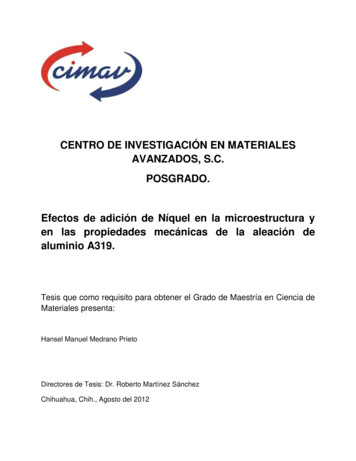
Transcription
CENTRO DE INVESTIGACIÓN EN MATERIALESAVANZADOS, S.C.POSGRADO.Efectos de adición de Níquel en la microestructura yen las propiedades mecánicas de la aleación dealuminio A319.Tesis que como requisito para obtener el Grado de Maestría en Ciencia deMateriales presenta:Hansel Manuel Medrano PrietoDirectores de Tesis: Dr. Roberto Martínez SánchezChihuahua, Chih., Agosto del 2012
Agradecimientos y Reconocimientos.Es para mi un placer, hacer un reconocimiento a todas las personas quecolaboraron para llevar a cabo este trabajo de investigación, a los técnicosde los laboratorios de CIMAV, a los maestros y amigos.Un especial reconocimiento a mi asesor de tesis, Dr. Roberto MartínezSánchez, por sus grandes aportaciones en mi enseñanza.También quiero agradecer y dedicar este trabajo mi esposa, mi hijo y a mifamilia quienes son los fuertes pilares en mi vida.ii
Índice.1.-Resumen.32.-Introducción.43.-2.1Las aleaciones Al-Si.42.2Efecto de los principales elementos aleantes en las aleaciones dealuminio.92.3Efecto del refinador de grano en la microestructura.112.4Modificador de morfología del silicio eutéctico.122.5Tratamiento térmico de endurecimiento por precipitación.122.6Etapas del Tratamiento térmico 6.3Esferoidización de partículas de Si eutéctico.142.6.4Temple.152.6.5Envejecimiento o tratamiento térmico de precipitación.162.6.6Secuencia de precipitación.162.7Elementos con aplicaciones especiales en las aleaciones dealuminio.182.8Empleo de Ni en las aleaciones de Aluminio.18Materiales y Métodos.213.1Fabricación de aleaciones.213.2Etapa Tratamientos Térmicos233.3Etapa Microscopía Óptica243.4Etapa ensayo de Dureza.253.5Etapa ensayo de Microdureza Vickers [VHN].25i
4.-5.-3.6Etapa Microscopía Electrónica de Barrido263.7Etapa de Difracción de Rayos X27Resultados y Discusión.284.1Microscopía Óptica.284.2Microscopía Electrónica de Barrido414.3Ensayo de Dureza [HRB].554.4Ensayo de Microdureza Vickers [VHN].624.5Difracción de Rayos X.704.5.1Cálculo del parámetro reticular de la fase de aluminio.75Conclusiones.78Referencias.79Anexos A,B82ii
1.-Resumen.La aleación de aluminio 319, es ampliamente utilizada en la industria automotriz, para lafabricación de monobloques y cabezas de motores de combustión interna, debido a suaplicación, requiere de excelentes propiedades mecánicas.Mediante la aplicación de tratamientos térmicos en combinación con adiciones deelementos de aleación, se logra incrementar sus propiedades mecánicas.En este trabajo de investigación, se fabricaron aleaciones mediante fundición, conpequeñas adiciones de níquel (0.5, 1, 1.5 y 2%) en la aleación de aluminio (A319)comercial, se realizaron tratamientos térmicos de envejecimiento T6 (endurecimientopor precipitación), para mejorar la propiedad de dureza de la aleación.El tratamiento térmico T6, consistió de solubilizar las piezas a 495 C, por 3, 4, 5, 6 y 7h, temple en agua a 60 C y envejecimiento artific ial a 170 C, por 0.5, 3, 4, 5, 10 y 96h, seguido por temple en agua temperatura ambiente.Esta investigación se enfocó a estudiar el efecto de las adiciones de níquel, en lamicroestructura y propiedad mecánica de dureza de la aleación A319, mediante lastécnicas de caracterización de: microscopia óptica, microscopia electrónica de barrido,ensayos de dureza, microdureza y difracción de rayos x.Los mejores resultados de dureza y microdureza se obtuvieron con la composición de 1% Ni, con 3 h de envejecimiento artificial T6.3
2.- Introducción.El material que será efecto de estudio, es la aleación de aluminio 319 comercial. Estaaleación pertenece a la familia de aleaciones más popularmente utilizadas en laindustria automotriz. La aleación A319 se caracteriza por presentar excelentesmoldeabilidad y buenas propiedades mecánicas. Está basada principalmente en elsistema Al-Si y contiene Cu como principal elemento de aleación además del Si. Estaaleación presenta también contenidos de Mg y algunos otros elementos en menorproporción como son Fe, Mn, Zn, Ni y Ti. [1]. La composición típica [2] en lasaleaciones 319 es mostrada en la Tabla 2.1Tabla 2.1.- Composición química estándar de la aleación 319.2.1.