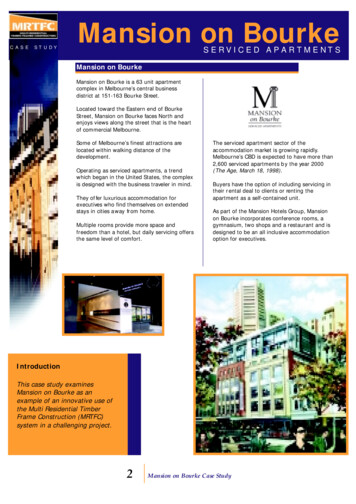
Transcription
C A S EST U DYMansion on BourkeS E RV I C E D A P A R T M E NT SMansion on BourkeMansion on Bourke is a 63 unit apartmentcomplex in Melbourne’s central businessdistrict at 151-163 Bourke Street.Located toward the Eastern end of BourkeStreet, Mansion on Bourke faces North andenjoys views along the street that is the heartof commercial Melbourne.Some of Melbourne’s finest attractions arelocated within walking distance of thedevelopment.Operating as serviced apartments, a trendwhich began in the United States, the complexis designed with the business traveler in mind.They of fer luxurious accommodation forexecutives who find themselves on extendedstays in cities a way from home.Multiple rooms provide more space andfreedom than a hotel, but daily servicing offersthe same level of comfort.The serviced apartment sector of theac commodation market is growing rapidly.Melbourne’s CBD is expected to have more than2,600 serviced apartments b y the year 2000(The Age, March 18, 1998).Buyers have the option of including servicing intheir r ental deal to clients or renting theapartment as a self-contained unit.As part of the Mansion Hotels Group, Mansionon Bourke incorporates conference rooms, agymnasium, two shops and a restaurant and isdesigned to be an all inclusive accommodationoption for executives.IntroductionThis case study examinesMansion on Bourke as anexample of an innovative use ofthe Multi Residential TimberFrame Construction (MRTFC)system in a challenging project.2Mansion on Bourke Case Study
The SiteThe ex-retail building that was tobecome Mansion on Bourke,consisted of an existing four storeystructure built with concrete,timber and steel.Three new levels were addedusing the MRTFC system.Being bor dered b y other buildingson three sides with weekend-onlyaccess for cranes from the fourthside, supplying building materialsto the roof for the additional threefloors would be a challenge.Timber presented itself as thelogical choice. Its relative lightweight and small section sizesmeant that it was ideal for thisproject as the material could be‘carried’ in as required, without the need fordifficult cr anage.The MRTFC system w as then incorporated inthe design of the apartments, enabling thespeed and ease of use of timber, whi lst stillmeeting the acoustic requirements necessaryfor this type of building.Building DesignDesigned by Reed HLS Architects in association withBarry Gale Engineers, the Class 2 MRTFC complex(sole-occupancy, self-contained, separate ownershipunits) was built using timber framing to achieve thesound and fire ratings requir ed by the Building Code ofAustralia.Timber was chosen as the ideal building material dueto access and design considerations, but was also themost cost competitive.The project designers considered three options for thebuilding extensions;1. timber construction2. combined timber and steel and3. concrete.Concrete was excluded due to the load capacitylimitations of the existing footings.Of the timber framed and timber and steel combinedoptions, timber construction proved to be slightlycheaper.Some steel sections wer e used in the building,however. Steel columns (90x90mm hollow sections)were used in some wall construction, particularly onthe inside of the Bourke Street façade. These wallsconsisted of a conventional glass/steel curtain wallsystem.The completed building is around 95% timber framed(with concrete lift and stair wells).3Mansion on Bourke Case Study
