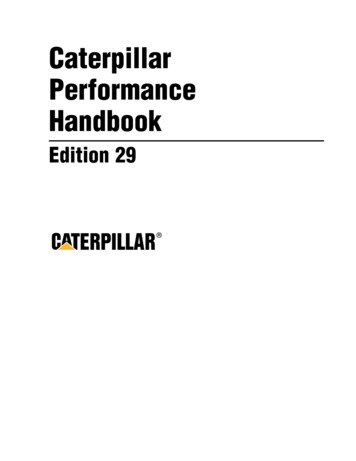
Transcription
CaterpillarPerformanceHandbookEdition 29
CONTENTSPagePreface . . . . . . . . . . . . . . . . . . . . .4Operator andMachine Protection . . . . . . . . .5Replacement Parts Warning . . . .7Nomenclature . . . . . . . . . . . . . . .8TRACK-TYPE TRACTORS1AGRICULTURAL TRACTORS2MOTOR GRADERS3EXCAVATORS4BACKHOE LOADERS5SKIDDERS6PIPELAYERS7WHEEL TRACTOR-SCRAPERS8CONSTRUCTION & MINING TRUCKS/TRACTORS9ARTICULATED TRUCKS10WHEEL TRACTORS SOIL/LANDFILL COMPACTORS11WHEEL LOADERS12TRACK LOADERS13INTEGRATED TOOLCARRIERS14TELESCOPIC HANDLERS15PAVING PRODUCTS16ELPHINSTONE UNDERGROUND MINING MACHINES17HYDROMECHANICAL WORK TOOLS181
ENGINES19FORMER MODELS20OWNING & OPERATING COSTS21TIRES22MINING AND EARTHMOVING23LOGGING AND FOREST PRODUCTS24STOCKPILE COAL HANDLING25LAND CLEARING26WASTE DISPOSAL27TABLES28INDEX293
PREFACEMachine performance must ultimately be measured in unit cost of material moved, a measure thatincludes both production and costs. Factors bearingdirectly on productivity include such things asweight to horsepower ratio, capacity, type of transmission, speeds and operating costs. The Performance Handbook considers these factors in detail.There are other less direct machine performance factors for which no tables, charts or graphs are possible. Serviceability, parts availability and operatorconvenience are examples. In comparing machineperformance, all factors should be considered. ThisHandbook is intended as an aid which, when coupledwith experience and a good knowledge of localconditions, can assist in estimating true machineperformance.Many sections of the Handbook include tables orcurves showing cycle times or hourly production figures for Caterpillar machines under certain conditions. Statements of conditions always accompanyor precede the curves or tables. Before using any performance information in this Handbook, a completeunderstanding of the qualifying conditions is essential.The data is based on field testing, computer analysis, laboratory research and experience; and everyeffort has been made to assure their correctness.However, all such data is based upon 100% efficiency in operation — a status which cannot beachieved continuously even under ideal conditions.Thus, in using such performance and productiondata, it is necessary to correct the results indicatedin the handbook tables by appropriate factors. Thisallows for the anticipated actual job efficiency, operator efficiency, material characteristics, haul roadconditions, altitude and other factors which mayreduce performance or production on a particular job.4Methods for estimating machine owning and operating costs vary widely, depending on locality, industry practices, owner preferences and other factors.One method is suggested in the Handbook sectionon Owning and Operating Costs. When used withgood judgment, it has provided reasonably accurateestimates in the past. Included in the Owning andOperating Section are guidelines, based on workingconditions, to assist in estimating consumption offuel and lubricants, tire life and repair costs forCaterpillar machines. However, what one Handbookuser regards as “excellent” conditions, another mayconsider “severe” or “average”, depending on his ownexperience and basis of comparison. Therefore, theseguidelines should be considered only approximations.Caterpillar Inc. has made every effort to assurethat the information contained in this Handbook isaccurate and is a fair statement of the results to beachieved in the circumstances indicated. However,because of the many variables involved in estimating the production or performance of earthmovingmachinery, their consumption of fuel and lubricants,tire life and repair costs, and the possibility of inadvertent errors or omissions in assembling this data,Caterpillar cannot and does not imply that all datain this book are complete nor that this level of performance will be achieved on a given job.Specifications shown in this Handbook were current at time of printing. However, due to Caterpillar’smany machine improvement programs, specifications and materials may change without notice. Forcurrent specifications relating to a machine’s performance, please refer to the most recent Caterpillarproduct specification sheet.Caterpillar Inc.
