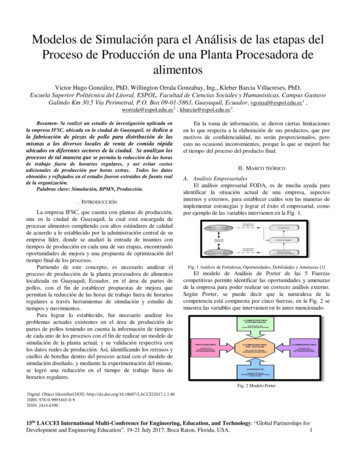
Transcription
Modelos de Simulación para el Análisis de las etapas delProceso de Producción de una Planta Procesadora dealimentosVictor Hugo González, PhD, Willington Orrala Gonzabay, Ing., Kleber Barcia Villacreses, PhD,Escuela Superior Politécnica del Litoral, ESPOL, Facultad de Ciencias Sociales y Humanísticas, Campus GustavoGalindo Km 30.5 Vía Perimetral, P.O. Box 09-01-5863, Guayaquil, Ecuador, vgonzal@espol.edu.ec1 ,worrala@espol.edu.ec2 , kbarcia@espol.edu.ec3.Resumen- Se realizó un estudio de investigación aplicada enla empresa IFSC, ubicada en la ciudad de Guayaquil, se dedica ala fabricación de piezas de pollo para distribución de lasmismas a los diversos locales de venta de comida rápidaubicados en diferentes sectores de la ciudad. Se analizan losprocesos de tal manera que se permita la reducción de las horasde trabajo fuera de horarios regulares, y así evitar costosadicionales de producción por horas extras. Todos los datosobtenidos y reflejados en el estudio fueron extraídos de fuente realde la organización.Palabras clave: Simulación, BPMN, Producción. INTRODUCCIÓNLa empresa IFSC, que cuenta con plantas de producción,una en la ciudad de Guayaquil, la cual está encargada deprocesar alimentos cumpliendo con altos estándares de calidadde acuerdo a lo establecido por la administración central de suempresa líder, donde se analizó la entrada de insumos contiempos de producción en cada una de sus etapas, encontrandooportunidades de mejora y una propuesta de optimización deltiempo final de los procesos.Partiendo de este concepto, es necesario analizar elproceso de producción de la planta procesadora de alimentoslocalizada en Guayaquil, Ecuador, en el área de partes depollos, con el fin de establecer propuestas de mejora quepermitan la reducción de las horas de trabajo fuera de horariosregulares a través herramientas de simulación y estudio detiempos y movimientos.Para lograr lo establecido, fue necesario analizar losproblemas actuales existentes en el área de producción departes de pollos teniendo en cuenta la información de tiemposde cada uno de los procesos con el fin de realizar un modelo desimulación de la planta actual, y su validación respectiva conlos datos reales de producción. Así, identificando los retrasos ycuellos de botellas dentro del proceso actual con el modelo desimulación diseñado, y mediante la experimentación del mismo,se logró una reducción en el tiempo de trabajo fuera dehorarios regulares.En la toma de información, se dieron ciertas limitacionesen lo que respecta a la elaboración de sus productos, que pormotivos de confidencialidad, no serán proporcionados, peroesto no ocasionó inconvenientes, porque lo que se mejoró fueel tiempo del proceso del producto final.II. MARCO TEÓRICOA. Análisis EmpresarialesEl análisis empresarial FODA, es de mucha ayuda paraidentificar la situación actual de una empresa, aspectosinternos y externos, para establecer cuáles son las maneras deimplementar estrategias y lograr el éxito el empresarial, comopor ejemplo de las variables intervienen en la Fig. 1.Fig. 1 Análisis de Fortalezas, Oportunidades, Debilidades y Amenazas [1]El modelo de Análisis de Porter de las 5 Fuerzascompetitivas permite identificar las oportunidades y amenazasde la empresa para poder realizar un correcto análisis externo.Según Porter, se puede decir que la naturaleza de lacompetencia está compuesta por cinco fuerzas, en la Fig. 2 semuestra las variables que intervienen en lo antes mencionado.Fig. 2 Modelo PorterFig. 2 Modelo PorterDigital Object Identifier(DOI): http://dx.doi.org/10.18687/LACCEI2017.1.1.40ISBN: 978-0-9993443-0-9ISSN: 2414-639015th LACCEI International Multi-Conference for Engineering, Education, and Technology: “Global Partnerships forDevelopment and Engineering Education”, 19-21 July 2017, Boca Raton, Florida, USA.1
