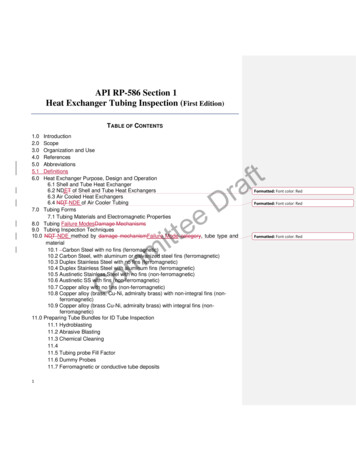
Transcription
API RP-586 Section 1Heat Exchanger Tubing Inspection (First Edition)TABLE OF nization and UseReferencesAbbreviationsDefinitionsHeat Exchanger Purpose, Design and Operation6.1 Shell and Tube Heat Exchanger6.2 NDET of Shell and Tube Heat Exchangers6.3 Air Cooled Heat Exchangers6.4 NDT NDE of Air Cooler Tubing7.0 Tubing Forms7.1 Tubing Materials and Electromagnetic Properties8.0 Tubing Failure ModesDamage Mechanisms9.0 Tubing Inspection Techniques10.0 NDT NDE method by damage mechanismFailure Mode category, tube type andmaterial10.1 Carbon Steel with no fins (ferromagnetic)10.2 Carbon Steel, with aluminum or galvanized steel fins (ferromagnetic)10.3 Duplex Stainless Steel with no fins (ferromagnetic)10.4 Duplex Stainless Steel with aluminum fins (ferromagnetic)10.5 Austinetic Stainless Steel with no fins (non-ferromagnetic)10.6 Austinetic SS with fins (non-ferromagnetic)10.7 Copper alloy with no fins (non-ferromagnetic)10.8 Copper alloy (brass, Cu-Ni, admiralty brass) with non-integral fins (nonferromagnetic)10.9 Copper alloy (brass Cu-Ni, admiralty brass) with integral fins (nonferromagnetic)11.0 Preparing Tube Bundles for ID Tube Inspection11.1 Hydroblasting11.2 Abrasive Blasting11.3 Chemical Cleaning11.411.5 Tubing probe Fill Factor11.6 Dummy Probes11.7 Ferromagnetic or conductive tube depositsmmitoC1etetfarDFormatted: Font color: RedFormatted: Font color: RedFormatted: Font color: Red
12.0 Reporting12.1 Baseline NDTNDE DataAPPENDIX A: NDTNDE Method Definitions and Detailed DescriptionsA1.0 Multi-Frequency Eddy Current TestingA2.0 Segmented Eddy Current Array (ECA) probes for use with non-magneticmaterialA3.0 Near Field Eddy Current (NFT) for use with magnetic materialsA4.0 Near Field Eddy Current ArrayA5.0 Partial Saturation Eddy CurrentA6.0 Full Saturation Eddy CurrentA7.0 Remote Field Eddy Current TestingA8.0 Magnetic Flux LeakageA9.0 Internal Rotating Inspection SystemA10 Remote Visual InspectionA11.0 Acoustic Pulse ReflectometryA12.0 Tube end calliperseteAppendix B: NDTNDE of Heat Exchanger Tubing TablesTable B-1 Suitability of NDTNDE methodsTable B-2 Flaw detection capabilities of NDTNDE methodsTable B-3 Flaw sizing capabilities of NDTNDE methodsFIGURES:moCtimFigure 1: Straight-tube heat exchangerFigure 2: U-Tube Heat ExchangerFigure 3: Typical forced draught air cooled heat exchangerFigure 4: O.D. of finned air cooled heat exchanger tubes – fouled vs. cleanFigure A1.1: MFET Coil DesignFigure A1.2: MFET Data Example: Left (Strip Chart), Right (Phase Angle)Figure A2.1 ECA data exampleFigure A3: Near Field Test CoilFigure A4: NFA data exampleFigure A7: RFT data exampleFigure A7.1: RFT probe designFigure A7.2: RFT dual exciter coil designFigure A8: MFL probe designFigure A9: IRIS probe designFigure A9.1: IRIS data set for a calibration tubeFigure A10: Remote visual inspection2tfarDFormatted: Indent: First line: 0"77910222326282932333335363738
Figure A10.1: RVI of internal tube depositsFigure A11: APR InstrumentFigure A11.1: APR PrincipleFigure A12: Tube end calliper38394040Formatted: Indent: First line: 0"1.0 INTRODUCTION1.1 Non-Destructive Testing is used extensively for the condition monitoring andremaining life estimates of heat exchanger tubing. This Recommended Practice outlinesthe principles, applications, capabilities and limitations of commercially availableNDTNDE methods for shell and tube and air-cooled heat exchangers. NDTNDE methodsare used to inspect tube bundles for the onset and progression of material damage towardfor the fitness for service