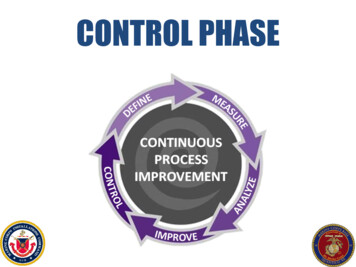
Transcription
CONTROL PHASE
DMAIC MethodologyDefineTollgate Review IDENTIFY OPPORTUNITYMeasureTollgate Review DESCRIBE AS-IS CONDITIONAnalyzeTollgate Review IDENTIFY KEY CAUSESImproveTollgate Review PROPOSE & IMPLEMENTSOLUTIONSControl SUSTAIN THE GAINTollgate ReviewGreen Belt Training - Control2
Learning Objectives: Control Phase Understand the tools necessary to complete theControl Phase. Develop a Control Plan to monitor and sustainimplemented improvements. Properly document and follow-up on completedprojects and events. Categorize and communicate project benefits. Explain Design for Six Sigma for new processes.Green Belt Training - Control3
Control Plan
What Is a Control Plan? Control Plans provide a written summarydescription of the systems used in minimizingvariation in the improved process. Control Plans do not replace informationcontained in detailed instructions (SOPs). The Control Plan describes the actions that arerequired at each phase of the process to assurethat all process outputs will be in a state ofcontrol. Based on Critical Customer Requirements (CTX’s).Green Belt Training - Control5
Control Plans Answer the Following Questions1. What is the process that is being controlled?2. What are the process outputs that are being monitored /controlled?3. What are the inputs that are being monitored /controlled in order to keep the output at its target level?4. How are the inputs and outputs being measured,monitored, and controlled?5. How does someone react when the inputs or outputsare not in control?Green Belt Training - Control6
Control System Contents Control Systems contain: Critical inputs. Desired outputs / performance levels. Capture and report of actual processperformance measures. A feedback mechanism to report deviations inactual outputs from desired levels. Adjustments to the process. Can be reinforcing (amplify the deviation) orbalancing (bring back to equilibrium) balancing is normally what gets implemented.Green Belt Training - Control7
A Basic Control SystemInspection orMeasurementor MeasurementControl Lag Time between Operation and whenany applied adjustment takes effect.Green Belt Training - Control8
Process Control Plan – Example No standard template, completely customizable tofit the organization’s needs. Ultimately, the Control Plan is a living documentreflecting current methods of control andmeasurement systems used.Process/EquipmentInput /OutputMeasurementTechniqueSpecification/ ocessLead TimeTime (Supplyto Delivery)275 secs. /25 secs.Haltproduction,investigateGreen Belt Training - ControlEvery order9
Control Plan Tips Establish controls to detect defects. Use illustrations. Use flow diagrams. Use work instructions that really work. Use reaction plans that really work. Focus on the quality of documentation, not the quantity. Use workers to help write the instruction. Clearly lay out authorities, roles, and responsibilities.Green Belt Training - Control10
Control Plan Tips (Cont.) Focus on the identification of nonconforming services. Ensure segregation by identification or location toprevent inadvertent use. Address the need for recall or previously providedservice. Ensure the benefit of rework versus loss. Ensure that rework actually produces first qualityservice. Ensure that corrective actions are initiated whenevernonconforming services are provided.Green Belt Training - Control11
Control Plans Summary Control Plans can be likened to sustainment in5S. Statistical Process Control is not successfulwithout religious use of Control Plans. Control Plans are living documents. Ifprocesses change and a new variation causedevelops, add it to the Control Plan.Green Belt Training - Control12
Project Closeout /Sustainment
Bringing the Event to Completion1. Ensure that: All feasible process improvement ideas have beenimplemented. The project sponsor / process owner and personnel from theaffected work area have been adequately trained on theprocess changes. Event objectives have been met or exceeded (Validate). Processes are updated. Needed controls are instituted in the process.2. Quantify event benefits Return on Investment (ROI)Green Belt Training - Control17
3 Week RIE Follow-Up ChecklistGreen Belt Training - Control18
Kaizen/RIE Follow-Up Beyond the EventGreen Belt Ensure standard work is implemented. Foster success – market results. Complete and submit documentation onevent. Handoff to Event Sponsor at completion ofevent week.Green Belt Training - Control19
Kaizen/RIE Follow-Up Beyond the EventEvent Sponsor / Process Owner Monitor (Control Charts, Control Plans, Gemba). Visit the area frequently for several weeks after theImprovement Event. Address stakeholder issues and concerns. Recognize participants of event and celebratesuccess. Is Takt Time being achieved? Keep up the pressure completing outstandingaction items.Green Belt Training - Control20
