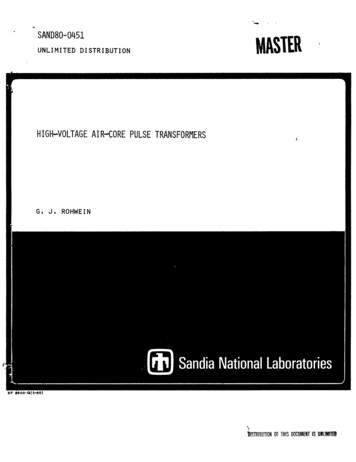
Transcription
SAND80-0451MASTERUNLIMITED DISTRIBUTIONHIGH-VOLTAGE AIR-CORE PULSE TRANSFORMERSG. J. ROHWEINH i ] Sandia National LaboratoriesSF 2«00-a(3-80)iSTRIBOTiON OF THIS DOCyMEHT IS UM.IH1TH)
Issued by Sandia National Laboratories,operated for the United States Departmentof Energy by Sandia Corporation.NOTICEThis report was prepared as an account of work sponsored bythe United States Government. Neither the United States northe Department of Energy, nor any of their employees, norany of their contractors, subcontractors, or their employees,makes any warranty, express or implied, or assumes any legalliability or responsibility for the accuracy, completeness orusefulness of any information, apparatus, product or processdisclosed, or represents a t its use would not infringeprivately owned rights.
DISCLAIMERThis report was prepared as an account of work sponsored by anagency of the United States Government. Neither the United StatesGovernment nor any agency Thereof, nor any of their employees,makes any warranty, express or implied, or assumes any legalliability or responsibility for the accuracy, completeness, orusefulness of any information, apparatus, product, or processdisclosed, or represents that its use would not infringe privatelyowned rights. Reference herein to any specific commercial product,process, or service by trade name, trademark, manufacturer, orotherwise does not necessarily constitute or imply its endorsement,recommendation, or favoring by the United States Government or anyagency thereof. The views and opinions of authors expressed hereindo not necessarily state or reflect those of the United StatesGovernment or any agency thereof.
DISCLAIMERPortions of this document may be illegible inelectronic image products. Images are producedfrom the best available original document.
DISCLAIMER .wd,n„,y „,e55lompletehessor„ ' ' J " " ' " ' " "»f J"V ig ncv thereof TO a n , of ,he,, employees m a k e s -„,efulr,es, o l " n r " , T „ ' , ' " , ''"''""""'"'" '"""'I"'" "I t e accuracyrepresehfs thai ,t, „,e would hol rrfrmeeTl* " " " ''" ''"'""" ' '''"' "''»'commercial produr, p r o o ir, ,1" """ " "" " ' " " " "" "» ' " ' " «H 'no, .ecessarly o o s f i r, " : , ' " ' " * " " ""' '"'""or ofherwise d o „Srates G o v e r l L m"" "*csemcn, recommendation or fayormg by ,he Unitedt.»ce e ;y state,r„r'ref;ea;roT,h' n 'tJ'," "r:Goyeroment'"' ' " ' "or' any ' "ajency " ' -thereof" ' - » - ' " * "or reflect those of the UnitedStates'HIGHrVOLTAGE AIR-CORE PULSE TRANSFOIMERS"G. J. RohweinSandia National Laboratories, Albuquerque, NM87185IntroductionAir core transformers basically consist of two or more inductively coupledcoils cind, in principle, function the same as magnetic core transformers. Theydiffer fron iron or ferrite core transformers in that no ferromagnetic corematerials are used to channel the magnetic flux throu the windings to assureflux linkage. With air core transformers, flux linkage is strongly dependent uponthe physical proximity of all turns of one winding with respect to all turns ofthe other winding.Consequently, the mutual coupling of air core windings tendsto be lover than magnetic core trans formers, peirticularly with high gain transformers v*iich have thick windings. However, since air core transformers do nothave magnetic cores, they are not limited in current handling capacity, by saturation of the magnetic materials or frequency limited by the cottposition of thecore. Not having core saturation and frequency limits are twD of the most significant advantages of air core pulse transformers. They are limited in power andenergy handling capacity prinrarily by the resistance of the windings and themechanical strength of the composite materials cind structure frctn v*iich they aremade.They are, therefore, best suited for use with large, high current energysources such as parcillel capacitor banks v*iich often generate peak power levelsover 10-'--'- watts or to lower energy fast pulse applications involving voltagestep up in the nanosecond time regime.In the high energy category air core pulsetransformers systons are well adapted to charging pulse forming lines (PFL) up totheraulti-raegavoltrange.In the low energy fast pulse category, air core*This work was supported by the U.S. Department of Energy, under ContractDE-AC04-76-DP00789.hCytJ
