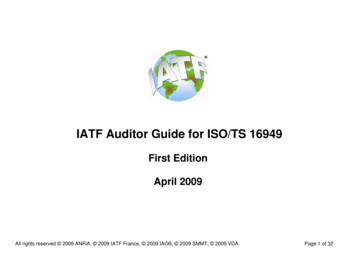
Transcription
IATF Auditor Guide for ISO/TS 16949First EditionApril 2009All rights reserved 2009 ANFIA, 2009 IATF France, 2009 IAOB, 2009 SMMT, 2009 VDA.Page 1 of 32
IntroductionRules for achieving IATF recognition, 3rd Edition for ISO/TS 16949, places the responsibility for the development and maintenance of auditorcompetency upon the certification body which employs the auditor as defined within Rules 3rd Edition clauses 4.2 to 4.5.To assist the certification bodies, the IATF Oversight Offices have authored the IATF Auditor Guide for ISO/TS 16949.PurposeThe purpose of the Guide is to define the logical activities and required auditor competencies in the ISO/TS 16949 audit process. The Guideamplifies the Rules and should be understood in conjunction with Rules.All rights reserved 2009 ANFIA, 2009 IATF France, 2009 IAOB, 2009 SMMT, 2009 VDA.Page 2 of 32
How to Use the CriteriaParagraphs 1 - 8 of the Rules for achieving IATF recognition have been divided into thirty-one activities in the Guide. The Guide has two maincomponents: a graphic representation of the certification audit process and a table that defines competencies for each activity.The GraphicThese 31 audit activities are shown in 33 blue boxes. Under some blue boxes are white text boxes that depict auditor activity during the auditboxes to which they are connected. Large yellow areas group activities into the general areas that they address (e.g., Section 1 - Stage 1Readiness Review, Audit Planning & Section 2 –Site Audit, (Stage 2, Surveillance and Recertification) Nonconformities Management andCertificate Issuance).The TableThe Table headings are: Activity Number – From 1 to 31. Activity Undertaken – the name of the audit activity. References/Document Linkages – the source of the competency requirement. These are related to the boxes to their right in the table,and are not individually linked to specific competencies. Competency – The definition of competency for the Criteria is “the demonstrated ability to apply knowledge and skills.” For eachactivity, therefore, competency is presented as Knowledge – the auditor should be able to demonstrate their knowledge (either from memory or by where to reference) of thematerial presented to the certification body, Skills – the auditor should be able to properly perform these activities during the audit.Some competencies will appear under several activities.The Activities represent the major steps as described in Rules. This is not a definitive list of all of the steps that could be in a process definitionof an audit. The activities shown, however, are required in the audit process definition for ISO/TS 16949.The Competencies are not exhaustive. They were drawn, after several years of IATF experience, from certification body witness audits andoffice assessments, auditor training and evaluation, IATF OEM concern investigation, and responding to questions from all the stakeholders inthe ISO/TS 16949 process. The Competencies, therefore, address areas of known auditor and audit concern; and reflect how the IATFevaluates auditors, audits and certification bodies. Certification bodies are encouraged to use this Guide in developing and maintaining thecompetency of their auditors.All rights reserved 2009 ANFIA, 2009 IATF France, 2009 IAOB, 2009 SMMT, 2009 VDA.Page 3 of 32
Purpose of the Section 3IATF believe further guidance is required both for the certification bodies and their auditors in terms of Essential & General competencies neededto perform an effective automotive process audit.The purpose of Section 3.1 (Essential Auditing Competency Criteria) is to define the competencies required against the six criteria; detailedbelow1.2.3.4.5.6.Process ApproachCustomer Specific RequirementsPrioritizationFocus on PerformanceKnowledge & Application of ISO/TS 16949, Rules 3rd Edition, SI’s and FAQ’s.Analyse & Synthesize dataThe purpose of Section 3.2 (General Auditing Competency Criteria) is to provide guidance on a further seven criteria; detailed below1.2.3.4.5.6.7.Interviewing TechniquesTime ManagementTeam CommunicationConfidentialityConflict ManagementCultural DiversityPolicy DeploymentAll rights reserved 2009 ANFIA, 2009 IATF France, 2009 IAOB, 2009 SMMT, 2009 VDA.Page 4 of 32
All rights reserved 2009 ANFIA, 2009 IATF France, 2009 IAOB, 2009 SMMT, 2009 VDA.Page 5 of 32
