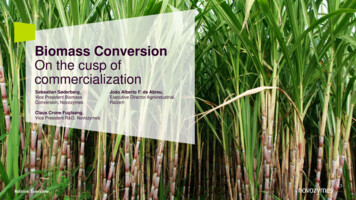
Transcription
Biomass ConversionOn the cusp ofcommercializationSebastian Søderberg,Vice President BiomassConversion, NovozymesClaus Crone Fuglsang,Vice President R&D, NovozymesJoão Alberto F. de Abreu,Executive Director Agroindustrial,Raízen
Forward-Looking StatementsThis presentation and its related comments contain forward-looking statements, including statements about future events,future financial performance, plans, strategies and expectations. Forward-looking statements are associated with wordssuch as, but not limited to, "believe," "anticipate," "expect," "estimate," "intend," "plan," "project," "could," "may," "might"and other words of similar meaning.Forward-looking statements are by their very nature associated with risks and uncertainties that may cause actual resultsto differ materially from expectations, both positively and negatively. The risks and uncertainties may, among other things,include unexpected developments in i) the ability to develop and market new products; ii) the demand for Novozymes’products, market-driven price decreases, industry consolidation, and launches of competing products or disruptivetechnologies in Novozymes’ core areas; iii) the ability to protect and enforce the company’s intellectual property rights; iv)significant litigation or breaches of contract; v) the materialization of the company’s growth platforms, notably theopportunity for marketing biomass conversion technologies or the development of microbial solutions for broad-acre crops;vi) the political conditions, such as acceptance of enzymes produced by genetically modified organisms; vii) the globaleconomic and capital market conditions, including, but not limited to, currency exchange rates (USD/DKK and EUR/DKK inparticular, but not exclusively), interest rates and inflation; viii) significant price decreases on input and materials thatcompete with Novozymes’ biological solutions. The company undertakes no obligation to update any forward-lookingstatements as a result of future developments or new information.2
Session outline Progress and challengeslast 18 months Reasons to believe in biomassconversion Innovation priorities Raízen: Views from leadingbrazilian sugar cane crusherand biomass conversionpioneer3
15 years of continuous development and oneof our largest R&D investments2001One of largest R&Dinvestments inNovozymes’ historywas initiatedFoundation42005200920122013Biomass conversionpilot plants worldwidetesting NovozymesenzymesLaunch of Cellic CTec for the firstcellulosic ethanoldemonstration plantsThe first commercialcellulosic ethanolplant: Crescentino –using Novozymes’Cellic technologyExclusive partnershipwith Brazil’s largestsugar-based ethanolproducerPilot stageDemo stageBusiness Development – BioAgriculture – Biomass Conversion – Animal Health & NutritionInitial commercial stage2015Five of seven largescale biomassconversion ethanolplants globally useCellic technologyOptimization stage
Progress towards commercialization sinceCapital Markets Day 20135Biomass conversion industry in fall 2013Biomass conversion industry today Beta Renewables’ Crescentino plant is the world’s firstand only commercially operating cellulosic ethanol plant Six commercial plants are in operation with Novozymessupplying five of them. DuPont to be #7 Three plants under construction in the US and two in LA All process steps undergoing optimizations Large number of publicly announced biomass conversionprojects 20 solid biomass conversion projects are underdevelopment globally (not all publicly announced) Expectation of a relatively fast industry commercialization Novozymes’ Cellic CTec3 is the leading enzymetechnology (one size fits all enzyme product)Recognition that industry commercialization will takelonger Novozymes is committed to pursue further processoptimizations beyond enzymes. Our customized nextgeneration Cellic enzyme solutions are being launched Novozymes heavily engaged in project development with“boots on the ground” globallyBusiness Development – BioAgriculture – Biomass Conversion – Animal Health & Nutrition
