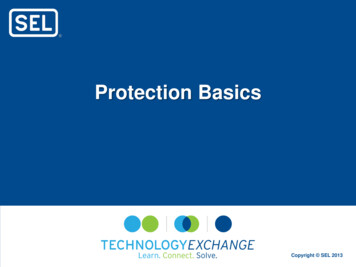
Transcription
Protection BasicsCopyright SEL 2013
Protection Review Fault types Electrical equipment damage Time versus current plot Protection requirements Protection system elements
Power System Faults Short circuits Contacts with ground Isolated neutral systems High-impedance grounded systems Open phases
Typical Short-Circuit-Type DistributionSingle-phase-to-ground70 – 80%Phase-to-phase-to-ground10 – 17%Phase-to-phaseThree-phase8 – 10%2 – 3%
Faults in Electrical SystemsProduce Current IncrementsabcDistributionSubstationIIWire
Temperature Rise From CurrentTConstantCurrentITTeEquilibriumTitdW 2 I Rdt T(t) (Ti – Te )e–tτ Te
Factors Influence Wire HeatingCurrentMagnitudeIdWire SizeWire MaterialPropertiesAmbientTemperatureand OtherEnvironmentalFactors
Insulated Conductor (Cable)Thermal DamageTITeInsulationTdInsulation DamageTitdt
Insulated Conductor Thermal DamageITTtI I3 I2I I2 I1I I1DamageCurvet1t2t3TdI ImdTit3 t2 t1tImd I1 I2 I3I
Electrical Equipment ComponentThermal Damage CurvetDamageCurveIn ImdRatingI
Mechanical DamageMechanical forces (f1 and f2) produced byshort-circuit currents cause instantaneousdamage to busbars, insulators, supports,transformers, and machinesf1f2i1i2f1 (t) k i1 (t) i2 (t)
Real-World Mechanical Damage
Power System Protection Requirements Reliability Dependability Security Selectivity
Power System Protection Requirements Speed System stability Equipment damage Power quality Sensitivity High-impedance faults Dispersed generation
Protection Functions Fault detection Faulted element disconnection Fault indication
Protective Devices Fuses Automatic reclosers Sectionalizers Circuit breakers Protective relays
Relay Classification Protective Regulating Reclosing andsynchronism check Monitoring Auxiliary
IEEE C37.2 Device Numbers51Time-overcurrent relay50Instantaneous-overcurrent relay67Directional-overcurrent relay21Distance relay87Differential relay52Circuit breaker
Protective Relaying SystemCurrentTransformers(CTs)Circuit unicationsChannelDCSupply
Protection System Elements Protective relays Circuit breakers CTs and VTs (instrument transformers) Communications channels DC supply system Control cables
Protection System Elements Protective relays Monitor Detect Report Trigger Circuit breakers Interrupt Isolate from abnormal condition
Instrument Transformers CTs Current scaling Isolation VTs Voltage scaling Isolation
Overcurrent Relay Connectionsabc50, 51IaIb52Ic50, 5150, 5150N, 51N3I0ResidualCurrent
DC Tripping Circuit( )SIDC itBreaker
Overcurrent Relay Setting 51 elements Pickup setting Time-dial setting 50 elements Pickup setting Time delay
Review What is the function of power systemprotection? Name two protective devices For what purpose is IEEE device 52 is used? Why are seal-in and 52a contacts used in thedc control scheme? In a typical feeder OC protection scheme,what does the residual relay measure?
Questions?