transformers have proven useful in spark gap triggering applications vAxere thepulse rises to several hundred kV is 10 ns or less.Fast pulse transformers nayalso be used to direct drive higher itipedance electron guns.Other devices could be included in a discussion of air core pulse transformers. This paper will cover only the general types designed for high voltagepulse generation and energy transfer applications.Special enipSiasis will be givento pulse charging systans v*iich operate up to the multi-megavolt range.DiscussioiThere are two basic types of high voltage air core pulse transformers v*iichcan be operated in theraegavoltrange. The first and most ccmraon is the singlelayer helical wound transformer (Figure 1).(Figure 2).The second is the spiral strip typeThese transformers differ from eacJi other primarily in the configura-tion of the secondary windings v\*iich, as will later be shown, accounts for a significant difference in their resistance to insulation failure frctn fast pulses. Theprimary windings for either type, whether single or multiple turn, nay be designedin a variety of ways without affecting electrical breakdown ciharacteristics of thetransformers. For reasons of high voltage isolation, the low voltage primarywinding is typically placed outside the secondary in either type transformer sothat the high voltage output of the secondary nay be led out through the center ofthe assatibly.With helical transformers high voltage stzmdoff between the parinary andsecondary windings is provided by an insulated space between the windings. Thespace nay be uniform or tapered in the longitudinal direction. When tapered, theinsulation thickness (usually oil) increases with the voltage along the length ofthe coils. With spiral strip transfomers voltage standoff is largely a functicaiof the radial thickness of the secondary winding since the turns directly overlayeach other. The winding stack therefore has a pure radial voltage gradient between2
the high voltage inner turns and the low voltage outer turns. Like helical typetransformers, the open volume in spiral strip transformers is usually insulatedwith oil. However, because of the high winding density, spiral strip windingsmust ordinarily be vacuum impregnated to displace air from the secondary winding.Two problems are cotnmon to both types of transformers. These are electricalbreakdown turn to turn or between windings and peurtial shorting from eddy currentsinduced in voltage grading devices and structural carponents v hich are necessarilypresent in high voltage transformers. Tum-to-tum breakdown is canraon withhelical transformers v« en used in charging systems for pulse forming lines (PFL).This problem arises from fast rising voltage transients (usually less than 10 ns)generated by the discharge of the PFL v iich are fed into the output of a directccxipled transformer. The turns of a helical winding are inductively and transittime isolated from each other and the capacitance conponents between turns andfrom each turn to ground (Figure 3) are not sufficient to grade fast risingtransients.Consequently, a voltage pulse approaching the full anplitude of thetransient canracmentarilyappear across the final turns of the secondary and causebreakdown. This problem was corrected in the FRIZZtransformer design by addinga capacitive voltage grading dish across the output turns of the trainsformer asshown in Figure 4.Spiral strip trsuisformersare inherently less prone to break-down from fast voltage transients because the intertum capacitance components areall directly in series to ground as shown in Figure 5. These capacitance canponents are ccnparatively leurge because of the large surface area and close spacingbetween turns of the spiral strip. Consequently, a fast voltage pulse is capacitively graded throu the thickness of the winding.The principal weakness ofsimple spiral strip windings, however, is their tendency to break down from thethin edges of the strip.An circ breakdown typically originates from the edge ofone of the final turns, flashes across the insulation margin and closes with the3
