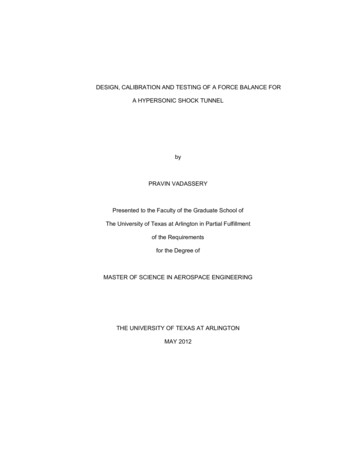
Transcription
DESIGN, CALIBRATION AND TESTING OF A FORCE BALANCE FORA HYPERSONIC SHOCK TUNNELbyPRAVIN VADASSERYPresented to the Faculty of the Graduate School ofThe University of Texas at Arlington in Partial Fulfillmentof the Requirementsfor the Degree ofMASTER OF SCIENCE IN AEROSPACE ENGINEERINGTHE UNIVERSITY OF TEXAS AT ARLINGTONMAY 2012
Copyright by Pravin Vadassery 2012All Rights Reserved
ACKNOWLEDGEMENTSForemost, I am thankful to God for having blessed me throughout my life, without whomnothing is possible. Next thanks go to Dr Frank Lu and Dr Don Wilson for their constant supportand for giving me the opportunity to work at the ARC (Aerodynamics Research Center). Again, Iam thankful to Dr Lu for his determination, enthusiasm and vast knowledge. His words ofencouragement, “Making mistakes is all part of the learning process”, helped me to overcomethe hardships during my research. A special thanks to Eric M Braun for his help, quicksuggestions and for always being around.I acknowledge my fellow team mates in doing an excellent job of reconstructing theUTA Hypersonic Shock Tunnel and getting it back on running condition. Special thanks go toTiago Rolim for his endless support and always assisting me in the times of repair, machiningand discussions. Thanks also to Derek Leamon, Nitesh K Manjunatha, Raheem Bello andDibesh Joshi.I appreciate the work of all the technical staff involved in the Mechanical and AerospaceDepartment. Special credit to Kermit Beird, Sam Williams and Rod Duke for fabrication of allnecessary parts and for sharing their practical knowledge. I sincerely thank everyone in theARC, also for making this place lively and ‘loud’.Finally, I would like to thank my parents, family and friends for their patience and forsupporting me.April 17, 2012iii
ABSTRACTDESIGN, CALIBRATION AND TESTING OF A FORCE BALANCE FORA HYPERSONIC SHOCK TUNNELPravin Vadassery, M.SThe University of Texas at Arlington, 2012Supervising Professor: Frank K. LuThe forces acting on a flight vehicle are critical for determining its performance. Ofparticular interest is the hypersonic regime. Force measurements are much more complex inhypersonic flows, where those speeds are simulated in shock tunnels. A force balance for suchfacilities contains sensitive gages that measure stress waves and ultimately determine thedifferent components of force acting on the model. An external force balance was designed andfabricated for the UTA Hypersonic shock tunnel to measure drag at Mach 10. Static anddynamic calibrations were performed to find the transfer function of the system. Forces wererecovered using a deconvolution procedure. To validate the force balance, experiments wereconducted on a blunt cone. The measured forces were compared to Newtonian theory.iv
TABLE OF CONTENTSACKNOWLEDGEMENTS .iiiABSTRACT . ivLIST OF ILLUSTRATIONS.viiLIST OF TABLES . xChapterPage1. INTRODUCTION . . . 11.1 Literature Survey . 11.2 Force Measurement Techniques . 21.2.1 Internal Force Balance . 31.2.2 External Force Balance . 31.2.3 Strain Gages . 41.2.4 Piezoelectric Film . 41.2.5 Accelerometer . 51.3 Convolution . 51.4 Objective of Research . 72. FACILITY. 82.1 UTA Hypersonic Shock Tunnel at the AerodynamicsResearch Center . 82.2 Reconstruction of the UTA Hypersonic ShockTunnel . 132.3 Diaphragm Test . 133. DESIGN AND EXPERIMENTAL SETUP . 153.1 Force Balance Design . 15v
3.1.1 Finite Element Analysis . 183.1.2 Force Balance Construction . 243.2 Calibration Technique . 293.2.1 Static Calibration . 293.2.2 Dynamic Calibration . 323.3 Shock Tunnel Testing . 424. RESULTS AND DISCUSSION . 434.1 Force Measurement Prediction . 434.1.1 Modified Newtonian Theory . 434.1.2 Coefficient of Drag Calculation usingPitot Pressure . 464.2 Experimental Results . 485. CONCLUSION AND FUTURE WORK . 535.1 Force Balance in the UTA Hypersonic Shock Tunnel . 535.2 Future Work and Recommendations . 55APPENDIXA. LIST OF DESIGN DRAWINGS. 56B. MATLAB PROGRAM FOR FORCE ESTIMATION . 63C. INSTRUMENTATION DETAILS . 67REFERENCES . 70BIOGRAPHICAL INFORMATION . 72vi