Digital Relay BasicsSEL-751A Feeder ProtectionRelayCopyright SEL 2013
Simple Protective RelayAuxiliary input(ac or dc)InputOutput (dry contact)Current,voltage (I and V),or other quantitiesSettingsSet relay thresholdsand operation timeContact used toenergize circuitbreaker trip coil
ElectromechanicalInstantaneous Overcurrent Elements
MagneticAttraction UnitContactsCoilInstantaneous ElementArmatureHingeContactsContactsCoilIron coreAdjustablestopOperatingmagnetForce of contact: F k I2RestrainingmagnetHinge
Pickup Current Setting Tap in relay current coil Adjust air gap Adjust spring
ElectromechanicalInverse-Time Overcurrent Elements
Anatomy ofInduction DiscOvercurrentRelaysMain Coil,NT TurnsPermanentMagnetTime Dial-5-6-7-8-91.0SpringMovingContactDiscMain Core
Simplified ViewShaded Pole sΦ1 Φ2Taps
Electromagnetic Induction PrincipleΦ1Φ2TorqueiΦ2F1 F2iΦ2iΦ1iΦ1
Summary of Induction51 Element Setting Pickup current setting – taps in relay currentcoil Time-current curve setting – controls initialdisc position (time dial setting)
Microprocessor-Based Protection
Digital Relay I/O SchemeAuxiliary inputs(ac or dc)Analog inputsDiscrete inputsComputer-basedrelay (digital)ComputercommunicationsDry contact outputs(trip and alarm)“Live” outputs
Digital Relay Architecture Analoginputsubsystem Operationsignalling ROM / PROM Tripping}CommunicationsportsEEPROM
Digital Relay AlgorithmRead present sample kDigital filteringPhasor calculationModify ifrequiredProtection methodsRelay logicNo tripTrip order
Relay OperationAnalog Inputs
Signal Path forMicroprocessor-Based lter andphasorMagnitudeandimpedance
A/D 10010010010000:.Analog signalDigital signal
Digital FilteringNonfiltered signal(samples)Digital filteringFiltered signal(samples)
Phasor CalculationFiltered signal(samples)Phasor calculationPhasor samples:magnitude and angleversus reference I θReference
Sinusoid-to-Phasor Conversionv(t)A2A0θ0t
Sinusoid to PhasorsCurrent Channels Are 7016562273
Sinusoid to Phasors Pick quadrature samples (1/4 cycle apart) Pick current sample (x sample) Pick previous sample 1/4-cycle old (y sample)IA1559–69–1656–2274–15587016562273y sample (1/4-cycle old)x sample (present)
Sinusoid to PhasorsMagnitude x y2 y Angle arctan x – 2274 Angle arctan 70 2Magnitude 70 2 (–2274 )2IA 2275 – 88.2 IA1cycles8YIa(t)–88.2t2275227470X
Relay OperationRelay Word Bits and Logic
Relay Word Bits Instantaneous overcurrent Time overcurrent Voltage elements Inputs Internal relay logic: SELOGIC variable (SV) and latches OutputsAssert to logical 1 when conditions are true,deassert to logical 0 when conditions are false
Instantaneous-Overcurrent Element 50P1P instantaneous phase-overcurrent setting Ip measured current of maximum phase 50P1P 1 if Ip 50PIP; 50P1P 0 if Ip 50P1Pab50P1P settingIp Comparatorc50P1PWhen b ( ) terminal is greater thana (–) terminal, c is logical 1
SEL-751A Protection SystemPhase Time-Overcurrent ElementRelay Word Bits51P1P PickupSetting51P1P51P1T Phase TimeOvercurrent Element CurveTiming and Reset TimingSettingsTorque Control SwitchIP(From Figure GICTorque Control51P1CT51P1MRPickupPickup TypeTime DialElectromechanicalReset? (Y / N)Constant TimeAdderMinimumResponseControls the Torque Control Switch51P1TCStateTorque ControlSwitch PositionSetting51P1RS Logical 1Logical 0ClosedOpenYNReset TimingElectromechanical1 Cycle51P1TCurveTimeout51P1R Reset
SEL-751A Protection SystemORED – Overcurrent Elements Relay Word bit ORED50T is asserted if50PnT, 50NnT, 50GnT, or 50QnT RelayWord bits are asserted Relay Word bit ORED51T is asserted if51AT, 51BT, 51CT, 51P1T, 51P2T, 51N1T,51N2T, 51G1T, 51G2T, or 51QT RelayWord bits are asserted