OPERATOR ANDMACHINE PROTECTIONA well trained operator, working under suitableconditions, utilizing a modern, properly-equippedmachine provides a machine-operator team capableof giving maximum production. These factors, alongwith appropriate job site rules and communicationprocedures, are essential to coordinate people andmachines working together. Appropriately protectedand maintained machines are less likely to sufferpremature component failure or damage, and giveoperators the confidence and assurance they needto carry out their work. Furthermore, training isnot complete until the operator reads, understandsand agrees to follow the instructions provided in theOperation and Maintenance Manual included withevery Caterpillar machine.Employers have a duty to provide a safe work placefor their employees. The purchaser of a Caterpillarmachine has a duty to review his/her particular application and job site for the machine to identify potential hazards inherent to that application or job site.Based on the results of this hazard analysis, theappropriate operator and machine protection configuration can be determined.Caterpillar designs, builds, and tests its productsto ensure the safety of operators, maintenance persons, service persons, and bystanders. Caterpillar provides as standard equipment the appropriate operatorand machine protection for most applications. However, particular applications may require additionaloperator and/or machine protection. Caterpillar offersrelated options for most such applications. However,there may be very special applications where theCaterpillar Dealer or the Purchaser may want to fabricate, or request Caterpillar to provide, custom orspecial guarding. Your Caterpillar Dealer can helpyou with this hazard analysis and guarding configuration process.I. Operator Training and Protection PracticesRemember that any kind of machine or mechanicaldevice can be hazardous if not kept in good condition, or if operated by careless or improperly trainedoperators, or if operated in an irresponsible manner.Listed below are some recommended basic stepsthat can be broadly applied to most work environments: Train operators for the job they are assigned todo. The length and type of training must complywith governmental and local regulations whereverthey apply. As an example, machine operators inmining activities must be trained in accordance withMine Safety and Health Administration (MSHA)regulations. Where specific regulations do not apply,no operator should be assigned to a job until he orshe meets the following minimum requirements:– Completes proper training to operate the assignedmachine and understands that seat belts must beworn whenever seated in operator’s compartment.– Reads and understands the Operation & Maintenance manual for that machine, and knowsthat a copy of that manual is stored in the operator’s compartment.– Reads and understands the EMI (EquipmentManufacturer’s Institute), CIMA (ConstructionIndustry Manufacturers Association), or anyother furnished manual related to rules for safemachine operation and identification of hazards.– Has appropriate personal safety equipment andknows how to use it. This includes such thingsas hard hat, gloves, safety glasses, hearing protection and safety shoes.– Knows what the job requirements are, whatother machines are working in the area, and isaware of any hazardous conditions that mayarise. Be sure operators are alert and in proper physical and mental condition to perform their workassignments safely. No machine should be operated by a person who is drowsy, under the affectof medicines or drugs, suffers blackouts, or is suffering from any physical or mental distractionthat could contribute to unsafe operation.5
