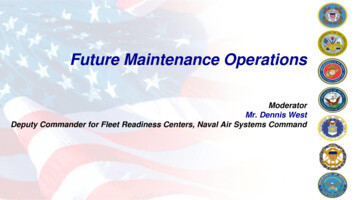
Transcription
Future Maintenance OperationsModeratorMr. Dennis WestDeputy Commander for Fleet Readiness Centers, Naval Air Systems Command
Mr. Dennis WestDeputy Commander for Fleet Readiness Centers, Naval Air Systems CommandRDML Mark WhitneyDeputy Commander, Logistics, Maintenance and Industrial Operations, Naval SeaSystems CommandMr. Mike MaddenExecutive Deputy, Marine Corps Logistics CommandMr. Jeff AllenExecutive Director, Air Force Sustainment Center, Air Force Material CommandMr. Larry MuzzeloDirector, Software Engineering Center, Communications Electronics CommandMs. Tricia UngerDirector of Performance Based Logistics Program, Honeywell Defense & Space
Systems Supported by DOD Maintenance31,900Combat Vehicles886Strategic Missiles239 ships16,900 Aircraft 361,400 tactical vehicles Support equipment Communications/electronics equipment Other systems
What’s it Taking?479 Inter. Maintenance ActivitiesApprox. 584,000 Field Level Maintainers 21 Software Maintenance Activities17 Depot Level ActivitiesApprox. 75,000 Depot Level Personnel1000’s of Private Sector CompaniesApproximately a 75 Billion Enterprise
The Problem Decreasing Readiness Changing Technologies Growing Pressure on Budget Aging Equipment Constant/Growing andShifting Demand Aging Facilities Aging Workforce
Questions We Must AskAre our current sustainment systems effective?Can we continue to afford our sustainment systems?Is this the best way to maintain our weapons systems?Is our commercial industrial base healthy?Is our organic industrial base healthy?
Challenges Technology identification and insertionTechnology development for maintenanceOverall maintenance strategiesSeparately managed maintenance systemsby serviceMaintenance level as a certification vicelocationMaintenance management on a global scalePersonnel training both Civ and militaryDeference to readinessCapability and capacity management acrossservices Common maintenance production systemsEvent based maintenanceCommon training systemsSite competitionTechnology and capability investmentCommon processesDigital threadAdditive manufacturingSoftware maintenance and smart systemsPartnershipsSRM InvestmentsModel based decision makingLogistics automation
Commander, Fleet Readiness CentersCOMFRCCOMFRC Vision 2025November 2014 Presented By: Mr. Dennis West
Current COMFRC Capability MiramarYumaMiramarBFTYumaCH NAVYFOR OFFICIAL USE ONLY9
Optimize Capability & CapacityRedundant/Inflexible CapabilityFocused CapabilityFOR OFFICIAL USE ONLY10
2014 Redundant /Inflexible Capability Site-Based Reactive Workload ManagementLocal Capacity Inefficient (Slow)ManualScheduled Long TermLocal Directed Civilian Level III TrainedMilitary Level II TrainedThree Different Training SystemsLevel of Maintenance is a Place Multiple Financial CorporaMultiple Rates for Same WorkLocal InvestmentsInability to use Workforce Interchangeably Redundant Overhead Excess Rate Burden Different Processes Title Title Title2025 Focused Capability Throughput Driven Workload ManagementGlobal CapacityGlobal MaintenanceManagement Efficient High VelocityAutomated TrackingEvent Based (Short Term)Globally IntegratedWorkforceProficiency Military & Civilian Trained TogetherUse of all sites for trainingOne Training SystemMaintenance is a Level of CertificationsFinancialModel Single Financial CorpusOne Customer RateGlobal InvestmentsFlexible Interchangeable Workforce Singular Services System Lower Rates Common Processes Title Title TitleOptimize Capability& CapacityServicesEngineering LogisticsServicesFOR OFFICIAL USE ONLYRapid, Affordable, Globally Focused OrganizationSlow, Inefficient, stove piped organizationCOMFRC Big Rocks/Threads11
Ops CenterFOR OFFICIAL USE ONLY12
Ops CenterFOR OFFICIAL USE ONLY13
RDML Mark WhitneyDeputy Commander, Logistics, Maintenance andIndustrial OperationsNaval Sea Systems Command14
