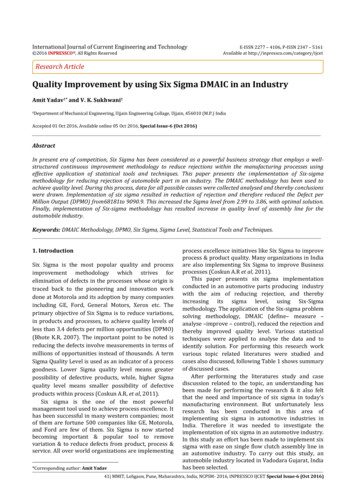
Transcription
International Journal of Current Engineering and Technology 2016 INPRESSCO , All Rights ReservedE-ISSN 2277 – 4106, P-ISSN 2347 – 5161Available at http://inpressco.com/category/ijcetResearch ArticleQuality Improvement by using Six Sigma DMAIC in an IndustryAmit Yadav†* and V. K. Sukhwani††Departmentof Mechanical Engineering, Ujjain Engineering Collage, Ujjain, 456010 (M.P.) IndiaAccepted 01 Oct 2016, Available online 05 Oct 2016, Special Issue-6 (Oct 2016)AbstractIn present era of competition, Six Sigma has been considered as a powerful business strategy that employs a wellstructured continuous improvement methodology to reduce rejections within the manufacturing processes usingeffective application of statistical tools and techniques. This paper presents the implementation of Six-sigmamethodology for reducing rejection of automobile part in an industry. The DMAIC methodology has been used toachieve quality level. During this process, data for all possible causes were collected analysed and thereby conclusionswere drawn. Implementation of six sigma resulted in reduction of rejection and therefore reduced the Defect perMillion Output (DPMO) from68181to 9090.9. This increased the Sigma level from 2.99 to 3.86, with optimal solution.Finally, implementation of Six-sigma methodology has resulted increase in quality level of assembly line for theautomobile industry.Keywords: DMAIC Methodology, DPMO, Six Sigma, Sigma Level, Statistical Tools and Techniques.1. Introduction1 SixSigma is the most popular quality and processimprovement methodology which strives forelimination of defects in the processes whose origin istraced back to the pioneering and innovation workdone at Motorola and its adoption by many companiesincluding GE, Ford, General Motors, Xerox etc. Theprimary objective of Six Sigma is to reduce variations,in products and processes, to achieve quality levels ofless than 3.4 defects per million opportunities (DPMO)(Bhote K.R, 2007). The important point to be noted isreducing the defects involve measurements in terms ofmillions of opportunities instead of thousands. A termSigma Quality Level is used as an indicator of a processgoodness. Lower Sigma quality level means greaterpossibility of defective products, while, higher Sigmaquality level means smaller possibility of defectiveproducts within process (Coskun A.R, et al, 2011).Six sigma is the one of the most powerfulmanagement tool used to achieve process excellence. Ithas been successful in many western companies; mostof them are fortune 500 companies like GE, Motorola,and Ford are few of them. Six Sigma is now startedbecoming important & popular tool to removevariation & to reduce defects from product, process &service. All over world organizations are implementing*Corresponding author: Amit Yadavprocess excellence initiatives like Six Sigma to improveprocess & product quality. Many organizations in Indiaare also implementing Six Sigma to improve Businessprocesses (Coskun A.R et al, 2011).This paper presents six sigma implementationconducted in an automotive parts producing industrywith the aim of reducing rejection, and therebyincreasing its sigma level, using Six-Sigmamethodology. The application of the Six-sigma problemsolving methodology, DMAIC (define– measure –analyse –improve – control), reduced the rejection andthereby improved quality level. Various statisticaltechniques were applied to analyse the data and toidentify solution. For performing this research workvarious topic related literatures were studied andcases also discussed, following Table 1 shows summaryof discussed cases.After performing the literatures study and casediscussion related to the topic, an understanding hasbeen made for performing the research & it also feltthat the need and importance of six sigma in today’smanufacturing environment. But unfortunately lessresearch has been conducted in this area ofimplementing six sigma in automotive industries inIndia. Therefore it was needed to investigate theimplementation of six sigma in an automotive industry.In this study an effort has been made to implement sixsigma with ease on single flow clutch assembly line inan automotive industry. To carry out this study, anautomobile industry located in Vadodara Gujarat, Indiahas been selected.41 MMIT, Lohgaon, Pune, Maharashtra, India, NCPSM- 2016, INPRESSCO IJCET Special Issue-6 (Oct 2016)