Headwinds and longer timelines than anticipated, butseveral reasons lead us to believe that these will be overcomeProlonged industry ramp-up Up-scaling of commercial plants takes longer thanexpected. From serving 15 plants by 2017 to anassumption of 15 by 2020New industries take time– it’s a marathon, not a sprint Many industries deliver lower Capex over time New projects struggle to find financing, as everyone isin waiting mode to get confirmation of the economics Novozymes as a full biotech solutions provider to bolsterbiomass conversion process optimization Some projects have been cancelled or on hold Healthy project pipeline continues to mature Expectation that internal combustion engines / liquidfuels will play a substantial role in the future National blending mandates in the EU(Italy announced, more in the making) Brazil ethanol blending mandate increase to E27Macro and regulatory uncertainty 6 Lower oil price casts uncertainty and makes for atougher environment for biofuels – particularly in theUS and AsiaUS ethanol demand stuck in limbo due to the blendwall and unclear regulatory frameworkBusiness Development – BioAgriculture – Biomass Conversion – Animal Health & Nutrition
Comparable disruptive technologies have taken 15 years to take off;enabling an industry is a “marathon” with multiple hurdles to be overcomeCorn ethanolSolarInstalled corn ethanol capacity (U.S.), 1990–2014Million gallons/yearGlobal solar power cumulative installed PV capacity 2000–2012MW120,000 4%15,000100,00010,000 57%80,000 29%60,000 9%5,00040,000 le gas030405060708Global cumulative installed wind capacity 1996–2013MW350,000300,000250,000200,000150,000 27%100,00050,00003025 38%201510 25%5002030405060708091011122013Source: US Renewable Fuels Association (annual capacities) after 1999 and SRI (from 1990); Industry reports; McKinsey analysis7020910112012WindGas production from shale gasBillion cubic feet per day2000 0101Business Development – BioAgriculture – Biomass Conversion – Animal Health & Nutrition200001020304050607 23%08091011122013
Significant learnings in first biomass conversion plants and the example of the US 1Gindustry suggest that Capex will reduce for the next wave of biomass conversion plantsMajor reasons for reduced Capex:Capex development over timeExample: 1st generation corn ethanol plants in the U.S. Optimized plant and process designincluding less over-engineering Development of standard modules400Capex, USD (2005) / m3 Bolt-on solutions use existinginfrastructure and 0350400Plant production capacity 1,000 m3 / yearSource: Data: LeBlanc and Prato, 1982, Gavett et al.1986, Whims, 2002, Understanding the reductions In UScorn ethanol production costs8Business Development – BioAgriculture – Biomass Conversion – Animal Health & Nutrition450
In spite of existing challenges, we see a solid project pipelinethat continues to mature across regionsWhile several biomass conversionethanol plants are already operating,more than 20 solid biomass conversionprojects are under developmentglobally (not all publicly announced) Publicly announced, commercial biomass conversionprojects under development by region (Q1/2015)*Project ItalyProject AlphaDifferent business models: Co-marketing with BetaRenewables Project development Large strategic partners e.g.Raízen*Non-exhaustive9Business Development – BioAgriculture – Biomass Conversion – Animal Health & NutritionTeck GuanPunjab
Major improvements in Novozymes’ enzyme technology have been a key enabler ofbiomass conversion commercialization and will drive further plant optimization 10080Enzymeuse costsdevelopment(indexed)6040200 everity2008Enzymedosing2009Cellic CTecTotal solidsloading2010Cellic CTec22012Cellic CTec32015CustomizedCellic 1.0Hydrolysis Biomass to sugarconversiontimeBusiness Development – BioAgriculture – Biomass Conversion – Animal Health & Nutrition2018YearsSweet spotoptimized to getthe lowest unitcost of ethanolCustomized Cellic enzymetechnology: Further improvement isachieved through customization ofenzymes to match specific processand feedstockEnzymes as a valuable tool:Sweet-spot optimized enzyme dosingensures the lowest unit cost of ethanolcost. For example, improved enzymeperformance has been shown to reducethe use of acid in pretreatment
Novozymes biotech solutions continue to bolster biomass conversionprocess optimization and its competitivenessNovozymes launches new family ofcustomized Cellic enzymestailored to reduce enzyme cost andimprove production performancePretreatment HydrolysisFermentationOngoing optimization of all processsteps will further reduce productioncostsNew customized Cellic solutions and further process optimizations continue toreduce biomass conversion costsCellulosic ethanol production costs Cellic CTec3Note: Based on NREL acid pretreatment process11Business Development – BioAgriculture – Biomass Conversion – Animal Health & NutritionCustomized Cellic solutionsCustomized Cellic Cellic solutionssolutionsCustomized further processe.g.further optimizationsprocessyeaste.g. yeastoptimizations
