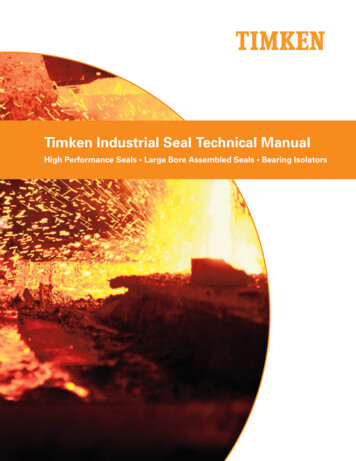
Transcription
Timken Industrial Seal Technical ManualHigh Performance Seals Large Bore Assembled Seals Bearing Isolators
IntroductionAt Timken, customers turn to us to for innovative solutions that solve their most criticalissues. When they do, they benefit from more than a century of knowledge in managingfriction and transmitting power for a variety of industries and applications. We’ve appliedthis technical know-how to offer OEMs, distributors and end users a complete line ofproducts and services – from bearings, maintenance tools and condition monitoringproducts to engineered surfaces, training programs, bearing and chock repair, and more.Now, from the people that brought you Timken industrial seals for small bore applicationscomes the latest addition to our seal family – a complete line of high-performance oil sealsand bearing isolators for large bore applications. Like all of our products and services, ourseals are backed by our leading technical support and a vast distribution network. Turn toTimken today for a full line of Timken industrial seals that help improve bearing, equipmentand bottom-line performance.WARNING: Proper maintenance and handling practices are critical. Failure to follow installation instructions and tomaintain proper lubrication can result in equipment failure, creating a risk of serious bodily harm. Never spin a bearing with compressed air. The rolling elements may be forcefully expelled creating a riskof serious bodily harm. This catalog is not intended to substitute for the specific recommendations of your equipment suppliers.Oil Seal SelectionSingle Lip Seal:All-purpose sealavailable in a widerange of sizes.Suitable for mostsealing applications.Dual Lip Seal:Used for difficultsealing problems orapplications involving the separationof two fluids orexclusion of foreignmaterials.Single Lip SplitSeal: Engineeredfor ease of installation on large shafts.Does not requirecostly teardown toreplace seal.Bonded Seal:Best choice forapplications withlower-end performance requirements.Economically priced.Special PurposeSeal: Designed foruse in high-speedapplications withspherical and taperedroller bearings.Bearing Isolator:Keeps bearingsprotected fromcontaminants inapplications wherelonger life and superior protection fromdebris are required.Protector Seal:Used in highly contaminated operatingenvironments toprotect bearings onboth rotating andstationary shafts.Uniquely designedusing microcellulartechnology.
Using This CatalogThe following pages contain the information that will allow you to make appropriate decisionsabout the seals best suited for your standard applications. Our technical manual includes: Organization by seal type, with specialsections for single lip, dual lip and specialpurpose seals. These three sectionsinclude critical information for easy andaccurate seal selection. General engineering information, includingnomenclature, technical specifications,tolerance charts and more. Installation instructions, with diagrams, andtroubleshooting tips for common problems.How to OrderTimken high-performance industrial seals and bearing isolators for large bore applicationsare available through our trusted network of authorized distributors. Timken works closelywith distributors to deliver unparalleled value and innovation to end users in a variety ofindustrial markets.When ordering oil seals for standard or special applications, please provide as muchinformation about the end user as possible, including: Customer nameand address Part name andnumbers shownon customer’sdrawing Intended use/application: Quantity Packagingrequirements Materialrequirements Functional testrequirements Suggested design Fixed dimensions RPMs/FPMs Shaft type Housing type Eccentricityrequirements Temperaturerequirements Medium tobe sealed Type of bearingTurn to Timken today for a full line of industrial seals that help improve bearing,equipment and bottom-line performance.Index for Technical ManualTechnology OverviewEngineering DataInstallation Instructions for Timken Oil SealsSeal & Material Selection Guides12711Oil Seal ConfigurationsOil Seal Product Information1213Bearing Isolator ConfigurationsBearing Isolator Products ppendixAppendixAppendixA – Product Identification by Model NumberB – Product Identification by Part Number Prefix NumberC – Compound Compatibility ChartD – Failure AnalysisE – Surface Speed ChartF – Application Data Sheets283137434748
