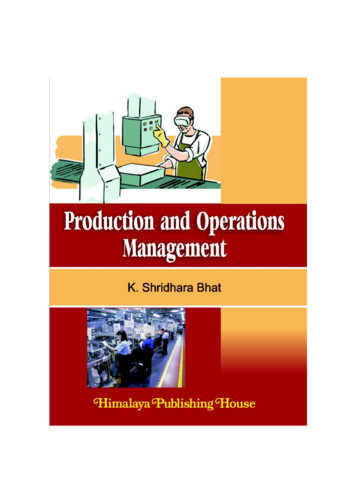
Transcription
Operations Management – An Overview1
2Production and Operations ManagementPRODUCTION ANDOPERATIONSMANAGEMENTProf. K. SHRIDHARA BHATB.E. (Mech), PG DIM, M.B.A. F.I.I.M.M.Managing DirectorAkshaya Management Consultancy ServicesBangalore - 560 085Karnataka, IndiaMUMBAI NEW DELHI NAGPUR BENGALURU HYDERABAD CHENNAI PUNE LUCKNOW AHMEDABAD ERNAKULAM BHUBANESWAR INDORE KOLKATA GUWAHATI
Operations Management – An Overview3 AuthorNo part of this publication may be reproduced, stored in a retrieval system, or transmitted in any form or by any means,electronic, mechanical, photocopying, recording and/or otherwise without the prior written permission of the publishers.First Edition : 2011Published by: Mrs. Meena Pandey for Himalaya Publishing House Pvt. Ltd.,“Ramdoot”, Dr. Bhalerao Marg, Girgaon, Mumbai - 400 004.Phone: 022-23860170/23863863, Fax: 022-23877178E-mail: himpub@vsnl.com; Website: www.himpub.comBranch Offices:New Delhi: “Pooja Apartments”, 4-B, Murari Lal Street, Ansari Road, Darya Ganj,New Delhi - 110 002. Phone: 011-23270392, 23278631; Fax: 011-23256286Nagpur: Kundanlal Chandak Industrial Estate, Ghat Road, Nagpur - 440 018.Phone: 0712-2738731, 3296733; Telefax: 0712-2721215Bengaluru: No. 16/1 (Old 12/1), 1st Floor, Next to Hotel Highlands, Madhava Nagar,Race Course Road, Bengaluru - 560 001. Phone: 080-32919385;Telefax: 080-22286611Hyderabad: No. 3-4-184, Lingampally, Besides Raghavendra Swamy Matham,Kachiguda, Hyderabad - 500 027. Phone: 040-27560041, 27550139;Mobile: 09848130433Chennai: No. 85/50, Bazullah Road, T. Nagar, Chennai - 600 017.Phone: 044-28144004/28144005Pune: First Floor, "Laksha" Apartment, No. 527, Mehunpura, Shaniwarpeth(Near Prabhat Theatre), Pune - 411 030. Phone: 020-24496323/24496333Lucknow: Jai Baba Bhavan, Church Road, Near Manas Complex and Dr. Awasthi Clinic,Aliganj, Lucknow - 226 024. Phone: 0522-2339329, 4068914;Mobile: 09305302158, 09415349385, 09389593752Ahmedabad: 114, “SHAIL”, 1st Floor, Opp. Madhu Sudan House, C.G. Road,Navrang Pura, Ahmedabad - 380 009. Phone: 079-26560126;Mobile: 09327324149, 09314679413Ernakulam: 39/104 A, Lakshmi Apartment, Karikkamuri Cross Rd., Ernakulam,Cochin - 622011, Kerala. Phone: 0484-2378012, 2378016;Mobile: 09344199799Bhubaneswar: 5 Station Square, Bhubaneswar (Odisha) - 751 001. Mobile: 09861046007Indore: Kesardeep Avenue Extension, 73, Narayan Bagh, Flat No. 302, IIIrd Floor,Near Humpty Dumpty School, Narayan Bagh, Indore - 452 007 (M.P.).Mobile: 09301386468Kolkata: 108/4, Beliaghata Main Road, Near ID Hospital, Opp. SBI Bank,Kolkata - 700 010, Phone: 033-32449649, Mobile: 09910440956Guwahati: House No. 15, Behind Pragjyotish College, Near Sharma Printing Press,P.O. Bharalumukh, Guwahati - 781009. (Assam).Mobile: 09883055590, 09883055536DTP by: Page Designers, BengaluruPrinted by: New Delhi.
