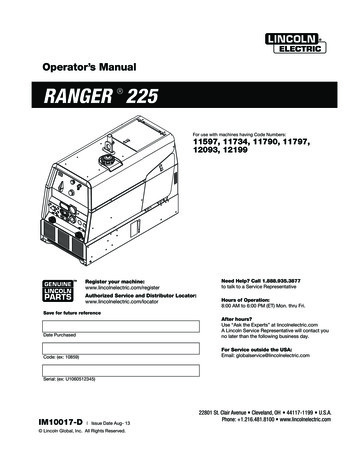
Transcription
Operator’s Manual RANGER 225For use with machines having Code Numbers:11597, 11734, 11790, 11797,12093, 12199Register your machine:www.lincolnelectric.com/registerAuthorized Service and Distributor Locator:www.lincolnelectric.com/locatorNeed Help? Call 1.888.935.3877to talk to a Service RepresentativeHours of Operation:8:00 AM to 6:00 PM (ET) Mon. thru Fri.Save for future referenceDate PurchasedAfter hours?Use “Ask the Experts” at lincolnelectric.comA Lincoln Service Representative will contact youno later than the following business day.Code: (ex: 10859)For Service outside the USA:Email: globalservice@lincolnelectric.comSerial: (ex: U1060512345)IM10017-D Issue Date Aug- 13 Lincoln Global, Inc. All Rights Reserved.
THANK YOU FOR SELECTINGA QUALITY PRODUCT BYLINCOLN ELECTRIC.PLEASE EXAMINE CARTON AND EQUIPMENT FORDAMAGE IMMEDIATELYWhen this equipment is shipped, title passes to the purchaserupon receipt by the carrier. Consequently, claims for materialdamaged in shipment must be made by the purchaser against thetransportation company at the time the shipment is received.SAFETY DEPENDS ON YOULincoln arc welding and cutting equipment is designed and builtwith safety in mind. However, your overall safety can be increasedby proper installation . and thoughtful operation on your part.DO NOT INSTALL, OPERATE OR REPAIR THIS EQUIPMENTWITHOUT READING THIS MANUAL AND THE SAFETYPRECAUTIONS CONTAINED THROUGHOUT. And, most importantly,think before you act and be careful.WARNINGThis statement appears where the information must be followedexactly to avoid serious personal injury or loss of life.CAUTIONThis statement appears where the information must be followedto avoid minor personal injury or damage to this equipment.KEEP YOUR HEAD OUT OF THE FUMES.DON’T get too close to the arc.Use corrective lenses if necessaryto stay a reasonable distanceaway from the arc.READ and obey the Safety DataSheet (SDS) and the warning labelthat appears on all containers ofwelding materials.USE ENOUGH VENTILATION orexhaust at the arc, or both, tokeep the fumes and gases fromyour breathing zone and the general area.IN A LARGE ROOM OR OUTDOORS, natural ventilation may beadequate if you keep your head out of the fumes (See below).USE NATURAL DRAFTS or fans to keep the fumes awayfrom your face.If you develop unusual symptoms, see your supervisor.Perhaps the welding atmosphere and ventilation systemshould be checked.WEAR CORRECT EYE, EAR &BODY PROTECTIONPROTECT your eyes and face with welding helmetproperly fitted and with proper grade of filter plate(See ANSI Z49.1).PROTECT your body from welding spatter and arcflash with protective clothing including woolenclothing, flame-proof apron and gloves, leatherleggings, and high boots.PROTECT others from splatter, flash, and glarewith protective screens or barriers.IN SOME AREAS, protection from noise may be appropriate.BE SURE protective equipment is in good condition.Also, wear safety glasses in work areaAT ALL TIMES.SPECIAL SITUATIONSDO NOT WELD OR CUT containers or materials which previouslyhad been in contact with hazardous substances unless they areproperly cleaned. This is extremely dangerous.DO NOT WELD OR CUT painted or plated parts unless specialprecautions with ventilation have been taken. They can releasehighly toxic fumes or gases.Additional precautionary measuresPROTECT compressed gas cylinders from excessive heat,mechanical shocks, and arcs; fasten cylinders so they cannot fall.BE SURE cylinders are never grounded or part of anelectrical circuit.REMOVE all potential fire hazards from welding area.ALWAYS HAVE FIRE FIGHTING EQUIPMENT READY FORIMMEDIATE USE AND KNOW HOW TO USE IT.Safety 01 of 04 - 5/16/2018
