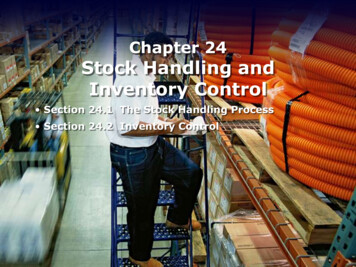
Transcription
Chapter 24Stock Handling andInventory Control Section 24.1 The Stock Handling Process Section 24.2 Inventory Control
The Stock Handling ProcessKey Termsreceivingrecordblind checkmethoddirect checkmethodspot checkmethodquality bjectives Describe the receiving process Explain stock handling techniques used inreceiving deliveriesMarketing Essentials Chapter 24, Section 24.1
The Stock Handling ProcessGraphic OrganizerCopy this flow chart. Use it to identify key steps inthe stock handling process.Marketing Essentials Chapter 24, Section 24.1
Stock HandlingThe steps in stock handling include: Receiving goods Checking them Marking the goods with information Delivering them to a place to be used, stored,or displayed for saleMarketing Essentials Chapter 24, Section 24.1
Receiving StockWhere stock is placed when it is received dependson the type and size of the business. Smallercompanies may just have stock rooms while largerbusinesses can have bigger areas, loading docks,and even warehouses.Marketing Essentials Chapter 24, Section 24.1
Receiving StockreceivingrecordInformationrecorded bybusinesses aboutthe goods theyreceive.A receiving record X is recorded informationabout goods received either manually orelectronically. Information recorded can include: A receiving number Person who received the shipment Name of shipper and carrierMarketing Essentials Chapter 24, Section 24.1
Receiving Stock Place from which the goods were shipped Number of items delivered and condition Shipping charges Department or store that ordered themerchandise Date the shipment was receivedMarketing Essentials Chapter 24, Section 24.1
Checking MerchandiseMerchandise is checked to verify quantity andcondition using these four methods: Blind check Direct check Spot check Quality checkMarketing Essentials Chapter 24, Section 24.1
Checking Merchandiseblind checkmethodThe receiver of adelivery writesthe description ofthe merchandise,counts thequantitiesreceived, andlists them on ablank form ordummy invoice.The blind check method X requires the receiverto write the merchandise description, count thequantities received, and list them on a blank form.It is the most accurate method but can be verytime-consuming.Marketing Essentials Chapter 24, Section 24.1
Checking Merchandisedirect checkmethodThe merchandiseis checkeddirectly againstthe actual invoiceor purchaseorder.With the direct check method X, themerchandise is checked directly against the actualinvoice or purchase order. This procedure is fasterthan the blind check, but errors may not be foundif the invoice is incorrect.Marketing Essentials Chapter 24, Section 24.1
Checking Merchandisespot checkmethodThe receiver of adelivery conductsa check of onecarton in ashipment to seeif the right kindand quantity ofgoods weredelivered.The spot check method X is a random check ofone carton in a shipment. The other cartons areassumed to be in the same condition, and thismethod is often used for products such as cannedgoods and paper products.Marketing Essentials Chapter 24, Section 24.1
Checking Merchandisequality checkmethodThe merchandiseis checked todeterminewhether thequality of goodsreceived matchesthe quality of theproducts, whichwere ordered.The quality check method X is used to inspectthe workmanship and general characteristics of thereceived merchandise. A buyer often performs thischeck. If the goods are damaged, a damage reportis prepared.Marketing Essentials Chapter 24, Section 24.1
Marking MerchandisesourcemarkingThe seller ormanufacturermarks the pricebefore deliveringthe merchandiseto the retailer;the markingoften uses auniversal productcode (UPC).The most common method of marking price is witha Universal Product Code (UPC). UPCs are oftenused for source marking X, a method in whichthe manufacturer or seller marks the price beforedelivering the merchandise to the retailer.Marketing Essentials Chapter 24, Section 24.1
Transferring MerchandiseTransferred merchandise is accompanied by aform describing the: Items Style numbers Colors and sizes Cost and retail pricesMarketing Essentials Chapter 24, Section 24.1
Transferring MerchandiseStock transfers between departments or storesoccur when merchandise is carried by onedepartment or retailer but is needed by another.They can also occur when off-season merchandiseis moved to surplus or discount stores.Marketing Essentials Chapter 24, Section 24.1
SECTION 24.1 REVIEW
SECTION 24.1 REVIEW- click twice to continue -
Inventory ControlKey entorysystemcycle countsstockkeepingunit (SKU)dollar controlunit controlObjectives Describe the process for providing effectiveinventory management Explain the types of inventory control systems Discuss the relationship between customerservice and distributionMarketing Essentials Chapter 24, Section 24.2