Section 1 - Stage 1 Readiness Review & Audit PlanningCompetency is the demonstrated ability to applyknowledge and skillsActivityNo1.2.ActivityUndertakenObtain materials forStage 1 ReadinessReviewKnowledge(able to ) Describe the Rules requirementsrelated to the Stage 1 ReadinessReview.Verify quotationinformation Describe the Rules requirementsrelated to quotation information.o Number of siteso Number of employees (full time,part time, temporary)o Support functionso Language(s) of audito Current certificationso Shift patternso Products and serviceso Product design responsibilityo Proposed scopeo List of customers Explain the audit days calculationrequirements. Describe the effect of non-automotiveproducts and personnel on thequotation and how the audit time isplanned and spent.Skills(able to ) Verify that all of the required documentation hasbeen obtained from the client within the one or twodays of the Readiness Review. Identify missing information not provided by theclient during the Readiness Review. Identify any changes since the quotation andcommunicate to the client and back to thecertification body. Verify the information used for audit daycalculation and resolve any discrepancies.All rights reserved 2009 ANFIA, 2009 IATF France, 2009 IAOB, 2009 SMMT, 2009 VDA.Page 6 of 32
Competency is the demonstrated ability to applyknowledge and skillsActivityNo3.ActivityUndertakenConfirm thatprocesses showingsequence andinteractionincluding keyindicators andperformance trendsfor the previous 12months minimum,have beenidentified 4.Confirm ifsupportingfunctions exist; andwhere applicable,other certificationbody reports areavailable Knowledge(able to )Describe what a process is.Describe how processes interact andhow interactions can be shown withina quality management system.Describe what is meant by theautomotive process approach (Rules)versus an elemental, “departmental”or “functional” approach.Describe what constitutes a risk to thecustomer.Define process effectiveness andefficiency.Describe how key indicators andperformance trends data could bemeasured.Describe how a Letter ofConformance could be applicable forsites with less than 12 monthsperformance data.Define a supporting function on-site orremote.Describe how supporting functionscan be identified within the qualitymanagement system.Describe the Rules requirementsrelated to multiple certification bodies. Skills(able to )Verify the client’s processes, including sequenceand interactions, are defined.Verify that outsourced processes have beenidentified by the client and included within thequality management system.Verify the client has a minimum of previous 12months key indicators and performance trend data.Verify that any on-site or remote support functionshave been identified within the client’s qualitymanual/system.Verify that any other certification body(ies) is/arecurrently IATF recognized.Determine that the reports from other certificationbody(ies) contain the minimum requiredinformation, and that the full supported productscope has been covered in relation to the site.All rights reserved 2009 ANFIA, 2009 IATF France, 2009 IAOB, 2009 SMMT, 2009 VDA.Page 7 of 32
Competency is the demonstrated ability to applyknowledge and skillsActivityNo5.ActivityUndertakenConfirm the clienthas implemented asystem whoseprocesses addressall the requirementsofISO/TS 16949 Knowledge(able to )Describe what a process is.Describe how processes interact andhow interactions can be shown withina quality management system.Describe what is meant by theautomotive process approach (Rules)versus an elemental, “departmental”or “functional” approach.Describe what constitutes a risk to thecustomer.Define process effectiveness andefficiency.Describe how key indicators andperformance trends data could bemeasured.Describe how supporting functionscan be identified within the qualitymanagement system.Describe how the client’s evidence,that their processes meet allrequirements of ISO/TS 16949, couldbe presented (e.g., a matrix). Skills(able to )Verify that the client has presented evidence thattheir system (of processes) addresses all therequirements of ISO/TS 16949.All rights reserved 2009 ANFIA, 2009 IATF France, 2009 IAOB, 2009 SMMT, 2009 VDA.Page 8 of 32
Competency is the demonstrated ability to applyknowledge and skillsActivityNo6.ActivityUndertakenConfirm a qualitymanual is availablefor each site to beaudited Knowledge(able to )Describe the minimum content of aquality manual as defined withinISO/TS 16949.Describe the Rules Stage 1Readiness Review requirements forthe client to have a quality manual. 7.Confirm the clienthas a list ofqualified internalauditors Describe the requirements for internalauditor qualification as defined withinISO/TS 16949 and any applicablecustomer specific requirements. 8.Confirm thecustomer specificrequirements to beincluded in theaudit Describe what a customer specificrequirement is.Describe how the client locatescurrent customer specificrequirements.Describe how the auditor locatescurrent customer specificrequirements. Skills(able to )Verify that each of the client’s sites has a qualitymanual.Verify that interactions with support functions onsite and remote are addressed in the qualitymanual.Verify that the scope defined in the quality manualaccurately matches the client’s automotivebusiness activities and proposed scope ofcertification.Verify that any exclusion identified for certificationis stated in the quality manual.Verify the list of internal auditors.Verify the client’s process for internal auditorqualification addresses quality system,manufacturing process and product audits.Verify that the process based internal audits areundertaken by qualified internal auditors.Verify the client has a defined process for theidentification of customer specific requirements.Determine from the list of customers whichcustomers have customer specific requirements.Verify the client has the current required revisionlevel of customer specific requirements.Captures IATF OEM supplier codes of the clientmanufacturing site where applicable.All rights reserved 2009 ANFIA, 2009 IATF France, 2009 IAOB, 2009 SMMT, 2009 VDA.Page 9 of 32
