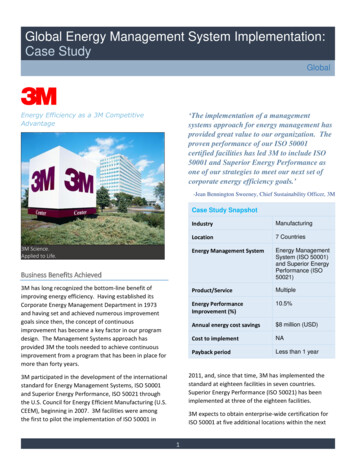
Transcription
Global Energy Management System Implementation:Case StudyGlobalEnergy Efficiency as a 3M CompetitiveAdvantage‘The implementation of a managementsystems approach for energy management hasprovided great value to our organization. Theproven performance of our ISO 50001certified facilities has led 3M to include ISO50001 and Superior Energy Performance asone of our strategies to meet our next set ofcorporate energy efficiency goals.’-Jean Bennington Sweeney, Chief Sustainability Officer, 3MCase Study Snapshot3M Science.Applied to Life.IndustryManufacturingLocation7 CountriesEnergy Management SystemEnergy ManagementSystem (ISO 50001)and Superior EnergyPerformance (ISO50021)Product/ServiceMultipleEnergy PerformanceImprovement (%)10.5%Annual energy cost savings 8 million (USD)Cost to implementNAPayback periodLess than 1 yearBusiness Benefits Achieved3M has long recognized the bottom-line benefit ofimproving energy efficiency. Having established itsCorporate Energy Management Department in 1973and having set and achieved numerous improvementgoals since then, the concept of continuousimprovement has become a key factor in our programdesign. The Management Systems approach hasprovided 3M the tools needed to achieve continuousimprovement from a program that has been in place formore than forty years.2011, and, since that time, 3M has implemented thestandard at eighteen facilities in seven countries.Superior Energy Performance (ISO 50021) has beenimplemented at three of the eighteen facilities.3M participated in the development of the internationalstandard for Energy Management Systems, ISO 50001and Superior Energy Performance, ISO 50021 throughthe U.S. Council for Energy Efficient Manufacturing (U.S.CEEM), beginning in 2007. 3M facilities were amongthe first to pilot the implementation of ISO 50001 in3M expects to obtain enterprise-wide certification forISO 50001 at five additional locations within the next1
Global Energy Management System Implementation: Case StudyGlobalfew months. Each of the five facilities will receiveSuperior Energy Performance Certification as well.Additionally, 3M has locations in Canada, Mexico, andthe U.S. participating in the recently announced NorthAmerican Energy Management pilot, with the objectiveof becoming certified by the end of 2017.Company Profile3MA Global Innovation Company3M is a global innovation company that never stopsinventing. Over the years, our innovations haveimproved daily life for hundreds of millions of people allover the world. We have made driving at night easier,made buildings safer, and made consumer electronicslighter, less energy-intensive and less harmful to theenvironment. We even helped put a man on the moon.Every day at 3M, one idea always leads to the next,igniting momentum to make progress possible aroundthe world.3M’s most recent corporate goal was to improve theenergy efficiency of its global operations by 15%between 2010 and 2015. Each operational facility isexpected to improve its energy performance to help thecorporation achieve the goal. At each location, plantenergy teams are provided management systemsguidelines that lead them to identify and implementenergy saving opportunitiesOur ValuesDuring the most recent five year goal period, 3M globaloperations improved their energy performance by14.1%. Facilities that are participating in ISO 50001 andSuperior Energy Performance are outpacing other 3Mfacilities and have provided energy efficiencyimprovements 60% greater than the 3M average. The resultant energy savings from 3M’s global programover the past five years have shown an energy savingsof 13 Trillion Btu’s and reduced greenhouse gasemissions of 1.9 million metric tons CO2e. 3M facilities participating in ISO 50001 and ISO 50021have shown an energy performance improvement of10.5% over the past three years. This has resulted in700,000 million Btu of energy savings and a reduction of104,000 metric tons of CO2e. The average energy costsavings at each of these facilities was greater than 1million USD.Act with uncompromising honesty and integrity ineverything we do.Satisfy our customers with innovative technologyand superior quality, value and service.Provide our investors an attractive return throughsustainable, global growth.Respect our social and physical environment aroundthe world.Value and develop our employees' diverse talents,initiative and leadership.Earn the admiration of all those associated with 3Mworldwide.Business Case for Energy Management3M recognizes the value of managing energy within ouroperations and is also eager to share with others thebest practices that have been developed. 3M’s energymanagement journey began in 1973 when energysupply and cost concerns were affecting the operationsof companies globally. 3M has maintained a continuouscorporate focus on energy management since 1973 andhas established ambitious energy performanceimprovement goals over the years.‘Implementing ISO 50001 and SuperiorEnergy Performance has provided measurableresults and raised the visibility of the energyprogram at 3M.’-Steve Schultz, Corporate Energy Manager, 3M2