4Production and Operations ManagementPrefaceProduction and Operation Management (POM) is about the transformation ofproduction and operational inputs into outputs, that when distributed, meet the needs of customers.POM incorporates many interdependent tasks which can be grouped under five main headingsviz., Product, Plant, Processes, Programmes and People. Production and Operations Managersensure that quality products are produced and delivered as quickly and cost effectively aspossible. Therefore, a basic knowledge of this subject is essential for students of MBAprogrammes.This book comprises 11 chapters covering various important topics such as OperationsStrategy, Production Planning and Control, Design of Production Systems, Design of WorkSystems, Aggregate Production Planning, Project Management, Scheduling of Operations,Maintenance Management, Quality Management and Facility Location and Layout.This book is specifically designed to cover the syllabus of MBA programme offered byBiju Patnaik University of Technology. However, it may be found useful to students of MBAprogramme of any other Indian university as well. The book has special features such asillustrations, solved problems, review questions, problems to be solved and case illustrationsand case exercises.I have great pleasure to express my sincere thanks to Sri Niraj Pandey and Sri Anuj Pandeyof Himalaya Publishing House for their keen interest and effort to publish this book. I am alsothankful to Sri Vijay Pandey for his effort in printing and promoting this book in a very short time.I thank Sri B.S. Madhu and Smt. Divya of M/s Page Designers for their excellent D.T.P.work. I am also thankful to Smt. Nimisha, Sri Rajesh, Sri Yogesh of HPH production unitfor their effort in designing the cover page and printing this book.I also thank my family members, friends and well-wishers for their constant support andencouragement for this endeavour. I also thank one and all who have directly or indirectly helpedor supported me in my work. I invite readers, both students and teachers to offer their valuablesuggestions as a feedback to me so as to improve the book in its future editions.K. SHRIDHARA BHATNo.680, ‘Akshaya’, 1 ‘C’ Main,Kempegowda Layout, 3rd Block,3rd Phase, Banashankari III StageBangalore - 560 085.Phone : (080) 26694761Email : sbhat680@yahoo.com
Operations Management – An Overview5ContentsCHAPTER 1. OPERATIONS MANAGEMENT - AN OVERVIEW1 - 30Meaning of "Production" – Meaning of “Operations” – Nature of Production/Operations– Production Functions – Managing a Production/Operating System – Distinctionbetween Production Management and Operations Management – Objectives ofProduction/Operations Management –Decision Making in Production/OperationsManagement – Organising to Produce Goods and Services – Functions of Production/Operations Managers – Problems of Production/Operations Management – The HistoricalEvolution of Production/Operations Management – The Scope of OperationsManagement – Recent Trends in Production/Operations management – Systems Designand Systems Operation – A Production System Model – Production System Diversity –Types of Production Systems – Differentiating Features of Production Systems – FactorsAffecting Production and Operations Management Today – Review QuestionsCHAPTER 2 : OPERATIONS STRATEGY31 - 46Productivity – Competitiveness – Production/Operations Strategy – Competitive Priorities– Building Production/Operations Strategy on Competitive Priorities – Elements ofProductions/Operations Strategy – Solved Problems – Review Questions – PoblemsCHAPTER 3 : OPERATIONS PLANNING AND CONTROL47 - 70Classification of Production Planning and Control Functions – Production Planning (orOperations Planning) – Factors Determining Production Planning Procedures – ProductionPlanning System – Production Control – Production Control System – FactorsDetermining Production Control Procedures – Production Planning/Operations Planningand Control – Role of Production Planning and Control in Operations Management –Scope of Production Planning and Control – Principles of Production Planning andControl – Phases in Production Planning and Control Function – Main Functions ofProduction Planning and Control Department – Levels of Production Planning –Production Planning Functions – Production Control Functions – Benefits of ProductionPlanning and Control Function – Limitations of PPC – Measuring Effectiveness of PPCFunction – Production Planning and Control in Different Production Systems –Organisation of PPC Department – Routing – Scheduling and Loading – Objectives ofScheduling – Elements of Scheduling – Types of Scheduling – Dispatching – Centralisedand Decentralised Dispatching – Progressing (or Expediting or Follow-up) – ReviewQuestionsCHAPTER 4. DESIGN OF PRODUCTION/OPERATIONS SYSTEMS[A] Product Planning and Development: What is a Product? – Need for Product Planningand Development – Objectives of Product Planning and Development – Characteristicsof Successful Product Development – Role of Production Management in ProductDevelopment – The Challenges of Product Development – New Product71 - 111
6Production and Operations ManagementDevelopment Strategy – New Product Development Process – Approaches to Speed upNew-Product Development – The Product-life Cycle Concept – Factors to be Consideredin Product Development. [B] Product Design: Product Design, Process Design andProduction Design – Importance of Product Design – What does Product Design Do? –Reasons for Product Design or Redesign – Objectives of Product Design – FactorsInfluencing Product Design – The Product Design Process as a part of ProductDevelopment Process – Sources of Ideas for Designing New Products or Redesigningthe Products – Stages in Product Design – Design Documents for Production – Effectof Product Design on Product Cost. [C] Process Management: What is a Process? –Process Planning – Process Management – Major Process Decisions – Make-or-buyDecisions – Make-or-buy Analysis – Procedure for Process Planning and Design –Process Design – Scope of Process Design – Basic Factors Affecting Process Design –Major Factors Affecting Process Design Decisions – Interrelationship Among ProductDesign,Process Design and Inventory Policy – Arithmetic Analysis – Logarithmic Analysis –Selecting a Learning Rate – Uses and Limitations of Learning Curves – Solved Problems– Review Questions – ProblemsCHAPTER 5 : DESIGN OF WORK SYSTEMS112 - 156(A) Productivity: Productivity Measurement – Productivity Improvement – FactorsAffecting Productivity – Productivity Improvement Techniques. (B) Job Design: JobDesign Decisions – Factors Affecting Job Design – Behavioural Considerations in JobDesign – Physical Considerations in Job Design – Machine-Worker Interaction –Ergonomics – The Work Environment. (C) Work Study: Objectives of Work Study –Scope of Work Study – Relationship between Method Study and Work Measurement –Basic Work Study Procedure – Method Study – Method Study Procedure – RecordingTechniques Used in Method Study – Motion Study – Principles of Motion Economy –Memomotion Study – Work Measurement – Objectives of Work Measurement –Techniques of Work-measurement – Time Study – Synthesis Method – AnalyticalEstimating – Predetermined Motion Time System (PMTS) – Work Sampling or ActivitySampling or Ratio-Delay Method – Solved Problems – Review Questions – ProblemsCHAPTER 6 : AGGREGATE PRODUCTION PLANNING157 - 185Aggregate Planning – Objectives of Aggregate Planning – Operations Planning andScheduling Systems – Aggregate Production (Output) Planning – Aggregate Planningor Aggregate Capacity Planning – Approaches to Aggregate Planning – Aggregate Plansfor Services – Capacity Requirement Planning – Capacity Requirement Planning (CRP)Process – Aggregate Capacity Planning Strategies – Level Capacity Plan – MatchingCapacity with Aggregate Demand Plan – Strategies for Aggregate Capacity Planning –Master Production Scheduling – Procedure for Developing MPS – Guidelines for MasterScheduling – Updating of MPS – MPS in Produce-to-Stock and Produce-to-Order Firms– Length of Planning Horizon of MPS – Symptoms of a Poorly Designed MPS – SolvedProblems – Review Questions – ProblemsCHAPTER 7 : CAPACITY PLANNINGTypes of Capacity – Measurement of Capacity – Capacity Decisions – Factors AffectingDetermination of Plant Capacity – Capacity Planning – Capacity Changes – Types ofCapacity Planning – Capacity Requirement Planning Strategies – Economic Batch186 - 209