Maintain proper job conditions and working procedures. Check the job for possible hazards, bothabove and below ground level. Look for all possible sources of danger to the operator and othersin the area. Pay particular attention to conditionswhich may be hazardous or near the operatinglimits of the machine: e.g., side slopes, steep grades,potential overloads, etc. Examine the work site forrestricted traffic patterns, obstructed views, congestion, etc. Hazardous work conditions shouldbe corrected wherever possible and adequate warnings should be posted when applicable. Provide the correct machine to handle the job andequip it properly for the job to provide the necessary operator protection. Check for compliancewith all applicable governmental and local regulations. It is the machine owner’s or employer’slegal responsibility to see that his equipment complies with, and is operated in accordance with, allsuch requirements. Make sure the machine is properly maintained.A walk-around inspection should be performed atthe beginning of each shift before the machine isplaced in operation. If this inspection reveals anyproblems that could affect safety, the machinemust not be operated until these problems are corrected. Some examples include:– Loose, bent or missing grab irons, railings orsteps;– Worn, cut or missing seat belts (any seat beltover three (3) years old must be replaced regardless of condition);– Damaged windows in the operator’s compartment;– Worn, rubbing or abraded electrical insulationand hoses;– Any fluid leaks; and– Missing or damaged guards.It is the machine owner’s or employer’s responsibility to ensure the machine is properly maintained.Your Caterpillar Dealer will be glad to assist youin selecting and equipping the machine best suitedfor your job and in providing maintenance for yourmachines.II. Machine ModificationsModifications must not be made to the machinethat:– Interfere with operator visibility;– Interfere with ingress, egress from the machine;– Exceed the rated payload or gross combinationweight of the machine resulting in overloadingthe braking and/or steering system or the rollover protective structure (ROPS) capacity rating (shown on a plate affixed to the ROPS); or– Place objects in the cab that intrude into the operator’s space or that are not firmly fixed into place.6III. Operator-related Equipment OptionsEach job presents unique conditions that must betaken into account. Consider direct dangers to theoperator as well as all possible sources of distraction that could reduce operator efficiency and increasethe chances of costly and dangerous mistakes. Climatecontrolled, sound-suppressed cabs, and special exterior lighting are options available from Caterpillarthat can address requirements of special workingenvironments.“Flexible” machines include hydraulic excavators(track-type, wheel-type, and compact), skid-steerloaders, backhoe loaders and integrated tool-carriers. Work tools or any tool used in hazardous applications like demolition and logging, can create a needfor special operator guarding. When flying debrisfrom impact, cutting, shearing or sweeping attachments is present, additional protective devices suchas a front screen, Falling Object Guarding System(FOGS, includes top & front guarding), thick polycarbonate windshields or a combination of these isrecommended by Caterpillar. Contact your CaterpillarDealer for operator guarding options on your machine.IV. Machine ProtectionCheck the job for unusually demanding conditionsthat could cause premature failure or excessivewear of machine components. Additional protectivedevices such as heavy-duty radiator guards, crankcaseguards, engine enclosures, track roller guards and/orbrake shields may be needed. Also, consider the useof anti-vandalism devices, such as cap locks and instrument panel guards. Contact your Caterpillar dealerfor machine-protection and vandalism-preventionoptions for your machine.V. Fire PreventionRemember that most fluids on your machine areflammable!To minimize the risk of fire, Caterpillar recommends following these basic steps:– Remove trash (leaves, twigs, papers, etc.) thatmay accumulate in the engine compartment.– Do not operate a machine if leakage of flammable fluids is noticed. Repair leaks beforeresuming machine operation. Most fluids usedin Caterpillar machines should be consideredflammable.– Keep access doors to major machine compartments in working order to permit the use of firefighting equipment, should a fire occur.– Avoid attaching electrical wiring to hoses andtubes that contain flammable or combustiblefluids.