Technology OverviewTechnology OverviewTimken Nitrile (N) Black Industrial SealsTaber Abrasion Resistance(ASTM D4060)Wear Index (mg/1000 loss)Oil SealsCreating the most advanced seals for heavy industrialmarkets requires quality materials. Timken industrialseals are manufactured using special elastomers thatare engineered for high-abrasion resistance, low wearand outstanding temperature and chemical resistance.In addition, we have materials and designs suited fora wide range of applications and our color-coded sealshelp you identify the seal to ensure you are using theright seal for the right application. Available in a varietyof sizes, our seals include:Taber Abrasion ResistanceThe elastomers used to make Timken oils seals weredeveloped with a special emphasis on abrasion resistance. In testing, our seals perform up to 90 percentbetter than seals made from traditional materials.60073% Enhancement4503001500Timken NNitrile (NBR)ElastomerTimken Hydrogenated Nitrile ButadieneRubber (HNBR) Blue Industrial SealsTaber Abrasion Resistance(ASTM D4060)Wear Index (mg/1000 loss)Turn to TimkenNo one knows bearings and how to protect them, betterthan Timken. Our complete line of high-performanceoil seals and bearing isolators are specifically engineeredfor long life and high performance in the toughestapplications. Turn to us for longer bearing life, increasedproductivity and reduced maintenance costs.12065% Enhancement9060300Timken ESHydrogenated Nitrile (HNBR)ElastomerTimken Fluoroelastomer (V) Green Industrial SealsTimken ES BluePeak Temp. 350 F (177 C)Timken V GreenPeak Temp. 450 F (232 C)TechnologyAs a technology leader in friction management solutions,we invest in our own research and development andpartner with trusted suppliers to develop the highestquality materials for all of our products. Our new lineof seals is no exception.Product quality – and resulting uptime and performance– depend heavily on material selection. Remember,all radial lip seals are contact seals. The elastomer ofthe seal contacts the rotating element of the equipment and, over time, all elastomers will wear away.The difference in how competing seals perform is inthe materials. Our oil seals are made with elastomersthat are designed to minimize wear, improve seal lifeand increase uptime.500Taber Abrasion Resistance(ASTM D4060)90% EnhancementWear Index (mg/1000 loss)Timken N BlackPeak Temp. 250 F (121 C)4003002001000Timken (V)Fluoroelastomer (FKM)ElastomerBearing IsolatorsTimken bearing isolators are an optimum choicewhen you require an extra layer of protection fromcontaminants in tough applications, such as pumps,motors, gearboxes and other rotating heavy equipment. Our metallic bearing isolators feature a camlock design and an engineered unitizing ring, providingenhanced protectionin a broad range ofenvironments. Madefrom PTFE material,our non-metallic bearingisolators also offersuperior protection.1
Engineering DataGeneral SpecificationsTimken industrial seals offer a leading combination ofquality, technology and high performance. However,there are additional considerations – such as shaftfinish, temperatures and other operating factors –that can impact the level of performance achieved.We recommend the following practices to ensure thatyou are maximizing the efficiency and the life of yourbearings and machinery. For specific application assistance, contact your Timken sales representative.Shaft FinishThe amount of contact between the shaft surfaceand the sealing element, and the condition of the shaftsurface, has a significant impact on how well sealsperform. Shafts containing “threads” or other textureare simply not able to be sealed effectively. Replacementoil seals always require new sealing surfaces.For best results and finishes we recommend using theplunge grind method. We recommend 10-20 µ in. Ra(0.25-0.50 µm) with no machine lead, scratches, dents,corrosion, pits or other surface defects.Shaft LeadSpiral