- Las aleaciones Al-Si.Las aleaciones Al-Si contienen de 4 % a 22 % de Si y comprenden más del 90 % de lasaleaciones fabricadas por moldeo. Las características más importantes de lasaleaciones Al-Si producidas por moldeo son sus propiedades mecánicas, la corrosión yla facilidad de moldeo. Estas propiedades están definidas por la composición química yla microestructura de la aleación. La microestructura está afectada por las condicionesde la fundición, el moldeo y las condiciones de los tratamientos térmicos empleados.Las aleaciones Al-Si sin contenido de Cu son empleadas cuando propiedades como lafacilidad de moldeo y resistencia a la corrosión son importantes. Si propiedades comodureza y resistencia mecánica son necesarias se les adiciona magnesio y pueden sertratadas térmicamente [3]. Estas aleaciones poseen baja resistencia y dificultad paramaquinarse, aunque la ductilidad y fluidez son de sus mejores propiedades [2].El contenido de Si va desde 4 % hasta 22 %, en este amplio rango se puede subdividiren tres intervalos: de 4 % a 9 %, 10 % a 13 % y de 14 % a 22 %, lo mostrado por elsistema binario Al-Si de la Fig. 2.1 [4], esto corresponde a aleaciones Hipo-eutécticas,eutécticas e hiper-eutécticas, Respectivamente [3,5]. El límite más bajo de contenidode Si (4 %) es usado cuando se quiere obtener un tiempo de solidificación relativamentecorto. El limite superior de concentración de Si, es usado cuando se quiere obtener unmínimo nivel de plasticidad debido a que las fases de Si disminuyen la ductilidad. Elcontenido de Si en la matriz de Al no excede de 1.0-1.5 %, el Si restante pasa a formarfases ricas en este elemento.4
Además del Si, los elementos aleantes básicos son el Cu y Mg, rara vez es utilizado Zny Ni como elementos de aleación. El principal objetivo de los elementos aleantes esincrementar las propiedades mecánicas como son, la resistencia mecánica y la dureza,aunque al incrementar estas propiedades disminuye la ductilidad de las aleaciones.Figura 2.1- Sistema binario Al-Si.Adiciones de cobre permiten lograr altos niveles de resistencia mecánica en lasaleaciones Al-Si en la condición de colada. La concentración de Cu puede alcanzarhasta 7-8 %. Sin embargo, de acuerdo al diagrama de fases Al-Cu [4] mostrado en laFig. 2.2, se recomienda utilizar como un máximo 4 %.Al mismo tiempo las fases que contienen Cu de origen eutéctico ejercen una influencianegativa muy fuerte en la plasticidad y otras propiedades mecánicas de la aleación.Después del tratamiento térmico de envejecido, el Cu disuelto en la matriz de aluminiopuede precipitar en forma de precipitados secundarios. En el caso del tratamientotérmico T6 son las fases metaestables θ’, θ" y la fase estable θ.5
Figura 2.2.- Sistema binario Al-Cu.La concentración de magnesio está dentro del intervalo de 0.2 % a 0.6 % y muy pocasveces excede el 1 %. El límite más bajo está definido por la necesidad de lograrsuficiente endurecimiento por dispersión debido a la precipitación de fasesmetaestables secundarias β' y β" (Mg2Si) de acuerdo a lo observado en el diagramade fases del sistema binario Mg-Si [4], mostrado en la Fig. 2.3. El límite superior debeasegurar una pequeña fracción de volumen de fases que contienen Mg de origeneutéctico (Mg2Si) para alcanzar un nivel de plasticidad. Entre lo elementos de aleación eimpurezas el magnesio ejerce la más fuerte influencia sobre las propiedades mecánicasdurante el tratamiento térmico de envejecido en las aleaciones Al-Si6
Figura 2.3- Sistema binario Mg-Si.El Hierro es usualmente una impureza, ejerce un efecto negativo en las propiedadesmecánicas de la aleación. La importancia del la influencia de las fases que contienenhierro esta definida por la morfología, tamaño y distribución de las mismas. El efectomás perjudicial es ejercido por la fase Al5FeSi (β) que son partículas en forma deagujas especialmente formadas después de la solidificación (cristales primarios).El manganeso forma el compuesto Al15(Fe,Mn)Si2, esta fase como una parte de lamicroestructura eutéctica posee una morfología de esqueleto. La presencia demanganeso permite evitar la formación de la fase Al5FeSi (β) partículas en forma deagujas. La concentración de manganeso en la matriz de aluminio es relativamentepequeña y típicamente en las aleaciones 3xx no excede de 0.5 %.Cuando en las aleaciones son empleados materiales con bajos contenidos deimpurezas, el Ni puede formar la fase Al3Ni. De acuerdo con [5] el diagrama ternario AlNi-Si Fig. 2.4, no se forma ningún compuesto ternario, solo hay tres fases en estadosólido, Al, Al3Ni y Si. La transformación de liquido a Al Al3Ni Si en estado sólidotoma lugar a los 557 C y la composición de Ni es d e 5 % con 11 a 12 % de Si.7