Standard Time-Current CharacteristicsIEEE C37.112-1996
SEL-751A Voltage Calculation(Minimum Phase Voltage Magnitude)VAB or VAVBC or VBVCA or VCVAVP min(Minimum Phase-to-Phase Voltage Magnitude)VPP minVoltage(Maximum Phase Voltage Magnitude)MagnitudeVP maxCalculation (Maximum Phase-to-Phase Voltage Magnitude)VPP maxVS
SEL-751A Single- and Three-PhaseVoltage ElementsRelayWordBitsWhen DELTA Y : WYEVPP max3P27 27P127P1P VnmVP min –27P1D27P1T027P227P2P Vnm –27P1D27P2T0
SEL-751A Relay Word Bit Tables8 Relay Word Bits Per Numbered RowRowRelay Word Bits150A1P 50B1P 50C1P 50PAF ORED50T ORED51T 50NAF250P1P 50P2P 50P3P 50P4P50Q1P50Q2P50Q3P 50Q4P350P1T 50P2T 50P3T 50P4T50Q1T50Q2T50Q3T 50Q4T450N1P 50N2P 50N3P 50N4P50G1P50G2P50G3P 50G4P550N1T 50N2T 50N3T 50N4T50G1T50G2T50G3T 50G4T52A
Logic
Boolean Logic Mathematics of logical variables (RelayWord bits) Operators: AND, OR, NOT, rising and fallingedge, parentheses SELOGIC control equations Booleanoperators Defined symbols Application rules
SELOGIC Control Equations TFunctionGroup termsChanges sign of numerical valueInvert the logicRising edgeOutput asserts for one processingR TRIGinterval on inputs rising-edge transitionFalling edgeF TRIGMultiply*Output asserts for one processinginterval on inputs falling-edge transitionMultiply numerical values
SELOGIC Control Equations OperatorsOperatorSymbolFunctionDivide/Divide numerical valuesAdd Add numerical valuesSubtract–Subtract numerical values , , , ComparisonCompare numerical values, , ANDANDORORMultiply Boolean valuesAdd Boolean values
SELOGIC Control Equation ExamplesABOR1CC A OR BABAND1CC A AND BABAND1C C A AND NOT BABABAB
Programmable Logic( )AACBDBCDLogicEE(–)Equation implementedE A AND B OR COR NOT D
SELOGIC Control Equation ExamplesTR 50P1P AND 50G150P1P50G1POUT101 TRIPTRIPOUT101TRWhen the TRequation asserts,the TRIP RelayWord bit assertsNormally open;closes whenOUT101 asserts
Typical Logic Settings for Trip
SELOGIC Control Equation ExamplesCL CC AND 3P59 AND 27S1OUT102 CLOSECLOSECC3P5927S1OUT102CLWhen CL equationasserts, CLOSERelay Word bitassertsNormally open;closes whenOUT102 asserts
SELOGIC ExampleOUT101 (51P1T OR OUT101) AND NOT TRGTR!TRGTROUT101 51P1TOUT101OUT101
Optoisolated s65000ms65000msIN101logical 0IN102logical 1 Relay Word bits IN101 and IN102 monitorphysical state inputs Debounce timer is built in and settable
Latching Control LogicSELOGIC LatchEquationRelayWord BitSETnLTnRSTnn 1 – 32SET01 CLOSE RST01 TRIP 52A LT01
SV Timer Set as logic placeholder andtimerSV05 Example settings SV05 50P1P SV05PU 0.17 secondsSV05SV05PUSV05D0 Operation SV05 asserts when 50P1P asserts SV05T asserts 0.17 seconds after50P1P assertsSV05T
nOUT102OUT102logical1energizeOUT102(a)Closed When OUT101 equation is true (logical 1),OUT101 closes Example setting: OUT301 SV05T Operation: OUT301 closes after 50P1P hasbeen asserted for 0.17 seconds
Track Relay Word Bit State ChangeWith Sequential Events Report (SER)Example: 50P1 4 A; CTR 120;Primary PU 480 A
Event Reporting Helpful in fault analysis Relay collects 15-cycle event reportwhen ER R TRIG 50P1P HIS command text
Summary Microprocessor-based relays createphasors from sinusoid (waveform) input Relay Word bits control relay I/O Microprocessor-based relays offer manytroubleshooting and fault analysis tools SELOGIC control equations provideprogramming flexibility to create virtualcontrol circuits
Questions?