lew voltage primary. Such breakdowns usually damage the insulating film in themargin and leave a heavy carbon path throu the oil.These edge breakdowns result from highly enhanced electric fields associatedwith equipotentials which onerge from between the high voltage turns and bendsharply around the edges toward the low voltage turns (Figure 6).The high fieldscan be reduced and edge breakdown eliminated by placing a coaxial shield acrossthe margins to shape the equipotentials into a coaxial distribution v\hich is nectrlypcirallel to the imiform field through the thickness of the winding. Figure 7.Adding the voltage grading structures to either type of transformer can leadto the second major difficulty with air core transformers which is eddy currentshorting of the transformer by the grading structures. Although these structuresmay be slotted, eddy currents can be induced in cylindrical shields as illustratedin Figure 8.Eddy current shorting decreases the gain and energy transfer effi-ciency of the transformer by an amount rou ly proportional to the magnitude ofthe currents. In one instcince, cylindrical shielding reduced the gain of a spiralstrip transformer by 58% ccnpared to an equiveilent unshielded transformer.The problem of electrostatic shielding and grading structure design musttherefore be concerned with making these devices transparent to magnetic fields.One grading technique that has been atployed successfully with transformers usedin single shot service consists of filling the open volume of the transformer witha resistive liquid such as water or a solution of water and copper sulfate. 'In these cases, voltages are resistively graded but the resistivity of the solutionis high enough to prevent large eddy currents. Resistive solution grading isadequate for single shot transformers but less satisfactory for repetitive pulseapplications because of resistive losses in the grading solution.The most successful method developed for grading spiral strip transformer isconcentric ring cage shielding across the margins4as shown in Figure 9.Magnetic
fields diffuse freely through the ring cage without inducing edcfy currents in theelements and yet maintain the proper electric field distribution in the margins.Each ring, of course, must have at least one circumferential gap to preventcurrent from flowing in the hoop direction of the rings. Spiral strip transformersshielded in this manner have been operated successfully in PFL charging applications to 3 MV with over 90% energy transfer efficiency from the primary toc qsecondary capacitor. 'Figure 10 is a diagram of a ring shielded transformerv c h operates with high efficiency in theraultimegavoltrange.At lower voltages, in the few hundred kilovolt range, ring shielding is oftennot necessary. Adequate electric field shaping along the edges of the high voltagewinding Ccin be provided by the primary turn and center coil form if they are madewider than the secondary winding strip. The maximum distance that the primary andcoil form should extend beyond the winding strip edges should be limited to anamount equal to the secondary winding thickness. Otherwise, eddy currents in theedges of the wider elements will begin to cause measurable degradation of transformer performance. This method of winding edge grading is illustrated inFigure 11 vhich is a diagram of a small 200 kV fast pulse trigger transformer.Transformer Circuit AnalysisFor transformers with perfect coupling, no winding resistance and negligibleintertum capacitance (Figure 12), a simple set of relations may be derived vhichrelate the primary and secondary current (I , Ig) and voltage (Vp, Vg) to theprimary and secondary turns (N , Ng) of the transformer:Ip Np Ig t Vp Np V N SS(1)(2)The primary and secondary impedances (Zp, Zg) are:5
V (3)Vc(4)from which%{-—V-(5)From these ideal relations it can be seen that a transformer can be used tochange current, voltage or inpedance. However, since no transformer is perfectand often both the primary and secondary sections of the circuit have resonantcharacteristics, the analysis of such circuits is somev\*iat more conplex.An analysis of various pulse transformer circuits by W. H. Boetick may befound in Glasoe and Lebaaqz. HCwever, the pulse charging circuit is of particularinterest to a discussion of air core transformers since they are often used inconjunction with low voltage capacitor banks to charge high voltage pulse formingtransmission lines. A basic transformer charging circuit is shewn in Figure 13.Neglecting stray parameters such as winding resistance, capacitance and eddy currentlosses, the voltage loop equations are,1tdl,dijC - / Il'3t h l t - - M d t - (4)1o.tdl* 1 / i2 dt L2-ar-M5r o2 ov ereLi (Lg Lp)I (IQ 1 )The equations have been solved for the general case' v iere the primary andsecondary frequences may not be matched and the coupling coefficient (K) is lessthan one.6(s)