– Replace any rubbing, damaged, frayed, kinkedor leaking hydraulic hoses or fittings.– Follow safe fueling practices as described inCaterpillar Operation & Maintenance Manuals,EMI or CIMA Safety Manuals, and local regulations.As an additional safety measure, keep a 10-pound(4.5 kg) minimum fire extinguisher on the machinein a location as specified in the Operator and Maintenance Manual.VI. Safety RegulationsRegulations vary from country to country andoften within country. Your Caterpillar dealer canassist you in properly equipping your machine tomeet applicable requirements. Note: The generalsummaries given below are not substitutes forreading and being familiar with the appropriate local laws.(a) United States (US)With a few exceptions, all machine operations inthe United States are covered by federal and/or stateregulations. If the machine is used in mining activities, the regulations are administered by the MineSafety and Health Administration (MSHA). Otheractivities, including construction, are under regulations administered by the Occupational Safetyand Health Administration (OSHA). These agenciesrequire employers to provide a safe working environment for employees. Caterpillar has the sameobjective.OSHA and MSHA have adopted criteria for ROPS,Falling Object Protective Structures (FOPS), seatbelts, warning horns, back-up alarms, operator soundlevels, steering systems, and braking systems. Additional operator’s compartment protection may berequired for machines engaged in logging, demolition and other special applications.(b) European Union (EU)The EU Machinery Safety Directive applies toCaterpillar machines and most work tools. Itrequires that the “CE mark” be applied to the product and that a manufacturer’s declaration be provided. The “CE mark” indicates that safety issueshave been addressed by applying the appropriatesafety standards in the design and manufacture ofthe machine. The objective of the Safety Directive isto protect operators, spectators and maintenancepersonnel. Caterpillar fully supports this objective.VII. Sound SuppressionDifferent marketing areas have different noiseemission requirements. Noise regulations usuallyspecify limits for operators and spectators.(a) United StatesOSHA and MSHA noise-control regulations setpermissible noise-exposure limits for machine operators and employees. Operator protection frommachine noise can be achieved by use of factorybuilt cabs as offered in the Caterpillar Price List.These cabs, when properly maintained and operated with the doors and windows closed, reduce theoperator sound level for an eight-hour operatingperiod to meet the OSHA and MSHA noise-exposurelimits in effect at the date of manufacture. Variablesthat may be encountered on the job site, such asother nearby noise sources or noise-reflecting surfaces, may reduce the allowable work hours. If thisoccurs, ear protective devices may be required.(b) European UnionOperator sound-exposure requirements formachines in Europe are very similar to the OSHAand MSHA regulations mentioned above. In addition to operator sound-exposure requirements, certain types of Caterpillar machines are subject toEuropean Commission regulations for exterior soundlevels. Caterpillar ensures its products sold in theEU comply with the applicable noise regulations.VIII. Replacement Parts for yourCaterpillar Machine!WARNINGWhen replacement parts are required for this product,Caterpillar recommends using Caterpillar replacement parts orparts with equivalent specifications including, but not limitedto, physical dimensions, type, strength and material.Failure to heed this warning can lead to premature failures,product damage, personal injury or death.7
