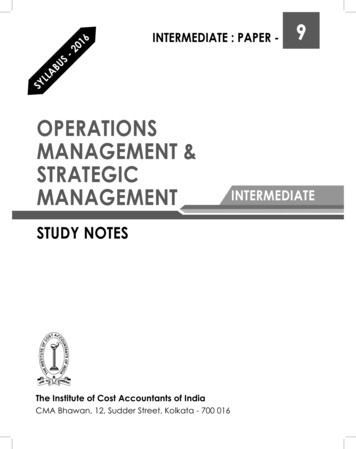
Transcription
6019syllabus-2INTERMEDIATE : paper -OperationsManagement &strategicmanagementstudy notesThe Institute of Cost Accountants of IndiaCMA Bhawan, 12, Sudder Street, Kolkata - 700 016INTERMEDIATE
First Edition : August 2016Published by :Directorate of StudiesThe Institute of Cost Accountants of India (ICAI)CMA Bhawan, 12, Sudder Street, Kolkata - 700 016www.icmai.inPrinted at :Copyright of these Study Notes is reserved by the Institute of CostAccountants of India and prior permission from the Institute is necessaryfor reproduction of the whole or any part thereof.
Syllabus - 2016Paper 9: Operations Management & strategic management (OMSM)Syllabus StructureThe syllabus comprises the following topics and study weightage:AOperations Management70%BStrategic Management30%B30%A70%ASSESSMENT STRATEGYThere will be written examination paper of three hours.OBJECTIVETo provide an in depth study of the various business process, analyze operations, production planning and strategicmanagement.Learning AimsThe syllabus aims to test the student’s ability to: Understand the business process and analyze the operations Acquire knowledge of production planning and resource management Understand the concept of Corporate Vision - Mission and Objectives Understand the concept of SWOT and Portfolio Analysis Understand the different stages in strategy formulation process Understand the concept of Strategic Business Unit and Business Process re-enginneringSkill Set requiredLevel B: Requiring the skill levels of knowledge, comprehension, application and analysis.Section A : Operations Management1.Operations Management – Introduction2.Operations Planning3.Designing of Operational Systems and control70%4. Production Planning and control5. Productivity management and quality management6. Project Management7. Economics of Maintenance and Spares managementSection B : Information Systems8.Strategic Management Introduction9.Strategic Analysis and Strategic Planning10. Formulation and Implementation of Strategy30%
Section A: Operations Management [70 marks]1. Operation Management Introduction:Scope characteristics of modern operations functions - recent trends in production / operations management.2. Operations Planning:Demand forecasting – capacity planning - capacity requirement planning - facility location - facility layout –Resource aggregate planning – Material requirements planning – Manufacturing resource planning – EconomicBatch quantity.3.Designing of operational systems and control:Product Design, Process design - Selection - Product Life Cycle – Process Planning – Process Selection.4. Production planning and Control:Introduction – Control Measures – Time study, Work study, Method study, Job Evaluation, Job Allocation(Assignment Technique), Scheduling Queuing Models, Simulation and Line Balancing – Optimum Allocationof resources – Lean Operations – JIT – Transportation Model and Linear Programming Technique (Formulationof equations only).5. Productivity Management and Quality Management:Measurement techniques of productivity index, productivity of employee, productivity of materials, productivityof management resources, productivity of other factors – productivity improving methods – TQM basic toolsand certification – ISO standards basics.6. Project Management:Project planning – project life cycle – Gantt charts, PERT and CPM.7.Economics of Maintenance and Spares Management:Break down Maintenance – Preventive Maintenance – Routine Maintenance – Replacement of Machine –Spare Parts Management.Section B: Strategic Manangement [30 marks]8. Strategic Management IntroductionVision- Mission and objective9. Strategic Analysis and Strategic PlanningSituational Analysis –SWOT Analysis – Portfolio Analysis – BCG Matrices – Stages in Strategic Planning – Alternativesin Strategic Planning10.Formulation and Implementation of Strategy:Strategy formulation function wise (Production Strategy, Marketing Strategy, Man Power Strategy) – Structuringof Organisation for implementation of strategy – Strategic Business Unit – Business Process re-engineering.