Competency is the demonstrated ability to applyknowledge and skillsActivityNo9.ActivityUndertakenConfirm customersatisfaction andcomplaint status(customer reports,scorecards, etc.)are available 10.Confirm internalaudits andmanagementreview planningand results from theprevious 12 monthsare available Knowledge(able to )Define the ISO/TS 16949 requirementrelated to customer satisfactionmeasurement.Describe what is meant by customerscorecards.Describe how the auditor locatescustomer scorecards, performancereports, and complaints status.Describe how to relate the customerperformance data back to the problempart(s).Describe the impact of GM NewBusiness Hold, Controlled Shippingand FORD Q1 Revocation on theReadiness decision.Describe the Rules Stage 1Readiness Review requirements(including that the 12 months auditand management review evidencemay be a mix of other standards[ISO, VDA,] and ISO/TS 16949).Define the difference betweensystem, process, and product audits.Describe the difference between aprocess approach and an elemental,“departmental” or “functional”approach for internal audits. Skills(able to )Verify the client has a defined process for theidentification and analysis of customer satisfactionand complaint status information.Determine from the list of customers, whichcustomers issue customer satisfaction andcomplaint status reports.Verify that the client has accessed and reviewedthe current report(s).Verify that customer satisfaction and complaintstatus information, where applicable, isdownloaded from the relevant website during theReadiness Review.Verify that customer objectives / reporting formats(e.g. QOS Quality Operating System) scorecarddata are used.Verify that 12 months internal audit andmanagement review data exists.Verify that a complete cycle of process basedinternal audits of the defined processes arefollowed by a management review.Verify that internal audits are scheduled on thebasis of status and importance.Verify that the management review records includeall required information.All rights reserved 2009 ANFIA, 2009 IATF France, 2009 IAOB, 2009 SMMT, 2009 VDA.Page 10 of 32
Competency is the demonstrated ability to applyknowledge and .Determine theappropriate scopeof certification12.Determine theclient’s readinessKnowledge(able to ) Describe what are the required inputsand outputs as defined within ISO/TS16949 that must be addressed in themanagement review process. Describe what are, and the differencebetween, process performance andproduct conformity. Describe what the applicabilityrequirements for ISO/TS 16949 are. Describe the difference betweenproduct and process designresponsibility. Describe what are permissibleexclusions related to ISO/TS 16949. Describe what an acceptable scope is(including where the client hasautomotive and non-automotiveproducts or a corporate auditscheme). Describe the Rules requirementsrelated to the Stage 1 ReadinessReview. Describe reasons why a client may bedeemed not ready for the Stage 2 siteaudit.Skills(able to ) Verify the scope of certification and wherenecessary communicate to the client why theproposed certification scope is being modified. Analyze the data obtained through activities 2 to11 and determine the client’s readiness for theStage 2 Site Audit.Note: The term “Stage 2 Site Audit” includes theaudit of site and supporting functions on site orremote.All rights reserved 2009 ANFIA, 2009 IATF France, 2009 IAOB, 2009 SMMT, 2009 VDA.Page 11 of 32
Competency is the demonstrated ability to applyknowledge and skillsActivityNo13.ActivityUndertakenPrepare the Stage1 ReadinessReview report 14.Deliver report to theclient regarding theoutcome of theStage 1 ReadinessReview Knowledge(able to )Describe the minimum contentrequirements for Readiness Reviewreport.Describe what is an “area of concern”.Describe that nonconformities maynot be issued at the Stage 1Readiness Review.Describe that advice orrecommendations may not be offered.Describe the Rules requirementsrelated to the Stage 1 ReadinessReview.Describe that advice orrecommendations may not be offered.Describe reasons why a client may bedeemed not ready for the Stage 2 siteaudit.Define the time limitation within theRules between Stage 1 ReadinessReview and Stage 2 Site Audit.Describe that the organizationrequires a new complete Stage 1Readiness Review, if it is judged notready. Skills(able to )Prepare a Stage 1 Readiness Review report thatmeets the minimum report requirements, usingtheir CB report format.Declare the client’s status as regards readiness.Identify, if applicable, all area(s) which arepreventing the client being deemed ready.Identify any areas of concern that could beclassified as a non-conformity during the Stage 2Site Audit.Deliver the report to organization and any auditteam members.Deliver the report without giving advice orrecommendations.All rights reserved 2009 ANFIA, 2009 IATF France, 2009 IAOB, 2009 SMMT, 2009 VDA.Page 12 of 32