B. Estudio de Tiempos y movimientos.En este estudio se consideraron todos los procesos de laempresa que consistieron desde recepción hasta inyecciónconsiderando la carta de flujo de procesos operativos paradeterminar cuáles operaciones son consideras como transporte,proceso, tiempos de espera y almacenamiento. Para cada unade estas actividades se realizó en la empresa la toma respectivade tiempos y movimientos dando como resultado ladeterminación de las variables y la construcción posterior delmodelo de simulación usado para la reducción de las horas enhorarios no regulares de la empresa. [2]III. METODOLOGÍAA. Metodología PropuestaPara una correcta comprensión de cada parte en losprocesos de producción que manejan en planta, se estudió demanera micro y macro el flujo de trabajo comprendiendodesde un análisis actual de la e m p r e s a hasta unaevaluación de los resultados obtenidos por la optimización delos procesos que ocasionaron el problema principal derecepción usando el software de simulación.La metodología empieza con el análisis, tanto de lasituación actual de la empresa o planta como de los procesosque ocasionan la baja eficiencia en los resultados finales. Elanálisis consistió en verificar su situación actual con análisismatricial estratégico (matrices EFE, EFI, DOFA) y lasentrevistas respectivas para identificar procesos junto conmétodos de tiempos y movimientos dentro de la planta paradeterminar si dichos procesos se están realizando de maneraeficiente. [5]Luego de realizar el análisis respectivo de situación yprocesos se realizaron hojas de procesos con tiempos ymovimientos para identificar los desperdicios de los procesosactuales y determinar si existe o no la posibilidad de aplicartécnicas de simulación para optimizarlos. [6]Del paso anterior, se simularon los procesos opteniéndosetablas y determinándose los cuellos de botella a atacarse paraincrementar la productividad.Así pues, luego de las etapas de análisis, diseño yejecución se realizó una evaluación comparativa de los flujos yresultados de la simulación con una validación del modelo conla situación real de la empresa determinando puntos críticospara el éxito de incremento de la productividad.Fig. 3 Metodología Propuesta [6]La aplicación de modelos de simulación permitió evaluarlas diferentes soluciones planteadas, y la elección de laherramienta adecuada dependió del tipo de procesos.Para la simulación de los procesos futuros de la empresase utilizó WITNESS porque nos permió analizar losdesperdicios y proponer varios escenarios de simulación.Para llevar a cabo una simulación correcta se debe seguirlos siguientes pasos:- Elaborar una lista de residuos y posibles soluciones- Desarrollar el modelo de oficina y producciónB. BIZAGI Es un Software de Gestión de Procesos de Negocio (delinglés BPM: Business Process Management) que permiterealizar diagramas y documentar procesos utilizando el modeloBPMN (Business Process Management Notation).Dentro de las características más importantes se destacanla simplicidad del modelamiento, ya que no se requiere unamplio conocimiento para realizar diagramas, basta conarrastrar y soltar el elemento sobre el área de trabajo paracomenzar a modelar los procesos.Cuenta con un sistema que permite establecer funciones enlos diferentes departamentos en la toma de daciones parecidoal diagrama de flujos, pero con el detalle de separación con lasáreas que intervienen en el proceso, con esta herramienta detrabajo muchas grandes empresas han optado por utilizar esteservicio que brinda facilidades y un entendimiento correcto encada poso a seguir [3].C. WITNESS La herramienta informática que se utilizará en el presenteproyecto es Witness horizon 20.0. El software Witness tieneuna interfaz gráfica de fácil interpretación, que nos permiteilustrar de mejor forma los procesos de la empresa.Witness nos permite evaluar distintos escenarios mediantedecisiones estratégicas que pueden implementarse en la15th LACCEI International Multi-Conference for Engineering, Education, and Technology: “Global Partnerships forDevelopment and Engineering Education”, 19-21 July 2017, Boca Raton, Florida, USA.2