Figura 2.4.- Sistema ternario Al-Ni-Si.Cuando Ni y Cu están presentes en la composición de la aleación, se esperaríala formación de dos compuestos Al6Cu3Ni y Al3(Ni,Cu)2, lo cual resulta de lareducción de Cu de la matriz de Al, incluso después del temple.Cuando la concentración de Ni es al menos 4 % y la de Fe es menor a 1 % es muypoco probable la formación de cristales primarios de Al-NiEl Ni entra dentro de la composición de las aleaciones Al-SI para fabricar pistones demotores de combustión interna. Esto se explica debido a la influencia positiva del Ni enla estabilidad térmica y en el coeficiente de expansión térmico [5].Las aleaciones A319, son consideradas las más populares en el sistema Al-Si-Cu, porque poseen un amplio intervalo de aplicaciones en la industria automotriz, aeroespacialy militar [6]. Las cuales se caracterizan por su alta capacidad para moldearse tanto enmoldes permanentes como en moldes de arena [7]. Poseen una alta relación pesoresistencia, alta resistencia a la corrosión y excelente conductividad térmica [8].Las principales aplicaciones dentro de la industria automotriz, son la fabricación demonoblock, pistones y cabezas entre otras piezas del motor de combustión interna. Eluso de esta aleación dentro de esta industria es debido a su capacidad de fácil moldeo,alta maquinabilidad y bajo peso [7]. Las aleaciones Al-Si son ampliamente usadasdebido a que se pueden obtener componentes con geometrías complejas, propiedad8
que da el Si [9], además de mostrar propiedades mecánicas adecuadas para laaplicación automotriz.Las aleaciones A319 utilizadas frecuentemente en la industria automotriz, suelen serusadas tanto en condición de colada como tratadas térmicamente. El propósito deltratamiento térmico en esta aleación es obtener la mejor combinación de resistencia yductilidad. El tratamiento térmico T6, es uno de los cuales proveen la mejorcombinación de estas propiedades. El empleo de componentes o piezas en la condiciónde colada es raramente encontrado, debido a las propiedades mecánicas relativamentebajas que ofrece esta condición [7, 10].En la aplicación automotriz, la aleación A319 debe caracterizarse por tener una buenaresistencia mecánica en combinación con ductilidad y al ser sometida a las condicionesde trabajo conservar dichas propiedades mecánicas. Por lo que las piezas fabricadasdeben cumplir con estrictos controles de calidad y seguridad, todo esto, con el propósitode disminuir el peso de los vehículos y por consecuencia, reducir el consumo decombustible.2.2.- Efecto de los principales elementos aleantes en las aleaciones de aluminio.Las aleaciones de aluminio son empleadas en diferentes áreas de manufactura ytecnología, como en las industrias automotrices y aeroespaciales. Estas aleacionescontienen un número limitado de elementos aleantes. Todos los elementos aleantesque son usados en las aleaciones de aluminio son clasificados en tres principalesgrupos: Elementos básicos, adiciones auxiliares (o dopantes) e impurezas.Mayormente solo 4 elementos aleantes son usados en las aleaciones de aluminio:Metales como magnesio, zinc y cobre, y el semiconductor silicio. Los cuales se lesdenominan elementos aleantes básicos o principales porque son introducidos en lasaleaciones de aluminio en cantidades relativamente altas y definen la microestructura ypropiedades de las aleaciones.La introducción de cantidades relativamente altas de los principales elementos aleanteses debido a que tienen una considerable solubilidad en el Al. Se conoce que la máximasolubilidad en aluminio excede el 1 % solo para los siguientes siete elementos:Magnesio, cobre, silicio, manganeso, litio, germanio y plata [5].De estos siete elementos dos pueden ser ampliamente usados como elementosaleantes principales debido a consideraciones económicas. La plata es un metalprecioso y caro, al igual que el germanio, el cual es principalmente utilizado en laindustria de los semiconductores. Adicionalmente no se han encontrado efectosinteresantes debidos a la influencia de estos dos elementos en las aleaciones dealuminio.9
