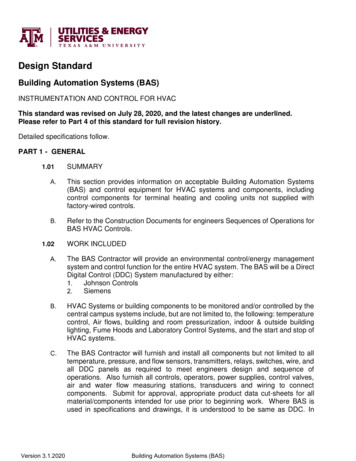
Transcription
Design StandardBuilding Automation Systems (BAS)INSTRUMENTATION AND CONTROL FOR HVACThis standard was revised on July 28, 2020, and the latest changes are underlined.Please refer to Part 4 of this standard for full revision history.Detailed specifications follow.PART 1 - GENERAL1.01SUMMARYThis section provides information on acceptable Building Automation Systems(BAS) and control equipment for HVAC systems and components, includingcontrol components for terminal heating and cooling units not supplied withfactory-wired controls.Refer to the Construction Documents for engineers Sequences of Operations forBAS HVAC Controls.1.02WORK INCLUDEDThe BAS Contractor will provide an environmental control/energy managementsystem and control function for the entire HVAC system. The BAS will be a DirectDigital Control (DDC) System manufactured by either:Johnson ControlsSiemensHVAC Systems or building components to be monitored and/or controlled by thecentral campus systems include, but are not limited to, the following: temperaturecontrol, Air flows, building and room pressurization, indoor & outside buildinglighting, Fume Hoods and Laboratory Control Systems, and the start and stop ofHVAC systems.The BAS Contractor will furnish and install all components but not limited to alltemperature, pressure, and flow sensors, transmitters, relays, switches, wire, andall DDC panels as required to meet engineers design and sequence ofoperations. Also furnish all controls, operators, power supplies, control valves,air and water flow measuring stations, transducers and wiring to connectcomponents. Submit for approval, appropriate product data cut-sheets for allmaterial/components intended for use prior to beginning work. Where BAS isused in specifications and drawings, it is understood to be same as DDC. InVersion 3.1.2020Building Automation Systems (BAS)
addition, when required, provide a complete installation of the Laboratory ControlSystem (LCS) completely integrated into the appropriate Campus BAS Software.All Controls, damper actuators, Valve actuators, shall be electronically controlled,no pneumatics of any type are allowed.The BAS Contractor shall provide Direct Digital Control (DDC) panels completewith all microprocessors, software, terminal strips, transducers, relays, andregulated power supply with battery backup at the mechanical room fieldequipment controllers and supervisory engines.The BAS Contractor shall furnish a HVAC Terminal Equipment Controller (TEC),electronic damper actuator(s), and electronic HW valve and actuator forinstallation on each VAV terminal unit and fan coil unit, as applicable, by theterminal equipment manufacturer. These DDC devices shall be delivered to themanufacturer's factory in sufficient time for the terminal equipment manufacturerto meet their scheduled delivery obligations.The BAS Contractor shall furnish all DDC LCS components, including TECs, LabSupply Air Terminal Units with reheat coils (duct mounted), General Exhaust AirTerminals, Fume Hood Exhaust Terminals, and all other associated controlscomponents required to meet the engineers design and sequence of operation.Installation of all air terminals shall be by the mechanical contractor.The BAS Contractor shall provide for each VAV box an inlet flow sensor suitablefor interfacing with a pressure transducer, and for VAV boxes and other terminalequipment as the design engineer requires. Also as required, any necessarydevices for proper operation to achieve full functionality as required by theengineers design and sequence of operation. The cost of mounting shall beincluded in the cost of the terminal equipment. All wiring and terminations relatedto the lab control system components shall be provided by the BAS contractor.The BAS Contractor shall provide for each TEC, a 24 vac, 40 va power source,and mount and connect these devices and the DDC controller as required forproper operation as required under this Section. All other wiring and terminationsrelated to the TEC shall be provided by the BAS contractor.Room temperature, CO2 sensors and humidity sensors and mounting plates shallbe provided and installed by the BAS Contractor.Temperature controls and non-DDC accessories that are standard catalogproducts as manufactured by Siemens Building Technologies, Inc. or JohnsonControls, Inc., will be acceptable. Industrial instrumentation supplied shall bestandard catalog products of Rosemount, Dwyer, Honeywell, Bristol, Foxboro,Leeds and Northrup, Taylor or Brown. All coordination and execution of workpertaining to the installation, service, and guarantee, under this Section of thespecifications, shall be the sole responsibility of the BAS Contractor.Version 3.1.2020Building Automation Systems (BAS)
