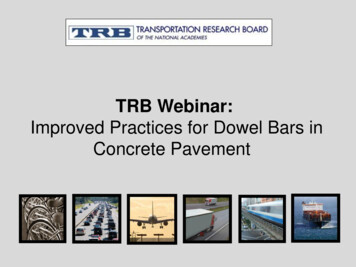
Transcription
TRB Webinar:Improved Practices for Dowel Bars inConcrete Pavement
The Transportation Research Board has met the standards andrequirements of the Registered Continuing Education Providers Program.Credit earned on completion of this program will be reported to RCEPP.A certificate of completion will be issued to each participant. As such, itdoes not include content that may be deemed or construed to be anapproval or endorsement by NCEES or RCEPP.
Learning ObjectivesAt the end of this presentation you will be able to:(1) Recognize improved ways to design dowel bars;(2) Establish acceptable level of misalignment in the field;(3) Predict the performance of alternate dowel bars; and(4) Improve the performance of dowel bar retrofit projects.
TRB Committee AFD50 – Rigid Pavement Design2011 TRB WebinarImproved Practices for Dowel Barsin Concrete PavementFebruary 16, 2011Time: 1:00 PM – 3:00 PM ESTTIME TOPIC1:00 PM Webinar Instructions – Lisa Marflak, Transportation Research Board (TRB)1:05 PMWebinar Overview – Robert Rasmussen, The Transtec Group, Inc. and Dulce RufinoFeldman, California Department of Transportation (Caltrans)National Concrete Consortium (NCC) Recommendations for Standardized Dowel1:10 PM Load Transfer Systems – Maria Masten, Minnesota Department of Transportationand Mark Snyder, Engineering Consultant1:30 PMOptimizing Dowel Bar Design using the DowelCAD Software – Robert Rasmussen,The Transtec Group, Inc.1:45 PMField Trials of Alternate Dowel Bars – James Cable, Cable Concrete Consultation,LLC2:00 PMEffects of Dowel Alignment in Concrete Pavements – Kyle Hoegh, University ofMinnesota2:15 PMDowel Bar Retrofit (DBR) Better Practices – Jeff Uhlmeyer, Washington StateDepartment of Transportation2:30 PM Questions and Answers3:00 PM Adjourn
2011 TRB Webinar-TRB Committee AFD50Improved Practices forDowel Bars in Concrete PavementModerated by:Robert Otto RasmussenThe Transtec Group, Inc.Dulce Rufino FeldmanCaltrans and Chair, TRB AFD50
Why a Webinar on Dowels? Dowel bars. Increase load transfer and extend pavement life Are used in new construction and to retrofit existingpavement In the next 90 minutes, you will hear about. New specifications for dowel systems Improved ways to design dowel bars Acceptable levels of misalignment in the field How to predict performance of alternate dowel bars Better practices for dowel bar retrofit Proven approaches and state-of-the-art practices
Webinar Presentation Outline National Concrete Consortium (NCC)Recommendations for Standardized Dowel LoadTransfer Systems Maria Masten, Minnesota Department of Transportation Mark Snyder, Engineering Consultant Optimizing Dowel Bar Design using the DowelCADSoftware Robert Rasmussen, The Transtec Group, Inc. Field Trials of Alternate Dowel Bars James Cable, Cable Concrete Consultation, LLC Effects of Dowel Alignment in Concrete Pavements Kyle Hoegh, University of Minnesota Dowel Bar Retrofit (DBR) Better Practices Jeff Uhlmeyer, Washington State Department of Transportation
Prepared byMark B. Snyder,Engineering Consultant to CP Tech CenterMaria Masten,Minnesota Department of Transportation
In 2001, MC2 approved a Universal Dowel Basket DetailIn 2009, Several presentations were given at NC2 regardingdowel bars and baskets focusing on how many SHA specifyeverything slightly differentlyTask force was formed to recommend a standardizeddowel basket assembly for possible adoption regionally oreven nationallyStandardization benefits may include: Lower unit cost of the basket assembly Reduce the costs by allowing the manufacturer to minimize set-up Flexibility to shift baskets from one project to another withoutdelay even between states
