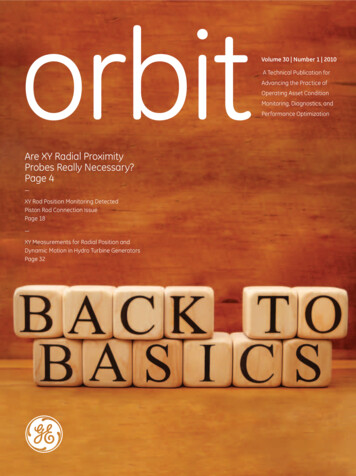
Transcription
orbitAre XY Radial ProximityProbes Really Necessary?Page 4—XY Rod Position Monitoring DetectedPiston Rod Connection IssuePage 18— Y Measurements for Radial Position andXDynamic Motion in Hydro Turbine GeneratorsPage 32Volume 30 Number 1 2010A Technical Publication forAdvancing the Practice ofOperating Asset ConditionMonitoring, Diagnostics, andPerformance Optimization
New ProductsEDITOR’SNOTEand ApplicationsFrom the Desk of Don MarshallChief Marketing Officer, Bently Nevada Asset Condition MonitoringOrbit: Looking Forward with the Experience of the PastBently Nevada has been a pioneer in the use of proximity2010 has proven to be a year of change. The economicprobes for industry-accepted measurements on thesecrisis of 2009 was a difficult time for all of us and this yearmachines, accommodating diagnostic plots that includebegan with a lot of uncertainty. However, as we near thethe orbit, shaft centerline and rod position. We willend of 2010, I think we can all agree that our environmentcontinue this legacy into the future as we apply solidfeels a bit more stable and we all have much to lookengineering concepts to facilitate condition monitoringforward to.for an ever-increasing range of machines that causeHere at Bently Nevada, a cornerstone of our strategy is toproblems for our customers.“protect the core.” This “core” represents all of the thingsAs we look to the future of the Orbit magazine, I amyou have come to expect from Bently Nevada. The deeppleased to announce that we will be bringing a new lookdomain knowledge you expect from our sales team, theand feel to Orbit in 2011. Don’t worry; our technical contentsuperior expertise of our services team, the service youwill only be enhanced by our continuing desire to makereceive from our local offices, the fast turn-around youthis magazine the benchmark of the industry. To meetexpect from our manufacturing team and the overallthis goal, we will be bringing a new editor on-board forquality you expect from our products. These are all2011. This will be combined with the goal of increasedimportant aspects of our legacy and our future.frequency of publication and an on-going commitmentAnother strategic aspect of our legacy that we will notforget is that of the Orbit magazine. In this issue, we willbe highlighting a cornerstone of our legacy: the needfor using the right transducer suite to make the rightmeasurement to solve the right problems. This “back tobasics” message is found in the use of XY proximity probesfor measuring vibration AND position. We will reinforce thismessage via three types of machines highlighted in thisedition of Orbit: horizontally mounted machinery, (turbinesand compressors), vertically mounted machinery (hydroturbine-generators) and reciprocating machinery.2 O R B I T Vol.30 No.1 2010for enhancing our technical leadership. Bently Nevadais the world’s leader in condition monitoring productsand services and the Orbit will continue to be one of ourprimary educational and informational tools. 2011 willtruly be an exciting year.