Protection Basics:Overcurrent ProtectionCopyright SEL 2008
Fast Protection Minimizes Temperature rise Mechanical damage frommagnetic forces Voltage sag Transient stability issues Shock and arc-flash hazards
Understand Basic ProtectionPrinciples Overcurrent (50, 51, 50N, 51N) Directional overcurrent (67, 67N) Distance (21, 21N) Differential (87)
Overcurrent Relays Protect RadialLinesmILoadRelayILOADE ZSource ZLine ZLOADIFAULTE ZSource m ZLineIFAULT ILOAD
Relay Operates When CurrentMagnitude Rises Above Threshold( )Overcurrent RelayI125 VdcTCCircuit Breaker Trip Coiland Auxiliary Contact52a(–)
Evolving Protective Relay Designs Electromechanical relays Electronic analog relays – solid state(transistors, integrated circuits) Microprocessor-based relays – digital ornumeric
How Do Instantaneous Relays Work?ContactsContactsCoilCoilArmatureIron CoreCoil 2AdjustableStopHingeCoil 1MagneticCoreContactsMoving Cupor CylinderElectromagnet
Plotting Electromechanical 50 ElementsTime vs. Current CurvetAdjustableIpickuptoperate 1.5 CyclesI
Digital Overcurrent Relay BlockDiagram AnalogInputSubsystem OutputSubsystemOperationSignaling ROM / PROM TrippingOutputs}CommunicationsPortsEEPROM
Digital Relays Use Sampled SignalsPresentSample t Sample Interval
Advantages of Digital 50 Elements No contact chatter with alternating currents Not affected by dc offset Reset-to-pickup ratio close to one Resistant to misoperation due to mechanicalshock
Anatomy ofInduction DiscOvercurrentRelaysMain Coil,NT TurnsPermanentMagnetTime Dial-5-6-7-8-91.0SpringMovingContactDiscMain Core
Induction Disc Operation ConditionOperating torque spring torqueK eI2 TsPickup condition2K eIpu TsPickup set by changing number of turns (TAP)Ipu Ts K e Ts K′ / NT
Induction Disc Relay DynamicsMCθSCθFAcceleration TorqueTa Top – Tpm – Ts – Tf
High Current Can Damage EquipmentThermal Damage CurvetTime vs. Current PlotDamageCurveIRated IdamageI
Changing Induction Disc OperationTimetAdjustment of Time Curve Displacement ofmoving contact isadjustableTimeDialDamageCurve Time dial sets totalmovement requiredto close contactAdjustableIpickupI
Curve Comparison for TDS 110Time (s)1ModeratelyInverseInverse0.1Very InverseExtremely Inverse0.01110100Multiples of Current PickupSelectOvercurrentRelay CurveCurve shape notadjustable forinduction disc relays
Time-Current CharacteristicsBecome Standard IEEE C37.112-1996 A t TD P B M 1 IEC 225-4At TD PM 1
Family of IEEE Inverse Characteristics102Time vs. Current PlotU.S. inverse curveTime (s)101TD 10100A 5.95, P 2, B 0.18 5.95 t OP TD 2 0.18 M 1 32110–110–2100101102Multiples of Current Pickup
Increase Flexibility With Digital 51RelaysSettings Pickup current (or tap)tTD Time-dial setting (TD)Curve Shape Curve shape – inverse,very inverse, etc.IpickupI
Connecting ElectromechanicalOvercurrent RelaysabcĪa50 / 51ĪbĪc50 / 5150 / 5150N / 51N3Ī052ResidualCurrent