Slab Thickness .5California1.250 1.250 1.250 1.250 1.250 1.500 1.500 1.500 1.500 1.500 1.500 1.500 1.500 1.500Iowa0.750 0.750 0.750 0.750 1.250 1.250 1.250 1.250 1.500 1.500 1.500 1.500 1.500 1.500Illinois1.000 1.000 1.250 1.250 1.500 1.500 1.500 1.500 1.500 1.500 1.500 1.500 1.500 1.500Indiana1.000 1.000 1.000 1.000 1.000 1.000 1.250 1.250 1.250 1.250 1.250 1.250 1.250 1.500Michigan1.000 1.000 1.000 1.000 1.250 1.250 1.250 1.250 1.250 1.250 1.250 1.500 1.500 1.500Minnesota1.000 1.000 1.250 1.250 1.250 1.250 1.250 1.250 1.250 1.500 1.500 1.500 1.500 1.500MissouriN/AN/A1.250 1.250 1.250 1.250 1.250 1.250 1.250 1.500 1.500 1.500 1.500 1.500North Dakota1.250 1.250 1.250 1.250 1.250 1.250 1.250 1.250 1.250 1.500 1.500 1.500 1.500 1.500Ohio1.000 1.000 1.000 1.000 1.000 1.250 1.250 1.250 1.250 1.500 1.500 1.500 1.500 501.3751.5001.000 1.000 1.250 1.250 1.250 1.250 1.500 1.500 1.500 1.500 1.500 1.500Illustrates recent trend toward largerdowels to reduce bearing stresses andminimize joint faulting and deflections.*Data from 2009 survey of NCC member states
Maria Masten, Minnesota DOTTom Cackler, CP Tech CenterMark Brinkman, Construction Materials Inc.Glenn Eder, WG BlockJenne Imholte-Decker, Simplex Construction SuppliesMark Snyder, ACPA-PennsylvaniaJohn Staton, Michigan DOTMatt Zeller, Concrete Paving Association of MinnesotaTom Nicholson, Dayton SuperiorBrett Trautman, Missouri DOT
Summarizes factors and design theories that should beconsidered in dowel load transfer system designIncludes practical considerations and results of NCC surveysand discussions concerning dowel basket design andfabricationDiscusses alternate dowel materialsPresents recommendations for widespread adoption (i.e.,standardization) Basket wire sizesBasket height as function of dowel diameterDoes NOT recommend dowel diameter for various pavement thicknessesDowel length and spacingAppendices with additional support documentation
LT achieved through both shear and momenttransfer, but moment contribution is small(esp. for joint widths of ¼” or less).Shear capacity of dowel is not critical, but Shear capacity of concrete (cover)? Bearing stress at joint/crack face? Maximum load transferred varies with slabthickness, foundation support, dowel layout,load placement, etc.
l (ECh3/12k(1 – μ2))0.25Typical critical dowel load 3000 lbs
σb Ky0 KPt(2 βz)/4β3EdIdβ (Kd/4EdId)0.25fb f’c(4 – d)/3
Standard typically 18 inches (since 1950s)Based on embedment requirements to match behaviorof Timoshenko 1925 analysis (semi-infinite embeddedbar)A few states successfully use shorter dowels (e.g., 15inches in MN)Shorter embedment lengths are supported by researchdating to 1950s
Teller and Cashell, 1959
Khazanovich et al, 2009
Typically required tobe placed at middepth Maximize concretecover (top and bottom) Dowel load andmoment do notchange significantlywith verticalplacement
Odden et al, 2004
Khazanovich et al, 2009
Many materials/products areavailable
Typical product: AASHTO M254/ASTM 775(green, “flexible”)ASTM 934 (purple/grey, “nonflexible”) hasbeen suggested
Typical product: AASHTO M254/ASTM 775(green, “flexible”)ASTM 934 (purple/grey, “nonflexible”) hasbeen suggested Perception of improved abrasion resistance (butgreen meets same spec requirement) Mancio et al. (2008) found no difference incorrosion protection What is needed: Durability, resistance to damage in transport,handling, service Standardized coating thickness
Most common approachto corrosion preventionsince 1970sLong-term performancehas varied withenvironment, coatingproperties, constructionpractice and otherfactorsPhoto credit: Washington State DOT Sometimes unreliable forlong performance periods.Photo credit: Tom Burnham, MnDOT
Many materials/products areavailable
Many materials are suitable Selection should consider environmental conditions, designrequirements (performance life), cost considerations Structural, behavioral considerations favor continueduse of metallic products no design adjustments needed (dowel diameter, spacing) For LLCP, stainless steel (316L) and zinc-sleeved products offerthe best combination of predictable structural behavior andcorrosion resistance Microcomposite steel is less corrosion-resistant; epoxy coatingmay be appropriate for long-life applications What about FRP dowels (E of FRP is 20% of steel E)?
