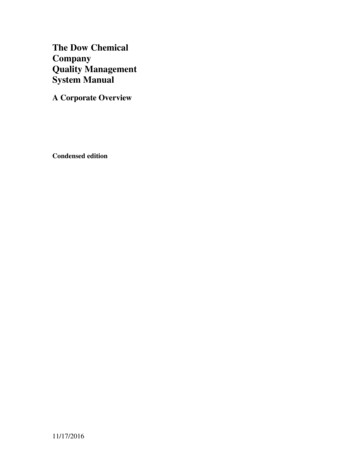
Transcription
The Dow ChemicalCompanyQuality ManagementSystem ManualA Corporate OverviewCondensed edition11/17/2016
Table of Contents1. Introduction2. Company Overview3. The Dow Quality ManagementSystem11/17/2016
IntroductionDow’s Quality PolicyThis manual describes, in a condensedformat, The Quality ManagementSystem of The Dow Chemical Company.It includes: Company overviewDow’s Quality PolicyResources and Commitment toQualityOverview of the QualityManagement System ElementsThe manual has two purposes: It briefly outlines the company’squality standards for use by Dowpeople. It provides an easy-to-followoverview of Dow’s qualitysystem for use by customers andother interested audiences.An Overview of DowDow combines the power of science andtechnology to passionately innovatewhat is essential to human progress. TheCompany is driving innovations thatextract value from the intersection ofchemical, physical and biologicalsciences to help address many of theworld's most challenging problems suchas the need for clean water, clean energygeneration and conservation, andincreasing agricultural y-leading portfolio of specialtychemical,advancedmaterials,agrosciences and plastics businessesdelivers a broad range of technologybased products and solutions.Further information may be obtained atThe Dow Chemical Company web page.11/17/2016Quality Performance is acommitment to excellence byeach Dow employee.It is achieved through teamworkand continual improvement.We are dedicated to being a leaderin providing quality products andservices that meet or exceed therequirements of our customersand all of our key stakeholders.Quality management plays an importantrole by ensuring that the company canreliably produce and deliver the qualityproducts and services expected by itscustomers.Customer FocusDow’s product and service qualityrequirements are defined by itscustomers. Dow works closely with itscustomers to understand their businessesand their expectations.This closeworking relationship helps Dow to bettermeet its customers’ expectations todayand to anticipate and meet their futureneeds.Global Quality System CorporateStructureDow has established an infrastructureand support organization to assistbusiness management in globallyimplementing the corporate QualityManagement System in a consistent andcoordinated manner. Under the Directorfor Manufacturing Support Services, theProduct Quality Director leads the
strategy for Dow’s Quality ManagementSystem throughout the company.The company has established a globalBusiness Quality Leaders network.These leaders are responsible fordeveloping and implementing qualitystrategies that address the needs of theirmarkets, whether it is in supplying bulkquantities of basic chemicals or smallvolumes of highly specialized materials.The Business Quality Leaders areaccountable for the implementation ofthe systems, policies and standards thatensure quality products and services aredelivered to Dow’s customers. Theleaders monitor the performance of thesystem and use data to driveimprovement opportunities.Continuous ImprovementDow has embraced a policy ofContinuous Improvement and utilizes anumber of key processes and tools toensure that Continuous Improvement is away of life for its employees.Dow employs Six Sigma methodologyfor: data-based decision making identifying and addressing theroot causes of a problem tracking results sustaining the gains long termJoining with Six Sigma is LEAN, aContinuous Improvement philosophyand mindset that focuses on value asperceived by the external customer.Dow’s emphasis on reliability is throughour Highly Reliable Organizationprogram, focused on driving fewerunplanned events.11/17/2016Continuous improvement of Dow’smanufacturing processes is guided bythe business expertise centers and theiruse of the Technology Implementationfor Competitive Advantage (TICA)process for aligning technologyimprovements with global businessstrategies.Quality Measurement SystemsDowhasestablishedqualitymeasurement systems to evaluate itsprogressincontinuousqualityimprovement. Some of the tools used tomonitor progress in each businessinclude external and internal customersurveys, auditing, organizational selfassessments, performance metrics, andstatistical tools.Employee Involvement / TeamworkAll Dow people play important roles inquality. A key value in Dow’s strategy isRespect for People, which states that“the employees of Dow are the engine ofvalue creation; our imagination,determination and dedication areessential to growth. We will work tocelebrate and reward the uniquebackgrounds, viewpoints, skills, andtalents of everyone at Dow. Respect forpeople is measured by how we includeand treat each other, by the contributionsthat flow from our diversity, by theproductivity of our relationships, and bya job well done, no matter what the job. Our customers are our partners increating value; their loyalty isour greatest reward.