Out Brief TipsFinal Tollgate Review - clearly captures the results of the event.Should include: Charter informationTools utilizedImprovements madeEvidence of data driven decision makingCurrent / Future State process flows and metricsROI calculationsOther improvement opportunitiesCPI Project Tollgate Template -Performanceand-External-Affairs/Green Belt Training - Control21
What’s a Quad Sheet ? Prepared for each Kaizen / RIE by the Project Sponsorwith the assistance of the Green Belt. Started at beginning of the Kaizen / RIE. A key document in the formal submittal of the event’sresults. Documents key Kaizen / RIE information, metrics, status& financial results as an executive summary on one page. A living document that is periodically updated during andafter the event as results are validated.Green Belt Training - Control22
Quad Sheet - TemplateProject / Event TitleBackgroundResultsGoalsTimeline / BenefitsGreen Belt Training - Control23
Lessons Learned Every improvement effort offers a lesson. It is what we do with these lessons that matters. For successful projects, we want to document ourefforts and conclusions to repeat the success. If not successful, we want to document whatwent wrong to prevent repeating the samemistakes. The availability of this type of information cangreatly accelerate future efforts.Green Belt Training - Control24
Definition of SustainmentConsistently adhere to process improvements,ensuring all benefits are fully realized. The old way is gone, the new way is the way. Human nature resists change and reverts to old mPerformancewithoutSustainmentBaselineRIE #1RIE #2RIE #3RIE #4Green Belt Training - Control25
Kaizen / RIE Follow-Up Beyond the EventDaily Board WalkCritical element of post-event follow upGreen Belt Training - Control26
RedeploymentRedeployment The movement of people from a process that has beenimproved either through attrition, reassigning them toanother CPI event or to other critical work.Ultimately, the key objective of a CPI Thinkingorganization is to reduce the amount of human effortrequired per unit of output, in other words increaseproductivity and capacity.When to use redeployment To make up for current attrition.Eliminate or reduce overtime.Reduce contractor support.Reduce work backlog.Green Belt Training - Control27
Replication OpportunitiesIdentify key lessons learned and data from thisproject that may be useful in other areas of thebusiness, or for other projects: Data about upstream process (input) measures. Data on problem areas outside your team’s scope,but important to the business. Reduction of waste and non-value added activities. Better utilization of resources. Benchmarking information. Customer requirements.Green Belt Training - Control28
Benefits
Review: Triple Constraints of Projects Project ManagementConstraintsCOSTTIME Quality (Better) Clear and Specific Time (Faster) Amount of Time to completeprocess tasks.QUALITY Cost (Cheaper) Money and Effort Prioritizing Constraints Should be based on the view of the customer.Green Belt Training - Control30
Benefit CategoriesGoal: Reduce Costs Metric: Type I Benefits – Cost Reductions to Budget LineItems. Example: Same work done with fewer resources.Goal: Increase Speed (Reduce Time) Metric: Type II Benefits – Process Time Reduction / ImprovedResource Utilization. Example: More done with same resources.Goal: Improve Safety and Quality of Life Metric: Type III Non-Financial / Other Benefits. Example: Risks to assets or personnel reduced. Customer satisfaction.Green Belt Training - Control31
Benefit Categories Flow ChartAt the Project – Were assets freed up?At the Business – What did we do with the assets?WY: Work YearBenefitsQuantifiableNoTYPE IIIe.g. SaferWorkplaceYesNoIs it less“stuff”?Is it awholebody?Morethan oneWY?NoYesYesYesTYPE I“STUFF”* Materials Equipment Inventory InfrastructureYesAttrite?CSS: ContractorSupport ServicesTYPE IYesTYPE INoNew workapproved?YesYesYesTYPE II Customers of improved process havedollars to give back. Includes less budgeted overtime. Customers of improved processhave dollars to give back. Customers of improved process haveTYPE IINoTYPE IIWY’s spreadacross multipledepartments orless than one WYNoReduceCSS?*Some “stuff” can be Type II (e.g.,reduce Infrastructure, but not enough toclose a building.Nodollars to give back. Business can now execute new work thatwas planned and budgeted for but wasabove and beyond current capacity.Available AssetGreen Belt Training - Control32
Design for Six Sigma
Design/Re-Design ApproachesDesign For Six Sigma (DFSS) methods would bethe method of choice when: There is no current process to fulfill customerrequirements (need a brand new process). The process is incapable of producing qualityproducts / services (better to start fromscratch than to fix the process).Green Belt Training - Control34
Design For Six Sigma (DFSS) DMADV: Define Measure Analyze Design Verify. Example: DFSS was use to develop the CT Scanner.Green Belt Training - Control35