Global Energy Management System Implementation: Case StudyGlobalManaging energy supports 3M’s corporate values. 3Mhas a corporate energy policy stating that we will seekto both promote the efficient use of energy in ouroperations and to deliver products to our customersthat help them save energy. In addition to settingnumerous internal goals for energy performanceimprovement, 3M has helped develop and participatedin voluntary programs to improve energy efficiency suchas the U.S. Environmental Protection Agency EnergyStar program, and numerous U.S. Department ofEnergy programs such as the Better Buildings programwhere we are a Challenge Partner. 3M facilities in manycountries support government initiatives to implementISO 50001 as demonstrated by our partnerships withNatural Resources Canada, the Korean EnergyManagement Agency, and others.EnMS Development and ImplementationHaving had a corporate energy management program inplace for many years, 3M recognized that the project byproject approach to managing energy could beimproved. In 2002, 3M developed a new approachusing concepts from the EPA Energy Star Guidelinesfor Energy Management and the Management Systemfor Energy (MSE 2000) program that had beendeveloped by Georgia Tech. Energy champions andenergy teams were established at each major facilitywith guidance for their roles and responsibilitiesprovided through the corporate energy managementgroup.3M developed an internal program to recognizefacilities that had successfully implemented the newapproach and met corporate goals for improved energyperformance. The concept of being able to offercertification and recognition from a reputable thirdparty led 3M to participate in the development of theISO 50001 and 500021 standards through an industrycollaborative led by the U.S. Department of Energy. 3Mfacilities were among the first to pilot the new programsand 3M continues to include ISO certification as one ofthe strategies to achieve corporate energy goals.Keys to Success Top Management Commitment and CorporateGoals Corporate Level Program Leadership Empowered Energy Leaders at Each Facility Sharing of Best Practices Among FacilitiesThe 3M facilities that are presently certified to ISO50001 and ISO 50021 have improved energyperformance 10.5% over the past three years,exceeding corporate goals. These facilities have saved700,000 million Btu of energy from being used and104,000 metric tons of CO2e from being emitted. Theaverage energy cost savings at each of these facilitieswas greater than 1 million USD.‘ISO 50001 is a standard that drives resultsdirectly to the bottom line. ISO 50001systematically drives down energy costs andimproves competitiveness through theassignment of responsibilities and raising thevisibility of energy management within theorganization.’3M’s Approach to Improving Energy Productivity-Andrew Hejnar, Energy Manager, 3M Canada3
Global Energy Management System Implementation: Case StudyGlobalsupport, sharing of best practices, and highlighting theenergy performance of these facilities throughout thecompany. Through this process of corporate levelenergy review and planning, we have engaged many ofour high priority facilities in the implementation of theISO 50001 Energy Management System.Eighteen 3M facilities are presently certified to ISO50001. At the corporate level, 3M is working to achievea corporate, enterprise-wide certification. A CorporateISO Leadership Committee provides support for thecorporate level ISO program. This top level committeeincludes the Chief Sustainability Officer, the GlobalDirector of Engineering, the directors of manufacturingthat have responsibility for the ISO facilities within 3M,and the corporate energy management group. TheCorporate Energy Manager serves as the managementrepresentative.3M energy performance improvement, ISO/SEP facilities compared toother 3M.3M is organized with five major business groupsoperating over 275 facilities globally. Each facility hasan energy champion identified who has responsibilityfor energy activities. Each facility is held accountablefor improving its energy performance through thepublication of quarterly energy dashboards. Resultsfrom facilities within each business group are totaled tocreate a business group energy dashboard, and thebusiness groups are totaled to create a corporatedashboard. These quarterly reports are provided to theCorporate Operating Committee which includes 3M’sChief Executive Officer and his direct reports. Thisleadership committee provides the direction for energyperformance activities within their business groups.The corporate energy management group tracks energyperformance at each facility, publishes the quarterlyenergy dashboards, provides energy team guidelinesand resources that facilities can use to improveperformance, and coordinates activity among multiplefacilities and internal organizations. The corporategroup also identifies leading technologies andapproaches to energy management and leads theirimplementation across 3M’s global operations.At the corporate level, energy review and planning isdone through the identification of significant energyuses, meaning we have identified the facilities that havethe largest impact on 3M’s corporate goals. We activelyengage those facilities through individual coaching andEighteen 3M facilities in seven countries are presently certified to ISO50001. Nine additional facilities are implementing ISO/SEP.4