Our communities are ourneighbors; their acceptance of usis vital to our ability to operate.Our shareholders are thebeneficiaries of our success; theirongoing commitment to us isbased on returning to themsuperior profits over time.Our respect for people alsoincludes the consumers whoselives we touch. We will strive toanswer people's most vital needs:forfood,water,shelter,transportation, communication,health and medicine.”To foster an environment whereinvolvement, continuous improvement,andteamwork(includingcrossfunctional teamwork) flourish, managersare encouraged to: treat employees as valued teammembers; actively solicit ideas on problemsand solutions from all people inthe work group; remove barriers as identified byemployees; empower people to makedecisionsandimplementsolutions; push decision making down tothe lowest possible level; collaborate with the entire workgroup to develop a mission.Responsible Care Dow has a long-standing commitment tosafety, health and the environment. Thecompany is committed to theResponsible Care initiative -- acontinuing effort to improve the11/17/2016chemical industry’s health, safety andenvironmental performance.The Dow Quality Management SystemPurposeEnsuring quality is a multi-functionaleffort covering many aspects of Dow’soperations. It is a continuous processinvolving: theidentificationanddocumentationofcustomerneeds; the development, manufactureand delivery of products andservices to meet those needsconsistently; feedback from the customer toassessthecompany’sperformance; action on the customer’sfeedbacktoimprovethecompany’s performance.Developed and endorsed by companymanagement,theDowQualityManagement System is part of anintegratedcorporatemanagementsystem, encompassing the requirementsof numerous external standards andinternal company requirements. Dow’squality management system conforms, atminimum, to specified requirements ofinternational standards, like ISO 9001.Product quality is maintained throughwork process and quality architecturestandardization, and process control.Service quality covers all aspects ofcustomer transactions and is ensured bythe function that is providing the service.Both product and service qualitycharacteristics are agreed upon by Dowand the customer.
Quality LeadershipDow Leadership takes a visible andleading role in creating and sustainingthe quality management system, through Establishing core values,policies, directions, performanceexpectations, Communicating qualitydirections and values Obtaining feedback on thequality management system Identifying necessary productrealization and support processes Creating an environmentencouraging the growth andinvolvement of people Providing necessaryinfrastructure and resources Focusing on customersatisfaction, and Continuous improvementDow Quality Leaders review themanagementsystemwithtopmanagement to ensure the overallsystem’scontinuingsuitability,adequacy and effectiveness, and toinitiate and/or leverage changes andimprovements.Resource ManagementDow ensures that the resources toachieve its objectives are identified andmade available, in part through Dow’swork processes for leading people,planning and allocating resources andmanaging information.Training and employee developmentsupports the company’s overall strategyto be a learning and continuouslyimproving organization.Requiredtraining is provided and documented to11/17/2016ensure the competence of all employeesin their intended roles.OperationDow’s product realization and supportwork processes are fully integrated andorganized to provide the capability tomeet the needs of our stakeholders.Management of Change is consistentlyapplied by employees to assure changesto our work processes, procedures,specifications have appropriate reviewsand approvals. Training is conducted,documentationisupdatedandappropriate communications, includingcustomer notifications, as appropriate.Dow’s Marketing and Sales organizationoperates to meet the needs of Dowcustomers and businesses, through anintegrated approach to Sales, Marketing,and Customer Service. g customer needs andensuringtheseexpectationsaretranslated into requirements for Dow’sproduct fulfillment processes areessential aspects ofwhat thisorganization does.All products and services sold by TheDow Chemical Company, as well as rawmaterials used in manufacturing andproduct packaging, are defined byspecifications.Specifications reflectDow’s commitment to the requirementsneeded at each stage of manufacture,distribution and redistribution to meetthe customers’ overall requirements forthe final, delivered productsDow’s Design and Developmentorganization has implemented processesto respond effectively and efficiently tothe needs of our customers. Dow’s
comprehensive Design and Developmentprocess considers many factors andcustomer inputs in designing products,including life cycle, safe handlingpractices, and product disposal.Dow’s Purchasing work process ensuresthat procured services and purchasedgoods are controlled to conform tospecifiedrequirements.Becausepurchased materials, goods and servicesdirectly affect the quality of Dow’sproducts and services, Dow has aprocess for developing an appropriatesupplier evaluation and developmentprocess to help ensure that all purchasedmaterials, goods and services conform toDow-specified requirements. Efforts aremade to establish a close workingrelationship and feedback system withsuppliers to ensure the highest value interms of quality.Dow’s processes for manufacturingproduct are carried out under controlledconditions.This includes detaileddescriptions of the products and processconditions, the means of testing ormonitoring the product to ensure that itmeets specified requirements at allstages of manufacture, and theconditions to ensure the productmaintains its integrity until delivery tothe customer.All Dow packagedproducts are labeled to ensure clear,unambiguous identification of theproduct and the party responsible for themanufacture of the product. They alsoidentify appropriate health, safety andenvironmentalinformationincompliance with all regulatory, /2016Performance EvaluationMeasuring performance, analyzing theresulting data through statisticaltechniques, prioritizing and initiatingimprovements is a process used by Dowto add value to its organization.Customer input, from a number ofcollection processes, is an important datasource both in understanding how wellwe are meeting current needs, and ingaining insight into how we can betterserve our customers in the future.In assessing our internal performance,each organization conducts periodicaudits and self-assessments to verify thatprocesses are consistent with specifiedrequirements and the intent of ourmanagement system.Processes for the planned monitoringand measuring of products areimplemented to ensure that specifiedrequirements are met throughout therealization process. Should products notconform to requirements, actions aretaken to ensure that the non-conformingmaterial is dealt with in an appropriatemanner.Dow’s process for corrective action isdesigned to ensure that issues areproperlycaptured,appropriateinvestigation is conducted - focused onpreventingrecurrence–andcommunication of the resolution tointerested stakeholders.Dow has created a culture ofempowering individuals to identifyopportunities for improvement, a systemfor capturing and evaluating theopportunities,andameansimplementing solutions.
Concluding RemarksDow has a comprehensive, integratedquality management system utilizing ourmajor work processes to enhancecustomer satisfaction by meeting orexceeding their expectations.11/17/2016
performance; action on the customer's feedback to improve the company's performance. Developed and endorsed by company management, the Dow Quality anagement System is part of an integrated corporate management system, encompassing the requirements of numerous external standards and internal company requirements.