Amit Yadav et alQuality Improvement by using Six Sigma DMAIC in an IndustryTable 1 Summary table of discussed caseS.N.1.2.3.4.5.6.Author NameMehdiuzZaman etal, 2013PrabhakarKaushiket al,2012Darshan D. Patel etal,2014Sunil Dambhare etal, 2013Mahesh S. Shinde etal, 2012M. Sokovic etal,2006ProblemRejection of weldingelectrodes inManufacturing industryMethod UsedSix sigmaDMAICSupporting ToolsProcess mapPareto chartIshikawa (fishbone) diagramResultsSigma levelcomes at 4.43from 3.41Sigma levelcomes at 5.46from 1.40Rejection of bush inbicycle chainmanufacturing companySix sigmaDMAICBrain stormingProcess mapPareto chartIshikawa diagramReduction of productioncost & process in bearingmanufacturing industrySix sigmaDMAICCause and effect diagramProcess capability analysisRework up to 16% boresper month in an engineblock manufacturingcompanySix sigmaDMAICControl chartsMR chartHistogramWeld defects in TungstenArc Welding (GTAW)process used forAerospace applicationSix sigmaDMAICDetailed process flow chartCause and effect matrixSigma levelcomes at 3.50from 2.98High production cost inautomotive partsproducing companySix sigmaDMAICPareto chartThought process mapControl chartOverall reductionin production cost2. Research Problems & ObjectivesA research problem is one which requires a researcherto find out the best solution for the given problem, i.e.,to find out by which course of action the objective canbe attained optimally in the context of a givenenvironment. In this study the research problem is toimplement the six sigma DMAIC method for thereduction in high rejections of automobile part clutchin an automobile parts producing industry to reducethe process variation. Detailed research problems areas follows.1) High rejection of clutches in single shift i.e.15 outof 220 on single assembly line of the industry.2) High Defect per Million Output (DPMO) thatis681813) Low process sigma level which is only 2.99Globalization has opened the doors of world market toIndian organizations, which in turn forcing them tobring their products & services to world class level. Forthat, along with various tools Six Sigma is becomingpopular in India. Considering specific need of Indiancompanies to implement Six Sigma effectively; themain objectives of this research work are;1) Understand the need of Six Sigma in anOrganization.2) Reduce the rejection of clutches producing in anautomotive industry in single shift.3) Reduce the Defect per Million Output (DPMO).4) Increase the process sigma level of that particularprocess of clutch assembly.5) Evaluate and compare Six Sigma and the existingway of workingSigma levelcomes at 3.76from 2.47Rework reducedfrom 16% boresper month to2.20% bores permonthTo achieve the above mentioned objectives DMAICmethodology has been used in present research.3. Methodology adoptedThe paper deals with an application of Six SigmaDMAIC (Define– Measure- Analyse- Improve- Control)methodology. DMAIC is a process that eliminatesunproductive steps, often focuses on newmeasurements, and applied technology for continuousimprovement as shown in table 2. Implementation ofDMAIC Methodology took place in five phases whereProblem identification and definition takes place indefine phase. After identifying main processes, theirperformance is calculated in measure phase with thehelp of data collection. Root causes of the problemwere found out in analysis phase. Solutions to solveproblem were implemented in improve phase.Improvement is maintained and assured in controlphase.3.1 Define phaseThe present study has been conducted in anautomobile industry “X automobileLtd.” situated atVadodara Gujarat, India. The industry produces variousclutches used in heavy vehicles and also variousassembly parts of clutch. The problem were found in asingle flow assembly line of a clutch in which 15clutches were rejected out of 220 in one shift due toclutch plate keyways depth not as per the specification.The data were obtained from monthly report of firm’squality department. Clutch plate is one of the manymanufactured components for the transmissionassembly. It’s a flat metal circular plate into which 4key ways.42 MMIT, Lohgaon, Pune, Maharashtra, India, NCPSM- 2016, INPRESSCO IJCET Special Issue-6 (Oct 2016)