New Products and ApplicationsIn this issueIn this Issueorbit4Cover Story Are XY Radial Proximity Probes Really Necessary?11Synopsis of SavingsBack to Basics18 XY Rod Position Monitoring Detected PistonRod Connection Issue32 XY Measurements for Radial Position andDynamic Motion in Hydro Turbine GeneratorsNew Products and ApplicationsVolume 30 Number 1 2010A Technical Publication for Advancingthe Practice of Operating Asset ConditionMonitoring, Diagnostics, and PerformanceOptimizationPublisher: GE EnergyEditor: Jerry PritchardContributing Editor: Gary SwiftDesign Coordination: Earl StewartDesign: Gina AlteriCirculation: Karen SchanhalsPrinter: RR DonnelleyCONTRIBUTORSGE EnergyC. HatchBrian HowardM. KalbJohn KinghamRaegan MacvaughDr. Ryszard NowickiDerek PrinslooA. WeissJohn G. WintertonFrancesca Wu483500 ENCORE* SeriesAgriumGerry Kydd50Delayed Coker Drum MonitoringBoqueron S.A.Donalson PernaleteJesus RodriguezCase HistoryCREDITSGE Measurement & Control SolutionsGlobal CommunicationsKen DarbyAngie HowellMeg Scott24 Cylinder Pressure and Rod Load Measurementin High-Pressure Upstream ReciprocatingCompressors Using System 1*40 Cracked Bearing Race Detection in WindTurbine Gearboxes53 System 1 at Agrium: Nutrient for GrowthQuestions, suggestions, and letters to theeditor may be addressed to:ORBIT Magazine1631 Bently Parkway SouthMinden, Nevada USA 89423Phone: 775.782.3611Fax: 775.215.2864e-mail: orbit@ge.comPrinted in the USA. Over 40,000 copiesdistributed worldwide. Copyright 2010General Electric Company. All rights reserved.Vo l . 3 0 N o. 1 2 0 1 0 ORBI T 3
BACK TO BASICSAre XY Radial Proximity Probes ReallyNecessary?John KinghamField Application EngineerGE Energyjohn.kingham@ge.comJohn G. Winterton, P. E.Principal EngineerGE Energyjohn.winterton@ge.com4 O R B I T Vol.30 No.1 2010The title of this article is a very common inquiryfrom customers considering retrofits on oldermachines that previously had minimal (or no)vibration instrumentation. For critical machineswith fluid film bearings, the short answer is yes.You really do need XYprobes at each bearing.To understand why thisis the case, it is helpfulto examine two separatebut interrelated aspects ofa vibration monitoringsystem’s purpose:machineryprotection andmachinerymanagement. Itis also helpful tounderstand thenature of radialvibration inside amachine’s bearingclearances.
BACK TO BASICSMachinery ProtectionAn extremely important aspect of a machinery vibrationmonitoring system, and indeed often the primarypurpose by which it is economically justified, is to preventmechanical problems from progressing to catastrophicfailures without prior warning – in other words, to savethe machine, the process, and a significant amount ofdowntime. To this end, a vibration monitoring systemis designed to provide operator annunciation alarms(i.e., ALERT alarms) when vibration levels exceed userconfigured setpoints, and to shut the machine downautomatically when second-level alarm limits (i.e.,DANGER alarms) are reached.As shown in Figure 1, a shaft within a horizonal rotorFigure 1: The path traced out by the shaft centerline as it vibratesabout the bearing clearance centerline is known as the shaftorbit. At the instant depicted, the shaft centerline is in the positionshown by the red cross-hairs.system will vibrate within its bearing clearances in acharacteristic pattern that is typically elliptical in naturerather than perfectly circular. The ellipticity of this orbit isa function of numerous parameters in the machine, suchas stiffnesses, that are different in one axis than another (amachine is typically stiffer in the vertical direction than inthe horizontal) and preloads such as gravity which tend tokeep the rotor in the bottom half of the bearing . However,stiffness and preloads are only two such parameters.Machinery alignment conditions, balance conditions,lubricant conditions, rotative speed, rotor critical speeds,and other rotordynamic aspects will all affect the orbitshape under both normal and malfunction conditions.As shown in figure 2, when XY probes are present, the full2-dimensional motion of the shaft can be ascertainedas well as the maximum excursion of the shaft. ThisFigure 2: With an orthogonal probe pair, the shape of the orbit canbe ascertained, rather than just the amplitude observed by oneprobe or the other. In this example, the major axis of the ellipticalorbit aligns primarily with the X probe; consequently, it will observeapproximately twice as much vibration amplitude as will theY-probe.is because any 2-dimensional shape can be uniquelyidentified by the path its x- and y- coordinates trace out.A simple analogy, is that the orbit path is what you wouldsee if a pencil lead at the shaft’s centerline traced theshaft’s path on a piece of paper (amplified of course).Definition:Radial proximity probes in an orthogonal ‘XY’ pairare mutually perpendicular. That is, their angularorientation is 90 degrees apart, as shown in Figure 2.Vo l . 3 0 N o. 1 2 0 1 0 ORBI T 5