σb Ky0 KPt(2 βz)/4β3EdIdβ (Kd/4EdId)0.25fb f’c(4 – d)/3
Dowel TypeDiameter(in)Dowel Modulus, E(psi)Applied Shear Force(lb)DowelDeflectionat JointFace 0005,600,0005,600,0001940 (12” spacing)1940 (12” spacing)1940 (12” spacing)1260 (8” spacing)0.00090.00150.00090.0009BearingStress (psi)1421.42185.81405.51419.7There is additional deflection across the joint
Davis and Porter (1998) Similar joint LTE for 1.75-in FRP @ 8 in and 1.5-in steel@ 12 in Melham (1999) 1.5-in FRP performed comparably to 1.0-in steel FHWA TE-30 (IL, WI, IA, etc.) IL (Gawedzinski, 2004): FRP LTE lower and more variable IA (Cable and Porter, 2003): FRP dowel max spacing 8inches; horizontal delamination observed in core. WI (Crovetti, 1999): Significantly reduced LTE for FRPdowels, but no performance differences in short term Larson and Smith (2005): “ low LTEs of FRPdowels in less than 5 years is a serious concern.”Odden et al., Popehn et al., 2003 (U-Mn)
Analytical, lab and field studies1.5-in FRP: higher bearing stress, 95% higherdeflectionsFRP performance OK with good support, closespacing, narrow joints LTE dropped to 50% with poor support (vs. 90% forsteel) LTE dropped from 94% to 72% for 1-in FRP at 6-inspacing after 2M load cycles when joint widthincreased from 0.25 to 0.40 in. Recommended 7.5-in max spacing for 1.5-inFRP, 4-in max spacing for 1.0-in FRP
Min rail wire diameter 0.306 in (1/0 ga.)“U” or “V” loop wires, min diameter 0.243 in(3 ga.), spacing 12 in ( ½ in)Spacer wires 4 (min) for full baskets, 2 (min) for mini-baskets Standard diameter 0.177 in (7 ga.) Standard basket: 11 dowels on 12-in centers(10 ft nominal basket length)Basket coatings at agency discretion*from Draft CP Tech Center Tech Brief
For round, metallic dowels, provide a minimum of 4inches embedment on each side of jointSelect dowel length to include embedmentrequirements and tolerances for placement and jointsawing variability Shorter dowels are possible for retrofit and full-depth repairswhere dowel placement and joint location are known moreprecisely*from Draft CP Tech Center Tech Brief
Not a standard, not tied to pavement thicknessA part of concrete pavement system design Impacts faulting, IRI and other performance measuresthrough resulting bearing stress, differential deflection,deflection energy, etc. Manufacturers of all products should producestandard diameters (to facilitate use of standardbasket sizes)*from Draft CP Tech Center Tech Brief
Dowel Bar Diameter, inHeight to Dowel Center, inIntended Slab Thickness, inDistance Between DowelCenter and Slab Mid-Depth, in 0.752.55–60 – 0.5136–80-11.2548 – 100-11.55 100-?1.756 120-?26 120-?In-range or upsize placements within 1 inchof mid-depthDownsize use placements within 2 inches ofmid-depth (closer to bottom than top)Vertical translation tolerances supported bytesting and experience*from Draft CP Tech Center Tech Brief
Remains least expensive, potentially effective optionOnly effective if durable and applied with sufficientand uniform thickness Consider use of improved epoxy materials 10-mil nominal minimum thickness meets or exceedsrequirements of all surveyed states Would allow individual measures as thin as 8 mils if averageexceeds 10 mils. Probably not necessary to specify upper limit Self-limiting due to manufacturer costs Potential downside is negligible for dowels*from Draft CP Tech Center Tech Brief
316L Stainless Steel products (solid, sleeved, tubes andproperly clad carbon steel) and Zinc-Clad (40-mils)carbon steel appear to be most resistant to steelcorrosion Behavior similar to traditional epoxy-coated steel dowels Other metallic products appear to be more susceptibleto steel corrosion, but may still be useful in someconditions and applications*from Draft CP Tech Center Tech Brief
