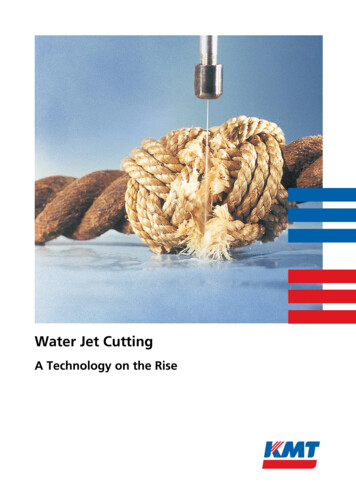
Transcription
Water Jet CuttingA Technology on the Rise
Water Jet CuttingA Technology on the RiseForeword:The purpose of this brochure is to give thereader a rough overview of WaterjetCutting. In addition to precise cutting ofvarious materials as presented, manyspecial applications i.e. medical and in thedecommissioning and demolition fieldexist – these however being outside thescope of this text. For any additionalinformation, our KMT Waterjet team isalways available. Also, we would like towelcome you to visit our homepagewww.kmt-waterjet.com, where you havethe option of downloading useful files.In order for you to get a betterunderstanding of KMT Waterjet Systems,we would also like to take this opportunityto present our company.Siberia to Iceland, from Norway to SouthAfrica.Specially trained technicians are constantlyon duty and can help you immediately atany time.Service and wear parts are shipped within24 hours.Our contract-cutting department takescare of our customers’ needs to the fullest,enabling us to perform test-cuttingprocedures in order to optimize thecutting method, allowing you foreconomically and technically soundoperation of your machines.The KMT Waterjet team in Bad Nauheim isalways available to answer your questions!In the Autumn of 2003, KMT AB ofSweden purchased the Waterjet CuttingDivision from Ingersoll-Rand. The KMTCorporation is an Internationally activecorporation with over 700 employeesworldwide. KMT Waterjet Systemsemploys 200 people. Further KMT brandsinclude UVA, LIDKOPING, KMT RoboticSolutions,KMTAqua-Dyne,KMTMcCartney, and KMT H2O. The focus ofall of these brands is metal working inIndustrial Applications.The KMT Waterjet production facility inBaxter Springs, Kansas USA has beenmanufacturing High Pressure componentsand pumps for over 50 years. The majorityof these is used in Waterjet Cutting,however notably the PetrochemicalIndustry has also been a large customer ofour pumps for over 50 years.Over 150 top quality specialists work inthis area, developing, manufacturing anddesigning these high-tech units for over50 years. KMT has over 6500 waterjetcutting pumps in worldwide service. OurEuropean Headquarters in Bad Nauheim,Germany, services the European market,plus Africa, west Asia and China. This iswhere we take care of customers fromOctober 2010Page 1
Water Jet CuttingA Technology on the Rise1. Introduction2. HistorySince ages, nature has proven that eventhe hardest materials change their formand shape when water is applied to them.The German folk saying has stated forages that a steady drop of water can drill ahole in a stone. The real life applications ofpressurized water date back to the 19thcentury, when Californian gold miners ofthe 1870’s used it to remove layers ofsand and rock. The 1920’s mark thebeginning of the use of water jets for theremoval of stones and sand in dailyconstruction work. These jets hadcharacteristically large flow rates withpressure levels reaching a few hundredbar; which is the combination necessary tomove the large volumes of material, asrequired for mining applications. Precisecutting in the modern understanding ofthe word, was not possible at the time.Thestructurescreatedbythisphenomenon can be both useful andbeautiful.In the 1950’s, McCartney Manufacturingof Baxter Springs, Kansas, USA, developedthe first Ultra High Pressure Pumps forCatalyst injection in Low DensityPolyethyleneproduction.In1963,McCartney was acquired by IngersollRand. McCartney was sold to KMTWaterjet in the Autumn of 2003.Fig. 1 The Grand Canyon was cut by waterflowing through stone.In the process of mineral erosion ofstones, it is not only the flow of water thatplays an important role. Also, theimplications of air and mineral particles i.e.sand, moving with the water, play animportant role.Almost the whole surface of our planet isand has been influenced by such processesin one way or another.October 2010In 1968, Dr. Norman Franz, a Professor atthe University of British Columbia,Canada, patented a concept of a WaterjetCutting machine with a cutting pressureof 700 bar.The first commercial application came intolife already in 1971. A system devised bythe KMT Waterjet subsidiary McCartneyManufacturing was used for cutting ofpaper tubes and was an instant success.At that time, only pure water cutting wasused. The cut materials included paperdiapers as well as honeycomb materialsused in the aerospace industry, whichwere difficult to process using traditionalmethods.Page 2