Digital Relays CalculateResidual CurrentIAIC IA IB IC 3I0 IG 0IBResidual currentfor ground faultResidual current forbalanced load orthree-phase faults3I0 IGIAIC IA IB IC 3I0 IGIB
Using Zero-Sequence CT forGround Fault ProtectionC B ACurrent InputsINIACOMINIBCOMINICCOMPhoto courtesy of NEI ElectricPower EngineeringININCOMZero-sequence or core-balance CT52
High Residual Current Due toCT Saturation Residual settings must be higher thanelements operating from zero-sequence CTs Residual elements may not be appropriatefor motors Zero-sequence CTs not subject to thisproblem
15,000 HP Motor Trips on StartNumerical Relay50G 4950NIG800/5IN50/5
What Are Negative-SequenceQuantities?IBIC Unbalanced loadIAIA Open phasesICIBPositiveSequence Rolled phasesNegativeSequence3I2 IA a2IB aICwhere a 1 120 Unbalanced faults
Negative-Sequence ElementResponseThree-Phase Faults52I2, IPhaseRelayFaultIA 1 0 3I2 IA IB 1 120 a2IBIC 1 120 aIC 1 0 1 240 1 120 1 120 1 120 0
Negative-Sequence Element ResponsePhase-to-Phase Faults52I2, IPhaseRelayFaultIA 03I2 IAIB 1 0 a2IB 0 1 240 1 0 1.73 – 90 IC 1 180 aIC 1 120 1 180
Maximum Load vs.Minimum Short CircuitI3-Phase Fault CurrentPhase-to-Phase Fault CurrentIPUPhase Relay MaximumReachILOADdRRelay
Sensitive Protection WithNegative-Sequence ElementsIb-c fault, 3I2b-c fault, phasecurrentReach of ConventionalPhase RelaysReach ofNegative-SequenceElementILOAD3I2 PUdRRelay
Coordinating FIR51RFeederRelay51F, 51QFFPhase 51, no 51Q
Traditional Phase CoordinationPlus Negative Sequence20Equivalent PhaseElement WithLow Pickup51EPSE 10CO 7N 5D 4S51F51R3210.70.50.40.30.20.11023 4 57CURRENT (A)10023 4 57IR IPU-E IF100023 4 5710000 23 4 57
Set Negative-Sequence Element Pickup51Q pickup 3 (51EP pickup)Negative-sequence element is faster and moresensitive than phase overcurrent element forphase-to-phase faults
Protection Plus
Questions?
Transformer Protection BasicsCopyright SEL 2013
Differential Protection Is Easy in TheoryI1I2I3nKirchhoff’s Current Law (KCL): Ik 0k 1
Current In Current OutBalanced CT RatioCTProtectedEquipmentCTExternalFault50IOP 0No Relay Operation if CTs Are Considered Ideal
Operate Current FlowsCTProtectedEquipmentInternalFault50IOP ISETTINGRelay OperatesCT
Differential Scheme Objective Provide security during through faults Operate fast for internal faults
What Makes DifferentialProtection Challenging?Transformer EnergizationI1Transformer CompensationI2CT SaturationI3
Examine CT Saturation Challenges
Unequal CT Performance ProblemsCTProtectedEquipmentCTExternalFault50IOP 0
Unequal CT Saturation200Current at LeftCurrent at RightSecondary Amperes150100500–50–100–150Differential Current–2000123Cycles456
Possible Scheme – PercentageDifferential Protection 7)IOP IS IRCompares:k IRTIS IR k 2
Differential Element
Differential Characteristic BasicsIOPOperateRegionIOPFor ExternalFault WithSaturated CTRestraintRegionIPUIRTRelay Operates When:IOP k IRT IPU
Percentage Differential RelaysIOP Versus W2