FRP, GFRP are low-modulus products ( 20% of steel) Straight replacement for steel results in much higher bearingstresses, higher deflections, lower initial LTE values, morerapid loss of LTE under repeated loads Theory is borne out by lab tests and field experience To match deflections and bearing stresses, larger dowelsand/or closer dowel spacings are required Close spacing can induce slab cracking, delamination at joint Long-term ( 15 years) performance of pavements with FRPdowels has not been established.Use of FRP/GFRP dowelsshould be approached with great caution!*from Draft CP Tech Center Tech Brief
Optimizing Dowel Bar DesignusingDowelCAD 2.0Robert Otto Rasmussen, PhD, INCE, PE (TX)Vice President & Chief Engineer, The Transtec Group, Inc.robotto@TheTranstecGroup.com
What is DowelCAD? It’s free software! It’s an interactive detail drawing It predicts concrete pavement behaviorusing different dowel size and spacings
What can DowelCAD do for me? Cut the initial cost of concrete pavementswithout compromising performance Show how concrete can be used on lowervolume roads, with dowels engineered tomeet the demand
What can DowelCAD predict? Dowel size and its effect on performance– Smaller dowels– Elliptical dowels Dowel spacing and its effect onperformance:– Move the corner dowel in– Leave out dowels from the center lane– Specify non-uniform dowel spacings
Dowel Sizing DowelCAD predicts critical responses:– Load transfer efficiency– Dowel-concrete bearing stress As a function of:– Slab properties– Dowel properties– Loading and slab support
DowelCAD – Dowel Sizing
Dowel Design Guidelines
Dowel Spacing DowelCAD predicts critical responses:– Slab stress– Slab deflections– Dowel-concrete bearing stress As a function of:– Slab properties– Dowel properties– Dowel configuration
Analysis Peak responses at slab edge Peak responses at slab corner Peak dowel bearing stressBearingStressEdgeDeflectionEdge StressCornerDeflection
DowelCAD – Dowel Spacing
AnalysisSlab Thickness / Dowel Designs 7 in. (178 mm) Thickness 1-in. (25-mm) Round Dowel9 in. (229 mm) Thickness1¼-in. (32-mm) Round Dowel14 in. (356 mm) Thickness1½-in. (38-mm) Round Dowel7 in. (178 mm) ThicknessSmall Elliptical Dowel (1.41/0.88 in. – 36/22 mm)9 in. (229 mm) ThicknessMedium Elliptical Dowel (1.66/1.13 in. – 42/29 mm)14 in. (356 mm) ThicknessLarge Elliptical Dowel (1.98/1.34 in. – 50/34 mm)
Corner Dowel SpacingCorner DowelSpacing
Corner Dowel SpacingWhat can we conclude: No significant change in slab stresses orcorner deflection Increase in bearing stress at thedowel-concrete interface– Greatest for thick slabs – up to 32%
Corner Dowel SpacingWhat can we do: Decrease dowel bearing stress using:– Elliptical dowels (vs. round dowels)– Larger dowels Can also mitigate through:– Keeping loads away from slab edge(widened lane)– Nominal increase in concrete strength Recognize there is already an existingfactor of safety!
Centerline Dowels
Centerline DowelsWhat can we conclude: Little effect at the corner Increases in edge stress and deflection– Especially for thinner slabs– Up to 16% higher stresses– Up to 10% higher edge deflection Increase in the bearing stress at thedowel-concrete interface– Up to 16% for thicker slabs
Centerline DowelsWhat can we do: Leave out 2 centerline dowels– 5% change in slab responses– Save over 15% on steel! Higher stresses can be mitigated– Small increase in concrete strength– Small increase in slab thickness (often ½”)
Alternate Dowel Spacings
Alternate Dowel SpacingsWhat can we conclude: Small change in responses– 7% increase in slab edge stress– 3% increase in deflection Decrease in the bearing stress at thedowel-concrete interface– Up to a 8% decrease Stresses redistribute due to change indowel placement
Alternate Dowel SpacingsWhat can we do: Steel savings can be considerable Increase in stress can be mitigated– Small increase in slab thickness– Small increase in concrete strength Again, recognize that there is already afactor of safety built into our current design!
In the end. Small increases in slab thickness orstrength can offset any increases inslab response Increasing concrete strength will alsoincrease bearing strength Reducing bearing stress can be done withelliptical dowels or by increasing doweldiameter. or even by repositioning the dowels!
