ Die ShearLow Frequency OscillationsEnvironment– Moisture– Hydrogen poisoning Water droplet test (condensation) Air sensitivityDefects –– measurement of defect densities in Gate edges / field plates MIMCAPs Vias Radiation Testing (remarkably few issues found to date)– Total ionizing dose– Single event effects10– Displacement damage– Transient radiation
Example of Drain SOAA destructive qual test Purpose is to show sufficient margin against the absolute maximumratings– Especially critical for high power devices– (This is a margin test, not a reliability test)Adequate margin is demonstrated using a statistical approach11
PLAN forwardSTATUS A draft qual document is now available Now soliciting comments from:– GaN Semiconductor vendors– Space Hardware ContractorsPlease send email to request latest draft:john.scarpulla@aero.orgGOAL To be released as a formal rev. 0 document (possibly AerospaceTOR)THE FUTURE Generalize these qual plans for power converter – centric devices– Example: E-mode switches12
3 GaN space qual guidelines document is currently "in press" Objective of this presentation: -To inform the space community about our new document -To provide some highlights of the GaN issues -To invite participation -Some History: -1994 first GaN HEMTs reported -2000'sAFRL HiReV program focusing on GaN reliability -2013 ESA launches Proba V satellite