KO)2, 2.1/2( )[Cos Sjt - Cos S, t]1V2(t)lOOj 2 - 2 (1 - 2K ) o(6) Ui ' l' v\hereCO 3 2 0 22 yJ(X) (ji Si2, S 2 12 - 2(1 - 2 K 2 ) iji Oi ' ,2,2 (1 - K )Pulse charging circuits may be operated in matched or off resonance modes, but aregenerally matched as nearly as possible to maximize energy transfer efficiency.In the matched frequency mode—that is, with the open circuit frequencies ofprimary and secondary sections of the circuit equal (LQ C-L L2* 2 ' * casesare of practical interest:1) first swing charging where maximum secondary voltageis reached on the first excursion (Figure 14a), and 2) dual resonance cihargingv ere maximum voltage occurs on the secoi or reverse voltage excursion of thesecondary (Figure 14b).The secondary voltage (V2) as a function of time for amatched frequency circuit with damping is given by: oV2 (t) 1i2 -t/T ctJtCos—— 1\ cotCos-(7)Vl K' .where4Lj L2'12T "S"7— p T.2,(1 - K' ) damping time constantVl " 1 2V Q Charge voltage on primary capacitorL] is the inductance of the transformer primary cirucitLj is the inductance of the transformer secondary circuitCO is the radian frequency of primary and secondary circuitsNn?2M is the mutual inductance.7
with Eq. 7 it can be shown that the second or reverse voltage peak exceeds the7first for all values of K 0.8.This implies that energy trauisfer efficiencydecreases for first-swing charging as the coupling coefficient decreases but tendsto increase with IcMer coupling at the second peak.Transfer efficiency at thesecond peak increases to a theoretical maximum of 100% hen K 0.6 which is themost cortnon coupling condition for the so called dual resonance charge cycle.This and other discrete coupling coefficients which satisfy requiratvents for 100%qenergy transfer are given by:. 2n - 1K —22n,,(5)- 2n 1for n 1, 2, 3, 4, . . .K 1, 0.6, 0.385, 0.28, . . .The case of K exactly equal to one is, of course, inpossible but for Kapproaching one, the secondary voltage maximum is reached on the first voltageexcursion. With air core transformers having a gain of ten or more, this operatingcondition is unrealistic because of the practical difficulty of constructing highvoltage transformers with coupling coefficients greater than about 0.85 to 0.9.Within the range 0.6 to 0.85 it is possible to produce a wide variety of transformer designs. For this reason dued. resonance trcinsformers having the lowercoupling coefficients of 0.385, 0.28 vSiich reach naxiraum voltage on the third orfourth voltage excursions are of little practical interest.In a dual resonance txcinsformer circuit operating with K 0.6, it is desirable to use a transformer vAiich by itself has a coupling coefficient greater than0.6. This permits exact resonant matching with the primary and secondary capaci-tors by adding small tuning inductors to both sections of the circuit (Figure 15).The values for primary and secondary tuning inductances (L 2 and L 2) may befound if the primary and secondary capacitances (C, and C2) and the inductances8
(Lp, Lg and M) of the transformer are known. From the relation for couplingcoefficient set K 0.6.MK \/ 1 20.6(10)The values of total primary and secondary circuit inductance, L- and L2, become,H I (o!'6)'(11)2L2 C (0T6) (12)Since h- C- 1 2 '"2' substition gives,M 1 - 0.6 2C 1(13) 2 .157(14)andMand the tuning inductances areL l Lj - (Lp Lj-,)where I is inductance of the primary capacitor bank.From the foregoing it can be seen that any transformer with a coupling coefficient greater than 0.6 can be adapted to a dual resonance circuit. As previouslyindicated, unless the circuit coupling is close to 1.0, it is more advantageousfrom the standpoint of transfer efficiency to operate in the dual resonance modewith K 0.6. With repetitive pulse systans, high transfer efficiency is essentialto preventing excessive energy dissipation in the system corponents from residualenergy ringing through the system after discharge of the scondary capacitor. Whenproperly tuned, a dual resonance charging systan will operate with cin overallefficiency between 90 and 95%.5'99