NomenclatureTHE CATERPILLAR PRODUCT LINETRACK-TYPE TRACTORS*Waste Handling Arrangements (WHA)Flywheel power 52 to 634 kW (70 to 850 hp)**available for sanitary landfill applications**Also available with hydrostatic power train.§ BrazilianDomestic OnlyD3C Series III**D3C XL Series III**D3C LGP Series III**D5C Series III**D5C XL Series III**D5C LGP Series III**D4C Series III**D4C XL Series III**D4C LGP Series III**D6M XLD6M LGPD6GD7R*D7R XRD7R LGPD5E§D5M XLD5M LGPD6R*D6R XLD6R XRD6R LGPD8R*D8R LGPD9R*D7GD10R*D11RAGRICULTURAL EQUIPMENT*Variable Horsepower arrangements available(SR) Super RuralD4E SR*D6G SR*Challenger 65EChallenger 75EChallenger 35Challenger 85E*Challenger 55Challenger 45Challenger 95ELEXION 460/465LEXION 480/485*All Wheel DriveMOTOR GRADERSFlywheel power 104 to 373 kW (140 to 500 hp)120H120H NA120H ES143H NA*8135H135H NA160H160H NA160H ES163H NA*12H12H NA12H ES14H140H140H NA140H ES16H24H
HYDRAULIC EXCAVATORSOperating Weight 6700 to 316 600 kg (14,770 to 698,000 lb)Track Models301.5307B307B SB320B320B L320B N320B LN320B S311B312B312B L322B322B L322B LN325B325B L325B LN375375 L350350 L315B315B L318B L318B LN330B330B L330B LN345B345B L – FIX345B L – VG52305130BWheel ModelsFront ShovelsOperating Weight 83 800 to 318 500 kg (184,600 to 702,000 lb)M315M31250805130BM3185230M320BACKHOE LOADERSDigging depth 4420 to 6528 mm (14'6" to 21'5")416C426C428C436C438CWHEEL SKIDDERSTRACK SKIDDERSFlywheel power 104 to 145 kW (140 to 195 hp)Flywheel power 89 to 112 kW (120 to 150 hp)515525528B517 Cable517 Grapple446B527 Cable527 GrapplePIPELAYERSLifting capacity 18 145 to 104 330 kg (40,000 to 230,000 lb)561M572R583R5899
*Available in auger scraper versionWHEEL TRACTOR-SCRAPERSStandard ModelsHeaped capacity 15.3 to 33.6 m3 (20 to 44 yd3)621F*631E Series II*651E*Tandem Powered ScrapersHeaped capacity 15.3 to 33.6 m3 (20 to 44 yd3)637E Series II*627F*657E*Elevating ScrapersHeaped capacity 8.4 to 26 m3 (11 to 34 yd3)613C Series II615C Series II623F633E Series IIPush-Pull ScrapersHeaped capacity 15.3 to 33.6 m3 (20 to 44 yd3)627F637E Series II657ECONSTRUCTION & MINING TRUCKS/TRACTORSConstruction & Mining TrucksCapacity 36.8 to 218 metric ton — 40.6 to 240 U.S. tons769D771D Quarry Truck773D775D Quarry Truck777D785C789C793CConstruction & Mining TractorsFlywheel power 699 to 962 kW (938 to 1290 hp)776D784CARTICULATED TRUCKSCapacity 22.7 to 36.3 metric tons (25 to 40 U.S. tons)10D25DD30DD250E Series IID300E Series IID350ED400E
WHEEL TRACTORSFlywheel power 164 to 597 kW (220 to 800 hp)814F824G834B844854GLANDFILL COMPACTORSSOIL COMPACTORSFlywheel power 164 to 353 kW (220 to 473 hp)Flywheel power 164 to 235 kW (220 to 315 hp)816F826G836815FWHEEL LOADERS825G* High lift arrangement available.Bucket Capacity (Heaped) 1.2 to 30 m3 (1.6 to 40 yd3)902906938G*950G980G*988F Series II*914G962G990 Series IITRACK LOADERS939C966F Series II*992G928G970F994***Wide track arrangements available.**General Purpose Bucket.Bucket Capacity (Heaped)** 1.0 to 3.6 m3 (1.3 to 4.2 yd3)933C*924F953C*INTEGRATED TOOLCARRIERS963B*973**General Purpose Bucket.Bucket Capacity (Heaped)* 1.3 to 3.1 m3 (1.7 to 4.0 yd3)IT14GIT24FIT28GIT38GIT62G11
TELESCOPIC HANDLERSTH62TH63TH82TH83TH103PAVING PRODUCTSCold PlanersCutting widths 1905 & 2100 mm (6'3" & 6'11")Flywheel Power 343 & 466 kW (460 & 625 hp)PM-465PM-565BReclaimer Mixers/Stabilizer MixersWindrow ElevatorsFlywheel power 250-321 kW (335-430 hp)Cutting width 2438 mm (8'0")Operating weight 5897 kg (13,000 lb)RR-250BSS-250BRM-350BBG-650Asphalt PaversPaving width 914 to 9754 mm (3 to 32 455CRoad WidenersLaydown width to 3048 mm (to 10'0")BG-73012