Customer-centric Novozymes Cellic enzyme development– tailored to the individual process and feedstock Diverging processes with differentfeedstocks are being established atindustrial scaleFor every combination of processand feedstock, there will be anoptimal enzyme systemEvery enzyme system benefits fromoptimization work BiomassPretreatmentBiomass after cid40%AlkaliEnergycropsBagasse20%Org. solventsCornstover12TailoredCellic solutions0%WheatstrawBusiness Development – BioAgriculture – Biomass Conversion – Animal Health & NutritionCelluloseHemicelluloseLignin
Customized Cellic enzyme solutions;process, feedstock, temperature and pH Key benefits vs. Cellic CTec3Yield boost – Improved hydrolysis performance on xylan-richsubstrates Robust activity – Broader pH and temperature profiles providerobust activity Contamination control – Higher hydrolysis temperature andlower pH inhibit contamination Lower OPEX – Reduced base consumption and waste treatmentcosts CustomizedCellic % conversion Cellic CTec3 What’s next? Adapt customization to evolving partner processes Continue optimization efforts together with partners – to drive outcost not only of enzymes but also of process and potential CapexEnzyme-relative dose13Business Development – BioAgriculture – Biomass Conversion – Animal Health & Nutrition
E2G ProgramJoão Alberto F. de Abreu
Agenda Introduction to Raízen Raízen's strategy How 2G fits into this Current status on Raízen's 2G efforts Learnings from plant #1 (in broad terms) Obstacles to overcome for the industry/Raízen Opportunities and plans for the future
RaízenLubrificantesCosan Lubrificantes eespecialidadesDownstreamUpstream
Business dimensionsWorld’s largest sugar producer andBrazil’s largest sugarcane ethanol producer915,000 ha2 bi litersof cultivated areaof ethanol96%941 MWmechanized harvestingof installed capacity4 m tonsof sugar
Fuel distributionA highly efficient and reliable network524591060Retail stationsConvenience storesDistribution depots58 Airports bases23,6 Billion m³
19Raízen – general numbers in 2013/14World cane crushing (mln land1107ºPakistan504ºChina8ºAustralia32* Source: LMC.100
Ethanol, sugar and bioenergyStrategic driversAspiration:Lower cost of production per sugarcane tonesCost reductionProductivityROACEX%Business driversPortfólio managementBiomassHSSEEnablersPeopleCrushing65,4MM TC
Ethanol, sugar and bioenergyProductionGreenfield in GO4,1 MtcJAT2,9 MtcFernandópolisVotuporangaJunqJalesGasa11,1 MtcAndradinaCADracenaCatanduvaDestBenMund AraçatubaUniv11,3 MtcJaboticabalAraraquara10,9 MtcPres.VenceslauBonfRibeirão PretoTamLinsTupãFrancaMaríliaPres. PrudenteBaurúPar49 Km tuIpau12,1 MtcS. J. daBoa VistaLimeiraMogiCoPiMirimUSHUBRPiracicabaRafIASF Campinas23 KmGreenfield in MS2,3 MtcOrlândiaBarretosS. J. doRio PretoGal. SalgadoAvaré1234567São Francisco, Rafard, Bom Retiro, Santa Helena, Costa PintoParalcool, Tarumã, Maracaí, IpaussuGasa, Univalem, Destivale, Mundial, Benálcool, JunqueiraJataíCaarapóSorocabaSão PauloMogidas CruzesSantosIlha de São SebastiãoSantos Port(Ilha Bela)ItapevaBarra, Dois Córregos, DiamanteBonfim, Tamoio, Serra, ZaninPindamonhangaba12,0 MtcItapetininga24 MillsGuaratinguetáBragançaPaulistaRegistro
Tops & leaves can be the main feedstock for 2G ifthe industry overcomes logistics challengesMechanization process has been increasingsignificantly and has reached 65% inindustryNot burning means extra 45M ton ofbiomass available in the industry.Two process must be selected :Bring biomass togethersugarcaneBales collection systemwiththe
Potential of biomassEthanol production per hectareSUGARJUICECANE STALKETHANOLMILL23,8 tons85 tonsBAGASSEDRY LEAVES14,1 tonsGREEN LEAVESTOPSBIOMASSExtra 2 m3ETHANOLMax. 7 a 8 m3
Integration opportunitiesPlug & play 2G with a 1G plantOpportunitiesSteam/Power SupplyBiomass HandlingC6 FermentationDistillationWater / Vinasse Utilities120 MM Liters1. Retrofit of an existing boiler instead of installing a new boiler.2. Lignin burning supplies steam and power required by 2G process.1. Synergies with existing assets;2. Existing know-how.1. Existing know-how.1. Synergies with existing assets;2. Existing know-how.1.2.3.4.Synergies with 1G water balance (final molasses dilution);Retrofit of existing vinasse disposal system;Existing know-how about vinasse disposal.Operational synergies between 2G and 1G process (utilities, ligninhandling, offices, warehouse, maintenance, etc.)
Sugarcane segment scenario in BrazilEnormous changes since 2009Number of new production unitsin the Centre-South regionMore than 50 kMT of crushing capacity lostNumber of closed mills
Brazilian matrix of fuelProjections 2020-2025Sugarcane (million tons)201564120206002025650Sugar (million tons)Exportation assumption35,624,440,528,846,334,0Ethanol (billion liters)Anhydrous 670,340Available ATR (million tons)SupplyDemandVolume gapSugar (million tons)EtoH anhydrous (billion liters)Fuels (billion liters)Current gasoline (EPE)Gasoline demandVolume gap30,644,714,231,454,122,7Even considering no hydrous ethanol supply,sugarcane volume is slightly lower thanmarket requirementsConservative importation volume (low fuelconsumption growth and decreasing Braziliansugar global market share)
Project E2G COPI (Costa Pinto)Located inCosta Pinto MillPiracicaba, SPCapacity: 42.200 m3/yearCapex: 230 MM R Commissioning:Out/2014 – C6 Fermentation;Out/2015 – C5 Fermentation.
E2G plantProject details Construction area:10.000m² 30.000m² for biomass storage*. * Biomass storage area considers existing one. Budget: R 230MM. Contractors: average 200 with a peak of 500. 800.000 working hours with no lost time incident Timing : 14 months. Equipments: 98% produced in Brazil.
2014 operationMain achievements All process units in E2G plant tested; Biomass handling and storaging as expected; Perfect integration between E2G plant and existing mill; Successfull technology scale up from demo to commercial scale; Enzyme logistics validated; Process Control implemented and tested.
Movie
2014 operationAction plan based on learnings Evaluation of process and equipment performance; Evaluation of main operation issues; erosion Process optimization in order to reach maximum capacity; Implement improvements based on lessons learned; Commissioning of dedicated boiler for E2G plant.
ChallengesFermentation Develop GMO yeast to produce ethanol from C5 (xylose); Choosing best fermentation design (once-through vs recycle); Develop process/equipment for yeast propagation on-site; Operation according to GMO regulation (CTNBio); Fermentation engineering and construction.
E2G roadmapPlan1 billion literstechnology licensing2014COPI2012Demonstration-Biomass Trial;- Technology Validation;- Project Starts.- COPI Operation;- TechnologicalPlatform Advances;- Progress ofInnovation Program;- Begin 2nd PlantDesign- 8 integrated plants;- Technology Licensing;- Technology tomaximize biomasseconomics;- Integration withChemical plants.SecondGen.Ethanol
Current land use in BrazilSugarcane for ethanol occupies less than 1% of the Brazilian land massTotal AreaMillions of HectaresProtected & NativeArable rcane51.78.14
Production mapSugarcane in Brazil35
Bonsucro certificationOnly international certification for sugar and ethanol madeform sugarcaneBonsucro:Raízen: 1st certified mill in the world 10 mills already certified: Maracaí, Jataí, Costa Pinto, BomRetiro, Bonfim, Univalem, Gasa, Dois Córregos, Junqueiraand Serra. Non-profit organization with 176 members of variouscountries and sectors: agricultural producers, mills,consumers, NGOs, tradersMulti-stakeholder process to measure, through metricindicators, the environmental, social and economicperformance of sugarcane-based activitiesChosen by the EU as one of seven authorized schemes toallow for the export of sugarcane products to Europe 32,1% of total sugarcane crushed by the company 712,000 m³ of ethanol Member of Bonsucro’s executive board Commitment to certify all mills
CO2 emissions2G improves the carbon footprint of RaízenGasolineEthanol 1GEthanol 2G
Conclusion Biomass conversion remains a transformative opportunity Getting biomass conversion off the ground has taken longertime than anticipated Steady improvements and significant progress made over last2 years Ramp-up process key to biotechnology development andindustry commercialization38Business Development – BioAgriculture – Biomass Conversion – Animal Health & Nutrition
optimizations beyond enzymes. Our customized next . Ben Ipau Tar Mar Par 49 Km Diam DC Barra ZaninSerra Tam Km UBR Raf IASF USH CoPi 11,1 Mtc 11,3 Mtc 12,0 Mtc 12,1 Mtc Greenfield in MS 2,3 Mtc 10,9 Mtc 2,9 Mtc Greenfield in GO .