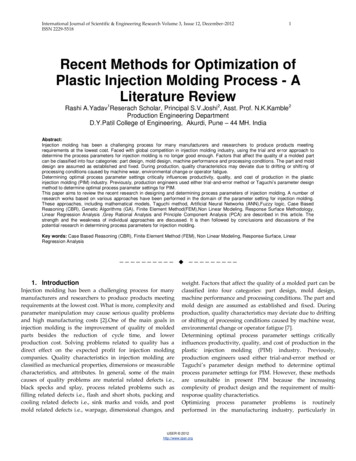
Transcription
International Journal of Scientific & Engineering Research Volume 3, Issue 12, December-2012ISSN 2229-55181Recent Methods for Optimization ofPlastic Injection Molding Process - ALiterature ReviewRashi A.Yadav1Reserach Scholar, Principal S.V.Joshi2, Asst. Prof. N.K.Kamble2Production Engineering DepartmentD.Y.Patil College of Engineering, Akurdi, Pune – 44 MH. IndiaAbstract:Injection molding has been a challenging process for many manufacturers and researchers to produce products meetingrequirements at the lowest cost. Faced with global competition in injection molding industry, using the trial and er ror approach todetermine the process parameters for injection molding is no longer good enough. Factors that affect the quality of a molded partcan be classified into four categories: part design, mold design, machine performance and processing conditions. The part and molddesign are assumed as established and fixed. During production, quality characteristics may deviate due to drifting or shifti ng ofprocessing conditions caused by machine wear, environmental change or operator fatigue.Determining optimal process parameter settings critically influences productivity, quality, and cost of production in the plasticinjection molding (PIM) industry. Previously, production engineers used either trial-and-error method or Taguchi’s parameter designmethod to determine optimal process parameter settings for PIM.This paper aims to review the recent research in designing and determining process parameters of injection molding. A number ofresearch works based on various approaches have been performed in the domain of the parameter setting for injection molding.These approaches, including mathematical models, Taguchi method, Artificial Neural Networks (ANN),Fuzzy logic, Case BasedReasoning (CBR), Genetic Algorithms (GA), Finite Element Method(FEM),Non Linear Modeling, Response Surface Methodology,Linear Regression Analysis ,Grey Rational Analysis and Principle Component Analysis (PCA) are described in this article. Thestrength and the weakness of individual approaches are discussed. It is then followed by conclusions and discussions of thepotential research in determining process parameters for injection molding.Key words: Case Based Reasoning (CBR), Finite Element Method (FEM), Non Linear Modeling, Response Surface, LinearRegression Analysis—————————— —————————1. IntroductionInjection molding has been a challenging process for manymanufacturers and researchers to produce products meetingrequirements at the lowest cost. What is more, complexity andparameter manipulation may cause serious quality problemsand high manufacturing costs [2].One of the main goals ininjection molding is the improvement of quality of moldedparts besides the reduction of cycle time, and lowerproduction cost. Solving problems related to quality has adirect effect on the expected profit for injection moldingcompanies. Quality characteristics in injection molding areclassified as mechanical properties, dimensions or measurablecharacteristics, and attributes. In general, some of the maincauses of quality problems are material related defects i.e.,black specks and splay, process related problems such asfilling related defects i.e., flash and short shots, packing andcooling related defects i.e., sink marks and voids, and postmold related defects i.e., warpage, dimensional changes, andweight. Factors that affect the quality of a molded part can beclassified into four categories: part design, mold design,machine performance and processing conditions. The part andmold design are assumed as established and fixed. Duringproduction, quality characteristics may deviate due to driftingor shifting of processing conditions caused by machine wear,environmental change or operator fatigue [7].Determining optimal process parameter settings criticallyinfluences productivity, quality, and cost of production in theplastic injection molding (PIM) industry. Previously,production engineers used either trial-and-error method orTaguchi’s parameter design method to determine optimalprocess parameter settings for PIM. However, these methodsare unsuitable in present PIM because the increasingcomplexity of product design and the requirement of multiresponse quality characteristics.Optimizing process parameter problems is routinelyperformed in the manufacturing industry, particularly inIJSER 2012http://www.ijser.org