PAVING PRODUCTS (Continued)Smooth Drum Vibratory Soil CompactorsDrum width 1270 mm to 2130 mm (4'2" to 573CCS-583CCP-533CCP-563CPadded Drum Vibratory Soil CompactorsDrum width 1270 to 2130 mm (4'2" to 7'0")CP-323CCP-433CDual Drum Vibratory Asphalt CompactorsDrum width 1000 to 2130 mm (3'3.4" to 534CCB-634CCB-534CCB-544Pneumatic Tire Asphalt CompactorsWheel loads 1134 to 5000 kg (2500 to 11,020 ation Vibratory CompactorDrum Width 1700 mm (5'7")CB-535BCB-54513
UNDERGROUND MINING (ELPHINSTONE)Load-Haul-DumpBucket sizes 2.4-8.8 m3 (3-12 yd3)R1300R1600Articulated TrucksAD40 Series IIR1700 Series IIR2900Rigid Frame TrucksAE40 Series II40 t (44 T) capacity69D Dump69D Ejector73D38 t (42 T)36.2 t (40 T)52.2 t (58 T)ENGINESApplication configurationsinclude: On and off highwaytrucks, stationary and mobileindustrial, marine, electricalpower generation and petroleum. Spark-ignited (SI) available as noted. Generator setkW shown is 60 Hertz.1.1 L Family 104 to 224 kW (140 to 300 hp)Diesel Engine3200 Family 93 to 317 kW (125 to 425 hp)Diesel Engine 160 to 200 kW DieselGenerator Sets3500 Family 448 to 1641 kW (600 to 2200 hp)Diesel Engine 715 to 2000 kW DieselGenerator Sets 392 to 858 kW (525 to 1150 hp)SI Engine 360 to 800 kW SI Generator Sets143300 Family 64 to 265 kW (85 to 355 hp)Diesel Engine 65 to 250 kW Diesel Generator Sets 62 to 164 kW (83 to 220 hp)SI Engine 85 to 150 kW SI Generator Sets3600 Family 1560 to 5420 kW (2090 to 7270 hp)Diesel Engine 1375 to 4910 kW DieselGenerator Sets3400 Family 186 to 746 kW (250 to 1000 hp)Diesel Engine 210 to 800 kW DieselGenerator Sets 336 kW (450 hp) SI Engine 270 to 470 kW SI Generator Sets
TRACK-TYPE TRACTORSWASTE HANDLING TRACK-TYPE TRACTORSHydraulic ControlsBulldozersRippers & WinchesTowed ScrapersCONTENTSTRACK-TYPE TRACTORSRIPPERSFeatures . . . . . . . . . . . . . . . . . . . . . . . . . . . . . . .1-2Specifications . . . . . . . . . . . . . . . . . . . . . . . . . . .1-3Power shift drawbar pull vs.ground speed curves . . . . . . . . . . . . . . . . . . .1-13Power shift travel speeds . . . . . . . . . . . . . . . . .1-20Direct drive travel speeds anddrawbar pull . . . . . . . . . . . . . . . . . . . . . . . . .1-21Ground pressures . . . . . . . . . . . . . . . . . . . . . . .1-23Extreme slope operation . . . . . . . . . . . . . . . . . .1-24Features . . . . . . . . . . . . . . . . . . . . . . . . . . . . . .1-57Ripper Dimension DrawingsAdjustable Parallelogram Ripper . . . . . . . . .1-58Radial Ripper . . . . . . . . . . . . . . . . . . . . . . . .1-60Fixed Parallelogram Ripper . . . . . . . . . . . . .1-60SpecificationsTrack-Type Tractors . . . . . . . . . . . . . . . . . . .1-61Tip selection . . . . . . . . . . . . . . . . . . . . . . . . . . .1-67Estimating ripping production . . . . . . . . . . . . .1-68Seismic wave velocity charts . . . . . . . . . . . . . .1-69Estimating ripper production graphs . . . . . . .1-75WASTE HANDLING TRACK-TYPE TRACTORSFeatures . . . . . . . . . . . . . . . . . . . . . . . . . . . . . .1-25Specifications . . . . . . . . . . . . . . . . . . . . . . . . . .1-26Bulldozer specifications . . . . . . . . . . . . . . . . . .1-28WINCHESHYDRAULIC CONTROLSFeatures . . . . . . . . . . . . . . . . . . . . . . . . . . . . . .1-77Physical specifications . . . . . . . . . . . . . . . . . . .1-78Operating specifications . . . . . . . . . . . . . . . . . .1-81Features . . . . . . . . . . . . . . . . . . . . . . . . . . . . . .1-31Specifications . . . . . . . . . . . . . . . . . . . . . . . . . .1-32TOWED SCRAPERSBULLDOZERSEstimated production . . . . . . . . . . . . . . . . . . . .1-83Features . . . . . . . . . . . . . . . . . . . . . . . . . . . . . .1-35Summary of blade options . . . . . . . . . . . . . . . .1-36Blade selection . . . . . . . . . . . . . . . . . . . . . . . . .1-37General dimensions (Tractor and Blade) . . . . .1-40Blade specifications . . . . . . . . . . . . . . . . . . . . .1-41Estimating bulldozer production off-the-job . .1-49Job condition correction factors . . . . . . . . . . . .1-53Measuring bulldozer production on-the-job . . .1-54Special attachments . . . . . . . . . . . . . . . . . . . . .1-541-11