Operations Management – An Overview7Quantity for Production – Long-Range Capacity Planning – Forecasting Long-termFuture Capacity Demand – Economies and Diseconomies of Scale – Developing CapacityAlternatives – Selecting from Among the Alternative Sources of Capacity (or CapacityAlternatives) – Solved Problems – Review Questions – ProblemsCHAPTER 8 : PROJECT MANAGEMENT210-237Project Management – Project Life Cycle –Project Organisation –The Role of a ProjectManager – Problems in Managing a Project – Project Planning and Control Techniques– Network Fundamentals – Commonly Used Network Symbols – Terms used in NetworkBased Scheduling Techniques – Networking Conventions – Project SchedulingTechniques – Scheduling Chart (Gantt Chart or Horizontal Bar Chart) – ProgrammeEvaluation and Review Technique (PERT) and Critical Path Method (CPM) – Critical PathMethod (CPM) – Purpose of CPM – Procedure for Drawing up a CPM Network – CPM- Time Analysis – Programme Evaluation and Review Technique (PERT) – DeterminingProbability of Meeting Scheduled Date in PERT Analysis – Crashing CPM Networks –Steps in Network Crashing – Solved Problems – Review QuestionsCHAPTER 9 : SCHEDULING OF OPERATIONS238 - 270The Production Environment – Production Activity Control or Shop Floor ActivityControl – Operations Planning and Scheduling – Scheduling – Scheduling Process Focused Production Systems – Scheduling Techniques for Job Shop – Stages inScheduling – Loading, Dispatching – Finite Loading and Infinite Loading – Load Chartsand Machine Loading Charts – Priority Sequencing – Single-Criterion Priority SequencingRules – Dynamic Sequencing Rules – Johnson’s Rule or Algorithm – Scheduling ProductFocused Systems – Batch Scheduling – Economic Batch Quantity (EBQ) or EconomicRun Length (ERL) – Solved Problems – Review Questions – ProblemsCHAPTER 10 : MAINTENANCE MANAGEMENT271 - 300What is Maintenance? – Areas of Maintenance – Types of Maintenance – Planning andScheduling of Maintenance – Control of Maintenance – Total Productive Maintenance– Reliability and Maintenance – Basic Concepts and Definitions – Evolution of the Fieldof Reliability – Reliability measurement – The Strategic Importance of Maintenance andReliability – Solved Problems – Review Questions – ProblemsCHAPTER 11 : FACILITY LOCATION AND LAYOUT(A) Facility Location: The Need for Location Decisions – The Nature of LocationDecisions – General Procedure for Making Location Decisions – Factors affectingLocation Decisions – Methods of Evaluating Location Alternatives – Single FacilityLocation versus Multi-facility Location – Centre of Gravity Method. (B) Facility Layout:Significance of Layout Choices – Factors Influencing Layout Choices – Principles ofPlant Layout – Types of Layout – Layout Planning – Layout Tools and Techniques –Analysing Layouts with Computers – Layout or Building? – Criteria for Selection andDesign of Layouts – Computerised Layout Techniques – Design of Group TechnologyLayout – Line Balancing – Line Balancing Methods – Solved Problems – ReviewQuestions – Problems301 - 363
8Production and Operations ManagementCHAPTER 12 : INVENTORY MANAGEMENT364 - 395Nature and Importance of Inventory – Classification of Inventories – Functions ofInventory – Inventory Costs – Inventory Decisions – Inventory Models – QuantityDiscounts for the EOQ Model – Importance of Inventory Management – InventoryControl Systems – Inventory Control Systems for Independent-Demand Items –Continuous Review System (“Q” System) – Selective Inventory Control – Measurementof the Effectiveness of Inventory Management – Simulation Technique for DecisionMaking in Inventory Management – Solved Problems – Review Questions – ProblemsCHAPTER 13 : RESOURCE REQUIREMENTS PLANNING396 - 426Resource Requirements Planning – Material Requirements Planning (MRP or MRP-I ormrp) – Objectives of MRP – Manufacturing Resource Planning or MRP-II – GeneralOverview of MRP (Material Requirements Planning) – Operation of the MRP System –Definitions of Terms used in MRP System – The MRP Computational Procedure – Issuesin MRP – Potential Benefits from MRP – Implementation of MRP – Problems in usingMRP – Problems in Designing the MRP System – Problems in Managing the MRP System– Evaluation of MRP – Manufacturing Resource Planning (MRP II) – Evolution of MRPII – Enterprise Resource Planning – Just-In-Time Systems (JIT) – Solved Problems –Review Questions – ProblemsCHAPTER 14 : QUALITY MANAGEMENT427 - 483Nature of Inspection – Inspection and Quality Control – Scope of Inspection – QualityControl – Organisation for Quality Control – Ensuring Quality – Statistical Quality Control(SQC) – Types of Control Charts – Test for Homogeneity – Control Charts for Attributes– Acceptance Sampling Technique – Operating Characteristic (OC) Curves – Types ofAcceptance Sampling Plans – Total Quality Management – What is quality management?