and remaining life of heat exchanger tubes. This recommendedpractice links these NDTNDE methods with common heat exchanger designs, materialsof construction and damage mechanisms.ete2.0 SCOPEittfarD2.1 This recommended practice provides general guidance on the selection and use ofcommon NDTNDE methods for shell and tube and air cooler heat exchanger tubingdesigns. This recommended practice is limited to internal inspection of tubing for out ofservice heat exchangers. provides general guidance on the selection and use of commonNDE methods of tubes for shell & tube and air cooler heat exchangers. Heat exchangershells and components are covered in the pressure vessel section of this recommendedpractice.Plate heat exchangers, Heat exchanger shells and components and helicaltubing are not in the scope of this document. See the pressure vessel section of thisdocument.mmoC2.2 The NDTNDE methods mentioned in this recommended practice are intended forferrous, non-ferrous and alloy heat exchanger tubing materials 0.375-1.00 inches inoutside diameter and 0.022-0.220 inches in wall thickness. This document covers inservice heat exchanger tubing damage mechanisms found in API RP-571 and anotherother applicable codes and specifications.2.3 All NDTNDE applications in this document are deployed while the heat exchanger isout of service and with internal access to the heat exchanger tubes. An appropriate levelof heat exchanger cleaning and job preparations are assumed for adequate inspectionperformance. (see section 11.0).3.0 ORGANIZATION AND USE3Formatted: Font color: Red, StrikethroughFormatted: Font color: Red, StrikethroughFormatted: Font color: Red, StrikethroughFormatted: Font color: Red, StrikethroughFormatted: Font color: Red, StrikethroughFormatted: Font color: RedFormatted: StrikethroughFormatted: Font color: Red, StrikethroughFormatted: Font color: Red, StrikethroughFormatted: Font color: RedFormatted: Font color: RedFormatted: Font color: RedFormatted: Font color: Red, StrikethroughFormatted: Font color: Red, StrikethroughFormatted: Font color: Red
3.1 The information contained in this Recommended Practice is provided in a formatshown below. Heat exchanger design, tube types, materials of construction and damagemechanisms failure modes are briefly described in relation to the selection and usecommonly accepted NDTNDE method(s) for each heat exchanger design and tubingmaterial combination:. Detailed information for heat exchanger designs, materials ofconstruction, damage mechanisms and NDTNDE method guidance on use can be foundin the referencing literature.1.2.3.4.5.6.7.Shell and tube and air-cooled heat exchanger designsHeat exchanger tube typesHeat exchanger tube materialsHeat exchanger damage mechanism failure modessHeat exchanger tube flawsNDTNDE method selectionNDTNDE method definitions and descriptions7.timFormatted: Font color: Red, StrikethroughFormatted: Font color: RedtfarDDetailed information for heat exchanger designs, materials of construction,damage mechanisms and NDE method guidance on use can be found in the referencingliterature (see section 4.0).eteFormatted: Font color: Red, Strikethrough3.2 NDTNDE method and techniques are defined and explained in Appendix A.Formatted: Font color: RedFormatted: Normal, No bullets or numberingFormatted: Font color: RedFormatted: Font: (Default) Arial, 12 pt3.3 NDTNDE method and techniques selection tables are shown in Appendix B.moC4.0 REFERENCES4.0 REFERENCES4.1 NORMATIVE REFERENCES4.1.1 ASTM E2096/E2096M–16 Standard Practice for In Situ Examination ofFerromagnetic Heat-Exchanger Tubes Using Remote Field Testing4.1.22 E309-16 Standard Practice for Eddy Current Examination of Steel TubularProducts Using Magnetic Saturation4.1.3.3 E243-13 Standard Practice for Electromagnetic (Eddy Current) Examination ofCopper and Copper-Alloy Tubes4.1.44 E426-12 Standard Practice for Electromagnetic (Eddy-Current) Examination ofSeamless and Welded Tubular Products, Titanium, Austenitic Stainless Steel andSimilar Alloys4Formatted: Font color: Red