Track-Type TractorsFeaturesTRACK-TYPE TRACTORSFeatures: Cat Diesel Engines provide power, high torquerise, reliability and performance you can depend on. Hydraulic Electronic Unit Injection on D9Rand D10R increases fuel efficiency, reduces smoke,improves cold starting and enhances diagnosticcapabilities. Electronic Unit Injection (EUI) on D11R. TheElectronic Control Module (ECM) performs muchlike a mechanical governor, but has no movingparts. The ECM signals the injectors regulatingthe fuel supply thus controlling engine speed andpower. EUI provides: Reduced exhaust smoke,automatic altitude compensation and cold startprotection. Oil cooled steering clutches and brakes standard on all models except the D8R. Improves reliability and component life. Oil disc brakes onD5M XL and up. Oil cooled contracting band typeused on D3C Series III, D4C Series III and D5CSeries III power shift models. Finger Tip Controls (FTC) of transmission,steering clutches and brakes available on D5M,D6M, D6R, D7R, D10R and D11R. Differential steering allows infinitely variableturning radius. Standard on the D8R and optionalon the D6R, D7R and D9R, allows the tractor tomake a “power turn” keeping both tracks workingfor more traction and higher performance. Hydrostatic Power Train System available onD3C Series III thru D5C Series III allows fullpower turns, stepless speed range, smooth modulation, dynamic hydrostatic braking, superiormaneuverability and excellent controllability. Combined hand lever steering located left ofoperator provides easier operation on D5M XL,D6M XL and D9R. Combined pedal steering standard on the D3C Series III, D4C Series III and D5CSeries III. Optional combined hand lever clutchand brake for D3C Series III, D4C Series III andD5C Series III. Standard Tractors designed for heavy dozingand general grading.1-2 XL Tractors offer higher horsepower and longerroller frames for increased finish grading capability, flotation and productivity. Wider gaugeavailable on D6R XL through Caterpillar CustomProducts. Sealed and Lubricated Track reduces pin andbushing wear for lower undercarriage repair costs.Heavy duty track chain available on D5M, D6M,D6R and D7R improves wear life and reduces pin/bore stretching and cracking. Elevated sprockets on D5M XL and up eliminatefinal drive stress induced by roller frame movement and ground impact loads. Final drives pullchain only. Seals moved up out of dirt, sand andwater for longer life. Blade visibility improvedbecause operator sits higher. Resilient mounted bogie undercarriage onD8R, D9R, D10R and D11R reduces shock transmitted to tractor. Solid mounted undercarriage standard onD3C Series III through D7R and optional on theD8R provides stable platform for low impact, highabrasion applications like finish grading andstockpiling. Accessible modular design on D5M XL and upgreatly reduces drive train removal and installation time resulting in reduced repair costs. Tag link on D7R and up; L-shaped push arms onD6M through D6R. Both designs allow closermounting of dozer blades. This reduces total tractor length, improves maneuverability, balance,blade penetration and pryout.