SAFETYSECTION A:WARNINGSCALIFORNIA PROPOSITION 65 WARNINGSWARNING: Breathing diesel engine exhaustexposes you to chemicals known to the Stateof California to cause cancer and birth defects,or other reproductive harm. Always start and operate the engine in awell-ventilated area. If in an exposed area, vent the exhaust to the outside. Do not modify or tamper with the exhaust system. Do not idle the engine except as necessary.For more information go towww.P65 warnings.ca.gov/dieselWARNING: This product, when used for welding orcutting, produces fumes or gases which containchemicals known to the State of California to causebirth defects and, in some cases, cancer. (CaliforniaHealth & Safety Code § 25249.5 et seq.)WARNING: Cancer and Reproductive Harmwww.P65warnings.ca.govARC WELDING CAN BE HAZARDOUS. PROTECTYOURSELF AND OTHERS FROM POSSIBLE SERIOUSINJURY OR DEATH. KEEP CHILDREN AWAY.PACEMAKER WEARERS SHOULD CONSULT WITHTHEIR DOCTOR BEFORE OPERATING.Read and understand the following safety highlights. Foradditional safety information, it is strongly recommendedthat you purchase a copy of “Safety in Welding & Cutting ANSI Standard Z49.1” from the American Welding Society,P.O. Box 351040, Miami, Florida 33135 or CSA StandardW117.2-1974. A Free copy of “Arc Welding Safety” bookletE205 is available from the Lincoln Electric Company,22801 St. Clair Avenue, Cleveland, Ohio 44117-1199.BE SURE THAT ALL INSTALLATION, OPERATION,MAINTENANCE AND REPAIR PROCEDURES AREPERFORMED ONLY BY QUALIFIED INDIVIDUALS.FOR ENGINE POWEREDEQUIPMENT.1.a. Turn the engine off before troubleshootingand maintenance work unless themaintenance work requires it to be running.with hot engine parts and igniting. Do not spill fuel when fillingtank. If fuel is spilled, wipe it up and do not start engine untilfumes have been eliminated.1.d. Keep all equipment safety guards, coversand devices in position and in good repair.Keep hands, hair, clothing and tools awayfrom V-belts, gears, fans and all othermoving parts when starting, operating orrepairing equipment.1.e. In some cases it may be necessary to remove safety guards toperform required maintenance. Remove guards only whennecessary and replace them when the maintenance requiringtheir removal is complete. Always use the greatest care whenworking near moving parts.1.f. Do not put your hands near the engine fan. Do not attempt tooverride the governor or idler by pushing on the throttle controlrods while the engine is running.1.g. To prevent accidentally starting gasoline engines while turningthe engine or welding generator during maintenance work,disconnect the spark plug wires, distributor cap or magneto wireas appropriate.1.h. To avoid scalding, do not remove the radiatorpressure cap when the engine is hot.ELECTRIC ANDMAGNETIC FIELDS MAYBE DANGEROUS2.a. Electric current flowing through any conductorcauses localized Electric and Magnetic Fields (EMF).Welding current creates EMF fields around welding cablesand welding machines2.b. EMF fields may interfere with some pacemakers, andwelders having a pacemaker should consult their physicianbefore welding.2.c. Exposure to EMF fields in welding may have other health effectswhich are now not known.2.d. All welders should use the following procedures in order tominimize exposure to EMF fields from the welding circuit:2.d.1. Route the electrode and work cables together - Securethem with tape when possible.2.d.2. Never coil the electrode lead around your body.2.d.3. Do not place your body between the electrode and workcables. If the electrode cable is on your right side, thework cable should also be on your right side.2.d.4. Connect the work cable to the workpiece as close as possible to the area being welded.2.d.5. Do not work next to welding power source.1.b. Operate engines in open, well-ventilated areas or vent the engineexhaust fumes outdoors.1.c. Do not add the fuel near an open flame weldingarc or when the engine is running. Stop theengine and allow it to cool before refueling toprevent spilled fuel from vaporizing on contactSafety 02 of 04 - 5/16/2018