Dual-Slope CharacteristicIOP(Multiples of Tap)UnrestrainedPickupOperateRegionSlope 1Slope 2RestraintRegionMinimumPickupSlope 1–2Transition(Multiples of Tap)IRT
How to Set Slope Characteristic Settings Load tap changer (10%) No-load tap changer (5%) Measuring relay error ( 5%) CT errors (1 to 10%) Transformer excitation (3 to 4%)
SEL-387 / SEL-787 LogicSEL-387 /SEL-7872nd and 4thHR / HBO87PDIFF
SEL-387 / SEL-787 Slope32.52IOP (IRT)1.510.50012345IRT6789 10
Examine TransformerCompensation Challenges
Transformer Connection CompensationPhase Shift(Degrees)030 lag60 lag120 lag150 lag180 lag150 lead120 lead60 lead30 Dy1Dz2Dz4Dy5Dd6Dy7Dz8Dz10Dy11Dz0Yz1Yz5Dz6Yz7Yz11
Traditional Compensation MethodCTR1(Ia Ib ) (N2 / N1 )N1 : N2Ia(Ib Ic ) (N2 / N1 )Ib(Ic Ia ) (N2 / N1 )IcR3(Ic Ia ) / CTR2(Ic Ia ) (N2 / N1 ) / CTR1R2(Ib Ic ) (N2 / N1 ) / CTR1(Ia Ib ) (N2 / N1 ) / CTR1CTR2R1(Ib Ic ) / CTR2(Ia Ib ) / CTR2
Compensation With Digital Relays Current magnitude and phase shiftcompensation Set relay according to transformercharacteristics Consider all possible connections
Tap CompensationMVA 1000 CTAP 3 KVLL CTRwhere:C 1 for wye-connected CTsC 3 for delta-connected CTs
Simpler and Better ConnectionsX1H1H3X3H2Winding 1ABCX2Winding 2H1H2X1X2H3X3IAW1 IAW2IBW1 IBW2ICW1 ICW2abc
DABY Transformer and CTConnection CompensationX1H1H3DABY Dy1 X3H2YY1Tap11Tap2YDAB87X2
Wye Connection CompensationIAW11Tap1IAW1I1W1C Tap1IBW11Tap1IBW1I2W1C Tap1ICW11Tap1YI3W1C ICW1Tap1
DAB Connection CompensationIAW21Tap2IAW2 IBW2)(1I1W2C Tap23IBW21Tap2IBW2 ICW2)(1I2W2C Tap23ICW21Tap2DABICW2 IAW2)(1I3W2C Tap23
Compensation MatricesIAWnCIAWnM12M1M2M11M10M3M9M4M8M5M7M6
SEL-387 Compensation Method IAWnC IAWn IBWnC [CTC(m)] IBWn ICWnC ICWn [CTC(m)]: 3 x 3 matrix m 0, 1, 12 m 0: identity matrix (no changes) m 0: remove I0; compensate angles m 12: remove I0; no angle compensation
Differential Element Operateand Restraint QuantitiesIW11 IW1' Transformer / I1CT ConnectionTap1Compensation IW21 IW2' Transformer / I2CT ConnectionTap2CompensationI1 I2IOP(Multiples of Tap)I1 I22IRT(Multiples of Tap)
Examine TransformerInrush Challenges
Phase C Inrush Current ObtainedFrom Transformer Testing300Primary Current (A)250200150100500–5001234Cycles567
Inrush Current Has HighSecond HarmonicPrimary Current(A)100Fundamental Frequency Magnitude2nd Harmonic Magnitude5001234567567CyclesPercentage ofFundamental80602nd Harmonic Percentage402nd Harmonic Block Threshold2001234Cycles
Internal Faults Versus InrushHarmonic-Based Methods Harmonic blocking Harmonic restraint
Inrush Conditions – BlockingIOPOperate RegionOperate PointSlope 2Restraint RegionSlope 1IRT
Inrush Conditions – RestraintIOPOperate RegionSlope 2Restraint RegionOperatePointSlope 1IRT
Conclusions Apply differential element Slope 2 tocompensate for CT saturation Set current compensation for phase andmagnitude differences across transformers Use harmonic blocking and restraint toprevent differential element assertionduring inrush
Questions?