DMADV DefinedDDefine the goals of the design activity. What is beingdesigned? Why? Use QFD or the Analytic HierarchicalProcess to assure the goals are consistent with customerdemands and enterprise strategy.MMeasure customer input to determine what is critical toquality from the customer’s perspective. Translate customerrequirements into project goals.Analyze innovative concepts for products and services tocreate value for the customer. Determine performance ofsimilar best-in-class designs.Design the new product, service or process. Use predictivemodels, simulation, prototypes, pilot runs, etc. to validatethe design concept’s effectiveness in meeting goals.Verify the design’s effectiveness in the real world.ADVGreen Belt Training - Control36
What We Have Covered: Control PhaseControl Phase Tools Control Plans. Project documentation and out-briefs. Project Benefits. DFSS/DMADV.Green Belt Training - Control37
Training Closeout
Continuous Process Improvement Continuous Process Improvement (CPI) Incremental Improvement. CPI is a proven method for improving processes,products, and logistics and has now proven usefulacross the full spectrum of operational,administrative, support, and R&D functions. Process Improvement will always be present insuccessful organizations regardless of the labelassociated with it. Greenbelts are on the frontlines of CPI.Green Belt Training - Control39
Lean Six Sigma SummaryLean is about flow. Increase process flow by eliminating waste. Waste is anything – effort, costs, or workthat adds no value in the eyes of thecustomer.Six Sigma is about quality and variation. Reducing defects by eliminating variation. Reducing differences in similar or identicalprocesses.Green Belt Training - Control40
Expectations of Green BeltUnderstand and be able to apply the basic conceptsof Lean Thinking and Six Sigma.Have the ability to lead a team through a Kaizen /RIE Event.Green Belt Training - Control41
Continuous Improvement for Your Career in CPIFirst step – finishing GB training.Next steps Get involved in a CPI event next week! Pursue Green Belt Certification (Lead aRIE/Project). Pursue Black Belt Training and Certification.Yellow BeltGreen Belt Training - Control42
Green Belt Certification Requirements Lead a Project / Event or significant support of BlackBelt Project Project/Event requirements: Black Belt Mentor (G-7 approved) Approves project/event Mentors Green Belt during project/event Provides P&I with recommendation for certification Demonstrated use of Lean Six Sigma Tools Must be a benefit to the Marine Corps Belt determines tools based on project/event Required tools - all projects/eventsGreen Belt Training - Control43
Business Solution Request FormDo you know an organization or process that needs some assistance?We can help!Just fill out our Business Solutions Form and we will provide assistance!Green Belt Training - Control44
Green Belt Mentoring RequirementsMentors provide the following services: Provide guidance on project charters. Provide event/project coaching and assistance withmeetings (as needed). Provide project assistance (tool identification andutilization). Review and provide guidance for tollgate and finalout briefs prior to presentation.Green Belt Training - Control45
Mentor Support AvailabilityCPI mentoring is based on the following: Command needs always have priority. Availability – First come, first serve. On a “demand pull” basis; you must arrange it. Attend scheduled periodic meetings as arranged. Mentors are to enable the project teams; teams stillmust be prepared to work.Green Belt Training - Control46
Green Belt Resources Green Belt Course Training Material Templates– G-7 External G-7-Performance-and-External-Affairs/– Useful templates uploaded as requested.Once you are CertifiedWE ARE LOOKING FOR OTHERS THAT AREINTERESTED IN TEACHING!Green Belt Training - Control48
What We Have Covered: Course GoalsUnderstand Lean Six Sigma (LSS) / ContinuousProcess Improvement (CPI) tools and how to applythem to your workplace.Understand the impacts of the Triple Constraints onprocesses.Facilitate small Projects or Events to attack andsolve current day problems.Assist Black Belts on Command-wide Projects andEvents.Green Belt Training - Control49
Additional Training InformationMilitary Students The below training event codes (Table 77)replaced the Military Service School codes from(Table 02). LX 3 LEAN SIX SIGMA - BLACK BELTLE 3 LEAN SIX SIGMA - EXECUTIVE BELTLG 3 LEAN SIX SIGMA - GREEN BELTLY 3 LEAN SIX SIGMA - YELLOW BELTGreen Belt Training - Control50
Prepared for each Kaizen / RIE by the Project Sponsor with the assistance of the Green Belt. Started at beginning of the Kaizen / RIE. A key document in the formal submittal of the event's results. Documents key Kaizen / RIE information, metrics, status & financial results as an executive summary on one page.