Global Energy Management System Implementation: Case StudyGlobalpresent energy performance, and estimate futureenergy use and consumption.Each facility included in the corporate certificate usesan Energy Review and Planning Tool provided by thecorporate energy management group. This toolprovides a common, comprehensive methodology forenergy review and planning. 3M requires that users ofthe tool complete corporately developed training and toreceive certification for its use.The Review and Planning Tool also leads each facilitythrough the process of establishing energy objectives,targets, and action plans. Corporate staff at 3M provideeach facility with guidance and awareness of legal andother requirements to be used along with the site’slocal knowledge to define legal and other requirements.Action plans are developed based on this backgroundand with knowledge of the opportunities that exist forimprovement. Actions are assigned and followed-upduring regular facility energy team meetings and duringfacility level management reviews. Sharing of theseideas across 3M facilities is a definite advantage toimplementing ISO 50001 at the corporate, enterpriselevel.The energy review and planning process is completedannually, or when significant changes occur at thefacility. The 3M corporate office has developed aschedule for each facility in the enterprise to use in theoperation of the Energy Management System.Q1JanuaryCentralOfficeFebruaryQ2MarchAnnual update of tools Review & PlanningTool/Management ReviewExternal Stage I auditsWorkbook, etc.Training on updated toolsprovided to plants.AprilMayExternal stage II auditsor surveillance auditsNew plants to joinenterprisePEPR's take place. PEPRWorkbook and Review& Plannng Tool savedand uploaded toSharePoint.PlantsQ3JulyThe 3M Energy Review and Planning Tool provides a common,comprehensive methodology for each facility to use in the review andplanning process.JuneAugustCentralOfficeInternal auditscompletedPlantsInternal auditscompletedQ4SeptemberOctoberParticipate in PEPR'sas alTop Managementaudits for upcomngReviewyear - Plant, Corporate,DEKRAPEPR's take place.SchedulePEPR Workbook andinternal/externalReview & Plannng Tool audits for upcomngsaved and uploaded to year - Plant, Corporate,SharePoint.DEKRACalendar showing the annual cycle of 3M EnMS activity including theupdate of corporate resources, internal audits, management review, andtop-management reviews.The Energy Review and Planning Tool leads each facilitythrough the process of identifying their current uses ofenergy and evaluating past and present energy use andconsumption. From that process, the facility identifiesthe significant energy uses, the factors affecting the5
Global Energy Management System Implementation: Case StudyGlobalThe corporate manual describes the requirements eachfacility must meet to obtain ISO certification. Thecorporate manual identifies standard operatingprocedures for the operation of the energymanagement system at the corporate level, and yetprovides flexibility for each facility to develop facilitystandard operating procedures to address specificcircumstances.Funding for energy projects is generally provided byeach business group. A Corporate Energy andSustainability Fund has been established to supportenergy projects that can have a significant impact onenergy performance, but do not meet the financialtargets of the individual business groups. As anexample, this fund has provided financing for theinstallation of combined heat and power projects atseveral 3M ISO 50001 certified facilities.The operation of the energy management system at thefacility level is the responsibility of the facility managerand the facility energy champion who serve the role oftop management and management representative atthe facility. Each facility has identified the significantenergy uses within the facility and is meeting ISOrequirements for operational control.Implementing ISO 50001 at our facilities elevated theimportance of managing energy, which provides theenergy champions and energy teams at our facilitiesgreater visibility and recognition from business groupleadership.3M utilized the services of numerous certified andtrained professionals during the implementation of ISOprograms at its facilities. During the first pilotimplementations, professionals from the U.S.Department of Energy and Georgia Tech trained andcoached our facility personnel on the implementationof ISO 50001. Staff from Georgia Tech also providedtraining and coaching to 3M for the implementation ofthe