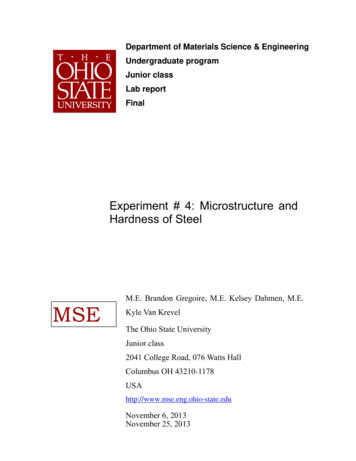
Transcription
Department of Materials Science & EngineeringUndergraduate programJunior classLab reportFinalExperiment # 4: Microstructure andHardness of SteelMSEM.E. Brandon Gregoire, M.E. Kelsey Dahmen, M.E.Kyle Van KrevelThe Ohio State UniversityJunior class2041 College Road, 076 Watts HallColumbus OH mber 6, 2013November 25, 2013
AbstractOne of the main focuses of material science engineering is to understand and linktogether the relationship between a materials physical properties and microstructure. Theobjectives of this work are to explore the effects of several heat treated steel samplesbased on hardness and microstructure images gathered from optical microscopy. Alsolearn basic metallographic sample preparation techniques. Sample A was determined tobe 1045 steel that was air cooled from the austenite phase. The volume fraction ofprimary alpha was 32.1%, 67.9% pearlite, and 8.15% cementite. Sample B wasdetermined to be 1085 steel that has been furnace cooled. The sample is determined to be1085 steel because the microstructure consists of mostly pearlite with the volume percentof primary alpha being 4.06% and pearlite 95.95%. Sample C was determined to be 1018steel that has been air cooled from the austenite phase and tempered. The hardness of thissample was 72.33 which are close to the theoretical value of 71 for 1018 steels. Thevolume fractions for this sample were 71.99% primary alpha and 28.01% pearlite, and0% cementite. Sample D was deduced to be 4340 steel that has been quenched in waterfrom the austenite phase field. Quenching steel from water avoids pearlite formationcompletely and produces mostly martensite. As seen in the volume fractions the majorityof the sample was 81.82%, with primary alpha at 13.08%, and cementite at 0%.Cementite for this sample was 0% because transformations into martensite are onlypossible through rapid quenching. Based on these sample images it is possible thatsample A and C have the same composition with similar heat treatments. They seem tohave similar heat treatments because the samples have similar compositions exceptsample C having smaller grain boundaries due to being both air cooled and tempered.
Table of ContentsAbstract1Table of Contents21Introduction and objectives1.1Purpose and Goals1.2Heat Treatment of Steels and Phase Transformations1.2.1TTT and CTT diagrams33342Approach and experimental procedures2.1Metallographic Preparation2.2Optical Microscopy and Hardness Testing6663Results and discussion3.1Sample A3.2Sample B3.3Sample C3.4Sample D3.4.1Analysis and Comparison of erences14A1515161819Appendix (optional)A.1Sample A Images4.1Sample B Images4.2Sample C Images4.3Sample D ImagesSymbols22Distribution List23
1Introduction and objectives1.1Purpose and GoalsOne of the main focuses of material science engineering is to understand and linktogether the relationship between a materials physical properties and microstructure. Theobjectives of this work are to learn basic metallographic sample preparation techniques,and determine the effects of several heat treatments on unknown steel samples by opticalmicroscopy. Also understand and contrast steel microstructures and hardness by findingcorrelations with these observations with the associated Iron-Carbon Phase diagrams andContinuous Cooling Transformation (CCT) diagrams.1.2Heat Treatment of Steels and Phase TransformationsSteel is a metallic alloy of iron with carbon used as primary structural materials. Steelsare composed of usually 0.002% to 2.1% carbon with additional elements such asmanganese, phosphorus, silicon and sulfur. Steel is one of the most used alloys due totheir mechanical properties such hardness, ductility, and strength are easy to manage andcontrol. The mechanical behavior of steels is influenced by its microstructure which canbe manipulated. When there is an alteration of a microstructure, it involves some kind ofphase transformation where a new phase is formed that has different chemical, physical,and structure from its original phase. Phase transformations are induced by, varyingcompositions, externals pressures and the most popular; varying temperatures by meansof heat treatment. Heat treatment includes changing the properties of a material byrapidly heating and chilling the material.Steels can have different microstructures or phases based on its composition of carbonand the rate it is heated or cooled. Phase or equilibrium diagrams are used to display aphase structure based on the combination of temperature, composition and pressure. Themost important phases found in the iron-iron carbide phase diagram are α-ferrite (BCC),γ-austenite (FCC), and cementite. There are also other possible phase changes dependingon the rate of cooling on the decomposition of austenite such as, pearlite, bainite, andmartensite. Phase diagrams are the best in predicting the phase in materials but they arelimited in their ability in which, it cannot predict the time it takes for the transformationsto occur. Also phase diagrams shows phases that develop under equilibrium conditionswhere most phase transformations occur in non-equilibrium conditions which are timeand temperature dependent. Time-Temperature-percentage completion of Transformation(TTT) diagrams are used to cover non equilibrium phase changes [1].