International Journal of Scientific & Engineering Research Volume 3, Issue 12, December-2012ISSN 2229-5518setting final optimal process parameters. Final optimal processparameter setting is recognized as one of the most importantsteps in injection molding for improving the quality of moldedproducts. Previously, engineers used trial-and-error processeswhich depend on the engineers’ experience and intuition todetermine initial process parameter settings. However, thetrial-and-error process is costly and time consuming, thus it isnot suitable for complex manufacturing processes. Faced withglobal competition in injection molding industry, using thetrial-and-error approach to determine the process parametersfor injection molding is no longer good enough.The aim of this article is to review the research of thedetermination of process parameters and mold design forplastic injection molding. Research based on variousapproaches, including Taguchi technique, Artificial NeuralNetworks (ANN), Fuzzy logic, Case Based Reasoning (CBR),Genetic Algorithms (GA), Finite Element Method (FEM), NonLinear Modeling, Response Surface Methodology, LinearRegression Analysis ,Grey Rational Analysis and PrincipleComponent Analysis are discussed.Cause and Effect Diagram for Injection MoldingThe main causes of defect in injection molding can be becauseof mold design, process parameters, machine, operator ormaterial .The details are shown in fish bone diagram.Fig. 1 Cause-and-effect diagram shown in fishbone schematics.There are many factors that influence the quality of molding.Recent methods which have been used successfully for molddesign and process parameter design of injection moldingprocess are discussed below with a retrospective.Fig No: 1 Fishbone DiagramTaguchi’s philosophy is an efficient tool for the design of highquality manufacturing system. Dr. Genichi Taguchi, aJapanese quality management consultant, has developed a2method based on orthogonal array experiments, whichprovides much-reduced variance for the experiment withoptimum setting of process control parameters. Thus theintegration of design of experiments (DOE) with parametricoptimization of process to obtain desired results is achieved inthe Taguchi method. Many experiments must be performedwhen the number of control factors is high. Taguchi methods[5] use a special design of orthogonal arrays to study the entirefactor space with only a small number of experiments. [2] TheTaguchi method attempts to optimize a process or productdesign and is based upon three stages, as follows:1. Concept Design2. Parameter Design3. Tolerance DesignThe concept design is considered to be the first phase of thedesign strategy. This phase gathers the technical knowledgeand experiences to help the designer to select the most suitableproduct. In parameter design, the best setting of the controlfactors is determined. This is the important step, as it does no taffect the unit manufacturing cost of the product. The thirdstep is performed only after completion of the parameterdesign step and is exercised when further improvements arerequired for the optimized design. This phase focuses on thetrade-off between quality and cost. However, designers in thisstage consider only tightening tolerances, upgrading materialstandards and components, if any, having a significant impacton quality through parameter design experiments. TheTaguchi method uses the signal-to-noise (S/N) ratio instead ofthe average to convert the trial result data into a value for thecharacteristic in the optimum setting analysis. The S/N ratioreflects both the average and the variation of the qualitycharacteristic. [2] The standard S/N ratios generally used areas follows: Nominal is best (NB), lower the better (LB) andhigher the better (HB). The optimal setting is the parametercombination, which has the highest S/N ratio. [2] Larger – the– better For larger the better type characteristic S/N ratio iscalculated asS/N ratio (η) -10 log10 (1/nΣ1/yiWhere i 1 to nWhere n number of replications.This is applied for problems where maximization of thequality characteristic of interest is sought. This is referred to asthe larger-the-better type problem.Smaller – the – betterFor smaller the better type characteristic S/N ratio is calculatedasS/N ratio (η) 10 log10 (1/nΣyi2)Where i 1to nThis is termed a smaller-the-better type problem whereminimization of the characteristic is intended.IJSER 2012http://www.ijser.org
International Journal of Scientific & Engineering Research Volume 3, Issue 12, December-2012ISSN 2229-5518Nominal – the – bestFor nominal the best type characteristic S/N ratio is calculatedasS/N ratio (η) -10 log10(μ2/σ2)where μ meanσ standard deviationThis is called a nominal-the-best type of problem where onetries to minimize the mean squared error around a specifictarget value. Adjusting the mean to the target by any methodrenders the problem to a constrained optimization problem.Another major tool used in Taguchi design is orthogonal arrayAn orthogonal array may contain both an inner array (controlarray) and an outer array. The inner array represents controlfactors involving a number of variables under the control ofthe experimenter. Each experimental run of the inner array isreplicated according to the outer array, which is anotherdesign array based upon a certain number of noise variablesfor which the experimenter either cannot control directly orchooses not to control.ApplicationChung-Feng et al. (2006) examined multiple qualityoptimization of the injection molding for Polyether EtherKetone (PEEK). This study looked into the dimensionaldeviation and strength of