Competency is the demonstrated ability to applyknowledge and skillsActivityNo15.15 a.15 b.ActivityUndertakenWrite and issue theAudit Plan(s)includingsupportingfunctions Knowledge(able to )Describe how to create an audit planthat is based upon the definedprocesses of the client, theirsequence and interactions, includingsupporting functions.Describe how the audit plan shall bedeveloped prior to arrival on siteincluding the potential sources ofinput into the plan (specifically withregard surveillance audit planning).Describe the effect of non-automotiveproducts and personnel on thequotation and how the audit time isplanned and spent.Describe Rules requirements for theaudit plan and the audit, includingsupporting functions and multiplecertification bodies.Describe the impact of customerconcerns and or special statuses(notifications related to quality ordelivery issues, e.g. GM newbusiness hold, GM controlledshipping, FORD Q1 revocation, andVolkswagen Qualitätsleistung:C) onthe audit plan. Skills(able to )Create an audit plan that is based upon thedefined processes of the client, their sequence andinteractions, including supporting functions,addressing as applicable the followingo analysis of actual or potential risk to thecustomer, product, and processeso auditor / multiple auditors demonstratinglinkages between audit trailso all shifts, manufacturing activities shall beaudited on all shifts where they occuro the required number of audit dayso optimizing audit time based on the layout ofthe cliento audit of supporting functions planned priorto the audit at the site with process linkagesreferencedo interfaces with the remote support functionsaudited by other certification bodieso audit team competencies and languageskills including the use of translators, wherenecessaryo customer specific requirements and coretools in all relevant processes, includingnew customers since the last audito customer concerns/complaints (reports,scorecards), special status notification andthe client’s responseAll rights reserved 2009 ANFIA, 2009 IATF France, 2009 IAOB, 2009 SMMT, 2009 VDA.Page 13 of 32
Competency is the demonstrated ability to applyknowledge and skillsActivityNo15.15 a.15 b.ActivityUndertaken (Continued) Knowledge(able to )Describe how to determine criticalareas for prioritization based upon riskto the customer, key indicators,performance trends, and criticality ofthe process(es).Describe how to allocate appropriateresources to critical areas of the audit.Describe the Rules requirementsrelated to auditing all shifts.Describe how to communicate theplan(s) to other audit team membersundertaking audits at other sites /supporting functions and the clientrepresentatives. Skills(able to )o internal performance data, internal auditand management review results and actionso progress made towards continualimprovemento effectiveness of the corrective actions andverification since the last audit (time forsuch verification to be additional see Rules5.2 d)o effectiveness of the management systemwith regard to achieving both customer andclient objectives.Issue the audit plan to the client and all audit teammembers.All rights reserved 2009 ANFIA, 2009 IATF France, 2009 IAOB, 2009 SMMT, 2009 VDA.Page 14 of 32
All rights reserved 2009 ANFIA, 2009 IATF France, 2009 IAOB, 2009 SMMT, 2009 VDA.Page 15 of 32
Section 2 - Stage 2 Site Audit, Nonconformities Management, and Certificate IssuanceCompetency is the demonstrated ability to applyknowledge and skillsActivityActivityNoUndertakenConduct audit of16.remote supportingfunctions prior tothe Site AuditConduct opening17.meeting Knowledge(able to )Describe the Rules requirements related toremote supporting functions.See Activities 17 to 22 below.Describe the certification body requirementsrelated to the opening meeting.Describe the impact of new or changedinformation from the client on the audit. Skills(able to )See Activities 17 to 22 below.Clearly communicate to the attendees, interms that are relevant and understandable,the following:o the automotive process approacho the audit plano the CB’s processes that govern theaudit.Reconfirm the following:o number of employees (full time, parttime, temporary)o number of shifts and shift patterno current customerso customer satisfaction and complaintsstatus including customer reports andscorecardso any customer special statuseso supporting functions.Revise the audit plan inline with changes,advised by the client, since the stage 1Readiness Review.Conduct the opening meeting using theirdefined CB process.All rights reserved 2009 ANFIA, 2009 IATF France, 2009 IAOB, 2009 SMMT, 2009 VDA.Page 16 of 32