Water Jet CuttingA Technology on the Rise3. Operating PrinciplesEvery cutting method is based on theinput of energy into the material, in orderto overcome the chemical bindingspresent in the structure of the material.Thermal cutting methods, for example,utilize the energy of chemical reactions,electricity, or light to produce hightemperatures in order to melt the materialat the cutting kerf.Mechanical methods utilize the kineticenergy of the moving tool or form ductilematerials through the application ofpressure.Fig. 2 Without waterjets, diapers would havebeen much more difficult to produce.Since the early 1970’s, Ingersoll-Rand hasbeen manufacturing pumps generating acontinuous output pressure of 3.800 bar.Another Ingersoll-Rand subsidiary, BestMatic, developed a machine in Europe forcutting wooden puzzles.Pure water is very well suited for cutting ofsoft, hard, and sensitive materials in a veryprecise manner. Unfortunately it is notpossible to cut very hard materials such asceramic tiles, steel, glass, or stone.Waterjet Cutting can be classified as amechanical method. The energy of therapidly moving jet is utilized either in theform of a pure waterjet or abrasivewaterjet and then applied to theworkpiece causing microerosion. Thecutting water works as a cooling agent ofcutting edge, thus allowing for a very highquality cut.The one main component which iswithout any doubt always necessary tocreate a waterjet is the high pressurepump.To overcome this shortcoming, tests wereconducted with adding hard abrasiveparticles to the jet. In the early 1980’s thistechnology left the laboratory. In 1984,Ingersoll-Rand’s hydroabrasive division wascreated.The development of capable Robotic armsopened a completely new large application area of „Cutting Boxes“ mainly forthe manufacturing of 3D automotive partse.g. headliners, or consoles.Today, KMT Waterjet does not build anycomplete waterjet cutting systems.Instead, our focus has been on thecontinuousdevelopmentandimprovement of our top quality highpressure components, as well as the verystrong support of our system partnersactive in the Machine Tool, Stone, Glass,and Food businesses as well as many otherareas of material processing.October 2010Page 3
Water Jet CuttingA Technology on the Riseoutput pressures of over 6.200 bar andflow rates between 1,5 and 15,2 l/min.The water is transported through specialhigh pressure tubing, which is partiallyflexible, allowing for the movements ofthe cutting head. The head consists of apneumatically controlled needle valve anda nozzle tube, at the end of which aspecial conus fitting a jewel orifice (mostcommonly diamond or sapphire) ismounted with a special nut. It is in thisvery nozzle that velocities of Mach 2-3 areachieved.Fig. 3 Streamline PRO-I High Pressure Pumpfrom KMT Waterjet SystemsDirect drive pumps offer large volumes ofhigh-pressure water. Their pressureranges, however, are limited, especially atthe top end. Their main area of applicationis in the areas, where large cutting powerwith-out very good accuracy is required,i.e. in the construction industry, surfacecleaning, material removal, etc.For cutting applications, so-called Intensifier pumps are mainly used. Theirpressure of the primary (oil) cirquit isachieved through the use of a variabledisplacement pump, only to be multipliedby 20 in the reciprocating intensifiertopworks.Fig. 5 KMT Waterjet Pure water cutting headFor abrasive applications, a specialAbrasive head is used for mixing the sandwith the high pressure water beneath thewater orifice.Fig. 4 The Intensifier principle: An electricmotor drives a hydraulic pump (below)pressurizing the oil circuit of the intensifier(center), where the pressure is increased 20times and fed into the system (above)These pumps have power ratings between10 und 149 KW (15-200HP) generatingOctober 2010Page 4
Water Jet CuttingA Technology on the RiseFor abrasive applications, the bulk transfersystem and the sand feeder are part of themachine as well as possibly a sand removaland recycling unit in some rare cases.Fig. 7 A cutting machine with waterpreparation, STREAMLINE SL-V High PressurePump, Waste Filtration, and ABRALINE sandfeeder systemFig. 6 KMT Waterjet Autoline Abrasive CuttingHeadThe movement of the cutting head isusually controlled by a CNC controller ofthe cutting table.The material is placed on a grid above thewater tank, which serves the purpose ofdisbursing and capturing the energy of thejet upon exiting the workpiece.In most cases, conventional tap water canbe used as the cutting medium. In somecases however, a conventional watersoftener is applied. Extremely pure,distilled water should not be used, aswithout any dissolved ions, the watertends to react with the high-pressurecomponents, causing excessive wear.October 2010Page 5