La principal función de los elementos aleantes es incrementar la resistencia de laaleación, debido a que el aluminio puro posee muy baja resistencia (σ 60 MPa). Elincremento en la resistencia es logrado vía formación de solución sólida o por víaendurecimiento por dispersión. Aunque por otro lado, la presencia de elementosaleantes puede afectar fuertemente la facilidad de moldeo de estas aleaciones [3,5].El silicio introducido en las aleaciones de aluminio se debe no solo por su solubilidad enel aluminio sino además por la formación de Al-Si eutéctico, lo cual define unapropiedad muy importante como es la capacidad de moldeo. Adiciones de Si al aluminiopuro incrementan en gran medida su fluidez y la capacidad de alimentación de losmoldes. Para procesos con moldes permanentes es recomendada una concentraciónde 7 a 9 % de Si, esto basado en la relación entre la velocidad de enfriamiento, fluidez yel porcentaje de Si eutéctico [3].Adiciones de Cu ofrece aumento en la resistencia por efecto de solución sólida yademás por endurecimiento por precipitación, después del tratamiento térmico desolubilizado, el temple y el envejecimiento. Las que contienen entre 4 y 6 % de Cupresentan mejor respuesta a los tratamientos térmicos. Desafortunadamente el cobrereduce la resistencia a la corrosión, además su concentración debe ser limitada debidoa que reduce la capacidad de moldeo.El Mg al 0.3 % en aleaciones por fundición de Al-Si con 7 o 9 % Si, es el que define laresistencia de la aleación, el Mn en aleaciones similares en porcentajes de 0.5 % suprincipal rol es neutralizar la influencia perjudicial del Fe y en aleaciones Al-Cu sufunción es incrementar la estabilidad térmica de la aleación.La función del Magnesio es incrementar las propiedades de dureza y resistenciamecánica en las aleaciones Al-Si mediante un tratamiento térmico. El Mg es empleadoen aleaciones más complejas que contienen Cu, Ni entre otros elementos con el mismoobjetivo. Las aleaciones Al-Si que muestran valores óptimos de resistencia empleanmagnesio en intervalos de 0.4 a 0.07 %.El zinc, introducido junto con otras adiciones especialmente con magnesio y cobreejerce un profundo efecto en las propiedades de las aleaciones tratables térmicamenteo en aquellas envejecidas naturalmente.En adición de los principales elementos aleantes usualmente menor al 1 %, están loselementos auxiliares que son usados casi en todas las aleaciones industriales. Enmuchos casos son metales de transición, tierras raras o hasta metales estratégicos,entre los cuales se encuentran, como el manganeso, titanio, cromo, vanadio, níquel,hierro, cerio, escandio, berilio, cadmio y boro entre otros.El elemento auxiliar mas comúnmente usado para las aleaciones de aluminio es elmanganeso el cual es adicionado en porcentajes de 0.1 % a 1 %. El principal objetivo10
del manganeso y de algunos metales de transición como titanio, zirconio, cromo yvanadio es lograr un efecto adicional en el aumento de la resistencia. Este efectoadicional toma lugar debido a la formación anómala de soluciones sólidassupersaturadas bajo condiciones de no equilibrio durante la solidificación [5], tambiénes utilizado debido a que ofrece un control en la estructura grano [3].Además del efecto en la resistencia que ofrecen los metales de transición en elaluminio, también mejoran su formabilidad debido al refinamiento de grano, titanio juntocon boro o en forma independiente.El último grupo de elementos químicos que entran en las aleaciones de aluminio esllamado impurezas. Estos pueden ser introducidos en las aleaciones de aluminiodurante el proceso de fundición, pueden provenir de los moldes de fundición o deinstrumentos utilizados. Hierro y silicio son comúnmente agregados a las aleaciones y alcombinarse con las impurezas forman compuestos que afectan negativamente a laspropiedades mecánicas de las aleaciones, especialmente en propiedades relacionadascon la elongación, fatiga y fractura [5].2.3.