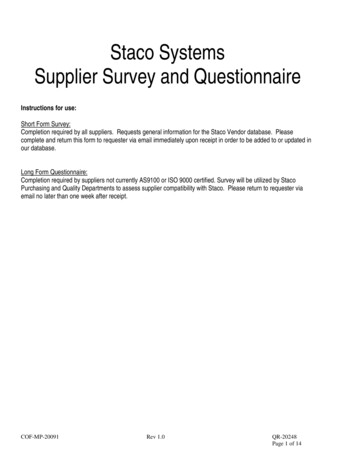
Transcription
Staco SystemsSupplier Survey and QuestionnaireInstructions for use:Short Form Survey:Completion required by all suppliers. Requests general information for the Staco Vendor database. Pleasecomplete and return this form to requester via email immediately upon receipt in order to be added to or updated inour database.Long Form Questionnaire:Completion required by suppliers not currently AS9100 or ISO 9000 certified. Survey will be utilized by StacoPurchasing and Quality Departments to assess supplier compatibility with Staco. Please return to requester viaemail no later than one week after receipt.COF-MP-20091Rev 1.0QR-20248Page 1 of 14
SUPPLIER SURVEY – SHORT FORMAssessment Type:New SupplierIncumbentSupplier’s Company Name:RevalidationPrimary Contact Name:Phone:Supplier’sAddress:Fax:Email:Remit To(if different)Payment Terms:WebsiteFed Tax ID #:(please provide W9)Privately OwnedPublic CorporationMinority OwnedSDV OwnedSmall BusinessWomen Owned Small BusinessAnnual Sales (USD): Subsidiary of or AKA:What Types of services are provided? (Check all that apply & explain if necessary)# of EmployeesPlant SizeDetail:# Years in Business# of LocationsSupplier’s ServicesManufacturerDistributorServiceFacilities & Equipment# of shiftsDescribe Equipment or Attach List:What % of your business is with the aerospace industry?What is your current manufacturing capacity (in percent)?1-10CertificationISO 9001AS9100AS 9120NADCAPOther61-80QUALITY SYSTEM – IF CERTIFIED, PLEASE ATTACH COPY OF CERT.Exp. DateNot Certified, please answer the following:Counterfeit Materials AvoidancePolicy? Yes:No:Conflict Minerals Policy?Yes:No:Y N21-4041-6081-100AS9100 Compliant?Quality Plan?Quality Policy?Risk Management Program?Document Retention?FOD (Foreign Object Debris) Program?Provide CofC (Certificate of Conformance/Compliance)?Are you willing to allow Staco representatives to visit/audit yourmanufacturing site on an on-going basis? YesNoKEY CONTACTSPositionName, E-Mail and Phone#President/GM:Quality Rep.:A/RName of person completing form and certifying accuracy:COF-MP-20091Rev 1.0DateQR-20248Page 2 of 14
Supplier’s Company Name:Supplier Questionnaire – Long FormName of Person Completing form:Phone Number:Email:QUESTIONS AND RESPONSES The questions posed in this survey are intended to reach beyond the essential business requirements of having programsand processes in place to sustain normal business operations. They are designed to ascertaining how well each programand process is implemented and engrained into the supplier’s core methods, techniques, behaviors, and culture. The Staco Systems Survey Questions are patterned after the requirements of AS9100 (current revision) and designed tofocus on a supplier’s operational capability in execution of its quality processes. The questions and corresponding responses are structured by these criteria:1 Point –No systemic approach is evident; information is anecdotal. Little or no deployment is evident. Improvement isachieved through reaction to problems. Individual work areas operate independently. There are no businessresults, trends or comparative information reported.2 Points – The beginning of an effective approach to requirements is evident. The approach is in its early stages ofdeployment in most work areas. Early stages of transition from reaction to problems to a general improvementorientation are evident. A few business results are reported. Little trend or comparative information is reported orit is reported for a few areas of importance.3 Points – An effective systemic approach is evident. The approach is deployed although some areas are in the early stagesof deployment. The beginning of a systemic approach to process evaluation and continuous improvement isevident. Improvements and performance levels are reported in many areas. Early stages of trends andcomparative information are evident.4 Points – The approach is well deployed in all areas. A fact based systemic evaluation and improvement process andsome organizational learning is in place. Business results are reported in most areas. No patterns of adversetrends or poor performance are evident. Early stages of relevant comparisons and benchmarking are evident.5 Points -An effective systemic approach, fully responsive to the requirements is evident. The approach is fully deployedwithout significant gaps or weaknesses. A fact-based evaluation and improvement process is evident throughoutthe organization. The approach is well integrated with the organizational needs and culture. Business results arereported for all areas. Trends, comparisons and benchmarks are reported and analyzed for improvementopportunities. Business processes and results fully address customer and market requirements.COF-MP-20091Rev 1.0QR-20248Page 3 of 14