compañía. Su objetivo es brindar un programa que satisfaga lasnecesidades de los usuarios los cuales necesitan representar deforma real modelos de negocios que simplifiquen los datos,obteniendo medidas de productividad y fomentando el trabajoen equipo [4].IV. ANÁLISIS DE INFORMACIÓNA. Presentación de la empresaEn el Ecuador empieza sus operaciones en 1991,estableciendo su planta en Quito y debido a la fuertedemanda apertura su segunda planta de producción en el año1999 en la ciudad de Guayaquil la cual es el objeto deinvestigación.Misión:Creer en Nuestra GenteInnovar continuamente el mercado de comida.Superar nuestros resultados todos los años.Visión:“Ser reconocidos como líderes del mercado en cada una delas categorías que participamos”Política de Inocuidad:“La Planta I F S C se compromete a procesar ydistribuir productos Inocuos de Calidad, cumpliendo connormas nacionales e internacionales para satisfacer lasexpectativas de nuestros clientes”Materia prima utilizada:El área de elaboración de productos de pollo trabajabásicamente con cuatro tipos de materia prima, esta es deacuerdo al peso y variedad del pollo, la misma que debencumplir con una serie de características físicas y organolépticasque avalen su grado de calidad e inocuidad que permita laelaboración en dicha área.TABLA IMATERIA PRIMATIPOPESO PROMEDIO(Kg)Standard 11.18 - 1.26Standard 21.26 - 1.32Standard 31.32 - 1.40Standard 41.40 - 1.48B. Situación actual de la empresaEn base a la investigación de campo y levantamiento deinformación que se ha realizado en la empresa se hanidentificado ciertas falencias en las actividades tanto en laprimera etapa de recepción de la materia prima hasta elalmacenamiento en la cámara de despacho de productoterminado, afortunadamente cuentan con registros para cadauna de las actividades que realizan, dado que necesitábamoscomprobar cada etapa del flujo.Para determinar el grado en que la empresa estáaprovechando estos factores se realizará la matriz yposteriormente de factores externos y la matriz de factoresinternos.Para contrarrestar las amenazas y debilidades en lasolución del problema y aprovechar las oportunidades yventajas que se presenten, es necesario realizar el análisis de losfactores externos. [9] En la formulación de estrategias seelaboró un cuadro de trabajo DOFA en el que se identificanventajas distintivas frente a otras empresas del medio paraencontrar su propio lugar en el mercado. [10]La empresa mantiene un total ponderado mayor alpromedio ponderado, lo que indica que está respondiendo biena las oportunidades y amenazas que se presentan en el entorno.Para el análisis de la situación actual de la empresa serealizaron entrevistas focalizadas a problemas empresarialescon los gerentes y los expertos, determinando las matrices deevaluación empresarial EFE y EFI con las cuales se obtuvieronpuntos claves en las estrategias a seguir con respecto a lasfortalezas, oportunidades, debilidades y amenazas de la misma.[10]Los resultados de este análisis se encuentran acontinuación en las tablas II, III y IV.TABLA IIANÁLISIS EFE [5]FACTORPESO CALIFICACIONOPORTUNIDADES1. oductos.2. Alternativas deampliacióndelárea deproducción3. Ampliarsusclientes.AMENAZAS1. Ingreso de nuevos competidores.2. Mano de obra a menor costo en el mercado.3. Presenciadenuevoscompetidores alrededordesu establecimiento.4. Dificultad para conseguir nuevos ,41,00TABLA IIIANÁLISIS EFIFACTORFORTALEZAS1. Posicionamiento en el mercado.2. Producto de calidad.3. Comunicación efectiva dentro de la empresa.4. Solucion de problemas oportunosDEBILIDADES1. Retrasosdelproveedorenlaentregademateriaprima.2. Producción limitada.3. Errores del area de despacho.4. Demora en contratacion de personalTOTAL2,6PESO 00,302,5515th LACCEI International Multi-Conference for Engineering, Education, and Technology: “Global Partnerships forDevelopment and Engineering Education”, 19-21 July 2017, Boca Raton, Florida, USA.3