SpecificationsTrack-Type Tractors1MODELFlywheel PowerOperating Weight*(Power Shift)Engine ModelRated Engine RPMNo. of CylindersBoreStrokeDisplacementTrack Rollers (Each Side)Width of Standard Track ShoeLength of Track on GroundGround Contact Area(W/Std. Shoe)Track GaugeGENERAL DIMENSIONS:Height (Stripped Top)**Height (To Top of ROPS)Overall Length (With P Blade)(Without Blade)Width (Over Trunnion)Width (W/O Trunnion —Std. Shoe)Ground ClearanceBlade Types and Widths:StraightAngleAngle StraightUniversalSemi-U“P” Straight“P” AngledFuel Tank Refill CapacityD3CSeries III52 kW70 hp7039 kg15,518 lb30462400694 mm3.7"120 mm4.7"5.0 L305 in35406 mm16"1899 mm6'2.8"D3C Series IIIHystat52 kW70 hp7112 kgD3C XLSeries III52 kW70 hp7231 kgD3C XL Series IIIHystat52 kW70 hp15,680 lb30462400694 mm3.7"120 mm4.7"5.0 L305 in35406 mm16"1899 mm6'2.8"15,941 lb30462400694 mm3.7"120 mm4.7"5.0 L305 in36406 mm16"2055 mm6'8.9"7304 kg16,103 lb30462400694 mm3.7"120 mm4.7"5.0 L305 in36406 mm16"2055 mm6'8.9"1.55 m21422 mm2390 in24'8"1.55 m21448 mm2390 in24'9"1.67 m21448 mm2586 in24'9"1.67 m21448 mm2586 in24'9"1.70 m2.66 m3.77 m2.93 m5'7"8'9"12'5"9'7"1.70 m2.73 m3.98 m2.96 m5'7"8'11"13'1"9'8"1.70 m2.66 m4.02 m2.98 m5'7"8'9"13'2"9'9"1.70 m2.73 m3.98 m2.96 m5'7"8'11"13'1"9'8"—1.83 m322 mm—6'0"12.7"1.85 m374 mm—————2.55 m2.31 m122 L—6'1"14.7"1.83 m374 mm—————8'4"7'6"32.2U.S. gal2.55 m2.31 m165 L—6'0"14.7"1.85 m374 mm—————8'4"7'6"43.6U.S. gal2.55 m2.31 m165 L6'1"14.7"—————8'4"7'6"43.6U.S. gal2.55 m2.31 m165 L8'4"7'6"43.6U.S. gal**Operating Weight includes ROPS canopy, operator, lubricants, coolant, full fuel tank, hydraulic controls and fluids, back-up alarm, seat belts, lights, rigid drawbar, frontpull device and standard service crankcase guard.**Height (stripped top) — without ROPS, exhaust, seat back or other easily removed encumbrances.1-3
Track-Type TractorsMODELFlywheel PowerOperating Weight*(Power Shift)Engine ModelRated Engine RPMNo. of CylindersBoreStrokeDisplacementTrack Rollers (Each Side)Width of Standard Track ShoeLength of Track on GroundGround Contact Area(W/Std. Shoe)Track GaugeGENERAL DIMENSIONS:Height (Stripped Top)**Height (To Top of ROPS)Overall Length (With P Blade)(Without Blade)Width (Over Trunnion)Width (W/O Trunnion —Std. Shoe)Ground ClearanceBlade Types and Widths:StraightAngleAngle StraightUniversalSemi-U“P” Straight“P” AngledFuel Tank Refill CapacitySpecificationsD3C LGPS
(track-type, wheel-type, and compact), skid-steer loaders, backhoe loaders and integrated tool-carri-ers. Work tools or any tool used in hazardous appli-cations like demolition and logging, can create a need for special operator guarding. When flying