grooves, or lead, may be generated on a shaftsurface by the relative axial movement of the finishingtool (lathe, belt, grinding wheel, etc.) during the finishing operation. Lead on a shaft can negatively affect aradial lip seal, allowing severe leakage and leading tosealing failure.Detecting LeadIt is nearly impossible to manufacture lead-free surfaces,but the thread method allows lead to be detected andquantified. To do so, use the following procedure:1. Mount shaft or sleeve in holding chuck.Unless otherwise indicated, it is recommended thatshaft finishes have a hardness of 30 to 40 RockwellC. A minimum of 45 Rockwell C can provide extraprotection from damage during handling or installation.See Table 1.2. Use 5 to 10 cps viscosity silicone oil to lightlycoat the shaft or sleeve.Table 1: Shaft Requirements4. Find a length of 100 percent extra strong quiltingthread (dia. of 0.009 in. or 0.23 mm) or unwaxeddental floss for next step.Seal TypeStandard Oil SealsPS-I Oil SealsBearing IsolatorsRequired Shaft Required Shaft FinishHardnessµin (microµm (microRockwell Cinches) Rameters) Ra30 - 4050 - 70Not Specified10 - 200.25 - 0.504-80.10 - 0.2064 maximum 1.63 maximum3. Because the most accurate results are achievedwhen the setup is level, check to ensure that theshaft or sleeve is level with the assembly.5. Use the thread to drape over the surface of the shaftand attach one ounce (28 g) weight at a distancebelow the shaft that will create a string-to-shaftcontact arc of 220 degrees to 240 degrees.Table 2: Determination of Lead (Source: RMA Handbook OS-1/1985)2Thread MovementDuring Clockwise(CW) RotationThread Movement DuringCounter-Clockwise(CCW) RotationFrom Fixed End Towards Free EndFrom Free End Towards Fixed EndNo MovementFrom Fixed End Towards Free EndFrom Free End Towards Fixed EndFrom Fixed End Towards Free EndNo MovementFrom Fixed End Towards Free EndFrom Free End Towards Fixed EndFrom Free End Towards Fixed EndFrom Fixed End Towards Free EndFrom Fixed End Towards Free EndFrom Free End Towards Fixed EndFrom Free End Towards Fixed EndAway From CenterToward CenterAway From CenterToward CenterLeadDefinitionClockwise Lead (Right-Hand) See Figure 1 and Figure 2Counter-Clockwise Lead (Left-Hand) See Figure 3 and Figure 4No Measurable LeadShaft may be tapered. Remount shaft end-for-end.If direction reverses, shaft is tapered.Shaft may be tapered. Remount shaft end-for-end.If direction reverses, shaft is tapered.Shaft may not be level. Remount shaft end-for-end.If direction does not reverse, shaft is not level.Shaft may not be level. Remount shaft end-for-end.If direction does not reverse, shaft is not level.Crowned ShaftCusped Shaft
Engineering DataEngineering Data6. Adjust machine’s rotational speed to 60 RPM.7. Measure the axial movement of the threadwhile the shaft or sleeve rotates for a periodof 30 seconds.8. Look for movement at both edges of the shaftby placing the thread there as well.9. Reverse the direction of the shaft or sleeverotation and repeat the test.10. Refer to Table 2 to determine results.Comparing Shaft Lead – Lead AngleThe lead of a shaft is compared with other shaftsof differing diameters by calculating the lead angle.This is found by dividing the string advance by theproduct of the shaft circumference (both in inches),and the number of revolutions required to advancethe string the measured amount.Figure 2: Clockwise LeadString AdvanceLEAD ANGLE (Shaft circumference) x (number of turns)For example, a string will advance 0.300 in. in 30seconds on a 4.000 in. shaft rotating at 60 RPM. Thelead angle equals 0.0456 degrees 0 degrees 2 minutes44 seconds. A 2 in. shaft with the same advance(0.300 in. in 30 seconds at 60 RPM) has a lead angle of0.0912 degrees 0 degrees 5 minutes 28.3 seconds.For best seal performance, industry standards recommendthat the lead angle of a shaft be 0 degrees /- 0.05degrees ( /- 0 degrees /- 3 minutes ).Figure 3: Counter-Clockwise LeadFigure 1: Clockwise LeadFigure 4: Counter-Clockwise Lead3
