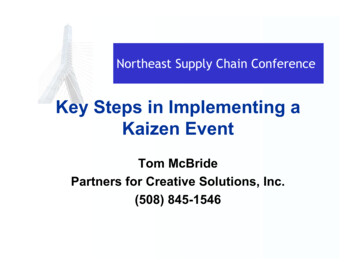
Transcription
Northeast Supply Chain ConferenceKey Steps in Implementing aKaizen EventTom McBridePartners for Creative Solutions, Inc.(508) 845-1546
What We Will Cover What are kaizen events?Choosing the best projectsSelecting a “pilot” eventTeam members and their rolesHow to prepare for a kaizen event10 steps for conducting the eventFinding the time for kaizen events2
About Kaizen Kaizen is continuous improvementKaizen is employee involvementKaizen requires a cultural changeAccording to the originators at Toyota 80% of the journey involves learning and living thenew philosophy 20% involves physical changes3
A Kaizen Event Is a highly focused “assault” on an area orprocess to achieve rapid improvement Uses a cross-functional team with processinsiders and outsiders Achieves as many improvements aspossible during a typical 3-5 day event Augments, but does not replace,continuous improvement4
Some Paths to Improvement Individual efforts Part-time groups or teams Kaizen events5
When Are Kaizen EventsAppropriate? Need for solution is urgent Competitive crisis High customer dissatisfaction Big impact projects Significant impact on sales or profits Bottlenecks Cannot tolerate prolonged disruption6
Selecting Candidates forKaizen Events Factors to consider Strategic goals of the organization Current performance of process, department,machine (good time for Value Stream Mapping) Feasibility (difficulty, resources required,probability of success) Selecting the top few candidates Decision matrix (sample available on request)7
Value Stream Map Technique to analyze the production of aproduct line from receiving dock toshipping dock Structured way to gather, organize, andpresent pertinent data about the existingprocess8
Value Stream Map - Current StateValue Stream MapWeekly shipments:700,000 lineal50,000 pieces6-day lead time as shown5,350 finished pieces/day5%90 %From F/J:Staging5%10%90%Lam #1I268piecesIResaw (4 saws)IMolder #4PrimeICrew size: 4Run speed 58 ft/minOutput: 500 pieces/hrCrew size: 1 1/3Run speed 184 ft/min.Output:1,584 pieces/hrCrew size: 4Run speed 300 ft/minOutput:1,285 pieces/hr% Reliability 98%% Reliability 95%% Reliability 98%% Reliability 73%Waste 1/2%Waste Waste 1/2%Waste 3%Sec available 27,000Sec available 108,000Sec available27,000Sec available 27,000Weekly hr 5Weekly hr 31.6Weekly hr 38.9Weekly hr 18.54,500C/T 7.2 secpiecesC/O 5 - 25 min% Crew:days 100%swing 0%.5 hr90009,000C/T 2.3 secpcs C/T 2.8 secpieces C/T 1.3 secC/O 7 - 30 minC/O 5 - 45 minC/O 1 min - 1 hr% Crew Days 100%% Crew:days 100%% Crew:days 100%Swing 0%swing 0 %swing 48 hr1,034 secCrew size: 3Run speed: 3,15 l ft/minOutput:1,350 pieces/hr48 hr230 sec48 hr280 sec130 secVA Ratio 1:311Production lead time 521,874 secValue-added time1,674 sec129
Selecting the “Pilot” Event High likelihood of success Results will be highly visible Makes a significant impact to theorganization Solves operational problems, notmanagement issues Area has a stable current process10
Preparing For the Event Select team sponsorSelect team leaderChoose the facilitatorChoose team participantsDevelop the team charterGather data prior to the eventPrepare the organization11
Team Sponsor High level champion of the causeUpper management advisor to the teamBreaks through road blocksArranges support for the team during theevent Ensures coverage so that team membersare not interrupted during the event12
Team Leader Determines session objectives andprocess to be followed Meets with facilitator to review sessionobjectives and process Sends agenda to team members inadvance Is the leader, not the boss13
Traits of Good TeamLeaders Previous success as a leader (church,scouts, military, civic, etc.) Has experienced a kaizen event Good knowledge of lean manufacturing (ifproduction area event) Good knowledge of waste eliminationtechniques Not dictatorial - understands participativemanagement Comfortable working in the target area Good people skills14
Team Facilitator Manages how people work together duringteam activities Keeps activities moving along the processand time schedule set by the team leader15
Recorder Records important results, actions, &decisions Promptly distributes minutes toparticipants Usually a team member16
Identify Other Members Insiders – who work in or around the process Machine OperatorBuyerAssemblerPlanner Outsiders Provides non-tainted viewpoint & new ideas Can be inside or outside of the company17