Performance Based DesignMulti-residential timber framed construction(MRTFC) was introduced to Australia viaAmendment Nº 7 to the Building Code ofAustral ia (BCA 90) in 1994.To el iminate the need to then fire-rate thesewalls, the floor joists were sized to satisfystrength requirements, supporting the wall in theevent of a fire.This amendment allowed MRTFC to be used inClass 1 construction, Class 2 up to three storeys(or four storeys over a lower level of car parkingconstructed of masonry or concrete) and amaximum of twostoreys for Class3 buildings.In this si tuation, the floor would sag excessively,but still satisfy strength and stabi lity requirementsand provide a one hour fire rating.Design Copyright 1997 Reed HLS Architects Suite 4/135 Sturt St, Southbank, VictoriaTo achieve lateralstability, a model w asused to estimate thenumber of w alls thatwould be lost in atypical fire. Thisinformation was usedto ensure thebuilding could remainstanding in a fire.However, as aresult of therelease of thenew performancebased BuildingCode of Austral iain 1996 (BCA 96)the possibilitiesfor MRTFCdevelopmentsmay now beexpanded invarious ways,such as increasing the number of storeys orsimply varying the methods of construction,provided the appropriate levels of life safety aremaintained*.The designers of Mansion on Bourke consultedPeter Luzinat and Partners P/L B uildingSurveyors from the first stage of design toensure that some of the innovative designsolutions they sought forthe building wouldcomply with BCA 96.The calculationswere then utilised toestablish which wallsrequired bracingwithout the need tofire rate them.This kind of design innovation and flexibility is oneof the major benefits of using timber inmulti-r esidential construction.Fire RatingThe one hour fire rating of internal walls w as alsoa result of the flexibility of performance baseddesign.A Class 2 building of thistype would ordinari lyrequire a floor/ceiling firerating of one and a halfhours.Structural DesignOne such innovationwas the approach todeflection control in thefloor design.Load bearing walls werespaced at 5-6m centres,requiring overly deep floor joists to maintaindeflection control.The final solution was to use previously nonload bearing wal ls (non-party walls) as supportfor the floor joists.*However, in a building ofless than 25 metres inheight, the BCA does notrequire an internalsprinkler system for aClass 2 building. By installing one throughout thecomplex, a reduction in fire rating was permitted.Additionally, all apartment doors were smokesealed to prevent smoke entering apartmentsfrom corridors and smoke detection systemscombined with early warning speaker systems ineach apartment, also assisted in permitting areduction of the fire rating necessary for thefloor/ceilings and wal ls.Refer to Gaining Approval for MRTFC Projects Under BCA 96 [Information Bulletin #2] for further detai l - see back page for a vailability.4Mansion on Bourke Case Study
Wall ConstructionOne of the most impressiv e benefits of using MRTFC is the ease with which soundtransmission requir ements can match and even exceed that achieved b y concreteand masonry.Load bearing walls between apartments were fire and acoustically rated.They were constructed with asingle stud timber frame of90mm top and bottom platesand 90mm studs with one layerof 6mm fibre cement sheet andone layer of 13mm fire gradeplasterboard on each side.This achieved an STC of 45 andan FRL of 60/60/60.Between service areas ofapartments (e.g. bathroomExample of a typical single stud MRTFC wall detailabutting bedroom in the nextapartment), an STC of 50 andan FRL of 60/60/60 with impact resistance was achieved b y using a staggered studwall frame (180mm plates) with two sheets of 13mm fire grade plasterboard oneach side.ConclusionAs a relatively new method ofconstruction in Austral ia,MRTFC is rapidly gainingwidespread ac ceptance andbeing incorporated intoincreasingly varied structuresright around the country.As with all such systems,evolution and dev elopmentresults from incr easing useand the performance basedBCA 96 is allowing new andinnovative design solutions tobe incorporated into MRTFCprojects.Mansion on Bourke benefi tedfrom the use of MRTFCthrough;·The use of timber;- It’s light weight made i tthe only real option whenexisting building footingswere to be consider ed- It was cheaper whencompared to combinedtimber and steelconstruction and concreteconstruction- Restricted access to thebuilding leant itself to atimber frame’s ability to beconstructed on site andthe portability of