Engineering DataEngineering DataShaft-to-Bore MisalignmentShaft-to-bore misalignment is the distance by whicha shaft is off center relative to its bore. To measurethis, calculate the distance between the shaft centerline and the bore centerline, as shown in Figure 5.“X” Shaft-to-bore MisalignmentShaft“X”BorePressure DataTable 3 shows the maximum operating pressuresuitable for standard oil seals and Table 4 showsmaximum pressure limits for a variety of sealing options.If an application generates higher surge pressures thanwhat are listed, full details should be submitted fordesign consideration and engineering recommendations.Custom and high-pressure seals can be developed,although features such as ability to take greater eccentricities may be sacrificed to gain pressure capabilities.If possible, machine designs should include vents toallow the seal to operate more efficiently.Table 3: Operating Pressure Limits For Standard Oil SealsShaft SpeedShaftm/s (metersper second)0-10001001-20002001 & up0 0-5.15.2-10.210.3 & uppsi (poundskPaper sq.in) (kilopascals)barBoreFigure 5: Shaft-to-bore MisalignmentDynamic RunoutDynamic runout is the amount by which a shaft, atthe sealing surface, does not rotate around the truecenter. You can measure dynamic runout by holdinga dial indicator against the shaft surface while it isslowly rotated. The resulting measurement is calleda total indicator reading, or TIR. See Figure 6.“Y” Dynamic Runout“Y”ShaftMaximum* Pressure*f/m (feetper minute)Center of rotation of shaft7534835210.480.350.21* Split oil seals are not recommended for applications involving fluidpressure.Table 4: Maximum Pressure LimitsSealTypeStandard Oil SealsPS-I Oil SealsBearing IsolatorsMaximum Operating Pressure*psi (poundsper ent0.4810.34Ambient* Maximum operating pressure decreases as surface speedincreases. Please consult your Timken sales representative forspecific application operating pressures.† Retaining plate required at pressures greater than 75psi.BoreShaft and Bore TolerancesSeal performance depends on close tolerances inthe finished dimensions of the shaft, housing boreand oil seal. Tables 5, 6 and 7 give more informationon proper tolerance allocation.Figure 6 — Dynamic Runout4
Engineering DataEngineering DataTable 5: Shaft Diameter Tolerances for Oil SealsShaft DiameterRecommended ToleranceinchmminchmmUp thru 4.0004.001 - 6.0006.001-10.00010.001 & UpUp thru 101.60101.61-152.40152.41-254.00254.01 & Up 0.003 0.004 0.005 0.006 0.08 0.10 0.13 0.15The recommended bore diameter tolerances shownin Table 6 apply only to housings made from ferrousmaterials. For recommendations on seals made fromnon-ferrous materials, submit full details to yourTimken sales representative.Surface SpeedShaft finish, misalignment and runout, lubrication,pressure and seal design are all factors in determiningsafe operating speeds and become more importantthe more the shaft speed increases. To determine theappropriate surface speed for your application(s), usethe formulas below or see Appendix F for the surfacespeed chart. Because surface speed limits vary withseal design, also refer to the product listings for limitson specific Timken industrial seals.Bore depth standard tolerance is /- 0.016 in. (0.4 mm).Surface Speed (f/m) Shaft Dia. (in.) x RPM x 0.262Surface Speed (f/m) Shaft Dia. (mm) x RPM x 0.0103Surface Speed (m/s) Shaft Dia. (in.) x RPM x 0.0013299Surface Speed (m/s) Shaft Dia. (m/m) x RPM x 0.0000524Table 6: Housing Bore Tolerances for Oil SealsConversion FormulasHousing Bore Diameter(Nominal)Recommended BoreDiameter ToleranceinchmminchmmThru 1.0001.001 - 3.0003.001 - 4.0004.001 - 4.3754.376 - 6.0006.001 - 7.0007.001 - 8.0008.001 - 9.0009.001 - 10.00010.001 - 20.000Thru 25.4025.41 - 76.2076.21 - 101.60101.61 - 111.13111.14 - 152.40152.41 - 177.80177.81 - 203.20203.21 - 228.60228.61 - 254.00254.01 - 508.0020.001 - 30.000508.01 - 762.0030.001 - 40.000762.01 - 1016.0040.001 - 60.0001016.01 - 1524.00 0.001 0.001 0.0015 0.0015 0.0015 0.002 0.002 0.002 0.002 0.002-0.004 0.002-0.006 0.002-0.006 0.002-0.010 0.03 0.03 0.04 0.04 0.04 0.05 0.05 0.05 0.05 0.05-0.10 0.05-0.15 0.05-0.15 0.05-0.25Conversion FormulasMultiplyByTo ObtainInch (in.)millimeter (mm)barbarkilopascal (kPa)kilopascal (kPa)psi (lb/sq. in.)psi (lb/sq. eter (mm)Inch (in.)kilopascal (kPa)psi (lb/sq. in.)barpsi (lb/sq. in.)barkilopascal (kPa)Temperature Conversion Formulas F 1.8 ( C) 32 C ( F - 32)/1.8Recommended Bore Finish 100 microinches Ra (2.54 micrometers)or smoother.Table 7: Shaft and Bore Tolerances for Bearing IsolatorsShaft DiameterinchThru 6.0006.001 & UpRecommended TolerancemminchmmThru 152.40152.41 & Up 0.002 0.003 0.05 0.08Bore DiameterRecommended ToleranceinchmminchmmThru 6.0006.001 - 10.00010.001 & UpThru 152.40152.41 - 254.00254.01 & Up 0.001 0.002 0.003 0.03 0.05 0.085
