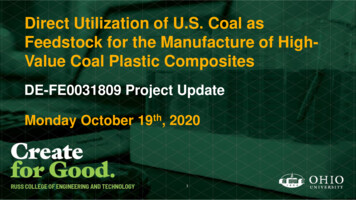
Transcription
Direct Utilization of U.S. Coal asFeedstock for the Manufacture of HighValue Coal Plastic CompositesDE-FE0031809 Project UpdateMonday October 19th, 20201
Disclaimer"This report was prepared as an account of work sponsored by an agency of the UnitedStates Government. Neither the United States Government nor any agency thereof, norany of their employees, makes any warranty, express or implied, or assumes any legalliability or responsibility for the accuracy, completeness, or usefulness of anyinformation, apparatus, product, or process disclosed, or represents that its use wouldnot infringe privately owned rights. Reference herein to any specific commercialproduct, process, or service by trade name, trademark, manufacturer, or otherwise doesnot necessarily constitute or imply its endorsement, recommendation, or favoring bythe United States Government or any agency thereof. The views and opinions of authorsexpressed herein do not necessarily state or reflect those of the United StatesGovernment or any agency thereof."2INSTITUTE FOR SUSTAINABLE ENERGY & THE ENVIRONMENT
Purpose and AlignmentPurpose Develop coal-based composite materialsfor high volume constructionapplications Utilize pulverized coal or waste materialfrom prep plant or settling ponds Initial Applications: Decking, railing, andframingComposite Decking Market U.S. composite market currentlyvalued at over 1 billion annually 12.5% AGR (2015-2020) 1% Market ShareIncrease 50M in AnnualDOE-NETL AdvancedCompositeCoal ProcessingProgramSalesDECKINGTrex Investor Presentation, August 20203INSTITUTE FOR SUSTAINABLE ENERGY & THE ENVIRONMENT
Project Team and SpecificsProject Specifics DOE Project Manager: Anthony Zinn Principal Investigator: Jason Trembly Lead Institution: Ohio University (OHIO) Industry Partners: CONSOL Energy and EngineeredProfiles Consultant: Clear Skies Consulting National Laboratory: Pacific Northwest NationalLaboratoryPeriod of Performance October 1, 2019 to September 30, 20214Project Budget Total: 2,006,578 DOE Share: 1,500,000 Cost Share: 506,678INSTITUTE FOR SUSTAINABLE ENERGY & THE ENVIRONMENT
Project Objectives –– ––––Overall: Develop a coal plastic composite (CPC) formulation which is cost competitiveand meets or exceeds ASTM and IBC specificationsPhase 1Demonstrate continuously manufactured CPC boards meet or exceed ASTM and IBCspecifications for decking applicationsIdentify additional promising decking applications for CPC materials (Railings, posts,etc.)Phase 2Demonstrate CPC board performance in the fieldIdentify CPC material installation methodologiesIdentify additional non-decking applications for CPC formulationsDevelop CPC marketing plan5INSTITUTE FOR SUSTAINABLE ENERGY & THE ENVIRONMENT
Flexural Strength (MPa)Flexural Strength504033384043303.220100370.91.91.3 1.5Flexural Modulus3019 21 222.0 2.1 2.4 2.30% 40% 50% 60% Trex C.D. T.T. Ver. Fib.3.53.02.52.01.51.00.50.0Flexural Modulus (GPa)Initial Technology Status: TRL-4CPCNo.8WPC WPCsCPC/PittCommercialCPC and WPC Flexure PropertiesAl-Majali et al., ACS Sustainable Chem. Eng., 2019, 7, 19, 16870-16878.6INSTITUTE FOR SUSTAINABLE ENERGY & THE ENVIRONMENT
Initial Technology Status: LCA ResultsSpecific energy demand for WPC and CPC Cases. Specific emissions for WPC and CPC Cases.CPC materials require 62% less energy to manufacture and generate 44% less emissions than WPCsIncluding HDPE adds 4800 MJ/tonne and 280 kgCO2/tonneAl-Majali et al., ACS Sustainable Chem. Eng., 2019, 7, 19, 16870-16878.7INSTITUTE FOR SUSTAINABLE ENERGY & THE ENVIRONMENT
CPC/P8OCPCCPC/Bituminous HDPE0.0400.025-0.038 0.021-0.0330.1250.054-0.084 .00.034-0.054WPCsWPCCPC/PRBWPCsTest performed per ASTM D790Bituminous formulations possess greater strength.All CPC formulations meet IBC specifications for decking applications.CPC Safety Factors: 34-468INSTITUTE FOR SUSTAINABLE ENERGY & THE ENVIRONMENTFlexural Modulus (GPa)3481-4275FiberOnOU WPCVerandaTimberTechChoicedekTrexFormulation 3Formulation 2Formulation 1 Stair Deflection (in)2.02.0Fiberon0.94047-46770.0 Floor Deflection .03.521.4WPCs18.7Choicedek W (lbs/ft2)2.33.2Trex2.4PRB/CPC3.64.030.429.7OU WPC2.02.1P8/CPCFormulation 40.918.72.632.0Formulation 31.92.3IBC21.8Spec2.01.521.433.0Formulation 23.6Category3.235302520151050Formulation 12.530.429.7Flexural Strength (MPa)33.0Flexural Modulus (GPa)Bituminous FormulationsPRB Formulations4.055Flexural StrengthInternational BuildingCodeFlexural (IBC)Strength503.5Flexural ModulusFlexural Modulus4539.739.3Specifications 055504540353025201510500% coalFlexural Strength (MPa)Current Project Status: Flexural Properties