Induction and Synchronous MotorProtection RecommendationsCopyright SEL 2013
Induction Motor Protection Phase overcurrent (50 / 51) Ground overcurrent(50G / 50N / 51G / 51N) Voltage (27 / 59) Current unbalance (46) Differential (87)
Induction Motor Protection Phase sequence (47) Resistance temperature device (RTD)thermal (49R) Thermal overload (49) Load-loss / load-jam (37) Starts per hour, time between starts (66) Antibackspin
Synchronous Motor Protection Induction motor protection elements Loss-of-excitation (40) Loss-of-synchronism (78) Field ground fault (64F)
Phase Overcurrent Protection (50 / 51)Ground Overcurrent Protection(50G / 50N / 51G / 51N)
Phase Overcurrent Protection Phase overcurrent devices detect phase-tophase and three-phase faults within motorwindings and on feeder cables Failure to clear fault quickly causes Increased motor conductor or feedercable damage Stator iron damage Prolonged system voltage dips
Settings Considerations Do not use relay phase fault protection withfused motor contactors Avoid tripping on motor inrush Symmetrical locked rotor current Subtransient component Asymmetrical (dc offset) componenteffectively removed from element bymicroprocessor-based relay Coordinate with upstream protection
Optimum Two-Level PhaseOvercurrent Protection Level 1 settings Phase overcurrent pickup at 1.2 to 1.5 LRA Overcurrent delay at 6 to 10 cycles to ridethrough subtransient inrush Level 2 settings Phase overcurrent pickup at 1.65 to2.0 LRA Phase overcurrent delay at 0
Ground Overcurrent Protection Ground overcurrent devices detect faultsinvolving ground within motor windings andon feeder cables Failure to clear these faults quickly causes Increased motor conductor or feeder cabledamage Stator iron damage Prolonged system voltage dips
Ground Fault Protection Depends onSystem Grounding Design Solidly grounded systems have high phaseto-ground fault currents Resistance-grounded systems limit phaseto-ground fault current Limiting current limits damage due toground faults but requires increased relaysensitivity
CT Connections(a) Solidly / Low-ResistanceGrounded Source(b) Solidly / Low-ResistanceGrounded SourceMPR(c)5050G3MPRLow- / N1MPRMotorMPR motor protection relay
Solidly Grounded Systems Ground fault currents in solidly groundedsystems can approach phase fault levels Ground fault protection for these systems isusually provided by residual protection,either calculated by relay or by external CTresidual connection to IN input
Settings Considerations Residual protection set to coordinate withupstream devices False residual current can occur because ofCT saturation Level 1 residual overcurrent pickup set at0.4 to 0.6 FLA Level 1 residual overcurrent delay set at 0.2s to ride through false residuals
Low-Resistance Grounded Systems Ground fault currents limited to 100 to 1000 A Ground faults cleared in 10 s Minimize fault arc damage Protect grounding resistors fromthermal damage Ground fault protection for motors is usuallyinstantaneous or definite-time
Settings Considerations Residual elements Set Level 1 residual overcurrent pickup at0.4 to 0.6 FLA Set Level 1 residual overcurrent delay at 0.2 sto ride through false residuals upon starting Ground elements with core-balance CT Set Level 1 neutral overcurrent pickup at5 to 20 A primary current Set Level 1 neutral overcurrent delay at 0.1 s
High-Resistance Grounded Systems Typically found on low-voltage systems butsometimes used on medium-voltagesystems Limit phase-to-ground fault currents to 10 A
High-Resistance Grounded Systems Single-phase-to-ground fault produces analarm only – ground can then be locatedand cleared in controlled manner This system requires core-balance CT forsensitivity
Settings Considerations Set Level 1 neutral overcurrent pickup at25 to 50% of available ground fault current Set Level 1 neutral overcurrent delay at2 to 5 s Program neutral overcurrent for alarm only
Ground OvercurrentSettings ConsiderationsAvailableSourceCTRelaySettingGround FaultDelayGroundingConnections Function roundedHighresistancegroundedCan approachphase faultlevels100 to 1000 A 10 Aa50Gb50Na50G40 to 60% FLA0.2 s40 to 60% FLA0.2 sb50Nc50N5 to 20 A(primary)0.1 s50N25 to 50% ofavailableground faultcurrent2 to5sc
Undervoltage Protection (27)Overvoltage Protection (59)
Undervoltage Running motors for prolonged periods atless than rated voltage can causeoverheating Undervoltage tripping can clear a bus aftercomplete loss of voltage – preventssimultaneous restart of connected motorswhen voltage returns