LIST OF ILLUSTRATIONSFigurePage1.1 Linear input-output system (a) continuous (b) discrete . 61.2 Convolution in time and frequency domain . 62.1 Schematic of the UTA Hypersonic Shock Tunnel . 92.2 Panorama view of the UTA Hypersonic Shock Tunnel . 92.3 Schematic of the double diaphragm section . 102.4 Photograph of double diaphragm section . 102.5 Steel diaphragms(a) scored diaphragm (b) ruptured diaphragm after test . 143.1 Different preliminary designs . 173.2 Fabricated force balance . 183.3 Generated mesh of the force balance . 193.4 FEA analysis settings . 203.5 Strain concentration in stress bars . 203.6 Simulated input load of 350 N . 213.7 Response to simulated impulse at(a) location1 (b) location2 . 223.8 (a) Simulated step load of 222.4 N (b) step response of location 2 . 223.9 Animated result of stress wave propagation . 233.10 Blunt cone model (a) side view (b) front view . 243.11 Hardened steel bolt hinge . 253.12 Installed model and balance in the test section . 263.13 Attached strain gages . 273.14 Installed model and balance in the test section, front view . 28vii
3.15 Schematic of static calibration procedure . 293.16 Static loading and unloading of force balance . 303.17 Average film output versus hammer force . 323.18 Schematic of a cut weight test . 333.19 Vertical cut weight test . 333.20 Schematic of impulse hammer calibration . 343.21 Raw data of hammer impulse test. 353.22 Sample hammer impulse . 353.23 Check signal for both raw and modified hammer pulse . 363.24 Detail view of check signal with error bar . 373.25 Simulated unit step input . 373.26 Modified hammer signal . 383.27 Enlarged view of the modified hammer pulse . 383.28 Impulse response obtained from FFT and JMECG . 393.29 Power spectral density plot of FRF . 403.30 Enlarged power spectral density plot of FRF for first 12 kHz . 403.31 Enlarged phase spectrum of FRF . 413.32 Spectrogram of the FRF . 414.1 Plot of (a) coefficient of drag (b) coefficient of lift . 454.2 Coefficient of drag from recovered force (condition 1) . 484.3 Recovered drag force and predicted force . 494.4 Raw pitot pressure signal . 494.5 Detailed view of the pitot pressure signal and drag . 504.6 Coefficient of drag from recovered force (condition 2) . 504.7 Recovered drag force . 514.8 Raw pitot pressure signal . 51viii
4.9 Detailed view of the pitot pressure signal . 52A.1 Force balance drawing . 57A.2 Blunt cone model drawing . 58A.3 PCB pressure transducer holder drawing . 59A.4 Hinge joint part 1 drawing . 60A.5 Hinge joint part 2 drawing . 61A.6 Scoring pattern on steel diaphragm drawing . 62C.1 Amplifier circuit diagram for piezoelectric film . 69ix
LIST OF TABLESTablePage2.1 Rupture properties of diaphragm tests . 143.1 Properties of some metals/alloys . 163.2 Static calibration results . 313.3 Test condition . 424.1 Force prediction using modified Newtonian theory condition 1 . 464.2 Force prediction using modified Newtonian theory condition 2 . 464.3 Comparison of experimental to theoretical drag . 52x
CHAPTER 1INTRODUCTIONThe forces acting on a flight vehicle are critical for determining its performance. Ofparticular interest is the hypersonic regime. Research in hypersonics has led to successful testsof scramjet (supersonic combustion ramjet) based vehicles, such as, NASA X-43A. Inhypersonic vehicle design, significance is laid on propulsion system integration, engineperformance, aerodynamics and thrust measurements. Specifically ground-based test facilitieshave limited steady test time thus making force measurement complex in this very shortduration of time.1.1 Literature SurveyHypersonic wind tunnels have been in use since the 1950’s and havedeveloped into different types, namely, continuous and impulse types. Impulse facilities includeshock tubes, reflected shock tunnels and expansion tunnels. The basic principle of theseimpulse facilities is to suddenly release a highly compressed gas in the so-called driver tubethrough rupturing a diaphragm. The sudden release of the compressed gas propagates a shockwave into a so-called driven tube filled with the test gas at low pressure.The shockcompresses and heats the test gas to the desired conditions, after which, it is expelled by anozzle to hypersonic conditions. For example, the T4 free piston shock tunnel at the Universityof Queensland is an impulse-type facility that simulates hypersonic flows [1].1