icionamiento en elmercado.Producto decalidad.Comunicaciónefectiva dentrode la empresa.Solución deproblemasoportunos.DEBILIDADESRetrasos delproveedor en laentrega demateria prima.Producciónlimitada.Errores del áreade despacho.Demora encontratación depersonal.1.2.3.1.2.3.OPORTUNIDADESCaptar nuevossegmentos demercado,diversificando susproductos.Alternativas deampliación del áreade producción.Ampliar sus clientes.Crecimiento de laempresa.ESTRATEGIAS(FO)Mejorar el servicio alcliente.Fortalecer ImagenEmpresarial.Realizar actividades ycharlas demotivación.ESTRATEGIAS(DO)Conseguir nuevosproveedores.Mantener lascertificaciones.Capacitar al personal.1.2.3.4.1.2.3.1.2.3.AMENAZASIngreso de nuevoscompetidores.Mano de obra amenor costo en elmercado.Presencia de nuevoscompetidoresalrededor de suestablecimiento.Dificultad paraconseguir igar a fondonuevos y mejoresproveedores.Hacer planificacionesestratégicas paraoptimizar losprocesos.ESTRATEGIAS(DA)Mejora en pedido deMateria Prima yDespacho.Mejora en procesode Reclutamiento.Dar mantenimiento alas maquinarias paraevitar retrasos.TABLA VDESPERDICIOS [8] (Hernández & Vizán, 2013)Tipo de desperdiciosSobre-producciónTiempo de esperaTransporteMovimientoConclusiónNo cuentan con tiemposadecuados en cada proceso.La planta no tiene correctamenteNo cuentan con un detalle de loscoordinado los tiempos detiempos de espera de cadaProceso que debe tener cada áreaprocesopara que continúe con el flujo.Cuentan con un adecuadotransporte de la materia primay producto terminado, perodebería aumentar ladisponibilidad de estaherramienta.Almacenamiento para que nopierda temperatura la materiaprimaTABLA IVMUESTRA PARA ENCUESTASCARGO# ervisores28%Total25RecepciónTieneun número limitado deherramientas de transporte, paraque aumente la productividaddebe adquirir más de unidades.Actualmente la planta y según elflujo de trabajo, en cada áreadebe almacenar en las cámaras losproductos en tránsito, pero unaalternativa es aumentar latemperatura del ambiente paraque los movimientos no seannecesarios.Regularmente en los procesostienen confusiones por losmovimientos de las cámaras sinun aviso previo ya que nocuentan con un encargadodirecto del almacén.InventarioCuentan con un correcto registrode ingreso a la planta pero notienen un control con losmovimientos dentro de las áreas.ProcesosNo cuenta con una correctasupervisión en horas específicasde procesoLa planta cuenta con variossupervisores, pero usualmenteestos tienden a realizar otrasactividades en las oficinasDefectosLapolítica de inocuidad y calidadde la planta es fundamental para laidentificación de defectos en losproductosControl de calidadde la plantausualmente toma más tiempo delo necesario en la revisión yaceptación de defectosCapacitaciones ConstantesCumplen con la capacitación en lasinducciones al ingreso, pero amenos que este cerca unaauditoria estos no son capacitadosen temas relacionadoFig. 4 Análisis DOFA [10]C. Identificación de desperdiciosDistribución de la muestra: Para Finalmente identificarlos desperdicios de la planta como son tecnología, procesos,medio ambiente y cultura. Se realizaron las entrevistas yencuestas a los trabajadores de las diferentes áreas de la plantalas cuales nos sirven para analizar los puntos críticos, acontinuación, se presentará los resultados obtenidos en elmodelo de encuesta realizado [6], [7].Aplicación de Encuestas y Resultados: Las encuestaspara el área de producción, que permiten el análisis paradetectar los desperdicios en el departamento son las áreasespecíficas de: recepción, corte e inyección, por esa razón serealiza los análisis pertinentes en el software de SPSS versión24.0 las cuales muestran a continuación.EvidenciaActualmente la planta no cuentacon estudios con indicadores detiempo máximo de proceso paraabastecer la necesidad de losclientes.Factor humanoD. Descripción de tareas por áreaRecepción: La recepción de la materia prima consiste enel proceso de receptar al pollo en la planta, esta es transportadaen camiones refrigerados para conservar la frescura del pollodesde San Isidro hasta que llegue a la planta en Guayaquil, lasactividades principales en esta primera etapa son las siguientes:- Descarga de la materia prima trasvasadas en jabas de20 unidades.