screws produced by the injectionmolding. This study applied the Taguchi method to cut downon the number of experiments and combined grey relationalanalysis to determine the optimal processing parameters formultiple quality characteristics. The quality characteristics ofthis experiment were the screws outer diameter, tensilestrength and twisting strength. First theprocessing parameters that may affect the injection moldingwere determined with the L18 (21 37) orthogonal, includingmold temperature, pre-plasticity amount, injection pressure,injection speed, screw speed, packing pressure, packing timeand cooling time. Then, the grey relational analysis, whoseresponse table and response graph indicated the optimumprocessing parameters for multiple quality characteristics, wasapplied.This study focused on the PEEK injection molding processusing the Taguchi method and to make the experimental planwith the least number of experiments. However, the Taguchimethod was used for obtaining the optimum processingcombination for a single quality characteristic only, and didnot give any consideration to the relationship betweenmultiple quality characteristics and processing parameters.Therefore, the grey relational analysis wasapplied to improve the drawbacks of the Taguchi method andto achieve the purpose of optimization for multiple qualitycharacteristics. As a result of the optimization of multiplequality characteristics, the dimensional deviation of thescrew’s outer diameter was successfully minimized, and the3tensile strength and twisting strength were maximized in themeantime. In addition, a quality prediction system of thePEEK injection molding was alsoestablished. Through the learning network, the RMSE canconverge to 0.00002. The predicted values and the targetvalues of this prediction system were all within 1.5748 %,which also shows its accuracy. It also means that the controlfactors and their levels as well as the learning parameters ofthe neural network were well planned and effectively chosen.This also reveals the reproducibility and reliability of theexperiment results. The efficiency of this optimization modelhad been successfully proven by experiments and can becompliant with the research purpose of taking active actionsfor waste prevention [4]. Dong Sung Kim et all (2008) hadexperimentally characterized the transcription properties of across microchannelby the injection molding process. The mold insert of the crossmicrochannel in the present injection molding experimentswas fabricated by UV-photolithography and the subsequentnickel electroforming processes. The parametric study of theinjection molding process was carried out by varyingimportant processing parameters of mold temperature,injection speed, packing pressure and melt temperature basedon the Taguchi method to reduce the number of experiments.A transcription measure, relative error for width and height ofthe microchannel, was newly suggested to quantitativelycharacterize the transcription properties. The optimal andworst processing conditions were found in this study from theinvestigations of the injection molded products via a scanningelectron microscope and a noncontact 3D confocal microscope.From the sensitivity analysis, it was identified that the moldtemperature is the most sensitive processing parameter. It wasalso found that the important processing parameter becomesmold temperature, injection speed, packing pressure and melttemperature in the order of sensitivity [3]. Ziegmann et al.(2009) designed and fabricated a special mold In order toobserve the developing duration of microscale weld line during injection molding ,the visualization unitwas integrated in the tool. Considering the limitation of fastfreezing of polymer melt during micro injection molding, avariotherm system (fast heating/cooling system) was alsoarranged in this micro weld line specimen producing tool. Theexperiments were carried out on a horizontal injectionmolding machine.This study determined, for PP material, the relation betweenweld line strength and processing parameters in microinjection molding based on a variothermal mold with visualstructure . The optimal processing parameters and thesignificance order of processing parameters influencing weldline were obtained by Taguchi Analysis. Then throughChebyshev orthogonal polynomial, the four variantsprediction formulation was set up for the micro injectionIJSER 2012http://www.ijser.org