The Problems and NAVSEA SolutionsADDITIVEMANUFACTURINGUSE FOR SHIPMAINTENANCEDecreasing ReadinessXGrowing Pressureon BudgetXConstant/Growing andShifting DemandChanging TechnologiesXAging EquipmentXAging FacilitiesXAging WorkforceCTDPROGRAMYARDTUBEVIDEOSCVN 78TECHNOLOGIESAND DESIGNFEATURESCBM PROCESSESFUTUREOF PMSTOOLSXXXXXXXXXXXXXXXXXXXXXXX15
Additive Manufacturing Use forShip MaintenanceCurrent Programs“Moonshine” and Rapid Prototyping Labs transform mechanic & engineer needsinto solutions.Primary Uses of AM1. Geometric fit checks2. Rapid PrototypingCurrent Technologies Being UsedFDM, Vat polymerization, Binder Jetting16
CTD Program: Moving from the classroom to the waterfront &Shops, (SME) owned Skills development of workforce The Continuous Training and Development (CTD) Program transforms the way wedevelop workers to a program that emphasizes on-the-job, hands on training, on the deckplate, and or in a structured shop environment using mock-ups. PURPOSE: Accelerate knowledge Transfer – People learn faster by doing;- Tell me I may forget, -Show me I will remember, -Let me do it – I will understand! - Safe to Fail environment, enhancing skill and proficiency.17
Production “CTD” Continuous Training and Development Program Transitions from Periodicity based driven class room training requirements, to individualassessment and needs, with emphasis to hands on learning.Eliminates one shoe fits all lecture based training, targeting individualized Skill/proficiency needs.Practical training with embedded problems and challenges with actual shipboard job examples (useof mock-ups, tools, technical work documents, and material) beginning to end. (job planning thrucertification of work)Basic Skills (Boot Camp) training for new employees, tools, methods, andsafety specific implemented end of CY-2013. 3 to 4 weeks structured hands on basic trade skills training administered prior to assignment ofworking shipboard.Immediate impacts to new employee ability and proficiency when assigned to shipboard crewsexecuting maintenance work, enhancing, accelerating “OJT” development.Special Emphasis/Critical Skills (Nuclear & Non-Nuclear) Utilizing Mock-ups, inside shop to develop higher end Journey level skills.Shipboard “OJT” done by assigning “SME’s” to in process work, providing deck-plate mentoringand reinforcement of shop skills training.18
Yard Tube Videos- Centrally Managed locally streamed across 4 Naval Shipyards. Went live on 3/17/14, includes shipyard geographichubs 400 videos and growing. Four to five minute videos (like you tube) on jobspecific techniques, and processes. Captures tacit knowledge/technique foraccomplishment, used for “JIT” refresher and existingtraining, will be accessible via E-TWDTypes of Videos (Sampling):Safety Confined Space Entry (Tanks/Voids)Arc Flash ProtectionRespirator UsageEnergy Control LO/TOIndustrial Processes: Ball Valve – Disassembly/Clean/InspectJoint Insert Brazing19
Types of Videos (Sampling) Continued:Industrial ProcessesChain Hoist Inspection and OperationLock wiringNDT X-Ray Inspection- Visual and eqpt usageMechanical Joint Make-upEHF Inspection and InstallationTLI - TestingFreeze Seal InstallationsPipe Hangar InstallationHydrostatic Test Stand OperationsPipe CuttingFiber Optic Cable Connector assemblyNuclear Repair Processes3D Laser ScannersHydraulic Valve ActuatorsCleanliness Closures/FME PlugsMulti-Pin Plug Fabrication20
CVN 78 TECHNOLOGIES AND DESIGN FEATURESIntegrated IslandSmaller IslandRe-PositionedAft & OutboardMast withClampAntennaDual BandRadarNew Propulsion/Electric PlantJoint PrecisionAll Electric Aux ServicesApproach andNewZonal ElectricalLandingPropulsionDistribution Flight DeckFootprint“PitStop”AdvancedHeavy UnderwayReplenishmentPlasma Arc WasteDestructionSystemArresting GearAircraft Elevators (3)Stbd SponsonRedesign HangarEnhancedFlight DeckImproved Weapon& Material HandlingBays (2)#4 CatapultUnrestrictedElectromagneticAircraft LaunchingSystem (4)UnderwaterProtectionImproved SurvivabilityEvolved SeaSparrow MissileEnhanced ShipSelf Defense