thecomponents·The design flexibilityoffered b y the MRTFCsystem and theperformance based B CA96 enabling creativesolutions that saved timeand money duringconstruction and stillmeeting all of the fire andsound requirements.All external walls of the building are required to be firerated to an FRL of 90/90/90.This was achieved b y using 100mm thick‘Hebel’ block laid in mortar with a 50mmcavity and 90mm f ramed timber wall withtwo layers of 13mm flush jointed firegrade plasterboar d on the insideand one layer of 10mm flushjointed plasterboard on allexposed surfaces.The vapour barrier andinfill consisted of52mm polyesterpartition batts.In combination, timber andMulti Residential TimberFramed Construction enabledthe developers of Mansion onBourke to construct a luxuryapartment complex on adifficult si te with cost and timesavings and still satisfy orexceed the r equirements ofbuilding codes andregulations.5Mansion on Bourke Case Study
MRTFC SUPPORT MATERIALAvailable from your State and National timber associations is acompr ehensive suite of manuals that detail timber wall and floor/ceiling construction systems for MRTFC buildings. Produced by theAustralian timber industry, these manuals provide a complete guidefor designers, local authori ties and builders on MRTFC construction tocompy with the Building Code of Austral ia.manualsSince the intr oduction of MRTFC into the BCA in 1994, the system has been in aconstant state of development as materials have changed and improved and differ entconstruction methods have been developed. Industry has produced data sheets toreflect the development of alternative joint details as well as a guide to approval ofprojects under the performance based BCA 96. Addi tional data sheets are current ly inproduction.data sheetsA 21 minute video has been produced by the National Timber Development Council topromote the use of MRTFC. The video comprises two parts; PART A - Introduction toMRTFC outlines the benefits and applications of the system featuring completedprojects and interviews with engineers and builders about their experiences wi thMRTFC. PART B - Building with MRTFC looks at the detail - discussing some of themore technical aspects of the MRTFC building system.videoAnd as part of the continuing effort by timber industry associations to provide timber users with the mostup to date inf ormation, an MRTFC newsletter is being produced quarterly to report on developments ofthe system. In addition, several other case studies have been produced to showcase some of theprojects that have already been constructed using MRTFC technology, including; Couran Cove Resort(Qld), Kensington Banks (Vic), Wickham Terrace (NSW) and Lutwyche (Qld).case studiesFor further information on MRTFC, contact:NEW SOUTH WALESTimber Development Association of NSW LtdTel: (02) 9360 3088 Fax: (02) 9360 3464TASMANIATasmanian Timber Promotion BoardTel: (03) 6224 1033 Fax: (03) 6224 1030QUEENSLANDTimber Research And Development Advisory Council of Qld (TRADAC)Tel: (07) 3358 1400 Fax: (07) 3358 1411WESTERN AUSTRALIATimber Promotion Council (WA)Tel: (08) 9380 4411 Fax: (08) 93680 4477SOUTH AUSTRALIATimber Development Association of SATel: (08) 8297 0044 Fax: (08) 8297 2772VICTORIATimber Advisory CentreTel: (03) 9877 2000 Fax: (03) 9877 6663Supplementary information:PINE AUSTRALIA830 High Street, Kew East, Victoria, 3102Freecall 1800 00 PINE (7463)PLYWOOD ASSOCIATION OF AUSTRALIA3 Dunlop Street, Newstead, Queensland 4006(07) 3854 1228This case study was produced with support f rom the Forest and Wood Products Research and Development Corporation Copyright - FWPRDC 1999Produced by Pine Australia - August 19996Mansion on Bourke Case Study
'Hebel' block laid in mortar with a 50mm cavity and 90mm framed timber wall with two layers of 13mm flush jointed fire grade plasterboard on the inside and one layer of 10mm flush jointed plasterboard on all exposed surf aces. The vapour barrier and infill consisted of 52mm polyester partition batts. Conclusion As a relatively new method of