Settings Considerations Motor standards require motors capable ofcontinuous operation at 90% of motor-ratedvoltage per motor specification Undervoltage protection should not tripmotors because of voltage dips caused byfaults or motor starts Undervoltage protection is not usually set totrip motors during fast bus transfers
Settings Considerations – Trip Set undervoltage trip pickup slightly underminimum rated operating voltage Set undervoltage trip delay longer than Maximum time required for fast bus transfers Maximum fault-clearing time for faults thatwould cause voltage to drop below pickup Starting time for any motor on bus if motorstarts will cause bus voltage to drop belowundervoltage trip pickup
Settings Considerations – Alarm Set undervoltage alarm level at or slightlyabove motor minimum rated operatingvoltage Set undervoltage alarm delay longer than Maximum time required for normal bustransfers Maximum fault-clearing time for faults thatwould cause voltage to drop below pickup
OvervoltageRunning motors for prolonged periods atgreater than rated voltage can cause loss ofinsulation life or insulation failure
Settings Considerations Motor standards require that motors becapable of continuous operation at 110%of rated voltage Overvoltage alarming is generally used infavor of overvoltage tripping If overvoltage tripping is applied, considerusing a time delay
Current Unbalance Protection (46)
Current Unbalance Caused by Unbalanced voltages Single phasing Creates negative-sequence current flowin rotor Heating effect at full load is same as lockedrotor condition Rotor overheats
Negative-Sequence HeatingRotor BarStatusStartingS′ S 1S SlipRunningS′ S 0.01UnbalanceS′ 2 – SS′ Rotor Current Frequency Negative-sequence current causes doublefrequency flux in rotor Rotor current occupies one-sixth of cross-sectionarea of bars, causing overheating at periphery
Current Unbalance Biases thermal overload element Is detected by Thermal model under moderate conditions Current unbalance elements undersevere conditions
Settings Considerations Trip Set current unbalance trip pickup to 15% Set current unbalance trip delay to 5 s Alarm Set current unbalance alarm pickup to 10% Set current unbalance alarm delay to 10 s
Differential Protection (87)
Differential ProtectionCT52M87 Phase differential (large machines) Self-balancing (87M) differential (machinesrated 1000 hp and up) Detection of phase faults and possiblyphase-to-ground faults depending onsystem grounding
Phase PercentageDifferential (87R)52OOORRRRRRO operating coilR restraining coil
Percentage Restraint (87)Differential CharacteristicIOP(Multiples of TAP)UnrestrainedPickupOperateSlope 125%Slope 260%RestrainMinimumPickupSlope 1 to 2Transition(Multiples of TAP)IRT
Self-Balancing (87M) Differential ProtectionABCore-balance CTMotorCIA87Neutral-side CT withIA, IB, and ICconnectedIB87ABMotorCIA87IAIBICNeutral-side CT withIA, IB, and IC notconnectedIC87ABIB87IC87MotorCIA87IB87IC87
Phase Sequence Protection (47)
Phase Sequence Also referred to as phase reversal Operates on voltage or current Checks that phase rotation signals appliedto relay match phase rotation setting
RTD Thermal Protection (49R)
RTD Thermal Element DetectsLoss-of-Cooling Efficiency Cooling pump failure Inlet air reduction Detection using direct temperaturemeasurement (RTDs)
Thermal Overload Protection (49)
Thermal Protection Running overload Starting / stalling Running unbalance
Running Protection Load greater than service factor causesexcessive I2R heating in stator windings Unbalance current causes excessiveheating in rotor
Thermal Model Protection Electromechanical relays using bimetal andsolder-pot elements do not match motortime constants Microprocessor-based relays can matchthermal properties identified by motor dataand can monitor RTDs embedded instator winding
Integrated Motor Thermal Protection Provides locked rotor, overload, andunbalance protection Defines operating characteristics by motorcharacteristics
Bimetallic Overload Element I2R heating opens contacts to trip motor Reset characteristic not related to motor This element has Uncertain response to unbalance Sensitivity to c
Nov 18, 2019 · 51P1T Phase Time-Overcurrent Element Curve Timing and Reset Timing 51P1P 51P1C 51P1TD 51P1RS 51P1CT 51P1MR Settings Relay Word