Competency is the demonstrated ability to applyknowledge and e to ) (Continued)18.Complete facilitytour(if needed) Describe how to confirm the validity of theaudit plan based on the opening meeting andfacility tour. 19.Meeting withTop Management Describe the requirements in ISO/TS 16949 fortop management.Describe which responsibilities of topmanagement under ISO/TS 16949 may be ormay not be delegated.Describe how processes interact and howinteractions can be shown within a qualitymanagement system.Describe what constitutes a risk to thecustomer.Define process effectiveness and efficiency.Describe how key indicators and performancetrends data could be measured. Skills(able to )Identify any changes since the Stage 1 auditand communicate to the client and back to thecertification body.Modify the audit plan based upon theadditional information collected during theopening meeting and facility tour (includinguse of translators, if any).Record and/or retain key observations for useduring the audit.Interview the top management to elicit thefollowing:o their description of the client’s qualitymanagement systemo their description of the client’s qualityobjectiveso their commitment to the effectiveimplementation of this system (e.g.,participation in meetings, setting objectives,linking objectives and plans, reviewingperformance, allocation of resources, etc.)o the key metrics/measures that they use toevaluate client performanceo what information is communicated (both toand from) top management to the cliento the degree of their participation inmanagement reviews, including correctiveand preventive actionAll rights reserved 2009 ANFIA, 2009 IATF France, 2009 IAOB, 2009 SMMT, 2009 VDA.Page 17 of 32
Competency is the demonstrated ability to applyknowledge and e to )(Continued) 20.Audit clientprocesses Describe the Rules requirements related toautomotive process approach auditing.Describe what is meant by the automotiveprocess approach versus an elemental,“departmental” or “functional” approach.Describe how to follow an audit plan and makeadjustments based upon audit trails.Describe how the process approach auditaffects where within the facility the audit takesplace.Define quality system effectiveness andefficiency.Describe how to choose a sufficient number ofexamples (e.g., processes, top management,operating personnel, documents) for a reliableappraisal of implementation.Analyze information and evidence to determinethe extent of fulfilment with certificationrequirements.Describe the minimum requirements to becovered during an examination of the client’sprocesses. Skills(able to )o to what degree they comprehend theircustomer’s requirements, expectations, andevaluations of the client.Record and/or retain key observations for useduring the audit.Demonstrate planning and conducting anaudit using the automotive process approachprinciples, guidelines and tools (e.g. use of“turtles” as a primary tool).Able to audit using the audit plan inconjunction with the client’s definedprocesses, including sequence andinteraction.Audit the client and ensure that the client’sprocess definition accurately describes reality.Audits processes identified in the audit plan inadequate detail and depth to give confidencethat the process(es) is capable of meetingprocess key performance indicators includingcustomer specifics.Use the audit plan to audit the client’sprocesses to ensure customer specificrequirements are identified, addressed, andmaintained within the quality managementsystem.Conduct interviews, etc. with auditees atappropriate locations (where the processoccurs).All rights reserved 2009 ANFIA, 2009 IATF France, 2009 IAOB, 2009 SMMT, 2009 VDA.Page 18 of 32
Competency is the demonstrated ability to applyknowledge and e to ) (Continued)21.Write up findingsand categorisenon-conformities(major / minor) Describe the IATF Rules requirements thatapply to writing nonconformity, including anySIs, FAQs and customer-specificrequirements.Describe that both negative and positivefindings are included based on objectiveevidence.Describe the difference between a major and aminor nonconformity.Describe the impact of a major nonconformityon the audit.Define the Rules definition of Opportunity forImprovement.Describe the Rules regarding the use of OFIwithout recommending solutions.Describe the impact of customer special statusconditions on nonconformity.Describe the certification body templatesrequired for reporting.Describe the maximum time during the