Transformer InsulaticaiProper application of insulating materials is an essential consideration inhigh voltage transformers design. As a minimum, it is necessary to know thedielectric strength of the materials and the voltage stresses that they will besubjected to in service. In reality, these tvro aspects eure a ccirplex of manyfactors, the details of v\*iich aure beyond the scope of this paper.It is useful,however, to summarize some of the general characteristics and modes of failure ofdielectric materials.For pulse transformers, the types of materials most cciimonly used are liquidsand film or cast solids, usually in combination.Failure in one invariably leadsto failure of both. The initiating mechanism can be pronpt in nature such as bulkbreakdcvm from over stressing or gradual as a result of deterioration of dielectricstrength from partial discharges. The process of dielectric deterioration frompartial discharges includes gas production in the liquid vhich leads to ionizationin the gaseous inclusions and erosion of solids in contact with the liquids.Three characteristics common to liquid and solid dielectrics used in pulsedvoltage applications include time dependent breakdown in the approximate rangegof 10Qto 10s, breakdown strength vhich decreases with a weak dependenceon increased stressed area in the range of a few square centimeters to severalthousand squeire centimeters and breakdown strength v*iich decreases with increasinginsulator thickness below 1 cm. Data also exists that shows the dielectricstrength of liquids such as transformer oil and n-Hexane decrease by a factorof three with increases in pulse voltage rate of rise in the range of 10 to10 kV/cm-jUs.lFigures 16 and 17 illustrate pulse time and electrode gapdependence on breakdown for several oils.Figure 18 is a plot of dielectricstrength as a function of thickness for Mylar polyester film. Although the trendsfor liquids and solids are similcur, the actual strength levels for given pulse10
times and thicknesses nay be very much different. With few exceptions, liquiddielectrics tend to be weaker than solids, particularly solid films.Various theoretical models have been developed to explain dielectric breakdownphenomena.Some authors consider licjuids and solids to be homogeneous dielectricsvhile others ascribe breakdown to the presence of various inpurities or faults inthe media. For practical purposes, any theory v*iich considers liquids or solidstotally homogenous can have only limited application. However, the effects ofinpurities and faults are inclined to neglect the fact that eventually it is theinsulator itself vAiich breaks dcwn.l Thus there is no single theory vhich isgenerally accepted for all cases.A model for time dependent breakdown of solids by Kuffel and Abdulleihl isillustrated in Figure 19. Breakdown strength vihich decreases as a function oftime is described as resulting from four different initiating mechanisms whichoperate in different time regimes. The highest strength a material can have, itsintrinsic strength, can only be obtained experimentally under the best of coiditions v\*ien all extraneous effects are removed so that breakdown is dependent ononly the material and temperature.—8Intrinsic breakdown occurs in times of 10 sor less at stress levels in excess of 10 V/cm.Intrinsic breakdown is postulatedto be electronic in nature and assumed to occur vhen dielectric electrons gainenough energy from the applied field to cross the forbidden energy gap from thevalency to the conduction band.The criterion condition is formulated by solvingan equation for energy balance between the gain of energy by conduction electronsfrom the applied field and their loss to the lattice.The second and next lower initiating mechanism is streamer breakdown v ich,with electrodes enibedded in the material to avoid external effects, occurs from anelectron entering the conduction band of the insulator at the cathode. As it driftstoward the anode under the influence of the electric field, the electrons gain energyII