Inventory ControlKey Termsinventoryturnoverbasic stock listmodel stocklistnever-out listreal-timeinventorysystemsObjectives Analyze sales information to determineinventory turnover Discuss technology and inventory managementMarketing Essentials Chapter 24, Section 24.2
Inventory ControlGraphic OrganizerCopy this concept map and use it to recordaspects of perpetual and physical inventorysystems.Marketing Essentials Chapter 24, Section 24.2
Inventory ManagementinventoryAll the goodsstored by abusiness beforethey are sold.Inventory X refers to all the goods stored by abusiness before they are sold. It includes: Raw materials and packaging materials Components purchased from suppliers Manufactured sub-assemblies Work in progress and finished goodsMarketing Essentials Chapter 24, Section 24.2
Inventory ManagementinventorymanagementThe process ofbuying andstoring materialsand productswhile controllingcosts forordering,shipping,handling, andstorage.Inventory management X is the process ofbuying and storing these materials and productswhile controlling costs for ordering, shipping,handling, and storage.Marketing Essentials Chapter 24, Section 24.2
just-in-time(JIT) inventorysystemAn inventorysystem thatcontrols the flowof parts andmaterial intoassembly andmanufacturingplants.Distribution, Inventory Management,and Customer ServiceEvery department in today’s business environmentmust be customer oriented.A just-in-time (JIT) inventory system Xcoordinates demand and supply so that suppliersdeliver parts and raw materials just before theyare needed.Marketing Essentials Chapter 24, Section 24.2
Inventory SystemsTwo methods of trackinginventory are the: Perpetual inventory system Physical inventory systemMarketing Essentials Chapter 24, Section 24.2
Perpetual Inventory SystemperpetualinventorysystemAn inventorysystem thattracks thenumber of itemsin inventory on aconstant basis.A perpetual inventory system X tracks thenumber of items in inventory on a constant basis.With this system, a business keeps track of salesas they occur.In a manual system, employees gather paperrecords of sales and enter that information.Marketing Essentials Chapter 24, Section 24.2
Physical Inventory SystemphysicalinventorysystemAn inventorysystem whereevery so often,stock is visuallyinspected oractually countedto determine thequantity onhand.In a physical inventory system X, stock isvisually inspected or counted to determine thequantity on hand. A company uses this system to: Calculate income tax Determine the value of its inventory Identify shortages and plan purchasesMarketing Essentials Chapter 24, Section 24.2
Physical Inventory Systemcycle countsA small portion ofthe inventory isphysically countedeach day bystockkeeping unitsso that the entireinventory isaccounted for on aregular basis.stockkeepingunit (SKU)The most popular method of inventorymanagement is physical inventory. Cyclecounts X allow a business to count a smallportion of the inventory every day to track theentire inventory. A stockkeeping unit (SKU) X,a unit or a group of related items, counts it.A unit or a group ofrelated items in aunit controlinventory system;the smallest unitused in inventorycontrol.Marketing Essentials Chapter 24, Section 24.2
Physical Inventory SystemVisual control is used mainly by smaller businesses.It uses stock cards noting the necessary numberof each displayed item. The difference between thenumber on the card and the actual number ofitems on hand is the amount that needs to bereordered.Marketing Essentials Chapter 24, Section 24.2
Using Both SystemsMost businesses find it effective to use bothsystems because they complement each other.The perpetual system gives an up-to-dateinventory record throughout the year. The physicalsystem gives an accurate count that can becompared to the perpetual records.Marketing Essentials Chapter 24, Section 24.2
Stock ControlStock control involves monitoring stock levels andinvestments including: Dollar versus unit control methods Inventory turnover calculations Three stock lists: model, basic, never-outMarketing Essentials Chapter 24, Section 24.2
Using Both SystemsWhen the physical count shows less merchandisethan is supposed to be in inventory, a stockshortage or shrinkage has occurred, such as: Employee and customer theft Receiving errors Incorrect counting and selling errorsMarketing Essentials Chapter 24, Section 24.2