CBM Processes22
Future of PMS Tools23
Air Force Sustainment CenterKeepwhatI n t‘eme g r i tflyingy - S e r v i cit’se - Ex c e l lwee n c do!e
“Art of the Possible”“Art of the Possible is about reaching beyond today’slimitations to grasp previously unimagined heights ofperformance. It is about challenging each other torecognize opportunities, eliminate constraints,improve processes, and optimize resources toachieve world-record results. It isn’t about workingharder, cutting corners or jeopardizing workplacesafety; but about expanding our visions of what istruly possible and refusing to settle for marginal- Lt Gen Bruce A. Litchfield, AFSC Commanderimprovements”.Integrity - Service - Excellence
Cost-Effective Readiness In the Past: Focus on speed & production throughput Now: Readiness costs are rising– Sustainment costs growing at an unsustainable rate– Costs are driving the size of the force– Force size determines our ability to fly, fight, & win Going Forward: Need to focus on Cost-Effectiveness– I.e., more readiness at Same Cost or same readiness atless costhave two choices:costsand reduce capability ntationplanchange thewayFuturewe do business”developed : orComplexof the- Lt. Gen. Bruce A. Litchfield, Commander, AFSCIntegrity - Service - Excellence
AFSC Cost Effectiveness Focus:The Complex of the Future (CoF) The “Art of the Possible" for future depotoperations Addresses National and USAF studyrecommendations ref: improved sustainment Attacks disconnects between emerging Depot &Supply Chain strategic needs and technologyresearch, development, maturation & insertionactivities (i.e. resource prioritization)Integrity - Service - Excellence
Art of the Possible (AOP)Question:Do You Recognize an Art of thePossible Technology Need WhenYou See It?Integrity - Service - Excellence
AOP 2014Integrity - Service - Excellence
CoF “Attributes” (Requirements)1.100% Data Availability2.100% Parts Availability3.Safe & EnvironmentallyCompliant4.Efficient Depot Operations5.Effective Workforce6.100% Process Control7.Intelligent SustainmentNetwork8.Software SustainmentIntegrity - Service - Excellence
Current Status Represents a 30 year framework for a depot development planning &modernization program for the depot and supply chain enterprise––––Establishes technology insertion & investment priorities across AFSCCollaboration with AFSC, AFRL, AFLCMC, & AFNWCComplex of the Future version 1.2 released 1 Oct 2014CoF 2.0 and execution roadmaps: Summer of 2015 Socializing with USAF stakeholders, industry, and academia Continued collaboration with Flight Line of the Future Complex of the Future– POC: Edward Ayer, AFSC/EN Technical Director, Edward.Ayer@us.af.milSeeking Good Ideas From All Sources to Achieve Cost-Effective ReadinessIntegrity - Service - Excellence
Measurement AndReplication System(MARS) EmbodiesComplex of theFuture Attributes 100% data integration and availability - All data sources are digitalDigital thread connects the process operations100% parts availability compresses production time and improves depot agility100% process control with minimal variance in process output because MARS measures, checks,and calibrates position BEFORE a hole is drilledEfficient depot with accurate scheduling/forecasting - on-time every timeSafe, environmentally compliant, energy efficientEffective workforce - eliminates non-value added labor/material from transfer template process 75% reduction in overall labor 50-75% reduction in span time to replace a componentIntelligent sustainment network uses common tools/processes across ALC repair operationsand can share workload among locations to support surge and back-upAdds flexibility and modularity to the “Art of the Possible” as systems can be configured to aproduct mix and/or upgraded over time using COTS componentsCommonality – All laser tracker guided systems will measure the same regardless of ALCMeasure/GuideMapDrill