Amit Yadav et alQuality Improvement by using Six Sigma DMAIC in an IndustryAre made using stamping (manufacturing process) asshown in fig.1. The depth of the keyways should be0.635cm and width should be 2.5 cm as per thespecification of the firm.Fig.1 Clutch plate keyway depthSo, on the basis of above mentioned rejection data,DPMO has been calculatedfor that particularproduction line with the help of following formula(www.isixsigma.com)DPMOFig.2 Process flow chart for keyway making process (Total defect / Total opportunity) x 106 (15 / 220) x 10, 00,000 681813.2 Measure phaseOn the basis of this DPMO we have calculated theProcess sigma level with the help of formula(www.isixsigma.com)Process sigma level 0.8406 {SQRT[29.37 – 2.221 x Ln (DPMO)]} 0.8406 {SQRT[29.37–2.221 x Ln (68181)]} 2.99Table 2 Details of DMAIC phasesPhaseDefine (D)Measure (M)Analyse (A)Improve (I)Control (C)DetailsSet project goals and objectivesMeasure the defects wherethey occurEvaluate data/information fortrends, pattern and root causesDevelop, implement andevaluate Solution targeted atidentified root causesMake sure that the problems has beencleared & method is improvingAfter getting this data it is clear that production of theline is at low sigma level and improvement isrequired.Since, the rejection of clutches occurs due tokeyways depth of clutch plate, we decided to applyDMAIC process on press shop where keyways weremade on clutch plate. For this purpose a process flowchart of keyway making process has been preparedwhich shows the various steps involve for defining theprocess.Process flow chart is shown in fig.2The measure phase consists of knowing, understandingthe process thoroughly, data collection, validation ofthe collected data and stating whether the process iscapable or not.Knowing the process is important as wemust know where to and what to collect the data from.It includes taking all the readings of the depths of thekeyways and to see where the mean of all thesereadings lie with respect to the expected value of 0.635cm. To solve the problem of identifying the exactkeyway where there was variation in depth, a smallmark was placed below one of the keyways and thatkeyway was identified as keyway 1 and goingclockwise around the clutch plate the keyways wasnamed 2, 3, 4 in successive manner. The measurementsof the depth of all four keyways were taken in every 15minutes are shown in the Table 3 and the datacollected was as follows.Table 3 Measurements of the depth of keywaysKeyways Serial 190.6170.6190.6220.6250.62543 MMIT, Lohgaon, Pune, Maharashtra, India, NCPSM- 2016, INPRESSCO IJCET Special Issue-6 (Oct 2016)
Amit Yadav et alQuality Improvement by using Six Sigma DMAIC in an IndustryThe table 3 clearly shows that the depth of key way 2and key way 4 is not as per the specification or there ishigh variation in the depth of them. Therefore in orderto observe these variations clearly, a process variationchart has been prepared which is shown in fig.3 Inprocess variation chart red and purple lines stands forkeyways 2 & 4 which clearly shows the high variationof depth from mean, whereas green and blue linesstands for keyways 1 and 3. The process variationchart helps to show the variation of depth of keywaysclearly and also provides strong base to move forwardfor analysis phase.overlooking the process it was noticed that the dieteeth dimensions were not according to therequirements, which was causing the variations inkeyway 2 and 4. Thus the ‘Die Teeth Defect’ wasidentified as the major cause of variation in the keywaydepths of keyways 2 and 4 of the clutch plate. Tosummarize this Pareto chart shown in fig.5 has beenprepared which includes the detailed observationreadings like frequency of defects occurring and fromwhich cause they occur and their percentage of occur.A Pareto chart is given by Vilfredo Pareto(18481923) an Italian economist later it is adapted by JosephJuran, is