In the end. Be rational about mitigating increases inslab response or bearing stress due tomodifications in dowel design Recognize there is already a significantfactor of safety inherent in the design wecommonly use today Use DowelCAD to save money withoutcompromising performance
How can I get DowelCAD?DowelCAD.comIt’s free!
Thank You!
Iowa’s Field Trials ofAlternate Dowel BarsBy Jim Cable, P.E.TRB Best Practices for Dowel Bars inConcrete Pavements WebinarFebruary 16, 2011
Dowel Research Goals Minimize the number & cost of dowel installationMinimize faultingOptimize dowel configuration relative to totalpavement design
Research Plan Five field projects– Two local roads– Three high truck volume routes Measure faulting, joint opening, distress &strainsConsider dowel bar materials, shape & spacing
Test Sites Selected HR-1069 – US 65, Des Moines BypassTR-420 – H-33, Creston Urban & P-33 CrestonRuralProject 5 – Iowa 330, Melbourne NBLTR-520 – Storm LakeProject – Iowa 330, Melbourne SBL
US 65 Test Site Information HR-1069, Des Moines (1997-2003)– Construction: 12 inch PCC on 10 inch aggregatebase on new grade– Bar Materials: 2 FRP, 1 Epoxy coated steel, 1stainless steel– Bar Diameter: FRP – 1 7/8, 1 ½, Stainless – 1 ½,Epoxy coated steel – 1 1/2– Bar Spacing: FRP & Stainless – 8 & 12 inches,Epoxy coated - 12 inches– Baskets: Full
Union County H-33 & P-33 Test SiteInformation TR-420, Creston (1998- 2003)– Construction: 9 inch PCC on 6 inches of sealcoat or3 inches of granular base– Bar Materials: Epoxy coated steel– Bar Diameter: 1 ½ inches– Bar Spacing: 12 inches– Baskets: no bars, 3 or 4 in OWP, full basket
Union County H-33 & P-33 Test SitePlacement
Iowa 330 NBL Test Site Information Project #5, Ia 330 Melbourne NBL (2002-2005)– Construction: 10 inch PCC on 6 inches granular base,on new grade– Bar Materials: FRP & Epoxy coated steel– Bar Diameter: FRP 2 ¼ x 1 ¼ inches, Epoxy coatedsteel 1 ½ inches– Bar Spacing: FRP @10, 12 & 15 inches, Epoxycoated steel @ 12 inches– Baskets: Full
Iowa 330 NBL FRP Dowel Placement
Storm Lake Test Site Information TR-520, Storm Lake (2004-2008)– Construction: 8 inch PCC on Compacted Soil in1988– Bar Materials: FRP & Epoxy coated steel– Bar Diameter: FRP 2 1/4x1 ¼ Elliptical, Epoxycoated steel 1 ½ inch round, 2x1 3/8 & 1 5/8x11/8Elliptical– Bar Spacing: 12 inches or 2,3,4 bars in OWP only– Baskets: Dowel Retrofit
Storm Lake Elliptical Dowel Placement
Iowa 330 SBL Test Site Information Iowa 330, Melbourne SBL (2002-2008)– Construction: 10 inch PCC on 6 inch granular base,new grade– Bar Materials: Epoxy Coated Steel Round & Elliptical– Bar Diameter: Heavy Elliptical 1.97x1.34 inches,Medium Elliptical 1.65x1.47 inches, Round 1.5inches– Bar Spacing: Heavy Elliptical & Round 12,15,18inches & Medium Elliptical 12 & 15 inches– Baskets: Elliptical – full or 4 in each wheel path
Iowa 330 SBL Wheel path Dowel Placement
US 65 Bypass Research Results FRP, Stainless & Epoxy coated steel dowelsperform equally in terms of faulting, joint openingand load transfer for 5 years.FRP bars should be placed on 8 inch spacing'sto provide performance equal to std. 1.5 inchepoxy coated barsNo bars experienced salt corrosion in 5 years.
Union Co
National Concrete Consortium (NCC) Recommendations for Standardized Dowel Load Transfer Systems – Maria Masten, Minnesota Department of Transportation and Mark Snyder, Engineering Consultant 1:30 PM Optimizing Dowel Bar Design using the DowelCAD Soft