ContentsStudy Note 1 : Operation Management – Introduction1.1Operations Management - Introduction11.2Production Management vs. Operation Management31.3Characteristic of Modern Operation Function41.4Recent Trends in Production / Operations Management4Study Note 2 : Operations Planning2.1Demand Forecasting72.2Capacity Planning152.3Capacity Requirement172.4Facility Location212.5Facility Layout242.6Resource Aggregate Planning332.7Material Requirements Planning362.8Manufacturing Resource Planning372.9Enterprise Resource Planning382.10Economic Batch Quantity38Study Note 3 : Designing of Operational System and Control3.1Production Design453.2Process Design & Selection483.3Process Planning483.4Product Life Cycle503.5Process Selection51Study Note 4 : Production Planning and Control4.1Production Planning and Control Introduction534.2Time Study, Work Study, Method Study & Job Evaluation564.3Job Allocation – Assignment Technique594.4Scheduling684.5Queuing Models73
4.6Simulation834.7Line Balancing924.8Lean Operations974.9Just-In-Time (JIT)974.10Transportation Model984.11Linear Programming Technique111Study Note 5 : Productivity Management and Quality Management5.1Measurement Techniques of Productivity Index1335.2TQM Basic Tools and Certification1415.3ISO Standard Basics143Study Note 6 : Project Management6.1Project Planning1476.2Gantt Charts1516.3PERT and CPM156Study Note 7 : Economics of Maintenance and Spares Management7.1Break Down Maintenance1677.2Preventive Maintenance1677.3Routine Maintenance1687.4Replacement of Machine1707.5Spare Parts Management173Study Note 8 : Strategic Management Introduction8.1Vission, Mission and Objective197
Study Note 9 : Strategic Analysis and Strategic Planning9.1Situational Analysis2119.2SWOT Analysis2129.3Portfolio Analysis2159.4BCG Matrices2169.5Stages in Strategic Planning2239.6Alternative in Strategic Planning226Study Note 10 : Formulation and Implementation of Strategy10.1Strategy Formulation Function-wise (Production Strategy, Marketing Strategy,Manpower Strategy22910.2Structuring of Organisation for Implementation of Strategy24310.3Strategic Business Unit24610.4Business Process Re-engineering248
Study Note - 1Operations Management – introductionThis Study Note includes1.1Operations Management - Introduction1.2Production Management vs. Operation Management1.3Characteristic of Modern Operation Function1.4Recent Trends in Production/Operations Management1.1 operations management - IntroductionOperations management is the management of that part of an organization that is responsible for producinggoods and/or services. There are examples of these goods and services all around you. Every book you read,every video you watch, every e-mail you send, every telephone conversation you have, and every medicaltreatment you receive involves the operations function of one or more organizations. So does everything youwear, eat, travel in, sit on, and access the Internet with.However, in order to have a clear idea of Operations Management, one must have an idea of ‘Operating Systems’.An Operating System is defined as a configuration of resources combined for the provision of goods or services.Retail organizations, hospitals, bus and taxi services, tailors, hotels and dentists are all examples of operatingsystems. Any operating system converts inputs, using physical resources, to create outputs, the function of whichis to satisfy customers wants. The creation of goods or services involves transforming or converting inputs intooutputs. Various inputs such as capital, labour, and information are used to create goods or services using oneor more transformation processes (e.g., storing, transporting, and cutting). To ensure that the desired output areobtained, an organization takes measurements at various points in the transformation process (feedback) andthen compares with them with previously established standards to determine whether corrective action is needed(control).It is important to note that goods and services often occur jointly. For example, having the oil changed in yourcar is a service, but the oil that is delivered is a good. Similarly, house painting is a service, but the paint is a good.The goods-service combination is a continuum. It can range from primarily goods, with little service, to primarilyservice, with few goods. Because there are relatively few pure goods or pure services, companies usually sellproduct packages, which are a combination of goods and services. There are elements of both goods productionand service delivery in these product packages. This makes managing operations more interesting, and also morechallenging.Objectives of Operations ManagementObjectives of operations management can be categorised into (i) Customer service and (ii) Resource utilisation.(i)Customer serviceThe first objective is the customer service for the satisfaction of customer wants. Customer service is therefore a keyobjective of operations management.The Operations Management must provide something to a specification which can satisfy the customer in termscost and timing. Thus, primary objective can be satisfied by providing the ‘right thing at the right price at the righttime’.These three aspects of customer service - specification, cost and timing - are described in a little more detail forthe four functions in Table 1. They are the principal sources of customer satisfaction and must, therefore, be theprincipal dimension of the customer service objective for operation managers.operations managment & strategic management1