“Some” Tools & Resources forImplementing Complex of the FutureEquipment Capital Improvement ProgramAir Logistics Complex Facility Maintenance & RepairIntegrity - Service - ExcellenceIncubatorsPartnershipsSmall Business Innovation Research (SBIR) /Small Business Technology Transfer (STTR) /Rapid Innovation Funding (RIF)AF Life Cycle Mgt Center Program TIONSHARING
Why Complex of the FutureBuild tomorrow’s goals Art-of-the-Possible Cost-Effective Readiness State of the art depots maintaining legacy and cuttingedge aircraft Fostering an environment of USAF, industry, andacademia collaboration Collaboration and innovation are the keys to meeting theCost-Effective sustainment needs of the Air ForceIntegrity - Service - Excellence
Questions?Integrity - Service - Excellence
We are AFSC49Integrity - Service - Excellence
UNCLASSIFIED//FOR PUBLICUNCLASSIFIED//FORPUBLICRELEASERELEASEFuture of Maintenance OperationsNovember 18, 2014Mr. Larry MuzzeloDirector, CECOM Software Engineering IFIED//FOR PUBLIC
UNCLASSIFIED//FOR PUBLIC RELEASEA History of Technological Advancements1997COMMERCIAL1983 DEEP BLUE CELL PHONE2001 3G1984 1980’s MACINTOSH INTERNET2013 SMARTPHONE2010LateFUTURE2007 4G1999 WEARABLE TECH2011 INTERNET OF THINGS SELF HEALINGCOMPUTERS MICRO DATASTORAGE BIG DATA WATSON BLACKBERRY1966 APOLLO 11SPACE COMPUTER1968 ARPANET19781988 GPS SATELLITES SINCGARS2000’s 2005 DIGITIZATIONOF ARMY SOFTWAREDEFINEDRADIOS SENSORS ONUNMANNEDAERIAL SYSTEMS1946 ENIACUNCLASSIFIED//FOR PUBLIC RELEASE2009 CREW DUKEMILITARYFUTURE
UNCLASSIFIED//FOR PUBLIC RELEASEHardware vs Software FixesHardware Fix:One effort one solution.Software Fix:One effort one solution . . . . . times all the items in the field!UNCLASSIFIED//FOR PUBLIC RELEASE
UNCLASSIFIED//FOR PUBLIC RELEASEDepots of Today M(A Shifting of Maintenance re at the crossroadsHWSWFY11FY12FY13FY14FY15FY16Organic Depot Workload TrendHardwareSoftwareAnticipated decrease between FY08-16 6.7M 2.6M Direct Labor Hours 4,100 1,600 Work Years 5,000 2,800 On Board Strength FY01 110M FY08 315M FY15 500MUNCLASSIFIED//FOR PUBLIC RELEASE
UNCLASSIFIED//FOR PUBLIC RELEASEChallengesHARDWARE DEPOT CHALLENGES: Modernization Implications Increasing System Reliability– Order of Magnitude Reduction in Hardware DirectLabor Hours by FY20 for Representative Systems Transformation to Software Intensive SystemsSOFTWARE DEPOT CHALLENGES Mission Continues to Grow Post Production Software Support (PPSS) GrowthDriven by– Software Intensive Nature of Systems– Increasing # of Systems in PPSS 30 New Systems FY15-20 Licenses are a Significant Component of Growth IAVM becoming More Critical to Cyber SecurityUNCLASSIFIED//FOR PUBLIC RELEASE
UNCLASSIFIED//FOR PUBLIC RELEASEStrategic FactorsORGANIC DEPOTOF THE FUTURE55UNCLASSIFIED//FOR PUBLIC RELEASE
2014 DOD MaintenanceSymposiumFuture Maintenance OperationsDiscussion PanelMs. Tricia UngerPBL Program Director, Defense Aftermarket Americas
Honeywell.comFuture Maintenance Operations2014 DoD Maintenance Symposium Theme:Delivering Agile and Affordable Maintenance CapabilityObjectives:1.Support the Warfighter – Ensure System Availability2.Drive affordabilityStrategy:Align Government and Industry Objectives through the Effective use ofPublic Private Partnerships57Document control numberUse or disclosure of data contained on this sheet is subject to the restriction on the title page.Honeywell Confidential