- Ubicación en columnas de siete jabas con susrespectivas etiquetas del lote de faena y recepción.- Transportación hasta la balanza de piso por medio delcoche.- Toma de pesos.- Almacenamiento en la cámara de recepción.15th LACCEI International Multi-Conference for Engineering, Education, and Technology: “Global Partnerships forDevelopment and Engineering Education”, 19-21 July 2017, Boca Raton, Florida, USA.4
Cabe recalcar que si la materia prima esta fueratemperatura de acuerdo al rango de aceptación, esta es retenidahasta que se realice el análisis de salmonella y detectar posiblesdesviaciones en su calidad. De la misma manera se toma unamuestra cada 100 unidades recibidas como medida adicionalpara detectar el cumplimiento de acuerdo a las característicaspropias de la faena, tales como desgarres, moretones, entreotras.Posterior a este proceso, se almacena en la cámara derecepción hasta que el encargado del área de corte los tomepara el siguiente proceso.Corte: Esta área es fundamental dentro del flujo delproceso, puesto que el tiempo que el producto permanezca enesta área afecta directamente a las demás, en esta etapa lamateria prima sufre su transformación como producto entránsito la principal actividad es cortar el pollo en nueve presaslas cuales son las siguientes:- 2 alas.- 2 muslos.- 2 caderas.- 2 costillas- 1 pechuga.Cabe recalcar que cada una de estas presas debe cumplircon parámetros según alineamiento de la administración centralde su empresa líder, el personal encargado de realizar estasactividades es capacitado y de acuerdo al tiempo dentro delárea que permita su puesta en práctica.Una vez realizada esta operación las jabas contendrán 180presas, las mismas que son monitoreadas por defectos en loscortes u otra falencia propia de la actividad, adicional a ello sonnuevamente ubicados en filas de 8 jabas para ser procesados deacuerdo al requerimiento del área de inyección.Inyección: El proceso normal de esta área depende de lavelocidad que el área que le antecede disponga la materiaprima cortada, actualmente cuentan con 3 máquinas inyectoraspero cada una tiene su función específica de acuerdo alproducto que se esté procesando, en el caso de las presasespeciales C, la maquina utilizada es la inyectora de 180 agujas,esta cuenta con una banda transportadora que permite elmovimiento e inyección de la salmuera característico delproducto, luego son llevadas a la mesa de acero inoxidabledonde se encuentra el personal que cuenta las unidades, lasclasifica para ser empacadas en fundas de 18 presas la mismasque se detalla a continuación:- 4 alas.- 4 muslos.- 4 caderas.- 4 costillas- 2 pechugas.Una vez realizada esta actividad son almacenadas en jabasde 10 fundas, de la misma manera ubicadas en filas de 8 jabaspara finalmente ser transportadas en coche de acero inoxidablehasta la respectiva cámara de despacho para su posteriorentrega.Cámaras de almacenamiento: Las cámaras dealmacenamiento están muy limitadas en lo que concierne aespacios, puesto que como máximo se contara con stock de 3días de procesos.E. Levantamiento de tiempos de procesosPara el estudio es importante conocer el tiempo normal deproceso. Sin considerar retrasos que influyen en la producción,es así, que consideramos el análisis de una jornada regular dedescarga de la materia prima el cual mostramos el tiempo totalen la primera etapa.TABLA VIUNIDAD DE ALMACENAMIENTOLEVANTAMIENTOY TOMA DE sentación20und/Jb385jabasUnidad de proceso7Jb/Fila55FilasComo primer punto se presenta la unidad de descarga dela materia prima, tenemos que en total en promedio por viaje7500 pollos, compartidos en 385 jabas de 20 unidades cadauna, de la misma manera la unidad de