BACK TO BASICSIn contrast, a single radial transducer is only able(so-called “Figure 8”) patterns or interior loop patterns.to detect vibratory motion in a single axis. ForThis occurs when the vibration frequency in one axis isexample, if only the X transducer were installedmarkedly different from the frequency in another axis.in Figure 3, it would be unable to differentiateDepending on the probe orientations, one probe may see abetween the orbits of Figures 3A, 3B and 3C. Thesingle amplitude peak for each shaft revolution, while theorbit in Figure 3A would normally not indicate aorthogonal probe may see two or more peaks per shaftmachinery malfunction. However, the orbits inrevolution.Figures 3B and 3C have very large amplitudesin the ‘cross-axis’ direction that would not bedetected by the X transducer. It is clear that if wehad only the X transducer installed, machineryprotection and alarming would be seriouslycompromised, and malfunction analysis would benearly impossible.Figure 4 shows an example of a classic “figure 8” orbitshape incurred during a rub. Notice that one probe seesonly one-fourth as much vibration amplitude as theother probe, even though something abnormal is clearlyoccurring in the machine. For a conventional vibrationmonitoring system that monitors only the amplitude from aprobe mounted in a single plane, the orbit in Figure 4 wouldWhile one might be inclined to dismiss such scenariosnot generate any kind of machinery alarm, assuming thatas “infrequent” or “unlikely” this is not necessarily thethe amplitude alarm for the X probe was 3 mils (a typicalcase. By their nature, machinery malfunctions arealert level for large 3600 rpm steam turbines) and only theunpredictable. For example, following the turnaround ofX probe was installed in the machine.a large steam turbine, the bearing might be assembledor shimmed incorrectly; or, the machine might be alignedimproperly; or, thermal expansion conditions might causethe machine to assume incorrect alignment. All of theseare examples of conditions that can lead to extremepreload on a shaft, constraining its vibration to primarilya single plane, and resulting in a highly planar orbit shape.As has been shown, only when orthogonal probes arepresent at each radial bearing can the true amplitude ofthe vibration be ascertained, regardless of the orbit shapeor orientation. And only when this amplitude canbe ascertained can adequate machinery protectionbe ensured.Further, it is impossible to predict in advance the directionThe most prominent industry standard pertaining toin which this preload might act. A case in point occurredvibration monitoring systems for machinery protectionwhere a customer installed a balance correction weightapplications is American Petroleum Institute standardon their 650 MW steam turbine – based on vibrationAPI 670. The usefulness and applicability of this standardmeasurements that were made using only a single X probetranscends the petrochemical industries and hason each bearing. We recommended against this actionbeen employed across many industry’s as part of theirwithout the addition of Y probes to prove that the rootpurchasing specifications for vibration instrumentation.problem was in fact balance related. We suspected thatHowever, for some machines, such as hydro-generatorsbalance was not the root cause because we knew that in(highlighted in this issue of Orbit), this standard may notthe winter, the vibration levels would change significantlybe applicable. To understand the standard’s wide appealif a loading bay door was opened (indicative of a thermalwith end users, it is helpful to consider that nearly everyalignment sensitivity). Orbit plots, and shaft centerline dataparagraph in the standard is the result of an end userswould have provided us with the confidence to proceed, orexperience with vibration monitoring systems, leading torecommend an alignment change.“best practice” recommendations that were often acquiredRubs are another very common machinery problemthat can result in not only highly planar orbit shapes,but also unusual orbits that exhibit either exterior loop6 O R B I T Vol.30 No.1 2010through “doing it the wrong way” and then embeddingin the standard a series of guidelines that would preventother users from making similar mistakes.
BACK TO BASICSFigure 3A: This orbit is fairly normal and is slightly elliptical.The Y-probe observes approximately twice as much vibrationas the X-probe.Figure 3C: This orbit again has the same amplitude and frequency(1X) as the orbits of Figures 3A and 3B. However, something isclearly different as shown by the “figure 8” pattern of the orbit.With only an X-probe installed, this change in condition would bemissed. Indeed, the monitoring system would detect no changeat all between Figures 3A, 3B, and 3C. It is only when a Y-probe isinstalled that such important changes can be detected.Figure 3B: This orbit has the same amplitude in the X-axis asthe orbit of figure 3A, while the amplitude in the Y-axis hasapproximately doubled. If only an X-probe were installed, it wouldindicate no change in vibration from the orbit of Figure 3A, andwould be oblivious to the fact that amplitude in the Y-directionwas nearly 3 times as large as that in the X-direction.Figure 4: This orbit shows approximately 4 times as much vibrationin the X-axis as in the Y-axis. If only amplitude from the X-probe wasobserved, as would be typical from a radial vibration monitor withonly a single probe, such a machinery condition would be missed.Indeed, the X-probe would observe exactly the same vibrationamplitude as in Figures 3A, 3B, and 3C.Vo l . 3 0 N o. 1 2 0 1 0 ORBI T 7
BACK TO BASICSCentral to this is the mandate within API 670 for XYcosts of 100,000 an hour or more, even a single hourprobes at each radial bearing. The petroleum industry aresaved by the ability to perfo
for enhancing our technical leadership. Bently Nevada is the world’s leader in condition monitoring products and services and the Orbit will continue to be one of our primary educational and informational tools. 2011 will truly be an exciting year. From the Desk of Don Marshall Chief Marketing Officer, Bently Nevada Asset Condition Monitoring