a type of chart that contains both bars and aline graph, where individual values are represented indescending order by bars, and the cumulative total isrepresented by the line.Fig.3 Variation in the keyway depth3.3 Analyze phaseFrom the statistical processes performed we can safelysay that keyway 2 and keyway 4 were rejected. Sincethe process variation chat clearly shows the variationof depth of keyway 2 and 4 is high, it is necessary toanalyze and find the cause which is causing thevariation in depths of keyway 2 and 4. A Cause andeffect diagram shown in fig.4 is constructed to analyzethe causes that are causing the depth variation.Fig. 5 Pareto chartWhere, in Pareto ChartA Defect due to die teethB Defect due to clutch plate mountingC Defect due to pressure of cutD Defect due to material of clutch plateE Other3.4 Improve phaseFig.4 Cause and effect diagramCause & effect diagram provides areas of observation,on the basis of that, deep monitoring has been carriedout with the help of industrial staff and experts of theprocess. Each and every area were deeply monitoredand analysed by the team. From observations whileThe goal of the DMAIC improve phase is to identify asolution to the problem that the project aims toaddress. This involves brainstorming potentialsolutions, selection solutions to test and evaluating theresults of the implemented solutions. The major toolused in this phase is brainstorming, since the rootcause encountered in analyse phase is die teeth defectwhich required the involvement of each and everyperson related to the process for getting the optimalsolution. The major defect of the cutting keyway onclutch plate is found in die teeth as shown in fig.6, sothe decision of Brain storming team is to replace thedie with the new one.44 MMIT, Lohgaon, Pune, Maharashtra, India, NCPSM- 2016, INPRESSCO IJCET Special Issue-6 (Oct 2016)
Amit Yadav et alQuality Improvement by using Six Sigma DMAIC in an Industry43.532.521.510.50Sigma levelBeforeFig.6 Die teethAfterFig.7 Visible resultsSome other solution wasalsobrainstorming session likediscussedwhile1) A computer model or other simulation can bebeneficial in the evaluation process using CADsoftware such as Cero which can assemblecomponents as well as simulate the working.2) Other manufacturing processes such as using alaser cut machine, CNC machine or a manual selfvalidated machine.For the effective and efficient six sigmaimplementation, it is prime importance of choosing theoptimal solution for improvement. Thus the best waywas to modify the system by replacing the die andhence improving the process.3.5 Control phaseThe primary objective of the DMAIC Control phase is tomake sure that almost the problems has been clearedand method is improving, hence to ensure thisrequirement of control phase we have again performedthe DPMO and process sigma level calculation whichare shown below1) After implementation of the six sigma DMAIC,rejection of the clutch during one shift has beenreduced from15 out of 220 units to 2 out of 220units according to the data obtained by the firm’squality department.2) Then DPMO has been calculated again for this data.3) DPMO (Total defect / Total opportunity) x 106 (2 / 220) x 10, 00,000 9090.94) After that process sigma level of improved processhas been calculated on the basis of new DPMO,Process sigma level 0.8406 {SQRT[29.37 – 2.221 x Ln (DPMO)]} 0.8406 {SQRT[29.37– 2.221 x Ln(9090.9)]} 3.86A chart has been prepared on the basis of abovecalculations, to show the visible results of increase insigma level achieved which is before and after 2.99 and3.86 respectively as shown in fig.74. Results &discussionsThe present research work concerned with thesuccessful implementation of Six Sigma DMAIC toreduce the rejection of clutches on single flowproduction line in an automobile industry. For therealization of the project, a Six Sigma DMAIC approachwas implemented.The use of the DMAIC methodology for the differentphases of the project helped to eliminate some causesof rejection in the process. The application of the Sixsigma problem solving methodology, DMAIC (define–measure – analyze –improve – control) reduced therejection and thereby improved quality