– Modern Quality Management – Process Management – Bench Marking – BusinessProcess Reengineering (BPR) – Quality Movement in India – Quality Circles (QC) –Quality Certification – Solved Problems – Review Questions – ProblemsANNEXURE484 - 486CASE ILLUSTRATIONS487 - 501CASE EXERCISES502 - 510INDEX511 - 522
Operations Management – An Overview9CHAPTER ONEOverview of Production andOperations ManagementThe managing of any organisation that produces products demanded by customers presents a greaterchallenge today than ever before. While all other functional managers are involved in planning, organisingand controlling in their own field of work, production/operations managers who are in charge of manufacturingthe products have the direct responsibility of getting the job done. They must be the leaders in the task ofproducing products demanded by the customers most efficiently and effectively. The production/operationsmanagers are involved in planning, organising, co-ordinating, executing and controlling of all activities thatcreate goods and/or services to satisfy the needs of their customers. Of all the functional areas of management,production management (which is also referred to as operations management) is considered to be crucialin any manufacturing organisation because it is responsible for converting raw materials into finished goodsensuring that the objectives regarding volume of production (quantity), quality of outputs (i.e., products),cost of production (i.e., productivity), the timeliness of production (i.e., delivery schedules to meet customerdemand), customer service and ultimately maximum possible customer satisfaction are met.Meaning of "Production"Production implies the creation of goods and services to satisfy human needs. It involves conversionof inputs (resources) into outputs (products). It is a process by which, raw materials and other inputs areconverted into finished products. Earlier the word "manufacturing" was used synonymously with the word"production", but nowadays, we use the term "manufacturing" to refer to the process of producing onlytangible goods whereas the word "production" (or operation) is used to refer to the process of creating bothgoods (which are tangibles) as well as services (which are intangibles).Any process which involves the conversion of raw materials and bought-out components into finishedproducts for sale is known as production. Such conversion of inputs adds to the value or utility of theproducts produced by the conversion or transformation process. The utility or added value is the differencebetween the value of outputs and the value of inputs. The value addition to inputs is brought about byalteration, transportation, storage or preservation and quality assurance.Meaning of “Operations”The term “operations” refers to a function or system that transforms inputs into outputs of greater value.Operations are often defined as a transformation or conversion process wherein inputs such as materials,machines, labour and capital are transformed into outputs (goods and services). In a productive system, if theoutputs are strictly tangible goods, such a system is referred to as a “production system” and thetransformation process is referred to as “production”. Nowadays, the service system in which the outputis predominantly a service or even a pure service, is also treated as a productive system and often referredto as an “operating system” instead of a “production system”9