4Experiment #4: Steels LabFigure 1: Iron-Iron phase diagram [3].1.2.1TTT and CTT diagramsIsothermal transformation (TTT) diagrams are plot transformations that occurcorresponding to a specific temperature versus time history. These types of plots are onlyaccurate for transformations that occur at constant temperatures throughout the reaction.The samples prepared in this lab were cooled from austenite temperature (912 C) to roomtemperature, which means the transformations occurred over a range of temperatures.Continuous Cooling Transformations (CCT) diagrams are used instead to show phasetransformations over a range of temperatures as shown in the figure below. Using thesediagrams and the images gathered from using optical microscopy, unknown samples canbe determined [2].
1Introduction and objectivesFigure 2: Continuous cooling transformation diagram for steel 4340 [4].5
6Experiment #4: Steels Lab2Approach and experimental procedures2.1Metallographic PreparationThree unknown steel samples A, B, and C of unknown compositions and heat treatmentwere distributed. First the samples were cleaned in a water bath and dried. Next thesamples were grinded on three different sized polishing wheels with the sizes of 6, 1 and0.5 micrometers. In between each of the intermediate polishing steps the samples werecleaned again with water and ethanol solution and checked under a microscope forimperfections such as black specks and scratches. After all the grindings were done anital etching solution was used to reveal the microstructure.2.2Optical Microscopy and Hardness TestingFirst a LECO optical microscope was calibrated to examine the surfaces of the unknownsteel samples. Each of the microscopes was equipped with a computer and PAX-itsoftware. Using the microscope multiple images were taken for each of the samples at 4different locations and at 200X, 500X, and 1000X magnifications. The PAX-it softwareallowed the images to be labeled with a scale marker and be saved.Using these images with the program ImageJ, the volume fraction of each of the differentphases can be determined. Each of the images had a grid of points laid over. The numberof points in the grid were counted and compared to the number of points that lay withineach phase or microconstituent. Using these numbers a volume fraction can bedetermined for each of the phases. Lastly, a hardness test was performed on each of thesamples using a Rockwell scale.
3Results and discussion3.1Sample AAfter obtaining micrographs for sample A at various magnifications, we performed imageanalysis using ImageJ. Figure 2 below shows sample A at a magnification of 500X.Figure 3: Sample A at 500X.Figure 3 shows two separate phases. The lighter white areas are primary phase (ferrite),and the dark grey areas are pearlite, which consists of about 12% cementite and 88%ferrite based on the Iron-Carbon phase diagram. The pearlite structure in sample A iscourse because the spacing between the lamellae is larger than sample C (see appendixA.3) and not all the cementite formed a lamellar structure.Using ImageJ analysis and a point counting method, the volume fraction of each of thephases were found as shown in the table below. The most abundant phases in samplewere primary alpha with the least amount being cementite. The amount of primary alphaonly describes the ferrite grains, while there is also ferrite in the pearlite lamella. Fromthe microstructure and the volume fraction the sample is determined to be 1045 steel thathas been air cooled from the γ (austenite) phase. From using the iron-carbon phasediagram and the lever rule, the percent of carbon was calculated to be 0.572% which isclose to the literature value of 0.45% in 1045 steel. The heat treatment of this sample wasdetermined to be air cooled because of the coarseness of the pearlite compared to theother samples. The pearlite layers are more fine and closer together compared to sample