Operations Management – IntroductionTable 1: Aspects of Customer ServicePrincipal customer wantsPrincipal functionPrimary considerationManufactureGoods of a given, requestedacceptable specificationOther considerationor Cost i.e. purchase price or cost of obtaininggoodsTiming, i.e. delivery delay from order or requestto receipt of goodsTransportMovement of a given, requested or Cost, i.e. cost of movement, Timing ,i.e.acceptable specification(i)duration or time to move(ii)SupplyGoods of a given, requestedacceptable specificationwait, or delay from requesting to itscommencementor Cost, that is purchase price or cost obtaininggoodsTiming, i.e. delivery delay from order or requestto supply, to receipt of goodsServiceTreatment of a given, requested or Cost, i.e. cost of treatmentacceptable specificationTiming, i.e.(i)Duration or timing required for treatment(ii)wait, or delay from requesting to itscommencementGenerally an organization will aim reliably and consistently to achieve certain standards, or levels, on thesedimensions, and operations managers will be influential in attempting to achieve these standards.Hence, this objective will influence the operations manager’s decisions to achieve the required customer service.(ii) Resource UtilizationAnother major objective is to utilize resources for the satisfaction of customer wants effectively, i.e., customer servicemust be provided with the achievement of effective operations through efficient use of resources. Inefficient useof resources or inadequate customer service leads to commercial failure of an operating system.Operations management is concerned essentially with the utilization of resources, i.e., obtaining maximum effectfrom resources or minimizing their loss, under utilization or waste. The extent of the utilization of the resources’potential might be expressed in terms of the proportion of available time used or occupied, space utilization,levels of activity, etc. Each measure indicates the extent to which the potential or capacity of such resources isutilized. This is referred as the objective of resource utilization.Operations management is also concerned with the achievement of both satisfactory customer service andresource utilization. An improvement in one will often give rise to deterioration in the other. Often both cannotbe maximized, and hence a satisfactory performance must be achieved on both objectives. All the activities ofoperations management must be tackled with these two objectives in mind, and many of the problems will befaced by operations managers because of this conflict. Hence, operations managers must attempt to balancethese basic objectives.Below Table 2 summarizes the twin objectives of operations management. The type of balance establishedboth between and within these basic objectives will be influenced by market considerations, competitions, thestrengths and weaknesses of the organization, etc. Hence, the operations managers should make a contributionwhen these objectives are set.Table 2 : The twin objectives of operations managementThe customer service objective.The resource utilization objective.To provide agreed/adequate levels of customer service To achieve adequate levels of resource utilization(and hence customer satisfaction) by providing goods (or productivity) e.g., to achieve agreed levels ofor services with the right specification, at the right cost utilization of materials, machines and labour.and at the right time.2operations managment & strategic management
Scope of Operation ManagementOperations Management concern with the conversion of inputs into outputs, using physical resources, so as toprovide the desired utilities to the customer while meeting the other organizational objectives of effectiveness,efficiency and adoptability. It distinguishes itself from other functions such as personnel, marketing, finance, etc. byits primary concern for ‘conversion by using physical resources’. Following are the activities, which are listed underProduction and Operations Management functions:1.Location of facilities.2. Plant layouts and Material Handling.3. Product Design.4. Process Design.5. Production and Planning Control.6.Quality Control.7. Materials Management.8. Maintenance Management.Location ofFacilitiesPlant g andControlFig. 1 : Scope of production and operations management1.2 productions management vs operations managemetThere are two points of distinction between production management and operations management. First, the termproduction management is more used for a system where tangible goods are produced. Whereas, operationsmanagement is more frequently used where various inputs are transformed into intangible services. Viewed fromthis perspective, operations management will cover such service organisations as banks, airlines, utilities, pollutioncontrol agencies, super bazaars, educational institutions, libraries, consultancy firms and police departments, inaddition, of course, to manufacturing enterprises. The second distinction relates to the evolution of the subject.Operations management is the term that is used nowadays. Production management precedes operationsmanagement in the historical growth of the subject.operations managment & strategic management3