Traits of Good Participants Understands the target area May work in area Can learn the area Open to doing things differentlyWill get involvedGood communicatorsBrings knowledge (technical orprocedural) that will help the teamsucceed18
The Kaizen Team Charter Team Charter clearly identifies rules ofoperation ObjectivesScopeResources available (budget, assistance, etc.)Authority of the team (and it’s limits)DeliverablesScheduleCode of Conduct (developed at kick-off meeting) Created by leader and approved by team19
Before 1st Team Meeting Gather detailed information in advance Process stepsWIP levelsCapacities/process timesWhat is produced and how much?Cycle and queue timesBatch sizes & changeover frequencyDefect RatesUp-timeNumber of operators Photos and layout of target area20
Rolling Out the Kaizen Event Preparing the Organization - considerations Developing a sense of trust across the organization Generating enthusiasm about the event Demonstration of commitment by management Publicizing the event - before and after Getting the union to cooperate Team Kickoff (includes sponsors) Review draft charter, modify, approve Develop code of conduct (agreement on rules) Discuss training and event logistics, etc.21
Setting the ProperEnvironment for the Event Logistics Location – off-site, on-site, or in work area Food – feed the team – feed everyone? Tools, supplies Work hours (in advance) Handling interruptions (coverage) Support from rest of organization(sponsor’s responsibility) Energy breaks22
Kaizen Event Sequence(Start to Finish)1. Training & kick-off activitiesA. Lean manufacturing (if in production area)B. Tools of continuous improvement(pareto, fishbone, run charts, 5-whys,process analysis, etc.)2.3.4.5.Analysis of current “state”Select areas of focusCreate possible solutionsSelect solutionsCreates a Plan Thathas Team Buy-in23
Useful Tool - Pareto Analysis Helps visualize thelarger sources ofwaste Visual application ofthe 80-20 rule Helps team focus onthose causes thathave the greatestimpact if solvedGolf Score Pareto Chart150puttschips100approachesdrives50fairways0# of strokestotal24
Analyzing the Current StateSome Wastes to Look For Too many process stepsExcessive travel distance or timeWaitingIneffective schedulingExcessive handlingInventory storage areasExcess WIP25
Analyzing the Current StateSome Wastes to Look For Bottlenecks Defects Poor organization of work area (5Sneeded) Large batch sizes and long setup times Disjointed process steps (need flow) Inefficient processes Opportunities to apply technology toimprove efficiency26
Creating Solutions Open your mind to new possibilities Don’t be bound by what is done today Do you need it?Should it be outsourced?Build it a different wayDesign it differently Don’t be discouraged by prior failures We tried to get approval for that before! That’ll never happen!27
Visualize the Perfect Solution What would be the ideal situation? What if all waste were eliminated? Elevates the target for generating solutions28
Kaizen Event Sequence6. Establish metrics forsuccess7. Plan & implement (repeatif necessary)8. Standardize and sustainGets the jobdone9. Report results10. CelebratePaves the way forfuture events29
Finding Time for KaizenEvents Work overtime to recover lost productionReroute production to other areaPerform the event over a weekendRun the event early in a production periodFinish “period” production early and thenrun the event Take advantage of a “slow” time Outsource some production to “buy” time Run the event concurrent with production30
Successful Uses of theProcess Sales - quotes take too long Reduced quote cycle by 40% Improved on-time delivery of quotes from “?” to 80 % Engineering – a bottleneck Improved on-time releases of engineering from 50% to 80% Assembly – high cost 40 % reduction in manual assembly costs31
Successful Uses of theProcess Quality costs – too high 50% reduction in defects Late material deliveries Late deliveries cut in half32
Summary What are kaizen events?Choosing the best projectsSelecting a “pilot” eventTeam members and their rolesHow to prepare for a kaizen event10 steps for conducting the eventFinding the time for Kaizen Events33
9 Value Stream Map 12 Production lead time 521,874 sec Value-added time 1,674 sec Weekly shipments: 700,000 lineal 50,000 pieces 1,034 sec 280 sec I Molder #4