enterprise-wide ISO certification. The CorporateEnergy Manager at 3M, who serves as the managementrepresentative, has been trained and is a CertifiedProfessional in Energy Management Systems and hasreceived certification as a Superior Energy PerformanceVerifier.Non-conformities, corrective actions, and preventiveactions at each facility are tracked using a corporatecorrective and preventive action tracking system. Thissystem provides corporate level visibility to the internaland external audit results and corrective actions beingaddressed at each facility. Repeated and commonfindings will initiate changes and updates to thecorporate Energy Management System.The 3M corporate energy management groupdeveloped extensive resources to support the facilitiespursuing ISO certification. This includes: Corporate Energy ManualCorporate Energy PolicyCorporate Energy Use and Cost Tracking SystemCorporate Energy Project Tracking SystemCorporate Supported Energy Review and PlanningToolCorporate Template for Plant Management ReviewsCorporate Corrective and Preventive ActionTracking SystemMembers of the 3M Naju, South Korea energy team celebrate their ISO50001 and Superior Energy Performance Certification. Assistance wasprovided through the Korean Energy Management Agency6
Global Energy Management System Implementation: Case StudyGlobalEach ISO/SEP facility conducts a facility levelmanagement review bi-annually to ensure that theEnMS is suitable, adequate and effective at meeting thefacility’s goals and objectives. The results of the facilitylevel management review are communicated to thecorporate level management representative forinclusion in the corporate level management review.The role of top management at the corporate level isheld by the Corporate ISO Leadership Committeeconsisting of the Chief Sustainability Officer, the GlobalDirector of Engineering, the directors of manufacturingwith responsibility for the ISO facilities within 3M, andthe corporate energy management group.The energy savings from energy projects implementedmetric demonstrates the value resulting from thecompletion of energy action plans within the facility andprovides a bottom-up validation of the energy use perunit of product metric.The effectiveness of the EnMS is measured using anenergy program effectiveness survey completedannually by each facility energy team and issubstantiated through the supporting ISO certifications.‘Since embarking on our ISO 50001 journeyin Decatur we have seen an 8% reduction inenergy usage. In addition to the savings, thevalue this program brings is in theimplementation of the measurement andmanagement systems that are needed forsustainable year on year improvements. Theenterprise-wide approach has enabled us tolearn from the other participating locationsand to leverage best practices. Implementationdoes take management commitment ofresources, but the payback in the end is wellworth the effort.’3M developed a strategy to incorporate a two tier managementreview process into the operation of the corporate, enterprisewide ISO 50001 Energy Management System.-Robin Higgs, 3M Decatur Site Manager3M measures energy performance utilizing three keyfactors. These factors are included on the energydashboard for each facility and are part of each facility’smanagement review: Measured energy use per unit of product produced Energy savings from energy projects implemented The effectiveness of the EnMSThe energy use per unit of product produced metric isexpected to show a reduction in energy intensity.Several methodologies are used to measure energyintensity including a simple Btu per unit of productcalculation, the EnPI tool developed by the U.S.Department of Energy, and the GT SEnPI Tooldeveloped by Georgia Tech.3M Decatur created cards for employees to carry in theiridentification badge holders to remind them of the energy policyand the significant energy uses the plant has identified.7
Global Energy Management System Implementation: Case StudyGlobalThe cost to implement the ISO 50001 and 500021program was greatly offset by having an alreadyestablished energy management program at eachlocation and by the leadership provided by thecorporate energy management group. The costs toimplement the program are not significant consideringthe savings in energy use, energy cost, and relatedenvironmental impacts achieved.through corporate leadership and with multiple plantsworking as cohorts through our enterprise-widecertification provided significant benefits in terms oftime savings, cost savings, and sharing of best practices.Having leadership within the organization with ISO50001 and 50021 training and experience is a definiteadvantage, as is the ability to call upon outsideresources as needed.The time and resource com
ISO 50001 and 500021 standards through an industry collaborative led by the U.S. Department of Energy. 3M facilities were among the first to pilot the new programs and 3M continues to include ISO certification as one of the strategies to achieve corporate energy goals. The 3M facili