SAFETYELECTRIC SHOCKCAN KILL.ARC RAYS CAN BURN.3.a. The electrode and work (or ground) circuits areelectrically “hot” when the welder is on. Donot touch these “hot” parts with your bare skin or wet clothing.Wear dry, hole-free gloves to insulate hands.4.a.Use a shield with the proper filter and cover plates to protect youreyes from sparks and the rays of the arc when welding orobserving open arc welding. Headshield and filter lens shouldconform to ANSI Z87. I standards.3.b. Insulate yourself from work and ground using dry insulation.Make certain the insulation is large enough to cover your full areaof physical contact with work and ground.4.b.Use suitable clothing made from durable flame-resistant materialto protect your skin and that of your helpers from the arc rays.4.c.Protect other nearby personnel with suitable, non-flammablescreening and/or warn them not to watch the arc nor exposethemselves to the arc rays or to hot spatter or metal.In addition to the normal safety precautions, ifwelding must be performed under electricallyhazardous conditions (in damp locations or whilewearing wet clothing; on metal structures such asfloors, gratings or scaffolds; when in crampedpositions such as sitting, kneeling or lying, if thereis a high risk of unavoidable or accidental contactwith the workpiece or ground) use the followingequipment: Semiautomatic DC Constant Voltage (Wire) Welder. DC Manual (Stick) Welder. AC Welder with Reduced Voltage Control.3.c. In semiautomatic or automatic wire welding, the electrode,electrode reel, welding head, nozzle or semiautomatic weldinggun are also electrically “hot”.3.d. Always be sure the work cable makes a good electricalconnection with the metal being welded. The connection shouldbe as close as possible to the area being welded.3.e. Ground the work or metal to be welded to a good electrical (earth)ground.3.f. Maintain the electrode holder, work clamp, welding cable andwelding machine in good, safe operating condition. Replacedamaged insulation.3.g. Never dip the electrode in water for cooling.3.h. Never simultaneously touch electrically “hot” parts of electrodeholders connected to two welders because voltage between thetwo can be the total of the open circuit voltage of bothwelders.3.i. When working above floor level, use a safety belt to protectyourself from a fall should you get a shock.3.j. Also see Items 6.c. and 8.FUMES AND GASESCAN BE DANGEROUS.5.a. Welding may produce fumes and gaseshazardous to health. Avoid breathing thesefumes and gases. When welding, keep your head out of the fume.Use enough ventilation and/or exhaust at the arc to keep fumesand gases away from the breathing zone. When weldinghardfacing (see instructions on container or SDS)or on lead or cadmium plated steel and othermetals or coatings which produce highly toxicfumes, keep exposure as low as possible andwithin applicable OSHA PEL and ACGIH TLV limitsusing local exhaust or mechanical ventilationunless exposure assessments indicate otherwise.In confined spaces or in some circumstances,outdoors, a respirator may also be required.Additional precautions are also required whenweldingon galvanized steel.5. b. The operation of welding fume control equipment is affected byvarious factors including proper use and positioning of theequipment, maintenance of the equipment and the specificwelding procedure and application involved. Worker exposurelevel should be checked upon installation and periodicallythereafter to be certain it is within applicable OSHA PEL andACGIH TLV limits.5.c. Do not weld in locations near chlorinated hydrocarbon vaporscoming from degreasing, cleaning or spraying operations. Theheat and rays of the arc can react with solvent vapors to formphosgene, a highly toxic gas, and other irritating products.5.d. Shielding gases used for arc welding can displace air and causeinjury or death. Always use enough ventilation, especially inconfined areas, to insure breathing air is safe.5.e. Read and understand the manufacturer’s instructions for thisequipment and the consumables to be used, including theSafety Data Sheet (SDS) and follow your employer’s safetypractices. SDS forms are available from your weldingdistributor or from the manufacturer.5.f. Also see item 1.b.Safety 03 of 04 - 5/16/2018