descarga es en filas de 7jabas cada una, como resultado el total de filas descargadas porviaje es de 55, según muestra el grafico.El área de recepción encargada de receptar toda la materiaprima cuenta con 5 actividades detallas en el gráfico, de lamisma manera muestra el tiempo que se toma en cada una deellas, para finalmente almacenar una fila de jabas es de 1minuto 49 segundo aproximadamente esto multiplicado por las55 filas nos da un total de 1 hora con 40 minutos en descargarel viaje completo de pollo.TABLA VIILEVANTAMIENTO DE TIEMPOS pación en FilasEtiquetadoPesadoAlmacenadoTiempo :30Tiempo0:00:390:01:090:01:190:01:491:39:55 Tiempo descarga promedioLos siguientes procesos son simultáneos, mientras másrápido cuente con materia prima cortada, más rápido será elproceso del área de inyección.La tabla VIII muestra el tiempo que se toma en cada unade las actividades, según la información levantada una mesa decorte se toma 27 minutos en completar de procesar una filapollo, el resultado de cortar el viaje de 55 filas tomaría15th LACCEI International Multi-Conference for Engineering, Education, and Technology: “Global Partnerships forDevelopment and Engineering Education”, 19-21 July 2017, Boca Raton, Florida, USA.5
alrededor de 25 horas de proceso, actualmente se cuenta con 4mesas, como resultado se trabajaría 6 horas con 14 minutosaproximadamente en completar el viaje de pollo.Finalmente, en el área de inyección, manteniendo el mismoesquema de estudio y levantamiento de tiempos para cadaetapa, está se demora en procesar 7 horas con 7 minutos, yaque debido al proceso de la maquina inyectora toma un pocomás de tiempo en la espera que el producto caiga en la mesa deconteo para que las personas encargadas empiecen con laseparación y empaque el producto.Una vez concluida se agrupa en filas para sualmacenamiento en la cámara de despacho, con un totalaproximado de 8 horas con 47 minutos y 5 segundos, luego dereceptar la materia prima en la planta.el área de producción, como la especificas que se estudiaran,además se utilizó el programa WITNESS para demostrar losmovimientos y actividades del proceso para cada producto quese procesa en la empresa.En la Fig. 4, se muestra la simulación con los tiemposlevantados en la planta para cada una de las actividades que serealizan.El tiempo total de proceso según Bizagi, es de 8 horas con48 minutos desde la recepción de la materia prima, el cualcumple con los datos reales de trabajo, que según ellevantamiento previo de tiempos en cada una de sus etapas esde 8 horas con 47 minutos y 5 segundos, es decir, su variaciónes de 59 segundos, apenas, con el real.TABLA VIIILEVANTAMIENTO DE TIEMPOS ÁREA-CORTEÁreaTareaTransportaciónUbicación en MesaCortadoUbicación en JabaAgrupación en FilasAlmacenadoCorteUnidad1 Fila7 Jabas1 Pollo1 Pollo7 Jabas1 58 Tiempo por Jaba Procesada0:55:056:13:46 Tiempo de Produccion TotalTABLA IXLEVANTAMIENTO DE TIEMPOS nUbicaciónen MaquinaInyecciónConteoEmpacadoUbicación en JabaAgrupaciónen FilasAlmacenadoUnida1 Fila7 Jabas1 Jaba1 Funda1 Funda1 Funda1 Jaba1 FilaTiempo 150:01:390:02:490:28:0:00:0:30:490:31:040:04:24 0:01:06 Tiempo por Jaba Procesada4:28:40 7:07:10 Tiempo de Produccion TotalF. Modelado de procesos actualesEl modelado de procesos ayuda a tener una mejorvisualización de las actividades que se deben seguir en laplanta. Para conocer los procesos actuales que tiene laempresa, se dividió por etapas el proceso de producción y semodeló mediante el programa BIZAGY tanto el flujo de todaFig. 4 Simulación de TiemposG. Evaluación de Jornadas de ProducciónPara conocer el tiempo que afecta este retrasopresentamos en la tabla X el detalle de las horas extras por día,15th LACCEI International Multi-Conference for Engineering, Education, and Technology: “Global Partnerships forDevelopment and Engineering Education”, 19-21 July 2017, Boca Raton, Florida, USA.6