Engineering DataOil Seals Installation InstructionsModel 145 Face Seal Dimensional DataCross-Section DimensionsDIM #Description1234567Height of cross-sectionShaft contact widthOverall free widthAssembled widthShaft DiameterMaximum face boreMinimum face diameterAssembled DimensionsModel 145A1IMPORTANT NOTERecommendations printed in this catalog pertaining to shaft finishes,misalignment, runout, speeds, temperatures and tolerances aregenerally applicable. The combination of a selected seal with a certainapplication, and the operating circumstances involved, could modifythe performance of the seal and/or the equipment. To get the mostout of your Timken seals, submit full information to ensure that theseal(s) you receive are suitable for your application.6Model 145A21.000 in. (25.4 mm)0.500 in. (12.7 mm)1.344 in. (34.1 mm)0.563 in. (14.3 mm)2.594 in. (65.9 mm)0.969 in. (24.6 mm)2.000 0.500 in. (50.8 12.77 mm) 0.781 0.156 in. (19.8 4.0mm)Application DependentApplication DependentShaft 1.000 in. (Shaft 25.4 mm) Shaft 0.391 in. (Shaft 9.9 mm)Shaft 1.000 in. (Shaft 114.3 mm) Shaft 1.750 in. (Shaft 44.5 mm)
Installation Instructions Oil SealsSeals Installation InstructionsEquipment Inspection and PreparationBefore installing any lip seal, equipment shouldbe thoroughly inspected. Follow the specificationsbelow for best results:Shaft Surface Finish [Roughness Averageor AA (Arithmetic Average)] With the exception of PS-1 (Model 61), all shaftsshould have a surface finish within 10-20 µin.(0.25-0.50 µm). For PS-1 (Model 61), the surface finish shouldbe within 4-8 µ in (0.10-0.20 µm). The surface finish direction of all seals mustbe perpendicular to the shaft axis of rotation.Bore Surface Finish, Ra ([Roughness Averageor AA (Arithmetic Average)] The surface finish of all bores must be 100 µin.(2.54 µm). The surface finish direction of all bores must beperpendicular to the shaft axis of rotation.B Minimum30 MaximumAShaftDia.Corners MUSTbe burr freeFigure 7: Shaft GeometryTable 8: Edge Relief for ShaftsA - Shaft DiameterB - Minimum*inchmminchmmThru 0.3940.395 - 0.7870.788 - 1.1811.182 - 1.5751.576 - 1.9691.970 - 2.7562.757 - 3.7403.576 - 5.1185.970 - 9.4499.450 & UpThru 10.0010.01 - 20.0020.01 - 30.0030.01 - 40.0040.01 - 50.0050.01 - 70.0070.01 - 95.0095.01 - 130.00130.01 - 240.00240.01 & 200.751.001.251.501.752.002.252.753.505.50* If a shaft lead-in radius is used, maintain the diametral differenceto no less than indicated valueShaft Surface Hardness, Rockwell C-Scale With the exception of PS-1 (Model 61), all shaftsshould have a surface hardness between30-40 Rockwell C.BoreDepth15 Min.25 Max. For PS-1 (Model 61), the surface hardnessmust be within 50-70 Rockwell C.CornerRadiusAdditional SpecificationsChamferLength Both the shaft and bore should include anedge relief (preferably an edge chamfer), asshown in Figures 7 and 8. See Tables 8 and 9for specific values. Both the shaft and bore should be clear of anydefects, such as spiral-machining marks, burrs,sharp edges, nicks, scratches and corrosion.Figure 8: Housing Bore DimensionsTable 9: Edge Relief for Housing BoresNominal SealWidthChamferLengthMax. HousingCorner RadiusinchmminchmminchmmThru 0.394Over 0.394Thru 10.00Over 00.757