77.6 rexFormulation 3Formulation 2Formulation 1Formulation 3Formulation tech23.9Formulation 113012011010090807060504030201000% coalOIT (min)Current Project Status: Oxidation Induction Time (OIT) Higher OIT value indicatesgreater oxidation resistance.Determined using O2-basedisothermal DSC method.Bituminous formulationspossess higher OIT values incomparison to PRB.formulations.Bituminous OIT values greaterthan most commercial WPCs.WPCTests performed according to ASTM D38959INSTITUTE FOR SUSTAINABLE ENERGY & THE ENVIRONMENT
Current Project Status: Oxidation Activation EnergyActivation Energy (kJ/mol)700 CPC/BituminousCPC/PRBTrexTimberTech600500 400 300200100 000.050.10.15 0.2 0.25Conversion (α)0.30.3510Activation energy determinedvia isoconversional analysesin air at multiple ramp rates.Higher activation energyindicates more stablematerial.Results indicate bituminousCPC formulations should havelonger product life thanWPCs.PRB CPC formulations moresusceptible to oxidation.0.4INSTITUTE FOR SUSTAINABLE ENERGY & THE ENVIRONMENT
Current Project Status: Flash/Self Ignition Temperatures (FIT/SIT)500FIT & SIT ( C)400300FIT390360 0400410 350320340320200 100 HDPECPC/BituminousCPC/ ulation 3Formulation 2Formulation 1Formulation 3Formulation 2Formulation 10% coal0FIT: Temperature at whichvolatiles ignite with externalflame.SIT: Temperature at whichmaterial ignites in absence offlame.CPC formulations possesshigher FIT values than WPCs.SIT values similar for CPCsand WPCs.WPCTests performed according to ASTM D129911INSTITUTE FOR SUSTAINABLE ENERGY & THE ENVIRONMENT
Current Project Status: Rate of Burning (RoB)50 32.835.0 35.030.13025.724.7922.12020.1 23.818.617.7 bertechChoicedekTrexFormulation 3Formulation 2Formulation 1Formulation 3Formulation 2Formulation 100% coalBurning Rate (mm/min)40.940Comparable to ASTM E84 forcomposite boards.Lower RoB value indicatesless flammable material.CPC formulations possesssignificantly lower RoBs thanWPC.Bituminous formulation RoBsslightly lower than PRBformulations.WPCTests performed according to ASTM D63512INSTITUTE FOR SUSTAINABLE ENERGY & THE ENVIRONMENT
Current Project Status: TEA/LCA Process simulations developed toaccurately assess material/energybalances for a commercialmanufacturing facility. Sensitivity analyses underway: Capacity, feedstock pricing,formulation, operating costs, etc. Analyses to date indicate 25-40%reduction in operating costs incomparison to WPC manufacturing. Projected manufacturing energy andGHG emissions reductions.EmissionsRaw nCuttingCoolingCompositeProductCoolingWaterSystem BoundaryResources(HDPE, Electricity,Natural Gas)13INSTITUTE FOR SUSTAINABLE ENERGY & THE ENVIRONMENT
Current Project Status: Continuous CPC Manufacturing Continuous manufacturing underwayat Engineered Profiles (Columbus,OH). Materials mixing system procured andinstalled. Extrusion tooling developed andinstalled on commercial extrusion line. Formulation development initiated inJanuary with board manufacturingtrials beginning in July.14INSTITUTE FOR SUSTAINABLE ENERGY & THE ENVIRONMENT
Current Project Status: Board Development Timeline(Jan. ‘20)(Jul. ‘20)(Aug. ‘20)(Sep. ‘20)(Oct. ‘19)15INSTITUTE FOR SUSTAINABLE ENERGY & THE ENVIRONMENT
Market Benefits & Path ForwardMarket Benefits Lower or equivalent priced product with better properties. Utilizes pulverized coal or mining waste materials. Easily translatable manufacturing methodologies.Technology-to-Market Path Results from project will provide blueprint to design, build, and operate acommercial CPC manufacturing facility. Additional market applications and new research areas have beenidentified.16INSTITUTE FOR SUSTAINABLE ENERGY & THE ENVIRONMENT
Next Steps Complete ASTM D7032 testing with CPCboards.– If necessary, refine CPC formulations. Continuously manufacture CPC boards foruse in full-size decks. Perform marketing study. Perform environmental and occupationalhealth studies. Develop and execute scale-up andcommercialization plan.17INSTITUTE FOR SUSTAINABLE ENERGY & THE ENVIRONMENT
Concluding Remarks Analyses indicate CPC formulations have equivalent or superiorproperties in comparison to WPCs for decking applications. TEA and LCA studies indicate attractive manufacturing cost savingsand energy/emissions reductions compared to WPCs. CPC manufacturing has been successfully scaled to a commercialWPC manufacturing line.18INSTITUTE FOR SUSTAINABLE ENERGY & THE ENVIRONMENT
Acknowledgements CONSOL Energy: Mr. Dan ConnellEngineered Profiles: Mr. Vick Dhanapal and Mr. Robert HeigelClear Skies Consulting: Dr. Robert StatnickPNNL: Dr. Keerti Kappagantula and Dr. Madhu SudhanreddyOHIO: Yahya Al-Majali (PhD candidate), Sam Forshey, LoganGutknecht, Dr. Damilola Daramola, Dr. Brian Wisner.19INSTITUTE FOR SUSTAINABLE ENERGY & THE ENVIRONMENT
Contact: trembly@ohio.edu20
INSTITUTE FOR SUSTAINABLE ENERGY & THE ENVIRONMENT Current Project Status: Oxidation Activation Energy 10 Activation energy determined via isoconversional analyses in air at multiple ramp rates. Higher activation energy indicates more stable material. Results indicate bituminous