All controls to be installed, calibrated and adjusted by trained instrumenttechnicians in the full-time employ of the BAS Subcontractor & low voltageelectrical subcontractor. The BAS Contractor will be responsible for all workperformed by their subcontractors.Submit engineering/wiring drawings and receive approval prior to beginning work.These drawings shall be submitted in a timely manner to provide sufficient timeto review drawings so as not to hold up the project.The DDC field panels will be located in mechanical rooms as shown on thedrawings. The BAS cabinets shall be labeled with a permanent labeled indicatingits name as shown in the control drawings All sensor and start/stop wiring will bebrought back to the panel responsible for controlling/monitoring themechanical/electrical equipment for which the sensor, start/stop wiring is directlyrelated. The location of these panels may not be shown on the drawings. TheDDC panels in the mechanical room shall be provided with a UPS to allowoperation of the panels during switchover to emergency power. The UPS shallprovide a minimum of 500 va, be similar to an Invensys Powerware 120, and beinstalled in a NEMA 1 hinged, lockable cabinet. The UPS shall provide a minimumof 500 va, be similar to an Invensys Powerware 120, and be installed in a NEMA1 hinged, mechanically-vented (both sides of enclosure) and lockable cabinet.5BAS panel UPS to meet the following6a.Manufacturer: Liebert or approved equal by UES.1)Voltagea)120V units: 0 - 140VAC, 50/60Hz, single-phase, 2-wireplus-ground.b)Input Voltage Tolerance: -25% at full load2)Output Load Capacitya).9 lagging power factor3)Designa)UPS must be true online double conversion: load ispowered from inverter and therefore provides full powerconditioning at all times.b)Marginal Inverter overload and time duration specificationsmust be: 60 seconds at 125%4)Communicationa)Standard protocol option is: Bac-Net over IPb)Manufacturer must include full integration advisement andservices of communication card: into existing BMS systemb.Version 3.1.2020For BAS panels enclosures, provide current panel point list includingvirtual points, panel configuration data (IP, subnet mask, router, HMIspeed ETC.) within the panel. This shall be laminated and hung on theinside door.8Building Automation Systems (BAS)
Power to each BAS panel shall be provided from a breakered, 20 amp dedicatedcircuit on emergency power having an insulated ground wire from the powerpanel ground buss wired to the duplex receptacle.The BAS Control System will perform all Sequence of Operations as required bythe Design Engineer.Furnish and install a network communications trunk (N.C.T.) between DDCpanels, and a separate LAN communications network between each terminal unitcontroller (or group of controllers) back to the DDC panel associated with theAHU which serves the terminal units. Trunks shall be connected to the panelswith CAT-6 conductors and required components (switches). In addition, theN.C.T. trunk shall be extended from the nearest Panel to an Owner-provided,network drop(s) locationAll terminal equipment controllers shall be Ethernet IP communications.3The project shall provide a dedicated Ethernet network connection between theBAS panel and the Campus BAS Software. The BAS Contractor is responsiblefor coordinating the network drop (s) required for integration to the Campus BASSoftware and will not receive final payment for the project until the BAS systemis fully integrated and accepted by TAMU Utilities & Energy Services (UES).All Ethernet routing devices shall be in a locked cabinet for security purposes.Use same kay as the building automation enclosures.4Provide graphics for all new work, compatible with existing campus front endsystem. Coordinate and provide BAS graphics that are acceptable to TAMUUtilities & Energy Services (UES). See section 1.10 below for more information.All exposed wiring shall be in conduit (3/4” minimum). Concealed wiring shall beplenum rated. All active Ethernet switches, hubs, and routers required for thecommunication between BAS panels shall be BAS Contractor-provided andinstalled. The conduit/wiring system required for the BAS shall be a complete,separate, independent system. Conduit sharing with other unrelated electricalsystems is not permitted. All conduit shall enter BAS panels and WAGESenclosures from the bottom of the panel or enclosure.A Schneider Electric 9788TAMUWAGESHMI metering panel, of the appropriatecapacity, will be provided by the Div 2615 Contractor, complete with allmicroprocessors, software, programming, point data base, trends, terminal strips,and regulated power supply with battery backup.The WAGES panel will require temperature and flow sensor wiring from the panelto sensors located in the primary supply and return piping on the Chilled Water,Heating Hot Water, and Domestic Hot Water, to be included as part of the BASContractor’s responsibilities. The WAGES panel will require flow meter wiringVersion 3.1.2020Building Automation Systems (BAS)