Operations Management – Introduction1.3 characteristic of modern operations functionThe production management of today presents certain characteristics which make it look totally different fromwhat it was during the past. Specifically, today’s production system is characterised by at least four features.1.Manufacturing as Competitive AdvantageIn the past production was considered to be like any other function in the organisation. WhefT demand washigh and production capacities were inadequate, the concern was to somehow muster all inputs and use themto produce goods which would be grabbed by -narket. But today’s scenario is contrasting. Plants have excesscapacities, competition is mounting and firms look and gain competitive advantage to survive and succeed.Interestingly, aroduction system offers vast scope to gain competitive edge and firms intend to exploit thepotential. Total Quality Management (TQM), Time-Based Competition, Business Process Re-engineering (BPRE),Just-in-Time (JIT), Focused Factory, Flexible Manufacturing Systems (FMS), Computer Integrated Manufacturing(CIM), and The Virtual Corporation are but only some techniques which the companies are employing to gaincompetitive advantage.2.Services OrientationAs was stated earlier, service sector is gaining greater relevance these days. The production system, therefore, needsto be organised keeping in mind the peculiar requirements of the service component. The entire manufacturingneeds to be geared to serve (i) intangible and perishable nature of the services, (ii) constant interaction withclients or customers, (iii) small volumes of production to serve local markets, and (iv) need to locate facilities toserve local markets. There is increased presence of professionals on the production, instead of technicians andengineers.3. Disappearance of SmokestacksProtective labour legislation, environmental movement and gradual emergence of knowledge based organisationshave brought total transformation in the production system. Today’s factories are aesthetically designed andbuilt, environment friendly - in fact, they are homes away from homes. Going to factory everyday is no moreexcruciating experience, it is like holidaying at a scenic spot. A visit to ABB, L & T or Smith Kline and Beecham shouldconvince the reader about the transformation that has taken place in the wealth creation system.4.Small has Become BeautifulIt was E.F. Schumacher who, in his famous book Small is Beautiful, opposed giant organisations and increasedspecialisation. He advocated, instead, intermediate technology based on smaller working units, communityownership, and regional workplaces utilising local labour and resources. For him, small was beautiful. Businessmen,all over the world, did not believe in Schumacher’s philosophy. Inspired by economies of scale, industrialists wentIn for huge organisations and mass production systems.1.4 recent trends in production/operations managementRecent trends in production/operations management relate to global competition and the impact it has onmanufacturing firms. Some of the recent trends are :1. Global Market Place : Globalisation of business has compelled many manufacturing firms to have operationsin many countries where they have certain economic advantage. This has resulted in a steep increase in thelevel of competition among manufacturing firms throughout the world.2.Production/Operations Strategy : More and more firms are recognising the importance of production/operations strategy for the overall success of their business and the necessity for relating it to their overallbusiness strategy.3.Total Quality Management (TQM) : TQM approach has been adopted by many firms to achieve customersatisfaction by a never-ending quest for improving the quality of goods and services.4.Flexibility : The ability to adapt quickly to changes in volume of demand, in the product mix demanded, andin product design or in delivery schedules, has become a major competitive strategy and a competitiveadvantage to the firms. This is sometimes called as agile manufacturing.4operations managment & strategic management