1. (Quality) Does the supplier have a documented quality manual?1 PointThe supplier does not have a documented quality manual.2 PointsThe supplier quality manual is documented but is not being used by the business operation.3 PointsThe supplier quality manual is used for production activities but does not have provisions for administrativeuse in the office areas.4 PointsProduction and office personnel use the quality manual.5 PointsThe supplier has an established and documented quality management system and continually improves theeffectiveness of the quality system through regular validation with its business processes.Supplier comments2. (Quality) Does the supplier have a risk assessment/risk management program?1 PointThe supplier does not have a risk management plan and does not recognize a need to assess its risks or aneed to determine steps necessary to mitigate any risks.2 PointsThe supplier recognizes a need for a risk management plan but has not yet initiated a process or procedurefor implementing such a plan.3 PointsThe supplier has initiated a process for identifying and assessing its risks. Evidence of Risk Assessmentactivities is visible (e.g. process maps, value stream maps, design trees, etc.) A Risk Management plan isnot available or is in the early stages of development.4 PointsThe supplier has an active process for Risk Assessment and has implemented fundamental steps of a RiskManagement program. Evidence of reactive risk management efforts is visible.5 PointsThe supplier has implemented risk assessment/risk management plans that address both preventative andreactive risk management activities, resulting in risk-informed decision-making. Risk Management appearsto be a culture instilled by and driven from the top levels of decision makers. The supplier’s riskmanagement culture is a continuous improvement culture.Supplier comments:COF-MP-20091Rev 1.0QR-20248Page 4 of 14
3. (Quality) Does the supplier have a robust internal continuous improvement process and is it flowed down to sub-tiersuppliers?1 PointThere is currently no continuous improvement process at supplier.2 PointsSupplier has a continuous improvement process on some customer products but not on all products.3 PointsSupplier and key sub-tier suppliers have a continuous improvement process on all customer products butnot on other products.4 PointsSupplier has continuous improvement processes throughout their business. Continuous improvementinitiatives are flowed down to some key sub-tier suppliers.5 PointsSupplier and key sub-tier suppliers have continuous improvement processes throughout their businesses.Supplier comments4. (Quality) Does the supplier have a current disaster preparedness plan?1 PointSupplier does not have any procedures addressing disaster preparedness.2 PointsA policy statement exists on disaster preparedness. The supplier has an informal disaster plan.3 PointsThe supplier has a documented disaster plan. The plan identifies key individuals, location of keydocuments, and general actions to be taken in case of a disaster.4 PointsThe supplier’s disaster plan identifies how business activities will be carried out in case of a disaster(including the death of any key personnel). Included are plans for contacting customers and maintainingproduction flow.5 PointsThe disaster plan allows for one or more contingencies (variations from the basic plan). The plan providesfor transferring supplier’s technology and work to other facilities if necessary in order to provide continuingcustomer support.Supplier commentsCOF-MP-20091Rev 1.0QR-20248Page 5 of 14
5. (Quality) Does the supplier have a defined environmental, health, and safety program in use?1 PointSupplier’s procedures do not address safety. Unsafe conditions observed in supplier’s facility.2 PointsHazardous conditions (e.g. guards removed from machinery in operation, oil on floor, tripping hazards,blocked exits, safety glasses not worn while operating equipment, etc.) are ignored in the supplier’s facility.Personnel safety is a low priority.3 PointsSupplier has a policy statement addressing safety. Personnel are trained / instructed in safety issues(training records maintained). Hazardous materials are identified, properly stored and disposed of. Supplierhas the MSDS sheets for all chemicals on-site and they are readily available to supplier’s personnel.Supplier has proper handling equipment / protective equipment available and it is in use. Observationshows that personal protective equipment is used (e.g. safety glasses, closed toe shoes). Observationindicates that no piping feeds directly into an open drain, and that there is proper venting of any paintbooths, plating / etching operations, and chemical hoods.4 PointsSupplier’s procedures address environmental and health issues via a policy statement. Supplier hasidentified an individual responsible for overseeing EHS program within its facility. Safety records (accidents)tracked. Visual controls in place relative to safety performance. Personnel are trained/instructed in safety,environmental, and health issues. OSHA 200 log of recordable injuries is available and annual posting isdisplayed and current.5 PointsProcedures address safety in manufacturing process, material handling, and design of work. Proceduresaddress notifying customers if safety matters (e.g. accidents, lost time) will affect product quality or delivery.Supplier utilizes a safety checklist and conducts audits to evaluate environmental, health, and safetyconditions. Supplier is conducting hazard analysis, covering the programs of energy control, machineguarding, powered industrial trucks, cranes, hoists and lifts, radiation, confined spaces, and blood bornepathogens (as applicable to supplier’s site). All applicable regulatory agencies’ permits are in place.Supplier comments6. (Quality) Are records of conformity to requirements and effective implementation of the quality management systemmaintained and readily available when requested by the customer?1 PointThe supplier does not maintain records of conformity to requirements or to its quality management system.2 PointsThe supplier maintains records. Some of the records are not legible and/or do not tie to the qualitymanagement system.3 PointsThe supplier maintains conformity and quality management records but the records are not well organized ormanaged. Some of the records are not legible and/or some records are missing and not readily retrievable.4 PointsThe supplier maintains legible complete conformity and quality management records. The records arelegible, readily identifiable and retrievable.5 PointsProcedures define the controls needed for the identification, storage, protection, retrieval, retention time anddisposition of the records. Records are established and maintained to provide evidence of conformity torequirements and of the effective operation of the quality management system. The records are readilyavailable when requested by the customer.Supplier commentsCOF-MP-20091Rev 1.0QR-20248Page 6 of 14
7.(Quality) Does the supplier have documented Work Instructions for manufacturing of product?1 PointSupplier does not have Work Instructions for manufacturing2 PointsSome informal Work Instructions are available but documentation is not controlled. Key fabrication and assemblyprocesses are not identified.3 PointsSome informal Work Instructions are available and in use but there is no evidence that documentation is controlledor maintained. Key fabrication and assembly processes are identified4 PointsFormal Work Instructions are available for most manufacturing processes and the documents are controlledthrough a formal release system.5 PointsFormal Work Instructions are utilized for all processes. A robust document control system is utilized tomanage documentation which includes a method to ensure that only controlled documents are utilized. WorkInstructions provide detailed fabrication and assembly steps and highlight steps that are critical to correctmanufacture of the product.Supplier comments8. (Ops) Does the supplier have procedures & work instructions that define methods of packaging products for shipmentto its customers that ensures damage will not occur during normal delivery process?1 PointNo formal shipping procedures are evident.2 PointsInformal work instructions are available to generally guide the shipping function. Little or no evidence ofcustomer requirements are evident.3 PointsFormal procedures or work instructions are in use. The instructions cover basic common shipping practicesbut do not address special packaging requirements or carrier selection.4 PointsThe supplier has procedures or work instructions that address basic shipping practices, special packagingand cartage requirements. There is little or no evidence of customer shipment notification or shipmenttracking capability.5 PointsThe supplier follows a documented shipping procedure to meet customer requirements. Shipping containersare designed to adequately protect the customers’ products during transit. The supplier utilizes a formalprocess for managing logistics, including the selection of carriers and the payment of shipping premiums. Itis capable of and supports customer requirements for advanced shipping notices. The supplier providesshipment-tracking services to its customers. The supplier also complies with market requirements forenvironmentally friendly packing and dunnage.Supplier commentsCOF-MP-20091Rev 1.0QR-20248Page 7 of 14
9. (Ops) Does the supplier have documented procedures that provide instructions on how components, assemblies andraw materials are to be handled and stored?1 PointSupplier’s procedures do not address material handling or storage. Material handling is inadequate and placesproduct at risk of handling damage.2 PointsHandling and storage of material appear to be adequate to prevent damage. Aged and environment controlledmaterial storage is available. No procedures exist that define storage and handling controls.3 PointsSupplier’s procedures define how material and products are to be handled and stored throughout themanufacturing process. Supplier’s procedures identify the records to be maintained, the duration of retention, andmethod for disposal of obsolete records. Procedures define the storage and handling of aged and environmentallycontrolled materials.4 PointsSupplier’s procedures define how product is to be stored