from Domestic Cold Water, Irrigation Water, and Steam. Provide all wiring fromthe flow tubes and flow transmitters to the WAGES panel. This WAGES panelwill require a dedicated 110 volt, 20 amp, single phase standby electric circuitsource. This WAGES panel will require a category 6 Ethernet cable. TheWAGES system will require start-up & integration to the Campus MeteringSoftware, by the Schneider Electric Square D Vendor. A meeting between theTAMU UES and the BAS contractor will be held as early as possible, prior topurchase of any material, to review the installation and finalize panel and wiringlocations The WAGES panel is used only when campus chilled or heating wateris servicing the facility.When only electric and domestic water are being metered, the electric meter thatis to be installed must have the option of field installable digital input/outputmodules that can be added at any time thus allowing monitoring of status points,consumption of water, air, gas, and or steam pulses. Also this unit must be easilyintegrated in the current TAMU power and energy management systemIntegration of the WAGES system to the UES Metering Software shall includeloading of the TAMU WAGES program into each WAGES panel, connecting tothe UES meter software, as well as five Graphic screens that represent the pipingand position of temperature sensors and flow tube for each commodity that isbeing metered in the WAGES system.The BAS contractor will be responsible for the connection and integration fromthe BAS in the building, to the Campus BAS software. The Contractor will beresponsible for programming the DDC panels with operational sequences andset-points as specified.All BAS controllers shall be mounted in an enclosure. 21.03RELATED WORKIf the project will include Chillers, Boilers, or other DX system the BAS shall haveall points mapped through BacNet, Modbus, or other means that will allow for theBAS to see, monitor, trend, alarm, as well as control, at a minimum, the start/stopand set point of each system.If the BAS Contractor believes there are conflicts or missing information in theproject documents, the Contractor shall promptly request clarification andinstruction from the design team.Shop Drawings:Schematic flow diagrams & graphic display.Power, signal, and control wiring diagrams.Details of control panel faces.Damper schedule.Valve schedule.Version 3.1.2020Building Automation Systems (BAS)
DDC System Hardware: Wiring diagrams, schematic floor plans, andschematic control diagrams.Control System Software: Schematic diagrams, written descriptions, andpoints list.Sequences of operation.Software and firmware operational documentation.Samples of Graphic Display screen types and associated menus.Field quality-control test reports.Operation and maintenance data.All points, (AI, AO, DI, and DO) along with all virtual points are to be trended in15 minute intervals or Change of Value (COV). UES to determine COV values 141.04RECORD DOCUMENTATIONOperation, Maintenance Manuals and Drawings:One (1) copy of the Operation and Maintenance Manuals, ControlDrawings, written Sequence of Operation, and latest mechanical As-Builtsshall be provided to the Utilities & Energy Services upon completion of theproject. The entire Operation and Maintenance Manual, Control Drawings,and written Sequence of Operation, shall be furnished on a USB Drive, andinclude the following for the BAS provided: 12a.Table of contents.b.As-built system record drawings. Computer Aided Drawings (CAD)record drawings shall represent the as-built condition of the systemand incorporate all information supplied with the approved submittal.c.Manufacturer’s product data sheets or catalog pages for all productsincluding software.d.Archive copy of all site-specific databases and sequences.e.BAS network diagrams.f.Interfaces to all third-party products and work by other trades.The Operation and Maintenance Manual CD shall be self-contained, andinclude all necessary software required to access the product data sheets.A logically organized table of contents shall provide dynamic links to viewand print all product data sheets. Viewer software shall provide the abilityto display, zoom,
electronic damper actuator(s), and electronic HW valve and actuator for installation on each VAV terminal unit and fan coil unit, as applicable, by the terminal equipment manufacturer. These DDC devices shall be delivered to the manufacturer's factory in sufficient time for the terminal equipment manufacturer to meet their scheduled delivery obligations. The BAS Contractor shall furnish all .