10Production and Operations ManagementDifference between Goods and Services(i) Services are usually intangible whereas goods are tangible (i.e., can be touched and seen)(ii) Services are often produced and consumed simultaneously, services cannot be stored whereasgoods can be produced and inventoried before consumption or use.(iii) Services are often unique, for example insurance policies, medical treatment procedures, haircutstyles, etc.(iv) Services have high customer interaction, services are often difficult to standardize and automatebecause customer interaction demands uniqueness. The service product may have to be customizedin most of the service offerings.(v) Services are often knowledge based, for example educational, health-care, legal and consultancyservices and, therefore, difficult to standardize and automate.(vi) Services are frequently dispersed because services may have to delivered to the client/customer athis/her place or office, a retail outlet or even at the residence of the customer/client.(vii) Goods can be inventoried and can be resold whereas reselling of services is unusual and servicescannot be inventoried.(viii) Some aspects of quality of goods are measurable whereas many aspects of quantity of services aredifficult to measure.(ix) Selling and production are distinct in case of goods whereas in case of services selling is often a partof the service.(x) Goods can be transported whereas service cannot be transported but the service provider can betransported.(xi) Location of facility to manufacture goods, affects costs whereas location of service facility affectscustomer contact.(xii) Manufacturing of goods can be easily automated whereas service is often difficult to automate.NATURE OF PRODUCTION/OPERATIONSThe nature of production or operations can be better understood by viewing the manufacturing functionas :(i)(ii)(iii)(iv)Production/operations as a system,Production/operations as an organisational function,Production/operations as a conversion or transformation process andProduction/operations as a means of creating utility.These four distinct views are discussed in the following section.Production/Operations as a SystemThis view is also known as "systems concept of production". A system is defined as the collection ofinterrelated entities. The systems approach views any organisation or entity as an arrangement of interrelatedparts that interact in ways that can be specified and to some extent predicted. Production is viewedas a system which converts a set of inputs into a set of desired outputs. A production system has thefollowing elements or parts : (i) Inputs, (ii) Conversion process or transformation process, (iii) Outputs(iv) Transportation subsystem, (v) Communication subsystem and (vi) Control or decision makingsubsystem.
Operations Management – An Overview11Exhibit 1.1 illustrates the systems view of production/operations function.Exhibit 1.1 : Systems View of Production/Operations FunctionExternal EnvironmentInputsCustomer/Client Participation t Goods and/or Services ofUtilityControl Subsystem.FeedbackDecision Maker(ProductionManagement)FeedbackExternal EnvironmentProduction/Operations as an Organisational FunctionTo create goods and services, all organisations whether manufacturing goods or providing servicesperform four basic functions. They are (i) Marketing function (ii) Production or Operations function. (iii)Finance function and (iv) Human Resources function. Production is considered as a crucial function whichcreates goods and services whereas marketing function generates demand for products or obtains customers’orders, finance function keeps track of how well the organisation performs and takes care of all cash inflowsand cash outflows, and human resources function looks into the people aspect of the organisation and the bestutilisation of people in the organisation. Production function plays a central role in achieving the objectivesof any business organisation.Production/Operations as a Conversion/Transformation ProcessThe conversion or transformation sub-system is the core of a production system because it consists ofprocesses or activities wherein workers, materials, machines and equipment are used to convert inputs intooutputs, i.e.,Conversion ProcessInputsOutputs(A simple production system)The conversion process may include manufacturing processes such as cutting, drilling, machining,welding, painting, etc., and other processes such as packing, selling, etc.Any conversion process consists of several small activities referred to as "operations" which are somesteps in the overall process of producing a product or service that leads to the final output.