SAFETYWELDING AND CUTTINGSPARKS CAN CAUSEFIRE OR EXPLOSION.6.a. Remove fire hazards from the welding area. Ifthis is not possible, cover them to prevent the welding sparksfrom starting a fire. Remember that welding sparks and hotmaterials from welding can easily go through small cracks andopenings to adjacent areas. Avoid welding near hydraulic lines.Have a fire extinguisher readily available.6.b. Where compressed gases are to be used at the job site, specialprecautions should be used to prevent hazardous situations.Refer to “Safety in Welding and Cutting” (ANSI Standard Z49.1)and the operating information for the equipment being used.6.c. When not welding, make certain no part of the electrode circuit istouching the work or ground. Accidental contact can causeoverheating and create a fire hazard.6.d. Do not heat, cut or weld tanks, drums or containers until theproper steps have been taken to insure that such procedureswill not cause flammable or toxic vapors from substances inside.They can cause an explosion even though they have been“cleaned”. For information, purchase “Recommended SafePractices for the Preparation for Welding and Cutting ofContainers and Piping That Have Held Hazardous Substances”,AWS F4.1 from the American Welding Society(see address above).6.e. Vent hollow castings or containers before heating, cutting orwelding. They may explode.6.f. Sparks and spatter are thrown from the welding arc. Wear oil freeprotective garments such as leather gloves, heavy shirt, cufflesstrousers, high shoes and a cap over your hair. Wear ear plugswhen welding out of position or in confined places. Always wearsafety glasses with side shields when in a welding area.6.g. Connect the work cable to the work as close to the welding areaas practical. Work cables connected to the building framework orother locations away from the welding area increase thepossibility of the welding current passing through lifting chains,crane cables or other alternate circuits. This can create firehazards or overheat lifting chains or cables until they fail.6.h. Also see item 1.c.6.I. Read and follow NFPA 51B “Standard for Fire Prevention DuringWelding, Cutting and Other Hot Work”, available from NFPA, 1Batterymarch Park, PO box 9101, Quincy, MA 022690-9101.6.j. Do not use a welding power source for pipe thawing.CYLINDER MAY EXPLODE IFDAMAGED.7.a. Use only compressed gas cylinders containingthe correct shielding gas for the process usedand properly operating regulators designed forthe gas and pressure used. All hoses, fittings,etc. should be suitable for the application andmaintained in good condition.7.b. Always keep cylinders in an upright position securely chained toan undercarriage or fixed support.7.c. Cylinders should be located: Away from areas where they may be struck or subjectedto physical damage. A safe distance from arc welding or cutting operationsand any other source of heat, sparks, or flame.7.d. Never allow the electrode, electrode holder or any otherelectrically “hot” parts to touch a cylinder.7.e. Keep your head and face away from the cylinder valve outletwhen opening the cylinder valve.7.f. Valve protection caps should always be in place and hand tightexcept when the cylinder is in use or connected for use.7.g. Read and follow the instructions on compressed gas cylinders,associated equipment, and CGA publication P-l, “Precautions forSafe Handling of Compressed Gases in Cylinders,” available fromthe Compressed Gas Association, 14501 George Carter WayChantilly, VA 20151.FOR ELECTRICALLYPOWERED EQUIPMENT.8.a. Turn off input power using the disconnectswitch at the fuse box before working onthe equipment.8.b. Install equipment in accordance with the U.S. National ElectricalCode, all local codes and the manufacturer’s recommendations.8.c. Ground the equipment in accordance with the U.S. NationalElectrical Code and the manufacturer’s recommendations.Refer tohttp://www.lincolnelectric.com/safetyfor additional safety information.Safety 04 of 04 - 5/16/2018