Installation Instructions Seals Typically, the shaft has a wear groove createdfrom previous seals. Make sure the new sealinglip does not seal in the same location. When drive features such as keyways or splinesare present, they must be covered using aninstallation tool similar to the one shown inFigure 10 below, and using “Installation MethodD” shown in Figure 10 on the next page. If theuse of a tool is prohibited by the size of the shaft,use one of the following options:Installation MethodsInstallation Method AThru Bore:Installation tool bottomson machined faceInstallation Method BThru Bore:Seal bottoms onmachined bore shoulderInstallation Method CThru Bore:Installation tool bottomson shaftInstallation Method DThru Bore:Mounting thimble assistsin compressing seal lip foreasier installation Polyethylene tape Brass shim stock with smooth edges Wooden plug with smooth edgesSeal InspectionSeal Outside DiameterSpringFigure 10: Installation MethodsSealing LipFigure 9: Seal Cross Section Inspect the sealing lip for any signs ofdamage, such as cuts, indentations and nicks. Make sure that the spring (finger or gartertype) is retained within the seal (bonded orassembled). Inspect the seal OD, looking for any signsof damage, such as cuts (in rubber seals),indentations and nicks.Solid Seal InstallationInstall the seal(s) using one of the proper installationmethods shown in Figure 10. When using installationtooling, the diameter, or contact area, should not bemore than 0.010 in. (0.254 mm) smaller than the borediameter. If the use of an installation tool is prohibitedby the size of the seal, then: Rest a block of wood (piece of 2 in. x 4 in. orsimilar) on the seal and use a mallet to drive theseal into position. Do not hit the seal directly withthe mallet, as it may cause damage. When using this method,follow a star pattern (asshown in Figure 11) toavoid “cocking” of the seal. Place the ends of thewooden block at positions1 and 2 (as shown inFigure 11).15843672Figure 11: Star Pattern Hit the center of the board with the mallet.8
Seals Installation Instructions Continue by rotating the wooden block to theappropriate positions (3 and 4, 5 and 6, 7 and 8),hitting the center of the block with the malleteach time.IMPORTANT NOTEThe 0.015 in. protrusion will be built into the width of the seal. Thedepth of the bore housing should be machined to the seal widthspecified on the package. Repeat the pattern until the seal is properly seatedin the housing bore. The seal is fully seated whenthe difference between the seal surface and thehousing surface is equal to or less than 0.010 in.(0.254 mm).Split Seal InstallationAmbient pressure/non-flooded applications only Apply a thin coat of lubricant to the seal lip andshaft. Split the seal along the axis of rotation (shownin Figure 12) and place the seal around the shaft.Figure 12: Split Seal Separation Beginning with the split ends, insert the seal intothe top of the housing bore. Make sure the splitends of the seal are touching. Working downwards on both sides, continueinserting the seal into the housing bore, finishingat the bottom. Once the seal is properly seated in the housingbore, it should protrude from the housing surfaceby 0.015 in. (0.381 mm), as shown in Figure 13.The 0.015 in. protrusion is built into the width ofthe seal. The depth of the bore housing shouldbe machined to the seal width specified on thepackaging.Figure 13: Split Seal InstalledInspectionAfter installation, inspect the sealing areas for leaks,paying special attention to the area around the sealinglip and the OD. Make sure that the sealing lip is not inthe groove worn into the shaft from the previous seal.ShaftDiameterNo. ofBolts“A” MinimumPlate Thickness3 in. - 8 in.(76.2 - 203.2 mm)61/8 in. (3.18 mm)Bolts on a max. of 6 in. (152.4mm) chord, spacing centeredabout split in end plate1/4 in. (6.35 mm)Over 8 in.RECESS DEPTH(? SPACE)SPLIT RETAINERPLATE"A"BOLT? INCH(? MM) ETER“B” 0.28 “X” Minimum, 0.5 “X” Maximum“X” Bore Dia. - Shaft Dia.2*Figures shown are for a guideonly. Good machine designpractices should be followed.Figure 14: Standard Oil Seal Installation9
Timken Bearing Isolators Installation InstructionsEquipment PreparationBefore installing an isolator, all equipment should beinspected. First, disconnect all power to the machineryand follow standard safety procedures to avoid personalinjury or equipment damage during installation.Second, inspect the shaft and bore surfaces. Theshaft finish should be better than 64 µin (1.63 µm)with minimal lead, but a polished surface is notrequired. The bore surface should be 64 µin (1.63 µm).Both the shaft and bore should have a chamfer orother edge relief to prevent the o-ring from shearing.Third, check the shaft and bore for damage orimperfections. They should