12Production and Operations ManagementTable 1.1 illustrates some examples of conversion processes used in the production systems.Table 1.1 : Examples of Conversion Processes used in Production utsSteel PlantIron ore, coal/coke limestone,labour, machinerySmelting, rollingSteel sections,sheetsRestaurantHungry customers, chefs,services, equipmentCooking andserving foodSatisfiedcustomersAutomobilePlantRaw materials andcomponents, machinery,labourFabrication ofparts and assemblyof automobilesAutomobileOil RefineryCrude oil, equipment, labourChemical processesPetroleum(Fractional distillation) ProductsSupermarketCustomers with needs,salespersonsSelling/retailingSatisfied customersCollege orUniversityHigh school students, teachersTeaching (Impartingknowledge and skills)Graduates (Educatedpersons)AirlineAeroplanes, pilots, engineers,flight attendantsAir transportationSatisfied customersto their destinationsProduction/Operations as a Means of Creating UtilityProduction is defined as the process of adding to the value of outputs or the process of creating utilityin outputs. "Utility" is the power of satisfying human needs. During the process of converting the rawmaterials into finished goods, various types of utilities are created while adding value to the outputs. Thesetypes of utilities are :(i) Form utility: which is created by changing the size, shape, form, weight, colour, smell of inputsin order to make the outputs more useful to the customers. For example, iron ore is changed tosteel, wood is changed to furniture, etc.(ii) Place utility: which is created by changing the places of inputs or transporting the inputs from thesource of their availability to the place of their use to be converted into outputs. For example theiron ore and coal are transported from the mines to the steel plant to be used in the conversionprocess.(iii) Time utility: which is created by storage or preservation of raw materials or finished goods whichare in abundance sometime, so that the same can be used at a later time when they become scarcedue to higher demand exceeding the quantity available.(iv) Possession utility: which is created by transferring the possession or ownership of an item fromone person to another person. For example, when a firm purchases materials from a supplier, thepossession utility of the materials will increase when they are delivered to the buying firm.(v) Service utility: which is the utility created by rendering some service to the customer. For example,a doctor or a lawyer or an engineer creates service utility to a client/customer by rendering servicedirectly to the client/customer.(vi) Knowledge utility: which is created by imparting knowledge to a person. For example, a salespresentation or an advertisement about some product communicates some information about theproduct to the customer, thereby imparting knowledge.
Operations Management – An Overview13The activities carried out while creating the utilities discussed above are referred to as productionfunctions.Production FunctionProduction function may be defined as the creation of useful products for sale with the help of inputssuch as materials, machines, labour, land, capital and management. The production function representsbasically a physical relationship between inputs and outputs. It may be represented asQ (a, b, c, d.)where ‘Q’ is the quantity of output and a, b, c, d, etc., represent the quantities of various inputs such asmaterial, machine hours, labour hours, energy, etc., The production function specifies the amount of outputsresulting from the amount of inputs used during a specified period of time. The productive use of theresources is described by the term productivity. Productivity is an index that measures outputs (goods andservices) relative to the inputs (materials, energy and other resources).OutputIt is usually expressed as, Productivity InputProductivity is also known as productive efficiency or the efficiency of the production process. Itindicates how well a productive process is carried out to convert a set of inputs into a set of outputs of valueto the customer which also provides reasonable profits to the manufacturer or seller.Importance of Production FunctionThe production is the core function of any business organisation. Production function creates goodsand services and organisations exist primarily to create goods and/or to provide services. Without productionfunction, there would be no need for any other function such as marketing, finance or human resourcefunction. Also, more than 50 per cent of employees in a business organisation have jobs in the area ofproduction. Moreover the production function is responsible for a major portion of assets in most organisations.Consumption of goods and services is an integral part of any society and production function facilitatescreation of goods and services for the benefit of people in the society.Box 1.1 lists some of the areas in which production/operations management can offer competitiveadvantage to a firm.Box 1.1 : Areas in which Production/Operations Management can offer CompetitiveAdvantage(i) Shorter new product lead time (i.e., speed to market)(ii) Higher inventory turnover (i.e., low inventory)(iii) Shorter manufacturing cycle time(iv) Higher product quality (i.e., reduced defects)(v) Greater flexibility(vi) Better customer service(vii) Reduced was
Systems, Aggregate Production Planning, Project Management, Scheduling of Operations, Maintenance Management, Quality Management and Facility Location and Layout. This book is specifically d