Using Both SystemsdollarcontrolThe planning andmonitoring of thetotal inventoryinvestment thata businessmakes during astated period oftime.Dollar control X represents the planning andmonitoring of the total inventory investment that abusiness makes during a stated period of time. Ithelps a business determine the cost of goods soldand the amount of gross profit or loss.Marketing Essentials Chapter 24, Section 24.2
Using Both Systemsunit controlThe quantities ofmerchandise thata businesshandles during astated period oftime.Unit control X measures the quantities ofmerchandise that a business handles during astated period of time. It allows purchasingpersonnel to see what brands, sizes, colors, andprice ranges are popular.Marketing Essentials Chapter 24, Section 24.2
Using Both SystemsinventoryturnoverThe number oftimes theaverageinventory hasbeen sold andreplaced in agiven period oftime.Inventory turnover X is the number of times theaverage inventory has been sold and replaced in agiven period of time. It is the most effective wayto measure how well inventory is being managed.Marketing Essentials Chapter 24, Section 24.2
Using Both SystemsThe higher the inventory turnover rate, the moretimes the goods were sold and replaced. Storesthat keep records of the retail value of stockcompute their inventory turnover rates as follows:Net sales (in retail dollars)Average inventory on hand (in retail dollars)Marketing Essentials Chapter 24, Section 24.2
Using Both SystemsWhen only cost information about inventory isavailable, inventory turnover can be calculatedwith this formula:Cost of goods soldAverage inventory on hand (at cost)Marketing Essentials Chapter 24, Section 24.2
Using Both SystemsWhen a store wants to look at the number of itemscarried in relation to the number of items sold, itcalculates its stock turnover rates in units with thisformula:Number of SKUs soldAverage SKUs on handMarketing Essentials Chapter 24, Section 24.2
Using Both SystemsThere are three plans used to monitor differenttypes of goods, staple items, fashionable items,and very popular items. They are: Basic stock list Model stock list Never-out listMarketing Essentials Chapter 24, Section 24.2
Using Both Systemsbasic stocklistA list used forthose stapleitems that shouldalways be instock.A basic stock list X is used for those staple itemsthat should always be in stock. It specifies theminimum amount of merchandise that should beon hand for particular products.Marketing Essentials Chapter 24, Section 24.2
Using Both Systemsmodel stocklistA stock list usedfor fashionablemerchandise.A model stock list X is used for fashionablemerchandise. Goods are classified by generalclasses and style categories. The model stock listidentifies how many of each type of item should bepurchased, but the buyer must select specificmodels.Marketing Essentials Chapter 24, Section 24.2
Using Both Systemsnever-out listAn inventorymonitoring planused for bestselling productsthat make up alarge percentageof sales volume.A never-out list X is used for best-sellingproducts that make up a large percentage of salesvolume. Items are added to or taken off the list astheir popularity fluctuates.Marketing Essentials Chapter 24, Section 24.2
real-timeinventorysystemsAn Internettechnology thatconnectsapplications,data, and usersin real time.The Future of InventoryManagementReal-time inventory systems X involveInternet technology that connectsapplications, data, and users in real time.This lets a company constantly track everyproduct it sells from when it is manufacturedto when a customer receives it.Marketing Essentials Chapter 24, Section 24.2
SECTION 24.2 REVIEW
SECTION 24.2 REVIEW- click twice to continue -
Section 24.1 Successful stock management procedures helpcontrol costs and ensure the continuation ofbusiness operations. The steps in the stockhandling process include receiving goods,checking them, marking the goods withinformation, and delivering them.continued
Section 24.2 Inventory is one of the most costly parts ofoperations for many businesses. Inventorymanagement is the process of buying and storingproducts for sale while controlling costs forordering, shipping, handling, and storage.
DECA performance indicators: Explain the receiving process. Explain the stock-handling techniques used inreceiving deliveries. Resolve problems with incoming shipments. Follow up orders. Demonstrate orderly and systematic behavior.
CHAPTER 24 REVIEW
CHAPTER 24 REVIEW- click twice to continue -
Physical Inventory System The most popular method of inventory management is physical inventory. Cycle counts X allow a business to count a small portion of the inventory every day to track the entire inventory. A stockkeeping unit (SKU) X, a unit or a group of related items, counts it. cycle co