so that oxidation and contamination are prevented.Procedures define authority for releasing product from storage areas to either production or shipping. Aged andenvironmentally controlled product storage is monitored and validated on a periodic basis.5 PointsThe supplier tracks inventory turns. It has a formal process for ensuring stock rotation and the management ofdate sensitive shelf life components and materials. The supplier has a process for prevention of product damageand preserving product integrity, including correct storage facilities, temperatures and humidity. Non-conformingmaterial is quarantined in controlled areas and not allowed to commingle with other inventory. Purchased productis not consumed or processed until it has been verified as conforming to specified requirements.Supplier comments10. (Quality) Does the supplier assure contamination free, clean products throughout its manufacturing process (FODprogram)?1 PointProcedures do not address product cleanliness.contaminated.2 PointsSupplier assures that completed products are clean both internally and externally from rust, oil, loose powder,metal chips or any other contaminants that may remain from the manufacturing operations. Clean parts arecoated with preservatives and packaged protectively prior to shipment to customers.3 PointsSupplier provides parts that have been subjected to a final cleaning process that is in compliance with therequirements. Parts delivered to customers are clean and free of contamination. Supplier appears to have aFOD program but there is no evidence of management support or compliance activity.4 PointsProduct handling and packaging throughout manufacturing processes is designed to prevent contamination. FODprogram appears active and compliance is encouraged.5 PointsSupplier has cleaning capability in accordance with the requirements. Product cleanliness is routinely verified onall products prior to stocking and prior to delivery to customer as required. The supplier has provisions forcleaning; prevention, detection and removal of foreign objects; special handling for sensitive products; markingand labeling including safety warnings; shelf life control and stock rotation; and special handling for hazardousmaterials.Products seen during manufacturing processes areSupplier commentsCOF-MP-20091Rev 1.0QR-20248Page 8 of 14
11. (Ops) Does the supplier have a formal maintenance program for its manufacturing equipment?1 PointProcedures do not address maintenance of equipment. Corrective maintenance is performed on equipmentonly when failure occurs.2 PointsPreventive maintenance is performed irregularly. Records of corrective and preventative maintenance arenot complete. Equipment is clean and appears to be maintained.3 PointsProcedures define a preventive maintenance program. A preventive maintenance schedule exists and isfollowed. Records reflect that preventative maintenance is performed per schedule and correctivemaintenance is fully documented.4 PointsHistorical maintenance of each piece of equipment is tracked. Machine availability (up time) is measured. ATotal Productive Maintenance (TPM) process has been introduced and is in the early stages ofimplementation.5 PointsMachine capability studies are performed. Visual controls on equipment maintenance are seen throughoutmanufacturing areas. An active fully implemented TPM process is in place to ensure machine availability(up time).Supplier comments12. (Ops) Does the supplier have a formal maintenance program for customer owned tooling/fixtures1 PointProcedures do not address maintenance of customer owned tooling/fixtures. Corrective maintenance isperformed on equipment only when failure occurs.2 PointsPreventive maintenance is performed irregularly. Records of corrective and preventative maintenance arenot complete. Tooling/Fixtures are clean and appear to be maintained.3 PointsProcedures define a preventive maintenance program. A preventive maintenance schedule exists and isfollowed. Records reflect that preventative maintenance is performed per schedule and correctivemaintenance is fully documented.4 PointsHistorical maintenance of each customer owned tooling/fixture is tracked. Machine availability (up time) ismeasured. A Total Productive Maintenance (TPM) process has been introduced and is in the early stages ofimplementation.5 PointsVisual controls on customer owned tooling/fixture maintenance are seen throughout manufacturing areas.An active fully implemented TPM process is in place to ensure that customer owned tooling/fixtures are inacceptable production condition.Supplier commentsCOF-MP-20091Rev 1.0QR-20248Page 9 of 14
13. (Ops) Does the supplier have a defined training program that assesses traini
Supplier Survey and Questionnaire . Instructions for use: Short Form Survey: Completion required by all suppliers. Requests general information for the Staco Vendor database. Please complete and return this form to requester via email immediately upon receipt in order to be added to or updated in our database. Long Form Questionnaire:File Size: 298KB