el cual se calculó el promedio diario y este valor es de 1 horacon 34 minutos, si multiplicamos este tiempo por las 25personas que intervienen en el proceso asciende a 15 horasacumuladas que se deben pagar adicionalmente cuando existenretrasos en la recepción y envió de la materia prima.TABLA XJORNADAS 08/201615/08/2016Jornadas ExtendidasPromedio en 0:102:001:003:301:003:302:502:30181:3425Para medir el impacto que ocasiona el retraso de la jornadade producción, a continuación, se muestra los datos del últimomes de recepción de materia prima y de producción de acuerdoa la hora de llegada.TABLA XIHORAS DE RECEPCIÓN Y PRODUCCIÓNRecepción TiempoTotal 401:35FinProducciónTiempoProducciónTotal Cantidad Total13:5515:15 280347435361535528249Hora 015:0020:0017:3016:1020:0019:2019:00H. Propuesta de optimización a través de BizagiCon la modelación del proceso actual en el programa deBizagi se logró apreciar que los datos obtenidos en ellevantamiento de tiempos promedios fueron los correctos, yaque la diferencia entre el modelo y el flujo real del proceso deproducción fue de 1 minuto, de esta manera nos da laconfianza de proponer escenarios en el cual optimice la jornadade producción.Escenario 1: Recepción de Materia PrimaLa primera propuesta, como medida de reducción dejornadas fuera de horarios regulares es el planteamiento alproveedor de materia prima que cumpla con los cronogramasde envíos, así como las horas propuestas para cada día, comose demostró en la modelación de Bizagi que el tiempo total deprocesos es de 8 horas con 40 minutos independientemente dela hora que envíen la materia prima para los procesos.Si cumplen con la recepción a la hora prevista 8:00 Am,con todo el tiempo de producción se finalizaríaaproximadamente a las 16:30 Pm completando la planificación15th LACCEI International Multi-Conference for Engineering, Education, and Technology: “Global Partnerships forDevelopment and Engineering Education”, 19-21 July 2017, Boca Raton, Florida, USA.7
a la hora que es, y no incurre en altos rubros por cancelaciónde horas extras.Escenario 2: Flujo Continuomodelaciones nos demuestran el aumento de productividad ypor qué debe realizarse un replanteamiento en su esquema deproducción, ya que según los resultados depende mucho deltiempo que el proveedor envié los pedidos.De acuerdo al flujo normal de trabajo la materia primadebe permanecer en la cámara de recepción una vez que hasido descargado del camión, de la misma manera cuando sufresu transformación en el área de corte debe ser almacenada en lacámara de fríos, considerando que la jornada laboral en elecuador es de 8 horas al día, completando 40 horas a la semanasin tener que cancelar horas extras a los empleados, pero si seimplementa esta propuesta en la planta de IFSC con el modelode trabajo siguiente este a mas que cumpliría con laplanificación saldrían en 8 horas 1 minuto.1. Eliminación del transporte hacia la cámara de fríosdesde el pesado de la materia prima, con esto sepropone enviarlos directamente al proceso deproducción en corte para que sea procesadoinmediatamente.2. Eliminación del almacenamiento una vez realizado elcorte, según el flujo esta debe ser guardado para queno pierda su temperatura, la propuesta estransportarlos directamente hacia el área de inyecciónpara que sean procesados y ajustando el ambientecontrolado de las áreas, puesto que el personal cuentacon calentadores, abrigos y polainas para protecciónen el ambiente frio.3. Transportación de la materia prima corta desde lacámara de frio, se pretende que los envíos seandirectos hacia las áreas.4. Finalmente, la adquisición de 2 nuevos coches detransportación de materia prima con ello, se reduce eltiempo de almacenamiento cuando se tenga lista másde filas
recepción usando el software de simulación. La metodología empieza con el análisis, tanto de la . básicamente con cuatro tipos de materia prima, esta es de acuerdo al peso y variedad del pollo, la misma que deben cumplir con una serie de características físicas y organolépticas que avalen su grado de calidad e inocuidad que permita la .