Water Jet CuttingA Technology on the Rise4. Advantages of Waterjet Cutting:Pure-waterHydroabrasiv Flexible production Flexible production Environmentally friendly Small kerf Small kerf Better material utilizationIn most cases eliminates after-cutmachining Cutting in all axes Better Material Utilization High speeds for various materials Cutting in all axes Easily adaptable to automaticcontouring High speeds for various materials Easily adaptable to automaticcontouring Easy programming with standardCAD/CAM systems Fits Multiple-axis systems Easily integrated into flexibleproduction systems Just-in-Time production Quick prototyping Only simple fixtures required Small tangential forces on cut material No heat affected zones No uncontrolled thermal tempering orhardening Stress free cutting No metallurgical deformation No material jump-off No tool sharpening No dust, fumes, or gases released Easy programming with standardCAD/CAM systems Fits multiple-axis systems Easily integrated into flexibleproduction systems Just-in-Time production Quick prototyping Only simple fixtures required Small tangential forces on cut material No heat affected zones Stress free cutting No material jump-off No tool sharpening No dust, fumes, or gases releasedOctober 2010Page 6
Water Jet CuttingA Technology on the Rise5. Two types of cuttingLet us take a closer look at the basics ofthe two waterjet cutting methods.Pure-water cuttingPure waterjet is used mainly for relativelysoft materials such as plastic, textiles,paper, sealing materials, metalic foils,plywood.Fig. 9 Plastic Inlay Floormat for a ClubFig. 8 Pure water samples cut at KMT Waterjet,Bad NauheimThese materials can be cut at very highspeeds. The limiting factor is usually notthe cutting power of the cutting head, butthe ability of the movement device tomove quick enough.Another interesting application field is inthe area of seal manufacturing. A press ismuch quicker; the tooling costs howeverare so high, that only high productionvolumes are feasible. Waterjet, on theother hand, allows for production in smallruns, i.e. 100 cylinder head seals, for arare automobile.In combination with an optical recognitionsystem and a nesting software package awaterjet cutting machine is able utilize apiece of leather in an optimal way.When trying to cut a material at 20m/min,it is not very likely that the cutting headwill have a chance to accelerate to thishigh speed within a small workpiece.Examples:Paper and plastic foils up to 200 m/minCarpeting: 15 - 30 m/min.For such materials, waterjet is used forcutting of production runs, where it isused as an alternatives to blade cutting.A pure waterjet has the width of a hair ataround 0,1 mm- 0,2 mm and is thereforeable to cut very sharp contours. Partsrequiring positive-negative inlays, can beput together without any problemwhatsoever. A company logo embeddedin a floormat is highly desirable from acustomer’s standpoint.October 2010Fig. 10 Leather cutting machine with opticalrecognition system and nestingThe raw leather is placed on a table, andscanned by a digital camera, in order tofind defects (i.e. holes, discolorations,etc.), which are recognized by the camera.The special software is able to optimizethe material utilization based on thedifferent shoe sizes.Page 7
Water Jet CuttingA Technology on the RiseThe water used for cutting has to be atleast the purity of drinkable water,therefore, waterjet is very well suited forapplications in the food industry.Frozen fish, previously available only insticks, now can be cut into sea horses,stars, whatever shapes found desirableand attractive, especially to kids.When cutting cake, it is certain that aforgotten cherry seed does not stick to theblade leaving an ugly looking mark.Chocolate also can be cut with nice edgequality.At the end of a pure water cutting head, anut holds a cutting orifice encased in steel.When the nozzle is worn, it can bereplaced within minutes.Hydroabrasive-cuttingThe hydroabrasive application is used forharder materials:Metals, Glass, Stone, Concrete, Glasscomposites, Ceramics and hard materialslike Aluminum oxide or Silicone Oxide.Fig. 11 Metal, Stone and plastic materials cutat KMT Waterjet Bad NauheimFig. 12View of the KMT Waterjet AUTOLINE Abrasivecutting headAfter the high pressure water passesthrough the water orifice, it flows into themixing chamber. Because of the high velocity, the jet causes a vacuum, thus suckingin the mixture of air and sand through theentry port. The sand quantity is controlledby the abrasive feeder.In order to bring this mixture intoalignment, a focusing tube with a conicallyshaped inlet of three times the diameter ofthe water orifice is r
Solutions, KMT Aqua-Dyne, KMT McCartney, and KMT H2O. The focus of all of these brands is metal working in Industrial Applications. The KMT Waterjet production facility in Baxter Springs, Kansas USA has been manufacturing High Pressure components and pumps for over 50 years. The majority of these is used in Waterjet Cutting, however notably the Petrochemical Industry has also been a large .