International Journal of Scientific & Engineering Research Volume 3, Issue 12, December-2012ISSN 2229-5518molding weld line. By confirmation experiments it was provedthat prediction errors in the model were lower than21%. Additionally, effects of the V notch profile on weld linestrength were also studied. The results showed that V notchsize in the specimens’ middle part is larger and deeper than inthe edge and the surface height in the middle surface is lowerthan in edge. The smaller V notch area also leads to a strongermicro weld line similar to macro scale case [9]2. Artificial Neural Networks (ANN)Artificial neural networks (ANNs) are defined asmathematical models which represent the biological process ofa human brain. There are three main components in theANNs; neurons or processing elements (PE), interconnections,and learning rules [11]. A neuron is a component thatprocesses data. It receives and processes input signals andcontinually passes its output to the next level neurons. Asingle neuron may have more than one input but only oneoutput. The output of a neuron depends on the input signals,weights of connections, threshold value and activationfunctions. The interconnection is a part of the network whichpropagates signals in a single direction from one neuron to theothers or even to itself. The learning rules govern the changeof the weight matrix in the network. Learning can becategorized into supervised and unsupervised learning.Supervised learning uses the data set that contains inputvectors and corresponding output vectors to train the networkwhile unsupervised learning relies on the local informationand internal control within the network [11]. Artificial neuralnetworks can be of many types like Back propogation neuralnetwork, radial basis neural net work, single layer andmultiple layer networks.Neural networks have been shown to be an effective techniquefor modeling complex nonlinear processes. Since theoperations of neural networks are in a parallel manner, theirprocessing is fast. Neural networks do not require any a prioriassumptions of the function.4optimal setting of the injection molding process of PPcomposite components was developed.This study provided an algorithm that integrates a black-boxmodeling approach (i.e., a RBN predictive model) and a SQPmethod to solve a multi-output constrained optimizationproblem. This algorithm offered an effective and systematicway to identify an optimal setting of the injection moldingprocess.Hence, the efficiency of designing the optimal parameters isgreatly improved. Moreover, the computational loading wastrivial. The total time for training the RBN and finding anoptimal solution was less than 5 minutes with a Pentium 4-M1.7 GHz CPU computer opposed to hours of a trial-and-errormethod for the DOE approach in order to find significantregression models[6].Rawin et al. (1997) presented a neural network-based designsupport tool to help designers to assess the impact of moulddesign on mould manufacturability (or mould complexity)before releasing the drawings to actual production.The proposed system used 14 input vectors (cost drivers) topredict mould complexity in terms of a numerical index (scaleof 1- 10). Quantitative tools for mould complexity assessmenthelp in increasing the efficiency of the product developmentprocess by reducing the number of mould design iterationsmade by the designer. The mould complexity index providedby the neural-net model indicates the degree of difficulty ofmould complexity. It was assumed in this research that thegreater the degree of difficulty the greater would be the mouldmanufacturing cost.However, the association (mapping) between mouldcomplexity and mould manufacturing cost is not alwayslinear.Mould complexity is influenced by several factors, suchas, part geometry, mould materials, parting line, and numberof cavities per mould. In the present study, a new design toolbased on an artificial neural network (ANN) for conductingmould complexity evaluation was proposed [11].3. Finite Element MethodApplicationsThe specimens were prepared under different injectionmolding conditions by varying melting temperatures, injectionspeeds and injection pressures of three computer-controlledprogressive strokes. Minimizing the contour distortions wasthe objective of this study. Sixteen experimental runs based ona Taguchi orthogonal array table were utilized to train theRBN and the SQP method was applied to search for anoptimal solution. In this study, the proposed algorithmyielded a better performance than the design of experiments(DOE) approach. In addition, the analysis of variance(ANOVA) was conducted to identify the significant factors forthe contour distortions of the specimens. A hybrid methodcombining a trained RBN and a SQP method to identify anA variety of specializations under the umbrella of themechanical engineering discipline (such as aeronautical,biomechanical, and automotive industries) commonly useintegrated FEM in design and development of their products.FEM allows detailed visualization of where structures bend ortwist, and indicates the distribution of stresses anddisplacements. FEM software provides a wide range ofsimulation options for controlling the complexity of bothmodeling and analysis of a system. Similarly, the desired levelof accuracy required and associated computational timerequirements can be managed simultaneously to address mosteng
injection molding is the improvement of quality of molded parts besides the reduction of cycle time, and lower production cost. Solving problems related to quality has a direct effect on the expected profit for injection molding companies. Quality