8Experiment #4: Steels LabC. The hardness value also reinforces that the sample is 1085 steel because it is close tothe literature value of 85 on the Rockwell scale.Table 1. Sample A volume percent and hardness.Sample ARockwell HardnessVolume Percent primary AlphaVolume Percent PearliteVolume Percent Cementite3.2Average99.3332.09%67.91%8.15%Error Bar 0.44 0.85 0.85 0.29Sample BImages of sample B were taken in the same process using optical microscopy. An imageof sample B at a magnification 1000X was taken and is shown below in Figure 3. Theonly microconstituent shown below is pearlite. At lower magnifications primary alphaferrite grains are visible, because of the minute amount of primary alpha in the sample.The pearlite structure is coarser than sample A due to the spacing of the pearlite.Figure 4: Sample B at 1000XThe sample was determined to be 1085 steel that has been furnace cooled from austenite.The sample is determined to be 1085 steel because the microstructure consists of mostlypearlite as shown in the table 2. The percent of primary alpha was found to be 4.06% andpearlite 95.95%. Based on the iron carbon phase diagram the cementite volume percent
39Results and discussionshould be 12% of the pearlite volume, however this cannot be determined using the pointcounting method at these magnifications. Sample B is determined to be furnace cooledfrom the austenite phase because of the coarseness of the pearlite.Table 2. Sample B volume percent and hardness.Sample BRockwell HardnessVolume Percent primary AlphaVolume Percent PearliteVolume Percent Cementite3.3Average22.704.06%95.95%0.00%Error Bar 0.30 0.53 0.53 0.00Sample CAn image of sample C at 500X magnification is shown in Figure 4 below. There are twophases visible in this sample. The light phase is alpha ferrite, and the dark phase ispearlite. The pearlite in this sample is the finest of the four samples.Figure 5: Samples C 500XThe sample was determined to be 1018 steel that has been air cooled from the austenitephase and tempered. The sample was determined to be air cooled because the pearlitewas fine, and it was tempered because the grain size was small relative to the othersamples. This sample was found to be alloy 1018 steel because it contains 72% primaryalpha, which is more than sample A. Table 3 shows the harness and volume fractions for
10Experiment #4: Steels Labthis sample. The Rockwell hardness was 72.33 which is also close to the theoretical valueof 71. Any cementite not contained in pearlite was negligible due to the fact of cementiteexisting on grain boundaries that cannot be determined at these magnifications.Table 3. Volume percent and Harness for sample C.Sample CRockwell HardnessVolume Percent primary AlphaVolume Percent PearliteVolume Percent Cementite3.4Average72.3371.99%28.01%0.00%Error Bar 0.51 1.07 1.07 0.00Sample DAn image of sample D taken at a magnification of 1000X is shown in the figure below.The microstructure depicts that the dark edges along the grain boundaries is cementite,with the lighter colored areas being martensite. The white areas are primary alpha ferrite.Figure 6: Sample D at 1000X.The sample was deduced to be 4340 steel that has been quenched in water from theaustenite phase field. Quenching steel from water avoids pearlite formation completelyand produces mostly martensite as shown in the volume percentages in table 4. Thevolume percent of martensite was found to be 81.82% and 13.08% primary alpha.
311Results and discussionThere is no cementite in this sample because martensite is formed in carbon steels byrapid quenching of austenite. Since the rate of quenching to form martensite is so fast,carbon atoms do not have enough time to diffuse out of the crystal structure to formcementite.Table 4. Volume Percent and hardness for sample D.Sample DRockwell HardnessVolume Percent primary AlphaVolume Percent PearliteVolume Percent CementiteVolume Percent Martensite3.4.1Average56.6713.08%0.00%081.82%Error Bars 0.44 0.58 0.000 0.63Analysis, Comparison of Samples, and ErrorBased on the images and the volume percentages it is possible that some of the sampleshave the same composition and was heat treated the same, specifically sample A and C.Sample A and C come closest to having the same microstructure with their microstructures somewhat being inverted. The amount of alpha in sample A was about 30% butin sample C 70%, and the amount of pearlite in sample A was about 70% and in sampleC 30% again. This is probably due to the way these steels were heat treated. Temperingsteel causes grain boundaries to become smaller, which explains why sample C or 1018steel
1.2 Heat Treatment of Steels and Phase Transformations Steel is a metallic alloy of iron with carbon used as primary structural materials. Steels are composed of usually 0.002% to 2.1% carbon with additional elements such as manganese, phosphorus, silicon and sulfur. Steel