viTABLE OF CONTENTSPageInstallation.Section ATechnical Specifications .A-1Safety Precautions .A-2Machine Grounding .A-2Spark Arrester .A-2Towing.A-2Vehicle Mounting.A-3Pre-Operation Engine Service.A-3Fuel, Oil, Battery Connections .A-3Welding Cable Connections .A-4 Angle of Operation .A-4Lifting, Additional Safety Precautions.A-4High Altitude Operation .A-4Muffler Outlet Pipe .A-4Location and Ventilation .A-5Stacking .A-5Connection of Wire Feeders .A-5Connection of Tig Module .A-5Additional Safety Precautions .A-5Welding Operation Output, Auxiliary Power Receptacles, and Plugs .A-6Motor Starting and Extension Cord Length Table .A-6Electrical Device Used with the Ranger 225 .A-7Auxiliary Power While Welding, Standby Power Connections .A-8Premises Wiring .A-9Operation.Section BSafety Precautions .B-1General Description.B-1Welder Controls Function and Operation .B-1Range, Polarity Control Switch and Fuel Consumption .B-2Start in/Shutdown Instructions .B-3 Starting the Engine.B-3Safety Precautions .B-3Stopping the Engine .B-3Break-In Period .B-3Welding Process .B-4Stick (Constant Current) Welding.B-4Scratch Start TIG (Constant Current) Welding .B-4Wire Feed Welding Processes (Constant Voltage) .B-5Arc Gouging .B-5Summary of Welding Processes .B-5Accessories .Section COptional Equipment .C-1Recommended Equipment .C-2Maintenance .Section DSafety Precautions .D-1Routine Engine Maintenance .D-1,D2Engine Adjustments.D-3Slip Rings .D-3Battery Maintenance .D-3Engine Maintenance Parts.D-3Troubleshooting .Section EHow to Use Troubleshooting Guide.E-1Troubleshooting Guide.E-2, E-3Wiring Diagrams, Connection Diagrams & Dimension Print.Section FParts List.P-618vi
A-1A-1INSTALLATIONTECHNICAL SPECIFICATIONS - RANGER 225 ( K2857-1)INPUT - GASOLINE orsepower2 cylinder4 CycleAir-CooledGasolineEngine.Aluminum Alloywith Cast IronLiners,ElectronicIgnitionOperatingSpeed (RPM)Displacementcu. in.(cu.cm.)High Idle 370023 HP @3600 RPMFull Load 350041.1(674)Low Idle lectric StartFuel:Group 5812 Gal (45.4 L)BatteryLubricating Oil:(435 cold 2.0 Qts. (1.9 L)CrankingAmps)RATED OUTPUT @ 104 F (40 C)- WELDERWelding OutputDC Constant Current 225A/25V/40%DC Constant Current 210A / 25V / 100%DC Constant Voltage 200A / 20V / 100%RATED OUTPUT @ 104 F (40 C)- GENERATORAuxiliary Power 19,000 Watts Continuous, 60 Hz AC10,500 Watts Peak, 60 Hz AC120/240 VoltsRECEPTACLES AND CIRCUIT BREAKERSRECEPTACLESAUXILIARY POWER CIRCUIT BREAKER BATTERY CHARGING CIRCUIT BREAKER(2) 120VAC Duplex (5-20R)(1) 120/240VAC Dual VoltageFull KVA (14-50R)Two 20AMP for Two Duplex Receptacle(1) 40AMP for Dual Voltage (2-pole)20AMP for Engine BatteryCharging CircuitPHYSICAL DIMENSIONSHEIGHTWIDTHDEPTH30.00** in. 21.50 in 42.25 in. 762.0 mm546.0 mm1073.0 mm** Top of enclosure, add 6.00”(152mm) for exhaust.MODEL / WEIGHTCodes 11797 and below514 lbs. (233kg.) Code 12093523 lbs. (237kg.) ENGINE COMPONENTSLUBRICATIONFull Pressurewith Full Flow Filter5% RegulationVALVE LIFTERSHydraulicAIR CLEANERENGINE IDLERDual Element1Automatic IdlerFUEL SYSTEMMechanical Fuel PumpAdditional electric fuel lift pumpon K2382-4.GOVERNORMechanical GovernorMUFFLERENGINE PROTECTIONLow noise Muffler: Top outlet Shutdown on low oilcan be rotated. Made from pressure.long life, aluminized steel.Output rating in watts is equivalent to volt - amperes at unity factor.Output voltage is within /-10% at all loads up to rated capacity.When welding available auxiliary power will be reduced.RANGER 225
A-2A-2INSTALLATIONSAFETY PRECAUTIONSWARNINGDo not attempt to use this equipment until youhave thoroughly read the engine manufacturer’smanual supplied with your welder. It includesimportant safety precautions, detailed enginestarting, operating and maintenance instructions,and parts ---------------------------ELECTRIC SHOCK can kill. Do not touch electrically live parts orelectrode with skin or wet clothing. Insulate yourself from work andground. Always wear dry insulating ----------------------------ENGINE EXHAUST can kill. Use in open, well ventilated areas orvent exhaust -----------------------------MOVING PARTS can injure. Do not operate with doors open orguards off. Stop engine before servicing. Keep away from moving ----------------------------See additional warning information atfront of this operator’s ---------------MACHINE GROUNDINGBecause this portable engine