between collisions and lose it on collisions. On occasions vhen the path is longenough to exceed the lattice ionizing energy an additional electron is produced bycollision. The process may lead to the formation of an electron avalanche v*iich,if a critical size is exceeded according to Seltz,1 will result in a streanerbeing formed. The fields at the streamer tip, estimated to be in the order of10 v/cm, exceed the intrinsic electric strength eund complete breakdown ensues.The concept is similar to the streamer theory developed by Loeb cind Meekl forgas breakdown and collisional ionization leading to electron avalanches andTOstreamer formation in liquids by Goodwin and MacFadyen.Thermal breakdown of a solid is associated with a decrease in electricstrength with increasing tanperatiare. The tenperature rise in a solid may occuras a result of heat transferred from an external source or direct dissipation inthe solid from electric stressing. When a DC field is applied to a dielectric atroom tenperature the conduction current is generally very low. The conductioncurrent increases rapidly with increasing tenperature if the heat is not conductedaway, causing a thermal run away condition. The electric stress sinply exceedsthe dielectric strength of the material at the elevated tenperature.In the caseof AC voltages, heat is generated inside the dielectric as a result of dipolerelaxation. The losses associated with AC fields are usually much greater than DCfields because the loss in relaxation phenomena such as dipolar motions dependupon the rate of change of the field.Consequently, thermal breakdown strength isgenerally lower for AC fields and decreases with increasing frequency.Erosion breakdown, as the name inplies, involves long term degradation of asolid from arcs, or parital discharges generated within or at the boundaries ofthe solid and an electrode surface or another insulating medium.Repeated surfacedischarges across a solid insulator surface can gradually raxove enough materialalong preferential paths until breakdown occurs. Cavities, voids or particle12
inclusions vhich have lower breakdown strengths -than the solid dielectric resultin corona generation and eventual failure from within the volume of the material.The problem of breakdown from gas filled voids is aggravated by the fact that thegas usually has a lower dielectric constant than the solid and the electric fieldin the void is correspondingly increased according to:192fl fo - 2e 1vhere E is the field in the solid in the absence of the void and e is thepermittivity of the solid. The same relation applies to bubbles in a liquid.In addition to the foregoing failure modes, solids, particularly soft onesmay be subject to electromechanical failure. This type of failure is the resultof electrostatic pressure produced by the electric field. A two-dimensionalmechanical stress is thereby produced in the insulator with cortpression throughthe thickness and tension in the lateral direction.Should the stresses exceedthe tensile or compressive strength of the material it will fail mechanically.Liquid dielectrics exhibit the same general characteristics as solids withrespect to failure modes and dielectric strength dependence on tatperature, pulsetime, stressed area cind thickness in the short gap ranges ( 1 cm).They differfrom solids in their sensitivity to particle and chemical contamination, absorbedgases and increased strength at high hydrostatic pressures.Probably the most widely used relationship for inpulse breakdown of liquiddielectrics is the enpirical formula developed by J. C. Martin"' for gaps greaterthcin 1 cm:Etl/3 AO-1 KvSiereE is the field strength in MV/cm13