audit towrite an audit report. Skills(able to )Record objective evidence, both of conformityand nonconformity with requirements,sufficient for an independent review to agreewith the audit conclusions andrecommendation.Write a nonconformity based upon factualdata, that containo A statement of non-conformityo The requiremento The objective evidenceAppropriately categorize non-conformities, asmajor or minor.Cross-reference nonconformity to both theclient’s quality management system and therelevant clause of ISO/TS 16949.Appropriately categorize opportunities forimprovement.Identifies opportunities without recommendingsolutions.Complete their certification body’s reportingforms as defined by the CB.All rights reserved 2009 ANFIA, 2009 IATF France, 2009 IAOB, 2009 SMMT, 2009 VDA.Page 19 of 32
Competency is the demonstrated ability to applyknowledge and skillsActivityActivityNoUndertakenComplete Annex 522.table or equivalent23.Determine AuditTeamRecommendation 24.25.Prepare draftreportConduct theclosing meetingand deliver thedraft report to theclient Knowledge(able to )Describe how to complete the Table forverification of completeness of the processoriented auditing versus ISO/TS 16949requirements.Describe the possible recommendations.Describe their certification body process fordetermining the audit team recommendation.Describe the Rules requirements on thecertification body process, to review the auditteam recommendation.Describe the acceptable level of qualitymanagement system performance for ISO/TS16949 certification.Describe the minimum content requirementsfor the draft report, including a list of IATFOEM supplier codes of the clientmanufacturing site.Describe their certification body’sprocess/procedure for the closing meeting.Describe the Rules requirements regardingclosure of nonconformities.Describe the certification body’s appealsprocess. Skills(able to )Prepare the Table for verification ofcompleteness of the process oriented auditingversus ISO/TS 16949 requirements for anaudit.Determine, following their certification bodyprocedures, the audit team recommendation.Prepare a draft audit report that meets Rulesminimum content requirements.Declare the audit team recommendationregarding certification.Identify all nonconformities and OFIs.Conduct the closing meeting using theirdefined certification body process.Deliver the draft audit report to the client.Record any findings that the client wishes toappeal.Discuss the closure of corrective actions,including timing (as applicable).Advise the client of the need to schedule afollow up audit (if applicable).All rights reserved 2009 ANFIA, 2009 IATF France, 2009 IAOB, 2009 SMMT, 2009 VDA.Page 20 of 32
Competency is the demonstrated ability to applyknowledge and skillsActivityActivityNoUndertakenIssue final audit26.report 27.Evaluate theclient’s root causeanalysis and verifysystemiccorrective actions 28.Complete followup audit (ifneeded) Knowledge(able to )Describe the minimum content requirementsfor the final audit report, including a list of IATFOEM supplier codes for the clientmanufacturing site.Describe the timing requirements for deliveryof the final audit report to the client.Describe acceptable methods for managementacknowledgment of the final report.Describe “root cause” analysis.Describe “systemic” versus “incident-specific”corrective actions.Describe several problem solving techniquesand processes (e.g., 5 Why, 8D).Define “100% resolved” as it relates to theclient’s response to a nonconformity.Describe the requirements (from the Rules,customers, and from their certification body)for when a follow-up audit is needed.Describe the purpose of a follow-up audit.Describe how to verify the implementation ofsystemic corrective actions. Skills(able to )Prepare and deliver a final audit report thatcomplies with certification body and IATFrequirements.Obtain management’s signature to final auditreport when the report is issued at the finalmeeting.Obtain formal acknowledgment from theclient’s management representative via emailwhere the report has been issuedelectronically.Verify that responses to nonconformitiesissued are based on effective root causeanalysis by the client followed by systemiccorrective action.Verify with objective evidence that thecorrective actions have been taken.Evaluate a client’s corrective action responsefor “100% resolved” when a corrective actionis not yet implemented.Conduct a follow-up audit.Verify with objective evidence and observationthe effective implementation of systemiccorrective actions.All rights reserved 2009 ANFIA, 2009 IATF France, 2009 IAOB, 2009 SMMT, 2009 VDA.Page 21 of 32
Competency is the demonstrated ability to applyknowledge and skillsActivityActivi
Rules for achieving IATF recognition, 3rd Edition for ISO/TS 16949, places the responsibility for the development and maintenance of auditor competency upon the certification body which employs the auditor