driven welder or generator creates it’s own power, it is not necessary to connect it’s frame to an earth ground, unless the machineis connected to premises wiring (your home, shop,etc.).WARNINGWhen this welder is mounted on a truck or trailer, it’sframe must be electrically bonded to the metal frameof the vehicle. Use a #8 or larger copper wire connected between the machine grounding stud and theframe of the vehicle.Where this engine driven welder is connected topremises wiring such as that in your home or shop, it’sframe must be connected to the system earth ground.See further connection instructions in the section entitled “Standby Power Connections”, as well as the article on grounding in the latest National Electrical Codeand the local code.In general, if the machine is to be grounded, it shouldbe connected with a #8 or larger copper wire to a solidearth ground such as a metal water pipe going intothe ground for at least ten feet and having no insulated joints, or to the metal framework of a buildingwhich has been effectively grounded. The NationalElectrical Code lists a number of alternate means ofgrounding electrical equipment. A machine groundingstud marked with the symbol is provided on thefront of the welder.SPARK ARRESTERSome federal, state, or local laws may require thatgasoline engines be equipped with exhaust sparkarresters when they are operated in certain locationswhere unarrested sparks may present a fire hazard.The standard muffler included with this welder doesnot qualify as a spark arrester. When required by localregulations, the K1898-1 spark arrester must beinstalled and properly maintained.CAUTIONAn incorrect arrester may lead to damage to theengine or adversely affect ----------------------------------TOWINGTo prevent dangerous electric shock, other equipment to which this engine driven welder suppliespower must: be grounded to the frame of the welder using agrounded type plug, or be double insulated.Do not ground the machine to a pipe that carriesexplosive or combustible -------------------------------The recommended trailer for use with this equipmentfor road, in-plant and yard towing by a vehicle(1) isLincoln’s K2635-1. If the user adapts a non-Lincolntrailer, he must assume responsibility that the methodof attachment and usage does not result in a safetyhazard nor damage the welding equipment. Some ofthe factors to be considered are as follows:1. Design capacity of trailer vs. weight of Lincolnequipment and likely additional attachments. 2. Proper support of, and attachment to, the base ofthe welding equipment so there will be no unduestress to the framework.RANGER 225
INSTALLATIONA-33. Proper placement of the equipment on the trailer toinsure stability side to side and front to back whenbeing moved and when standing by itself whilebeing operated or serviced.4. Typical conditions of use, i.e., travel speed; roughness of surface on which the trailer will be operated;environmental conditions.5. Conformance with federal, state and local laws(1)A-3FUELFill the fuel tank with clean, fresh, lead-free gasoline.Observe fuel gauge while filling to prevent overfilling.Stop fueling once the fuel gauge reads full. Do not topoff tank. Be sure to leave filler neck empty to allowroom for expansion.(1) Consult applicable federal, state and local laws regarding specificrequirements for use on public highways.VEHICLE MOUNTINGFULLWARNINGImproperly mounted concentrated loads maycause unstable vehicle handling and tires or othercomponents to fail. Only transport this Equipment on serviceablevehicles which are rated and designed for suchloads. Distribute, balance and secure loads so vehicleis stable under conditions of use. Do not exceed maximum rated loads for components such as suspension, axles and t
2.d.1. Route the electrode and work cables together - Secure them with tape when possible. 2.d.2. Never coil the electrode lead around your body. 2.d.3. Do not place your body between the electrode and work cables. If the electrode cable is on your right side, the work cable should also be on your right side. 2.d.4.