t is effective pulse time, the time the voltage is greater than 0.63 of itsmaximum valueA is electrode area in cm2K 0.5 for transformer oil.The expression has been experimentally verified for areas up to 10pulse times from less than 20 ns to at least 1.0/is.a gap dependence of d ' om2 andFor small electrode spacingsin the expression gives a better fit to breakdowndata:21Etl/3A0-ld-l/4 KMartin's liquid breakdown formula applies specifically to bulk breakdownconditions with conparatively long time intervals (at least minutes) between shotsso that the effects of arr ' disturbances in the liquid such as partial dischargesor streamers that do not completely cross the electrode gap have time to heal.Gas generated by partial discharges and streamers in the captive oil volumeof a transfonner can not generally be tolerated because of shot to shot buildup.The transformer designer must therefore be more concerned with the corona inceptionvoltage (CIV) than with dielectric strength. Corona or partial discharge damagein transformers has been a well known problem in AC power transformers and lowvoltage pulse transformers for over 50 yecirs. It has only recently received attention as a major problem with high voltage pulse transformers. The primary reasonis that high voltage pulse transformers were used in single shot applicationsv iere mild corona discharges had little or no effect over a life of five to tenthousand shots. However, with repetitive pulse systems which have life ejtpecQtancies of at least 10shots, corona danage has become a dominant considerationin pulse transfomer design.Figure 20 is a photograph of damage to Mylar filmproduced by repetitive pulsing with partial discharges for several thousand shots.14
This type of failure is common in spiral strip transformers when partial dischargesoccur in the oil adjacent to the film surface.22Clarkgives a brief description of the products of corona m mineralinsulating oils.He shcvs that the products of ionization associated with coronabear a strong resemblance to those produced by controlled heat treatment (heatcracking).The primary gaseous products include:HydrogenH2Carbon MonoxideCOCarbon e 2In addition to the gaseous products, carbon particles amd unsaturated liquid hydrocarbons are formed. The liquids have poor oxidation stability and in generallower dielectric strength. Thus corona discharges over a long period of timeresult in the buildup of lav strength liquids which eventually render the oiluseless as a dielectric.It is well known that moderate carbon particle, dust and moisture contamination in many insulating oils does not decrease the dielectric strength appreciablyunder fast pulse conditions in the range of nanoseconds to at least 10 fis. These23contaminates do, however, lower the CIV v\hich is not as sensitive to pulse time.With silicone oils, for exanple, a reduction of nearly 30% has been measuredbetween dry oil sanples and ones with a moisture content of 170 pprtr (Figure 21).The CIV reduction is lineeu: over that range and fits the equation:CIV - 0.55 X 3610 kV/cmX water content (ppm)15
other experiments with oil inpregnated m/lar-copper disk laminates sandwichedbetween flat plate electrodes (Figure 22) showed similcir results with respect topartial discharge effects. A variety of oils were pulse tested in both "barrelfresh" condition and in the dry degassed condition.In some cases breakdown ofthe laminate from repetitive partial discharges differed by as much as 30%.Table I summarizes the oils tested and the nominal breakdown levels.Table IOnset of Partial Discharges in Various OilsTested in Laminate StructuresDry Degassed ConditionkV/cmBarrel Fresh ConditionkV/cm325590360620460650Transformer Oil, InhibitedX-ray Oil (Marcol 2930)Silicone Oil (Dow Coming 200)MIPB (Mansanto 1238)DAA (HISOL SAS 10 E)Paraffin Oil (RTEnp)250510305410390380Voltage stresses are mean values and are intended to illustrate cortparativeproperties of the oils in two conditions. To determine -the actual stress in theoil and mylar film it is necessary to caipute the stress distribution in the twodielectric system according to the relation:%Vo, d -H d (e/e ) / " oE2 d (e /e ) d , v/cmv ereV Q is the total voltage across the electrodes, kVE-j and E2 are the voltage stresses in materials 1 cind 2e-j and &2 the dielectric constants of materials 1 and 2d-j and d are the thicknesses of materials 1 and 2 in an.16
Considerable caution must be exercised in interperting dielectric strengthand pcirtial
pulse rises to several hundred kV is 10 ns or less. Fast pulse transformers nay also be used to direct drive higher itipedance electron guns. Other devices could be included in a discussion of air core pulse trans formers. This paper will cover only the general types designed for high voltage pu