5.Time Reduction : Reduction of manufacturing cycle time and speed to market for a new product providecompetitive edge to a firm over other firms. When companies can provide products at the same price andquality, quicker delivery (short lead times) provide one firm competitive edge over the other.6.Technology : Advances in technology have led to a vast array of new products, new processes and newmaterials and components. Automation, computerisation, information and communication technologieshave revolutionised the way companies operate. Technological changes in products and processes canhave great impact on competitiveness and quality, if the advanced technology is carefully integrated intothe existing system.7.Worker Involvement : The recent trend is to assign responsibility for decision making and problem solving tothe lower levels in the organisation. This is known as employee involvement and empowerment. Examples ofworker involvement are quality circles and use of work teams or quality improvement teams.8.Re-engineering : This involves drastic measures or break-through improvements to improve the performanceof a firm. It involves the concept of clean-slate approach or starting from scratch in redesigning the businessprocesses.9. Environmental Issues : Today’s production managers are concerned more and more with pollution control andwaste disposal which are key issues in protection of environment and social responsibility. There is increasingemphasis on reducing waste, recycling waste, using less-toxic chemicals and using biodegradable materialsfor packaging.10. Corporate Downsizing (or Right Sizing) : Downsizing or right sizing has been forced on firms to shed their obesity.This has become necessary due to competition, lowering productivity, need for improved profit and for higherdividend payment to shareholders.11. Supply-Chain Management : Management of supply-chain, from suppliers to final customers reduces the costof transportation, warehousing and distribution throughout the supply chain.12. Lean Production : Production systems have become lean production systems which use minimal amountsof resources to produce a high volume of high quality goods with some variety. These systems use flexiblemanufacturing systems and multi-skilled workforce to have advantages of both mass production and jobproduction (or craft production).operations managment & strategic management5
Operations Management – Introduction6operations managment & strategic management
Study Note - 2Operations planningThis Study Note includes2.1Demand Forecasting2.2Capacity Planning2.3Capacity Reqirement2.4Facility Location2.5Facility Layout2.6Resource Aggregate Planning2.7Material Requirements Planning2.8Manufacturing Resource Planning2.9Enterprise Resource Planning2.10 Economic Batch Quantity2.1 demand forecastingForecastingForecasting means peeping into the future. As future is unknown and is anybody’s guess but the business leadersin the past have evolved certain systematic and scientific methods to know the future by scientific analysis basedon facts and possible consequences. Thus, this systematic method of probing the future is called forecasting. In thisway forecasting of sales refers to an act of making prediction about future sales followed by a detailed analysis offacts related to future situations and forces which may affect the business as a whole.Foresight is not the whole of management, but at least it is an essential part of management and accordingly, toforesee in this context means both to assess the future and make provisions for it, that is forecasting is itself actionalready. Forecasting as a kind of future picture wherein proximate events are outlined with some distinctness, whileremote events appear progressively less distinct and it entails the running of the business as foresee and providemeans to run the business over a definite period.As far as the marketing manager is concerned the sales forecast is an estimate of the amount of unit sales for aspecified future period under the proposed marketing plan or program. It may also be defined as an estimate ofsales in rupees of physical units for a specified future period under a proposed marketing plan or program andunder an assumed set of economic and other force outside the organisation for which the forecast is made.When we consider the function of production and operations management, no doubt Production and Operationdepartments will produce goods as per the sales program given by the sales department, but it has to prepareforecast regarding machine capacity required, materials required and time required for production and so on.This needs the knowledge of what exactly happened in the production shop in previous periods.Making of a proper forecast requires the assessment of both controllable and uncontrollable factors (botheconomic and non economic) inside and outside the organisation.All business and industrial activities revolve around the sale and its future planning. To know what a business will dowe must know its future sales. So, sales forecasting is the most important activity in the business because all otheractivities depend upon the sales of the concern. Sales forecasting as a guiding factor for a firm because it enablesthe firm to concentrate its efforts to produce the required quantities, at the right time at reasonable price and ofthe right quality. Sales forecasting is the basis of planning the various activities i.e.; production activities, pricingpolicies, programme policies and strategies, personnel policies as to recruitment, transfer, promotion, training,wages etc.operations managment & strategic management7