4.1.5 E570-15e1 Standard Practice for Flux Leakage Examination of FerromagneticSteel Tubular Products4.1.6 E571-12 Standard Practice for Electromagnetic (Eddy-Current) Examination ofNickel and Nickel Alloy Tubular Products4.1.7 E690-15 Standard Practice for In Situ ElectromagneticExamination of Nonmagnetic Heat Exchanger Tubes4.1.87 E2906/E2906M-13(EddyCurrent)Standard Practice for Acoustic Pulse ReflectometrytfarD4.1.90 API RP-571 Damage Mechanisms Affecting Fixed Equipment in the RefineryIndustry (2011)4.1.102 API RP-572 (2016) Inspection Practices for Pressure Vessels4.2 Informative Referencesete4.2.19 API- RP-660 (2015) Shell-and-tube Heat Exchangerstim4.2.210 9th Edition TEMA StandardsFormatted: Font color: Red4.2.311 API Standard 661 (2013) Petroleum, Petrochemical, and Natural GasIndustries- Air-Cooled Heat ExchangersmoC4.10 API RP-571 Damage Mechanisms Affecting Fixed Equipment in the RefineryIndustry (2011)4.12 API RP-572 (2016) Inspection Practices for Pressure Vessels5.0 NDE R: Acoustic Pulse ReflectometryBWG: Boiler Wall GaugeBirmingham Wire GaugeECT: Eddy Current TestingECA: Eddy Current ArrayFS-ECT: Full Saturation Eddy Current TestingID: Inside DiameterIRIS: Internal Rotating Ultrasonic Inspection SystemMFECT: Multi-Frequency Eddy Current Testing-TubingMFL: Magnetic Flux Leakage TestingMFA: Magnetic Flux Leakage Array Testing (MFA)Formatted: Font color: Red, StrikethroughFormatted: Font color: RedFormatted: Font color: Red, StrikethroughFormatted: Font color: RedFormatted: Font color: RedFormatted: Font: Bold
5.11 NFT: Near Field Testing5.12 NFTA Near Field Testing Array5.13 OD: Outside Diameter5.14 ASCC: Polythionic Acid Stress Corrosion Cracking5.145 PS-ECT: Partial Saturation Eddy Current5.156 RFT: Remote Field Eddy Current Testing5.16 RFTA: Remote Field Testing Array5.17 R-ECT: Rotational Eddy CurrentFormatted: Font color: Red, StrikethroughFormatted: Font color: RedFormatted: Font color: Red, StrikethroughFormatted: Font color: RedFormatted: Font: (Default) Arial, 12 ptFormatted: Normal, No bullets or numbering5.187 RVI: Remote Visual Inspection5.19 SECT: Segmented Eddy Current ArraytfarDFormatted: Font: (Default) Arial, 12 ptFormatted: Font: (Default) Arial, 12 pt, Font color: Red5.18 APR: Acoustic Pulse Reflectometry 5.18 APR Acoustic Pulse ReflectometryFormatted: Normal, No bullets or numberingFormatted: Font: (Default) Arial, 12 ptFormatted: Font: (Default) Arial, 12 pt, Font color: Red5.1 DefinitionseteSee Appendix A for NDE definitionstim6.0 HEAT EXCHANGER PURPOSE, DESIGN AND OPERATION6.1 Shell and Tube Heat ExchangerShell and tube Heat exchanger is the most common type of heat exchanger in oilrefineries and other large chemical processes, and is suited for higher-pressureapplications. This type of heat exchanger consists of a pressure vessel shell with aaninternal tube bundle that is typically supported by tube sheets and intermittent tubebaffles. Heat is transferred from the warmer fluid to the other through the tube walls tothe colder fluid with heat transfer taking place from either from tube side to shell side orvice