-Efecto del refinador de grano en la microestructura.El control de la microestructura es un requerimiento fundamental en la industria de lafundición. El tamaño de grano es una característica importante para la calidad de lasfundiciones, es necesario obtener granos pequeños y dendritas con morfología globularcon el objeto de llenar los moldes en su totalidad.El refinamiento de grano es un tratamiento efectivo en las fundiciones para elevar sucalidad. Una estructura de grano fina asegura que sus propiedades mecánicas seanuniformes, mejora la alimentación de la masa fundida en los moldes para evitarporosidades y encogimientos, además distribuye homogéneamente las fasessecundarias y las microporosidades [1].El tamaño y la forma de los granos formados son determinados por la composición de laaleación, velocidad de solidificación y la adición de aleaciones maestras (refinadores degrano) que contienen fases intermetálicas que proveen sitios para la nucleación de losgranos de forma heterogénea. Refinadores de grano usados en la industria del aluminioson Ti o B o una mezcla de ambos en proporciones controladas (aleaciones maestrasAl-Ti o Al-Ti-B). [3].El Boro se combina con otros metales formando compuestos como AlB2 y TiB2, elcompuesto de boro-titanio forma sitios de nucleación estables que interactúan con fasesactivas refinadoras de grano como TiAl3 [2].11
2.4.- Modificador de morfología del silicio eutécticoSodio, estroncio, calcio y antimonio son usados en pequeñas cantidades 0.01 % comomodificadores de Al-Si eutéctico en aleaciones por fundición de la serie 3xx, estoselementos son usados con el objetivo de mejorar sus propiedades mecánicas. Lo cualconsiste en modificar el silicio eutéctico de morfología acicular a forma de fibras oglóbulos mejorando así sus propiedades mecánicas, particularmente el porcentaje deelongación. La modificación del silicio es lograda mediante la adición de pequeñascantidades de estos elementos en la masa fundida de la aleación [3,7].2.5.-Tratamiento térmico de endurecimiento por precipitación.El endurecimiento por precipitación es el método con el cual aleaciones como Al-Si, AlCu, Mg-Al, incrementan propiedades como dureza y resistencia mecánica, por medio dela formación de pequeñas partículas de una segunda fase finamente dispersas en lafase original matriz denominadas precipitados. El endurecimiento se obtiene mediantela deformación de la red cristalina de la matriz principal, la cual se deforma en lascercanías de las partículas precipitadas, las deformaciones obtenidas en la red evitanun libre movimiento de las dislocaciones. Este método es conocido también comoendurecimiento por envejecimiento debido a que se van obteniendo las propiedadesmecánicas en función del tiempo. [12].La aleación A319 posee las características para ser endurecida al ser tratadatérmicamente e incrementar su resistencia mecánica.Para obtener componentes de fundición con mejores propiedades mecánicas sepueden tratar térmicamente. Varios ciclos de tratamientos térmicos, a diferentescombinaciones de temperaturas y tiempos, son realizados dependiendo del proceso dela fundición, la composición de la aleación y de las propiedades mecánicas deseadas.El tratamiento T6 es típicamente usado para las aleaciones Al-Si obtenidas mediantemoldes de arena y moldes permanentes por el método de vaciado por gravedad.Siguiendo la ruta de un tratamiento térmico T6 el cual posee las etapas de solubilizado,temple y envejecido artificial mostradas en la Fig.2.5 [8].2.6.- Etapas del Tratamiento térmico T6.Tratamiento térmico de solubilizado.- Este tratamiento es llevado a cabo a altatemperatura, cercana a la temperatura del eutéctico en la aleación, el objetivo es laobtención de una solución sólida sobresaturada homogénea de una sola fase, en dondequedan disueltos los átomos de soluto, reduciendo cualquier segregación de estospresentes en la aleación original. [11].12