level. Variousstatistical techniques were applied to analyze the dataand to identify solution. Calculations such as the sigmalevel and DPMO helped the team to understand whichcauses were more critical to the process.Analysis was carried out with the help of statisticaltools like process flow chart, process variation chart,fish bone diagram and Pareto chart, where processvariation chart, fishbone diagram and Pareto chartwere played key role in this research work since,process variation chart helps to identify key problemarea, fishbone diagram helps to find possible causes ofthat problem and Pareto chart helps to identify rootcause.After the successful implementation of six sigmaDMAIC, clutches rejection were felt down from 15 to 2out of 220 in single shift, defect per millionopportunities were felt down on 9090.9 from 68181and rise in process sigma level from 2.99 to 3.86 hasbeen achieved and thus quality level of the assemblyline has got improved.ConclusionsThis research is concerned with the analysis of theproblem of rejection of clutch in an automobileindustry due to the variations in depth of keyway of theclutch plate and to reduce them by six sigma DMAICimplementation following important conclusions weredrawn1) Results of this study reveal that Six Sigmaimplementation can provide a breakthroughimprovement in an automobile industry.45 MMIT, Lohgaon, Pune, Maharashtra, India, NCPSM- 2016, INPRESSCO IJCET Special Issue-6 (Oct 2016)
Amit Yadav et alQuality Improvement by using Six Sigma DMAIC in an Industry2) Following improvements were obtained by sixsigma DMAIC implementation3) Rejection of clutches reduced from 15 out of 220to 2 out of 220 in single shift, which is a hugereduction of 87%.a) Reduction in DPMO from 68181to 9090.9.b) Increase in process sigma level from 2.99 to 3.86,which is increased by 30%.c) Finally, quality improvement of the assembly linehas been achieved with sigma level 3.86.Even though this is a small research work with a smallimpact on the company’s production, it can be certainlyconcluded that, six sigma is really a tool that can beused to obtain positive results in processimprovements. If the methodology is applied throughall the production lines, it would be very beneficial forthe company as it would result in significant saving ofresources.ReferencesBhote K.R, (2007), The Ultimate Six sigma beyond qualityexcellence to total business excellence, PHI Learning, NewDelhi, India, pp. 2.Coskun A.R, Tamer C and Serteser M, (2011), Six sigmaprojects and personal experiences, Intech,Turkey, pp,5,772-679.Dambhare Sunil, AphaleSiddhant, KakadeKiran, ThoteTejas,and BoradeAtul, (2013), Productivity Improvement of aSpecial Purpose Machine Using DMAIC Principles: A CaseStudy, Journal of Quality and Reliability Engineering, pp. 113.Patel D D, Gawande K R, (2014), Productivity improvementthrough six sigma methodology in bearing manufacturing,International journal for research in applied science andengineering technology, 2,(3 ) pp, 233-239.PrabhakarKaushik, DineshKhanduja, KapilMittal, PawanJaglan, (2012), A case study: Application ofSix Sigma methodology in a small and medium‐sizedmanufacturing enterprise, The TQM Journal, 24, (1), pp, 416.Shinde M S, Inamdar K H, (2012), Improving TIG WeldingQuality using DMAIC, International Journal of Science andResearch (IJSR), 3, ( 6), pp, 2379-2382.Sokovic M, Pavletic D &Krulcik E, (2006), Six Sigma processimprovement in automotive parts production, journal ofAchievements in Materials and Manufacturing Engineering(JAMME), 19, (1), pp, 96-102.Zaman Mehdiuz, Pattanayak S K, and Paul A C, (2013), Studyof feasibility of six sigma implementation in amanufacturing industry: A case study, InternationalJournal of Mechanical and Industrial Engineering (IJMIE),3,(1) , pp, 96-100.46 MMIT, Lohgaon, Pune, Maharashtra, India, NCPSM- 2016, INPRESSCO IJCET Special Issue-6 (Oct 2016)
are also implementing Six Sigma to improve Business processes (Coskun A.R et al, 2011). This paper presents six sigma implementation conducted in an automotive parts producing industry with the aim of reducing rejection, and thereby increasing its sigma level, using Six-Sigma methodology. The application o