1.2 Force Measurement TechniqueThroughout this thesis, force measurements refer to techniques for impulsefacilities unless noted otherwise. Force measurement is complicated in impulse facilities due tothe short test duration that will likely prevent the force balance from attaining a steady state.This limitation of short test times in such facilities was overcome by applying the stress waveforce measurement technique (SWFM), proposed by Sanderson and Simmons [2]. Due toimpulsive aerodynamic loading, stress waves that are created, propagate and reflect throughthe model and support structure, which are measured and analyzed by this method. Extensionof this work by Daniel and Mee [3] using finite element modeling led to the design of a threecomponent force balance. The SWFM technique is based on the principle that, when stresswaves travels, no force equilibrium is reached in such a short duration of time so that the strainhistories are the crucial feature for developing force measurement techniques.An investigation into internal and external force balances was undertaken by Robinsonet al. [4] which showed that a higher accuracy of the recovered force and moment loads wasattained using an external force balance. Also, for a blunt body, these authors found that theinteraction of external balance on the model forces was negligible when compared to that of aninternal balance. Some of the recent developments include comparing the experimentalmeasurements with CFD calculations by Boyce and Stumvoll [5], which showed goodagreement for a range of Mach numbers and test gases.On the other hand, accelerometer-based force balance were used by Kulkarni andReddy [6] and Sahoo et al [7], which was a single-component accelerometer force balance. Thedata were in accordance with modified Newtonian theory. Sahoo et al. [8], found that the dragmeasured on a 30 degree semi-apex angle blunt cone model at Mach 5.75 with an acceleratorbased balance agreed closely to the SWFM technique.2
1.2.1 Internal Force BalanceInternal force balances are defined as those that have the measuring instruments likestrain gages, accelerometers placed inside the model. The mounting system (sting) has toadapt depending on the location of the force balance. Models are generally attached to a longsting and placed in the test section of the tunnel. The geometry of the model has toaccommodate the sting. A common way to measure forces is by strain gages. Strain gageswork on the principle that when a load is applied, the stretching or deformation of the gagecauses a change in electrical resistance, details can be found in Section 1.2.3.1.2.2 External Force BalanceExternal balances are those where the measuring instruments are located outside themodel but may be within the test section. The definition of external balances used to berestricted those that are mounted outside the test section, which has been updated to balancesthat are specifically external to the model, but which can be within the test section. The principleof external balances is similar to that of internal balances but the difference is that themeasuring devices are placed on a supporting structure, such as a sting. The forces on themodel are tran
fabricated for the UTA Hypersonic shock tunnel to measure drag at Mach 10. Static and dynamic calibrations were performed to find the transfer function of the system. Forces were recovered using a deconvolution procedure. To validate the force balance, experiments were conducted on a blunt