Honeywell.comEffective Public-Private PartnershipsFocus on the “WHAT” versus the “HOW” Identify the Critical Few Sustainment Metrics- Reliability, Availability, Cost Control, Depot Utilization, etc. Drive Work-scope Responsibility to the PPPs- Industry investment in innovation and development at depots- Drive commercial repair practices into Government depots- Encourage Lean / Six Sigma Principles and Practices Provide Industry Partners Appropriate Level of ControlPerformance Work Statements Exceedingly Prescriptive – Driving Costs andLimiting Innovation58Document control numberUse or disclosure of data contained on this sheet is subject to the restriction on the title page.Honeywell Confidential
Honeywell.comEffective Public-Private PartnershipsDrive Accountability for PPP Success at Depots Reduce variation in Partnership maturity and execution between the Service’sdepots Process efficiency's / cost reductions required for industry to offer savings to theGovernment- Incentivize depot operations to implementation of process efficiency and improveperformance- Create a consequence / recourse for depot non-performance Educate depot business teams on the importance of creating value to drivegrowth versus entitlement59Document control numberUse or disclosure of data contained on this sheet is subject to the restriction on the title page.Honeywell Confidential
Honeywell.comEffective Public-Private PartnershipsNurture a Culture of Efficiency Improve visibility of repair, parts usage and cost data for identification ofprocess improvement ideas Establish processes to eliminate onerous bureaucracy for getting ideasapproved and implemented Facilitate rapid adoption into Depot Work Instructions Drive Lean / Six Sigma processes to depot shared resources Expand the use of On-condition Maintenance to drive cost-savings inrepair and replacement practices60Document control numberUse or disclosure of data contained on this sheet is subject to the restriction on the title page.Honeywell Confidential
Honeywell.comEffective Public-Private PartnershipsEliminate Depot Labor Rate Disincentive Depot rate structures and reconciliation to Actuals creates risk for industrypartners- Industry partners absorbing depot-wide operating results in rates- Industry to weigh risks of using Depot in cost-reimbursable PPPs Depot Labor rates, applicable to PPPs, should be limited to the specificGovernment artisans, buildings and resources required to execute under thePartnership Equitable adjustment clauses should be used to account forincreases/decreases NOT caused by industry partners61Document control numberUse or disclosure of data contained on this sheet is subject to the restriction on the title page.Honeywell Confidential
Honeywell.comEffective Public-Private PartnershipsEmbrace Engineering / Technical Changes Eliminate unnecessary hurdles / delays of industry-fundedproduct and process improvements Establish commonality in approach for concurrence andapproval of Class1 & Class 2 Changes- Balance requirement of approvals with the impact to the system- Streamline engineering change control processes to encouragecollaboration between the Depots and Industry62Document control numberUse or disclosure of data contained on this sheet is subject to the restriction on the title page.Honeywell Confidential
Honeywell.comFuture Maintenance OperationsDrive Effectiveness of PPP’s: Focus on the “WHAT” versus the “HOW” Drive Accountability for PPP Success at the Depot Nurture a Culture of Efficiency Eliminate Depot Labor Rate Disincentive Embrace Engineering / Technical Changes63Document control numberUse or disclosure of data contained on this sheet is subject to the restriction on the title page.Honeywell Confidential
Basic Skills (Boot Camp) training for new employees, tools, methods, and safety specific implemented end of CY-2013. 3 to 4 weeks structured hands on basic trade skills training administered prior to assignment of working shipboard. Immediate impacts to new employee