versa. One fluid runs through the tubes, and another fluid flows over the tubes(through the shell) to transfer heat between the two fluids. The tube bundle may becomposed of several types of tubes: plain, longitudinally finned, low finned, or twistedtube.moC6.1.1 Two fluids, of different starting inlet temperatures, flow through the heatexchanger. One flows through the tubes (the tube side) and the other flows outside thetubes but inside the shell (the shell side). Heat is transferred from one fluid to the otherthrough the tube walls, either from tube side to shell side or vice versa. The fluids canbe either liquids or gases on either the shell or the tube side. See figure 1.6.1.2 The tube pitch (center to center distance of adjoining tubes) is typically a minimumof 1.25 times the tube outer diameter or larger. The tube pitch usually limits externalinspection access to the accessible outer tubes of a tube bundle. Subsequently,inspection of the remaining heat exchanger tubes is limited to internal tube inspection6Formatted: Font: (Default) Arial, 12 ptFormatted: Font color: RedFormatted: Font color: Red, StrikethroughFormatted: Font color: RedFormatted: Font color: Red, StrikethroughFormatted: Font color: Red, Strikethrough
methods/The tube pitch (center to center distance of adjoining tubes) is typically aminimum of 1.25 times the tube outer diameter or larger. The tube pitch usually limitsinspection access to the tube outer surfaces for visual or other external non-destructivetesting tubing inspection methods. Heat exchanger tubing inspection is normally limitedto internal tube inspection methods. With the exception of visual inspection of theoutside tubes in the tube bundle, heat exchanger tubing inspection is normally limited tointernal tube inspection methods.Formatted: Font color: Red, StrikethroughFormatted: Font color: Red6.1.3 Typically, the ends of each tube are terminated through holes in a tube sheet thatis made of the same or different material than the tubes. The tubes are mechanicallyrolled or welded into tube sheet face. Tubes may be straight or bent in the shape of a U,called U-tubes. (See figure 2).tfarD6.1.4 Baffles (or Tube Support Plates) used in shell and tube heat exchangers servetwo purposes. The first is to direct fluid across the tube bundle, providing adequateheat transfer. The first is to direct fluid across the tube bundle, providing an increase inthe overall heat transferred. The second purpose is to provide additional tube support toprevent sagging of the tubes (over a long span) and to prevent or minimize the tubesfrom vibrating within the tube bundle.etetimmoCFigure 1: Straight-tube heat exchanger7Formatted: Font color: Red, StrikethroughFormatted: Font color: Red
Figure 2: U-Tube Heat Exchangerete6.2 NDTNDE of Shell and Tube Exchanger TubingtimtfarDMost of the electromagnetic NDTNDE techniques provide an estimated semi-qualitativeFormatted: Font color: Red, Strikethroughtube wall thickness estimation as compared to that of a known calibration tube. TheFormatted: Font color: Redestimated wall thickness is also an average or the entire wall circumference as themoCsingle magnetic field provides a s
service heat exchanger tubing damage mechanisms found in API RP-571 and another other applicable codes and specifications. 2.3 All NDTNDE applications in this document are deployed while the heat exchanger is out of service and with internal access to the heat exchanger tubes. An appropriate level of heat exchanger cleaning and job preparations are assumed for adequate inspection performance .