Operations PlanningThe period of forecasting, that is the time range selected for forecasting depends on the purpose for which theforecast is made. The period may vary from one week to some years. Depending upon the period, the forecastcan be termed as ‘Short range forecasting’, medium range forecasting’ and ‘Long range forecasting’. ‘Shortrange forecasting period may be one week, two weeks or a couple of months. Medium range forecasting periodmay vary from 3 to 6 months. Long range forecasting period may vary from one year to any period. The objectiveof above said forecast is naturally different.In general, short term forecasting will be of more useful in production planning. The manager who does short rangeforecast must see that they are very nearer to the accuracy.In long range forecast, the normal period used is generally 5 years. In some cases it may extends to 10 to 15 yearsalso. The purpose of long range forecast is:(i)To work out expected capital expenditure for future developments or to acquire new facilities,(ii)To determine expected cash flow from sales,(iii) To plan for future manpower requirements,(iv) To plan for material requirement,(v) To plan for Research and Development. Here much importance is given to long range growth factor.In case of medium range forecasting the period may extend over to one or two years. The purpose of this type offorecasting is:(i)To determine budgetary control over expenses,(ii)To determine dividend policy,(iii) To find and control maintenance expenses,(iv) To determine schedule of operations,(v) To plan for capacity adjustments.In case of short-term forecast, which extends from few weeks to three or six months and the following purposesare generally served:(i)To estimate the inventory requirement,(ii)To provide transport facilities for finished goods,(iii) To decide work loads for men and machines,(iv) To find the working capital needed,(v) To set-up of production run for the products,(vi) To fix sales quota,(vii) To find the required overtime to meet the delivery promises.Everyone who use the forecast for one purpose or the other expects that they need that forecast should beaccurate. But it is practically impossible to forecast accurately. But decisions are made everyday to run the businessby using the best information available with them. Management scientists have developed various methods forforecasting. One has to decide which method has to be used to suit the information available with him and to suithis needs. The manager, who is concerned with forecasting, must have knowledge of factors influencing forecast.Various factors that influence the forecast are:(i)Environmental changes,(ii)Changes in the preference of the user,(iii) Number of competitive products,(iv) Disposable income of the consumer.8operations managment & strategic management
In forecasting the production important factors to be considered are:(i)Demand from the marketing department,(ii)Rate of labours absenteeism,(iii) Availability of materials,(iv) Available capacity of machines,(v) Maintenance schedules,(vi) Delivery date schedules.Steps in forecastingWhatever may be the method used for forecasting, the following steps are followed in forecasting.(a) Determine the objective of forecast: What for you are making forecast? Is it for predicting the demand? Is it toknow the consumer’s preferences? Is it to study the trend? You have to spell out clearly the use of forecast.(b) Select the period over which the forecast will be made? Is it long-term forecast or medium-term forecast orshort-term forecast? What are your information needs over that period?(c) Select the method you want to use for making the forecast. This method depends on the period selected forthe forecast and the information or data available on hand. It also depends on what you expect from theinformation you get from the forecast. Select appropriate method for making forecast.(d) Gather information to be used in the forecast. The data you use for making forecasting to produce the result,which is of great use to you. The data may be collected by:(i)Primary source: This data we will get from the records of the firm itself.(ii)Secondary source: This is available from outside means, such as published data, magazines, educationalinstitutions etc.(e) Make the forecast: Using the data collected in the selected method of forecasting, the forecast is made.Forecasting Methods:Methods or techniques of sales forecasting: Different authorities on marketing and production have devisedseveral methods or techniques of sales or demand forecasting. The sales forecasts may be result of what marketpeople or buyers say about the product or they may be the result of statistical and quantitative techniques. Themost common methods of sales forecasting are:1.Survey of buyer’s inventions or the user’s expectation method: Under this system of sales forecasting actualusers of the product of the concern are contacted directly and they are asked about their intention to buythe company’s products in an expected given futur
2.8 Manufacturing Resource Planning 37 2.9 Enterprise Resource Planning 38 2.10 Economic Batch Quantity 38 study Note 3 : Designing of operational system and control 3.1 Production Design 45 3.2 Process Design & Selection 48 3.3 Process Planning 48 3.4 Product Life Cycle 50 3.5 Process Selection 51 study