both be clear of burrs,nicks, indentations and any other defects. Clean allforeign debris from the area. Note that, in manycases, the previous seal may have worn a grooveinto the shaft. Make sure that the rotor o-ring of thenew seal does not ride in this area.Finally, if drive features such as keyways or splinesare present on the shaft, they must be covered duringinstallation. To do so, use an installation tool, polyethylenetape, brass shim stock with smooth edges or a woodenplug with smooth edges.Installation Instructions IsolatorsIf your isolator has a drain port, rotate it to the 6 o’clockposition. For isolators with a mark on the OD of thestator, rotate it to the 12 o’clock position to ensureappropriate positioning of the drain port. Some nonmetallic bearing isolators may be installed in any direction, and there is no need to position the seal. SeeFigure 15 for clarification, or contact your Timken salesrepresentative if you require additional information.Drain at 6:00 position,Mark at 12:00 position.Figure 15: Drain Port PositioningUsing your hands only (no installation tool required),push the isolator gently into the bore. If required, gentlytap the isolator using a soft-faced mallet. While flangedisolators are fully seated when the flange is flushagainst the housing, flangeless isolators can be installedat the bottom of the housing and are fully seatedwhen they are flush with the bore face. See Figure 16for clarification.Seal PreparationIMPORTANT NOTETimken metallic and non-metallic bearing isolators are unitized,and any attempts to take them apart will not only cause sealdamage, but will void the warranty on the product.Before installation, inspect the o-ring’s OD and ID,making sure they are free of any defects. Use thelubricant included with your isolator to lightly greaseall the o-rings.InstallationUsing your hands only (no installation tool required)push the isolator evenly onto the shaft as shown inFigure 14.Figure 14: Seal Installation on Shaft10Figure 16: Flanged Seal Flush with Housing FacePost-InstallationInspectionAfter installation, inspect the sealing area fordamage. Gently spin the shaft to make sure therotor is working properly.IMPORTANT NOTEDo not flood the isolator or block the expulsion ports, as theseactions can cause seal damage and failure.RemovalTo remove an old isolator from your equipment, startfrom the back side of the seal and perform installationinstructions in reverse. If access to the back side ofthe isolator is difficult, pry it from the housing a littleat a time. Be careful not to damage the shaft orhousing bore during seal removal.
Seal & Material Selection GuideSeal & Material ntof FrictionTimken ESDark Blue881.053Timken VGreen761.158SiliconeLight Blue82Over2.0000.100(FDA - Red)BlackN/AXX XN/A N/AN/A N/ASpeed (FPM)XMax RadialMisalignment XXXXXXXXXXXXXXXXXN/AN/AX XMaxPressureXXXN/AN/AXXXXXN/AN/AXMediaLevelXSeal Material*** Values shown are generally applicable limits. For specific application help, contact yourTimken sales representative.** Seal materials shown are typical for oil seals. Other materials are available upon request.Contact your Timken sales representative for more information.# Models 145 and 143 face seals are notavailable in Timken N, but are suppliedwith standard nitrile material.-40 F to 200 F(-40 C to 93 C)-40 F to 300 F(-40 C to 150 C)-22 F to 400 F(-30 C to 204 C)-75 F to 350 F(-59 C to 176 C)-120 F to 400 F(-84 C to 204 nceColor80XXXN/AN/AUnder0.005Max SpikeTemperatureType ofMotionShaft EStainless SteelXXXBlackGylon XXXXN/AN/AMaterial Selection Guide*Material Type#Timken XXXTimken VXXXXXXXXXXTimken ESXXXTimken NXXX100%XXXXX50%XXXXXX25%XX150 psiXXXXXXXX7 -5000RotaryXX0-1000Over 12 inchesXXReciprocating6-12 inchesXXXOperatingTemperatureParameter3-6 inchesSeal TypeModel 57Model 58Model 63Model 53Model 23Model 26(solid)Model 26(split)Model 59Model 87Model 64Model 145#Model 143#P/S (Model
Oil Seal Selection Single Lip Seal: All-purpose seal available in a wide range of sizes. Suitable for most sealing applications. Dual Lip Seal: Used for difficult sealing problems or applications involv-ing the separation of two fluids or exclusion of foreign materials. Single Lip Split Seal: