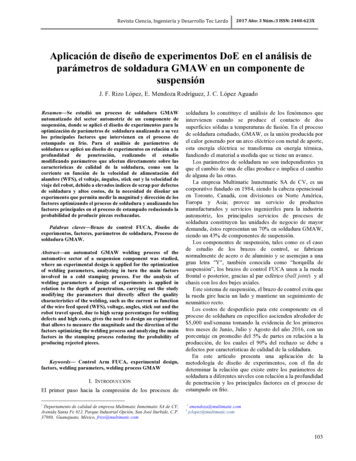
Transcription
Revista Ciencia, Ingeniería y Desarrollo Tec Lerdo2017 Año: 3 Núm.:3 ISSN: 2448-623XAplicación de diseño de experimentos DoE en el análisis deparámetros de soldadura GMAW en un componente desuspensiónJ. F. Rizo López, E. Mendoza Rodríguez, J. C. López AguadoResumen—Se estudió un proceso de soldadura GMAWautomatizado del sector automotriz de un componente desuspensión, donde se aplicó el diseño de experimentos para laoptimización de parámetros de soldadura analizando a su vezlos principales factores que intervienen en el proceso deestampado en frío. Para el análisis de parámetros desoldadura se aplicó un diseño de experimentos en relación a laprofundidad de penetración, realizando el estudiomodificando parámetros que afectan directamente sobre lascaracterísticas de calidad de la soldadura, como son lacorriente en función de la velocidad de alimentación delalambre (WFS), el voltaje, ángulos, stick out y la velocidad deviaje del robot, debido a elevados índices de scrap por defectosde soldadura y altos costos, da la necesidad de diseñar unexperimento que permita medir la magnitud y dirección de losfactores optimizando el proceso de soldadura y analizando losfactores principales en el proceso de estampado reduciendo laprobabilidad de producir piezas rechazadas.Palabras claves—Brazo de control FUCA, diseño deexperimentos, factores, parámetros de soldadura, Proceso desoldadura GMAW.Abstract—an automated GMAW welding process of theautomotive sector of a suspension component was studied,where an experimental design is applied for the optimizationof welding parameters, analyzing in turn the main factorsinvolved in a cold stamping process. For the analysis ofwelding parameters a design of experiments is applied inrelation to the depth of penetration, carrying out the studymodifying the parameters that directly affect the qualitycharacteristics of the welding, such as the current as functionof the wire feed speed (WFS), voltage, angles, stick out and therobot travel speed, due to high scrap percentages for weldingdefects and high costs, gives the need to design an experimentthat allows to measure the magnitude and the direction of thefactors optimizing the welding process and analyzing the mainfactors in the stamping process reducing the probability ofproducing rejected pieces.Keywords— Control Arm FUCA, experimental design,factors, welding parameters, welding process GMAWI. INTRODUCCIÓNEl primer paso hacia la compresión de los procesos de1Departamento de calidad de empresa Multimatic Inmetmatic SA de CV,Avenida Santa Fe #12, Parque Industrial Opción, San José Iturbide, C.P.37980, Guanajuato, México, frizo@multimatic.comsoldadura lo constituye el análisis de los fenómenos queintervienen cuando se produce el contacto de dossuperficies sólidas a temperaturas de fusión. En el procesode soldadura estudiado, GMAW, es la unión producida porel calor generado por un arco eléctrico con metal de aporte,esta energía eléctrica se transforma en energía térmica,fundiendo el material a medida que se tiene un avance.Los parámetros de soldadura no son independientes yaque el cambio de una de ellas produce o implica el cambiode alguna de las otras.La empresa Multimatic Inmetmatic SA de CV, es uncorporativo fundado en 1984, siendo la cabeza operacionalen Toronto, Canadá, con divisiones en Norte América,Europa y Asia; provee un servicio de productosmanufacturados y servicios ingenieriles para la industriaautomotriz, los principales servicios de procesos desoldadura constituyen las unidades de negocio de mayordemanda, éstos representan un 70% en soldadura GMAW,siendo un 43% de componentes de suspensión.Los componentes de suspensión, tales como es el casode estudio de los brazos de control, se fabricannormalmente de acero o de aluminio y se asemejan a unagran letra "Y", también conocida como “horquilla desuspensión”, los brazos de control FUCA unen a la ruedafrontal o posterior, gracias al par esférico (ball joint) y alchasis con los dos bujes axiales.Este sistema de suspensión, el brazo de control evita quela rueda gire hacia un lado y mantiene un seguimiento deneumático recto.Los costos de desperdicio para este componente en elproceso de soldadura en específico ascienden alrededor de 5,000 usd/semana tomando la evidencia de los primerostres meses de Junio, Julio y Agosto del año 2016, con unporcentaje en promedio del 5% de partes en relación a laproducción, de los cuales el 90% del rechazo se debe adefectos por características de calidad de la soldadura.En este artículo presenta una aplicación de lametodología de diseño de experimentos, con el fin dedeterminar la relación que existe entre los parámetros desoldadura a diferentes niveles con relación a la profundidadde penetración y los principales factores en el proceso deestampado en com103
Revista Ciencia, Ingeniería y Desarrollo Tec LerdoII. PARTE TÉCNICA DEL ARTÍCULOLos modelos de diseño de experimentos son modelosestadísticos clásicos cuyo objetivo es averiguar si unosdeterminados factores influyen en una variable de interés y,si existe influencia de algún factor, cuantificar dichainfluencia.La metodología del diseño de experimentos se basa en laexperimentación. Se sabe que si se repite un experimento,en condiciones indistinguibles, los resultados presentan unacierta variabilidad.A. Proceso de soldadura GMAWEl proceso GMAW puede usar equipos semiautomáticoso automáticos en aplicación de la soldadura de altaproducción. La mayoría de los metales pueden ser soldadoscon este proceso, y más aún pueden ser soldados en todaslas posiciones utilizando las variaciones de baja energía delmismo.El estudio sobre el comportamiento de la soldadura en lapieza de suspensión, una característica de profundidad depenetración sobre la lámina 2 resulta interesante en lacalidad de la soldadura, que refleja la resistencia que éstava a soportar al ser sometida a un esfuerzo dinámico.Los parámetros de soldadura que en forman parte de lascaracterísticas de la calidad de soldadura son: Tensión (voltaje) Velocidad de alimentación Extensión del electrodo o stick-out Velocidad de desplazamiento Ángulo de inclinación de la pistola Gas de protección Calor de entradaB. Proceso de troqueladoEs el conjunto de operaciones con las cuales sin producirviruta, sometemos una lámina plana a ciertastransformaciones a fin de obtener una pieza de formageométrica propia, este trabajo se realiza con troqueles enmáquinas llamadas prensas (generalmente de movimientorectilíneo alternativo).La Tabla I y II muestran el material especificado porcliente GMW3032M-ST-S-HR420LA es una acero de bajaaleación de alta resistencia a la cedencia desde 180 MPahasta los 700 MPa, y si es aplicable el recubrimiento depintura o no, con un proceso de laminación en frío.TABLA ICOMPOSICIÓN QUÍMICA DE ACEROS DE BAJA ALEACIÓN DE ALTARESISTENCIA2017 Año: 3 Núm.:3 ISSN: 2448-623XTABLA IIPROPIEDADES MECÁNICAS DE ACEROS DE BAJA ALEACIÓN DE ALTARESISTENCIAC. Diseño de experimentosLos modelos de diseño de experimentos son modelosestadísticos clásicos cuyo objetivo es averiguar si unosdeterminados factores influyen en una variable de interés y,si existe influencia de algún factor, cuantificar dichainfluencia.El análisis estadístico se basa en un modelo estadísticoformal subyacente. La interpretación adecuada del análisisrequiere la comprensión del modelo.D. Diseño factorialLos diseños factoriales producen experimentos máseficientes, pues cada observación proporciona informaciónsobre todos los factores, y es factible ver las respuestas deun factor en diferentes niveles de otro factor en el mismoexperimento.El diseño factorial se puede usar para evaluar si laactuación de los factores es independiente a la profundidadde penetración de los especímenes de prueba. En la tabla IVse ilustra el arreglo factorial para los especímenes de pruebapreparados con dos métodos de compactación (alto y bajo)usando cuatro factores.TABLA IIICORRIDAS DEL DISEÑO FACTORIAL FRACCIONADOStdOrder RunOrder CenterPt Blocks WFS TS Trim Gap1111300 25 0.902211550 25 0.9 2.23311300 42 0.9 2.24411550 42 0.905511300 25 1.04 2.26611550 25 1.04 07711300 42 1.04 08811550 42 1.04 2.2El objetivo de correr un diseño factorial fraccionado esreducir el número de corridas identificando las variablessignificativas del diseño. Así mismo se puede identificaralgunas respuestas preliminares que nos muestra elexperimento.E. Modelo TaguchiLos diseños experimentales de Taguchi (ver Tabla IV),están basados en arreglos ortogonales y se hicieron104
Revista Ciencia, Ingeniería y Desarrollo Tec Lerdopopulares por el ingeniero Genichi Taguchi. Normalmentese identifican con un nombre como L8, que indica unarreglo con 8 corridas.Los factores críticos que se seleccionaron para estametodología son: a) velocidad de alimentación del alambre;b) velocidad de viaje; c) voltaje (trim); d) Stick out; e)ángulo de ataque; f) ángulo de trabajo. Los nivelesseleccionados se muestran en la tabla 5.El diseño de Taguchi se elaboró en el software minitab17, donde se introdujeron los seis factores con susrespectivos niveles.La medición de la profundidad de penetración comoúnica variable de respuesta se da a través de unapreparación metalográfica con un ataque químico con nitalal 20%.2017 Año: 3 Núm.:3 ISSN: 2448-623Xdiferentes celdas designadas M10, M20, , M60. Verfigura 1.Los dos principales defectos de soldadura, mostrados enel diagrama de pareto, son el socavado y la perforación, queestán directamente relacionados a los parámetros desoldadura y a la preparación del material base en losherramentales de las celdas.TABLA IVCORRIDAS DEL DISEÑO DEL MODELO .580.250.630.280.22WFS TRIM TS Stick Out A Ataque A trabajo330 0.92 2810345330 0.92 2810550330 0.92 28101055330 0.95 3515345330 0.95 3515550330 0.95 35151055330 1.00 3919345330 1.00 3919550330 1.00 39191055400 0.92 3519350400 0.92 3519555400 0.92 35191045400 0.95 3910350400 0.95 3910555400 0.95 39101045400 1.00 2815350400 1.00 2815555400 1.00 28151045480 0.92 3915355480 0.92 3915545480 0.92 39151050480 0.95 2819355480 0.95 2819545480 0.95 28191050480 1.00 3510355480 1.00 3510545480 1.00 35101050Figura 1. Diagrama de pareto de defectos de soldadura.B. Variabilidad del proceso de troquelado de estampadosEn el proceso de troquelado la zona que permite tener unapreparación correcta sin generar un tamaño de abertura(gap) en exceso que afecte la aplicación de la soldadura esla superficie donde está colocado el anillo donde vansujetados dos bujes axiales.En el análisis de variabilidad de las dimensiones de lasuperficie en el proceso de troquelado fue de una corrida de3000 piezas tomando un muestreo cada 100 en 100 hastaterminar.III. RESULTADOSA. Variabilidad del proceso de GMAW del brazo decontrolPara determinar la variabilidad del proceso de soldaduraGMAW del brazo de control se contó con una base de datosde las diferentes resultados de piezas que fueron analizasuna vez que fueron rechazadas de las celdas de seisFigura 2. Análisis de varianzas en relación del trim de la superficie delestampado superior con respecto al gap.105
Revista Ciencia, Ingeniería y Desarrollo Tec LerdoFigura 3. Fotografías y macrografías de soldadura de variación de gap enrelación a los parámetros elegidos.En el análisis de varianzas se determinó que la suma delas tres zonas resulta en un 71.8% de probabilidad enrelación lineal, que al disminuir la dimensión del trim(quiere decir que aumentó la fluidez del material en elestampado), el gap que se genere en el sub ensamble delestampado superior/estampado inferior aumentará su valor,esto en el caso de las zonas 1 y 3. En el caso de la zona 2 noimpacta en la condición final del gap.El estudio para determinar el gap máximo permisible serealizó una prueba de soldar partes variando el gap hastallegar a 2.0 mm con la finalidad de obtener un estimado dela calidad de la soldadura a diferentes cantidades de tamañode gap a los parámetros establecidos.2017 Año: 3 Núm.:3 ISSN: 2448-623Xerror da finalmente un tamaño de gap máximo de 1.08 mmpara asegurar el mínimo tamaño de pierna vertical, asímantiene en un estado aceptable los otros requerimientosmedidos.Para obtener el tamaño máximo de gap de 1.08 mm deacuerdo a la figura 12, es necesario designar los controlesnecesarios de la superficie del estampado para la zona 1serían de 2.20 mm a 2.80 mm y para la zona 3 de 2.20 mma 2.9 mm y finalmente dejando a la zona 2 con 2.40 mm a2.90 mm. Las modificaciones del troquel fueron realizadaspara asegurar estas dimensiones.Finalmente se realizó un monitoreo del porcentaje derechazo total de las celdas en el transcurso de un año dejunio 2016 a junio 2017 con la finalidad de observar lareducción de éste en el momento de implementación de laoptimización de parámetros de soldadura a finales de enero2017.La gráfica de porcentaje de rechazo de partes tiene unatendencia de disminución a partir de donde se comenzarona tomar acciones en agosto 2016 a enero 2017 manteniendoun promedio de 2.3% de rechazo en relación a la produccióny un promedio de 1.3% se redujo después de laimplementación de la optimización de parámetros desoldadura en febrero a junio 2017 manteniendo unpromedio de 1.00 % de rechazo.Figura 5: porcentajes de rechazo mensual de piezas del brazo de controlFUCA.C. Resultados corrida DFFLos datos de la profundidad de penetración en el estudiopreliminar de las corridas que se elaboraron en el DFF,donde se colocaron las ocho corridas y se tomaron en cuentatres aplicaciones de soldadura dando una profundidad depenetración promedio para los resultados del diseñopreliminar con 4 factores.Figura 4. Gráficas de correlación lineal de tamaño de gap en relación alas diferentes características medidas de calidad de la soldadura.De acuerdo a lo obtenido el efecto del gap sobre lasoldadura es directamente proporcional al tamaño de lagarganta, tamaño de la pierna vertical y a la profundidad desocavado que lo limita al 30% del espesor del material. Losresultados representan que al aumentar el tamaño de gap seven afectados estas tres características tomando dereferencia máxima de 1.26 mm de gap menos el 14% deFigura 6. Corridas y profundidad de penetración del DFF.106
Revista Ciencia, Ingeniería y Desarrollo Tec Lerdo2017 Año: 3 Núm.:3 ISSN: 2448-623XFigura 7. Fotografías y macrografías de soldadura de las corridas delDFFDel análisis de inspección visual de los cordones desoldadura se puede observar que la muestra 1 no presentafusión en el canto ni hundimiento con respecto a los demás,pero se ve afectada la profundidad de penetración por lo quese buscaría un valor objetivo de al menos el 50% al 70% enrelación a sus espesor de 2.1 mm.Se realizó el análisis ANOVA para determinar cuál es elefecto principal y significativo que afecta a la profundidadde penetración (ver figura 8). Los P-Values menores a 0.05indican los factores significativos. La velocidad dealimentación del alambre (WFS) con un valor de 0.006 fueel único valor significativo en esta corrida con unatendencia lineal a la profundidad de penetración.Figura 8. Análisis de varianzas y gráfica de pareto sobre la profundidadde penetración en la corrida DFF.El valor objetivo de la profundidad de penetración seráde 50% a 70%, los cuales se mantendrá a una velocidad dealimentación del alambre de 400 a 450 IPM.D. Resultados corrida modelo TaguchiEl 83.03% de la variación de la respuesta “profundidadde penetración” (ver figura 9) es explicada por el modelo.Acorde a los valores que se escogieron como meta del 50%al 70% y un valor en específico de 1.26 mm se elige WFS:400 IPM, TS: 32 IPM, Trim: 1, Stick Out: 15 mm, ángulode ataque: 5 y un ángulo de trabajo de 45 , es acorde a lascinco alternativas que reporta el minitab 17 en su resultadode regresión múltiple lineal de proyección y optimización.Figura 9. Corridas y profundidad de penetración del método Taguchi.IV. CONCLUSIÓNCon esta investigación se cumplió el objetivo general,donde se encontraron los factores significativos del procesode soldadura del brazo de control FUCA aunado a losparámetros óptimos que redujeron la probabilidad deproducir piezas rechazadas por un defecto de soldadura loscuales fueron:WFS 400 IPMVelocidad de viaje 32 IPMTrim 1.00Stick out 15 mmÁngulo de ataque 5 Ángulo de trabajo 45 Perfil de superficie en estampado superior 2.2-2.8 mm(zona 1); 2.4-2.9 mm (zona 2); 2.2-2.9 mm (zona 3) Tamaño máximo de gap 1.08 mm Para evitar generar piezas rechazadas se debe establecery mantener los niveles óptimos encontrados, en el procesode soldadura GMAW del brazo de control FUCA.Se redujo el porcentaje de piezas desechadas promediode 2.3% pasando a un promedio de 1.0% con laoptimización de parámetros. El costo generado del 2.3% esdel 14,000 usd/mes fue reducido a 6,500 usd/mes. Alfinal del año 2017 se estima un ahorro con laimplementación del cambio de parámetros en un total de 82,500 usd.107
Revista Ciencia, Ingeniería y Desarrollo Tec LerdoV. AGRADECIMIENTOSAgradecemos a la empresa Multimatic Inmetmatic por elapoyo recibido mediante el financiamiento al proyecto dela aplicación de un diseño de experimentos en las partesdescritas como brazo de control FUCA.VI. An American National Stándard. (2001). Standard Welding Termsand Definitions. ASW A3.0.Ferjutz, K.; Devis J. R. (1993). Welding brazing and soldering,Metals. ASM Handbook, Vol 6. Park, Ohio: ASM International.Fisher, R.A. (1990) Introduction to “The Arrangement of fieldexperiments”. Technical report, No 253, California.Granjon, H. Fundamentals of welding metallurgy. Cambrige:Woodhead Publishing., 1991.Jeffus F. Welding: Principles and Applications. Clifton Park. NewYork, Dekmar Cengage Learning. 2002Kah, P. Welding of sheet metal using modified short arc MIG/MAGwelding process. Finland, 2007.Kavanaugh, C. Los diseños de Taguchi contra los diseños clásicosde experimentos. Conciencia Tecnológica, núm. 19. InstitutoTecnológico de Aguascalientes Aguascalientes, México. abril,2002.Manual de Soldadura EXSA-OERLIKON Edición 1995.Montgomery, D. Diseño y análisis de experimentos. 2da edición.Limusa Wiley. Arizona, 2004.O’Brien, R. Welding Handbook: Welding Processes. 8th Edition;Miami: American Welding Society. ISBN 0-87171. 1991.Orellana, L. Regresión lineal. Mexico, 2008.Tanco, M. Practical applications of design of experiments in thefield of engineering. John Wiley & Sons, Ltd. 2008.2017 Año: 3 Núm.:3 ISSN: 2448-623Xrobótica, PLC, maquinados. Su línea de investigación está en el ajuste eintegración de programas automatizadosIng. Mendoza, capacitaciones en integración de robots, mantenimientos acontroladores, programación de robots.López Aguado Juan Carlos. Nacimiento en laciudad de Celaya, Guanajuato el 31 de Enero del1980. Estudió la carrera de Ingeniería Mecánicaen el Instituto Tecnológico de Celaya en los añosde 1997 al 2001, cuenta con una Maestría enCiencias de Ingeniería Mecánica en el ITC en losaños 2003-2005.Actualmente labora en una empresa de autopartesllamada Inmetmatic Multimatic SA de CV en el estado de Guanajuatocomo Gerente de Producción desde noviembre del 2012.Su experiencia desde el 2005 fue en la industria automotriz depempañandodiferentes funciones de ingeniero y gerente. Su línea de investigación estáen la optimización de procesos de soldadura.M. en C. López, Capacitaciones en administración, procesos de soldadura,resolución de problemas, liderazgo.VII. BIOGRAFÍARizo López José Francisco. Nacimiento en laciudad de Guadalajara Jalisco el 5 de septiembre de1988. Estudió la carrera de Ingeniero Químico enMateriales en la facultad de química de laUniversidad Autónoma de Querétaro en los años de2008 al 2012.Actualmente labora en una empresa de autopartesllamada Inmetmatic Multimatic SA de CV en elestado de Guanajuato como Ingeniero de Soldadurasiendo responsable del laboratorio de pruebas desdemarzo del 2015. Su experiencia desde el 2012 fue como responsable dellaboratorio en diferentes giros metal mecánico en la industria. Su línea deinvestigación está en la optimización de procesos de soldadura con el usode herramientas estadísticas.IQM Rizo, Inspector de Soldadura Certificado por la Sociedad Americanade Soldadura. Capacitaciones en core tools, procesos de soldadura,tratamientos térmicos, resolución de problemas, materiales.Mendoza Rodríguez Elias. Nacimiento en laciudad de San Luís de la Paz, Guanajuato el 18 deJunio del 1987. Estudió la carrera de IngenieroMecatrónica en el Instituto Tecnológico deQuerétaro en los años de 2005 al 2010.Actualmente labora en una empresa de autopartesen el estado de Guanajuato como Ingeniero deSoldadura siendo coordinador de mantenimientodesde Febrero del 2013. Su experiencia desde el 2010 fue como integrador108
En el análisis de variabilidad de las dimensiones de la superficie en el proceso de troquelado fue de una corrida de 3000 piezas tomando un muestreo cada 100 en 100 hasta terminar. Figura 2. Análisis de varianzas en relación del trim de la superficie del estampado superior con respecto al gap.