Los propósitos más importantes del tratamiento térmico de solubilizado en la aleaciónA319 son tres:-Disolver las fases presentes de Cu y Mg que se formaron durante la solidificación.-Homogeneizar en la aleación a los elementos aleantes.-Esferoidizar las partículas de Si eutéctico.La velocidad de estos tres procesos se eleva, tal cual se incrementa la temperatura detratamiento térmico de solubilizado, además de que la resistencia obtenida después deltratamiento térmico de envejecido también se ve incrementada por que se obtiene lamáxima solubilidad en la matriz de aluminio. La temperatura máxima de tratamientotérmico de solubilizado de las aleaciones Al-Si-Cu-Mg se obtienen a partir de lasconcentraciones de Cu y Mg que contiene la aleación y esta limitada debido a la fusiónque puede ocurrir en algunas fases ricas en estos elementos que se formaron durantela ultima solidificación debido a la segregación. Zonas fundidas localizadas en laaleación representan distorsión que substancialmente reducen las propiedadesmecánicas de la aleación.Para las aleaciones Al-Si-Cu-Mg, con bajo contenido de Mg empiezan a fundir a 519 C.Y para la aleación 319 con una concentración aproximadamente 0.5 wt. % fases ricasen cobre empiezan a fundir a 505 C en presencia de la fase Q-Al5Mg8Si6Cu2.2.6.1.- Disolución- Durante el proceso del tratamiento térmico de solubilizado no todaslas fases se pueden disolver, algunas fases como β-Mg2Si y θ-Al2Cu son fáciles dedisolver mientras que otras fases como la fase π-Al8Mg3FeSi6 y Q- Al5Mg8Si6Cu2.Son difícilmente disueltas o transformadas en estado sólido.Fases como α-Al15(Fe,Mn)3Si2 (script fase), que son ricas en hierro prácticamente noson afectadas por el tratamiento térmico de solubilizado; por otro lado, la fase β-Al5FeSi(platelets), se va fragmentando y experimenta una disolución gradual a largos tiempos yaltas temperaturas de tratamiento térmico de solubilizado.Para efectuar un tratamiento de envejecido efectivo, es necesario disolvercompletamente las fases ricas en Cu y Mg. Ya que los átomos de Cu y Mg quepertenecen a las fases que no se disolvieron durante el tratamiento térmico de solución,no estarán disponibles durante el tratamiento térmico de envejecido para incrementar laresistencia de la aleación mediante el endurecimiento por precipitación.2.6.2.- Homogeneización.- Cuando los átomos se desprenden de fases grandesformadas durante la solidificación, ellos difunden a través de la matriz de aluminio para13
decrecer el gradiente de concentración formando una solución sólida homogénea. Eltiempo necesario para homogeneizar la aleación depende directamente de la naturalezade difusión de los átomos (velocidad de difusión), de la temperatura del tratamientotérmico de solubilizado y de la distancia de difusión; la cual es determinada por lo burdode la microestructura, y normalmente es medida por el espaciamiento existente entrelos brazos secundarios de las dendritas (SDAS).El tiempo necesario para la disolución y homogeneización de las aleaciones dependede factores como: composición, morfología, tamaño y distribución de las fases que seformaron durante la solidificación y además de la temperatura del tratamiento térmicode solubilizado.En las aleaciones Al-Si-Cu en la condición de colada, la fase θ-Al2Cu apareceprincipalmente en dos diferentes formas, la primera es en forma de un bloque pequeñode Al2Cu y la segunda es como fase Al2Cu eutéctico, aunque también se puedepresentar en una mezcla de ambas fases. La fase θ-Al2Cu empieza su nucleación en lafase β-Al5FeSi (platelets) o en partículas grandes de silicio eutéctico durante la ultimaetapa de la solidificación.Si la velocidad de solidificación es alta, se promueve la cristalización de la fase Al2Cueutéctico; mientras que si se emplea Sr para modificar la aleación, se observa unaumento en la cristalización de la fase en forma de un bloque pequeño de Al2Cu.En la condición de tratamiento térmico de solubilizado, se han observado dos tipos defases Al2Cu, una de la cuales es de origen eutéctico, la cual se fragmenta en pequeñossegmentos que posteriormente se esfereoidizan y que finalmente se disuelven en lamatriz de aluminio, por otra parte la fase Al2Cu que no tiene origen eutéctico es mascompleja de disolver, debido a que no se fragmenta, solo se va esfereoidizando, lo cualprovoca mayor tiempo para la disolución en la matriz de aluminio [8].Mientras se realiza el proceso de disolución, en la fase de Al2Cu la concentración de Cuy Al es siempre constante y el Cu que se difunde en la matriz proviene de la última capade la fase Al2Cu.La disolución de las fases de Al2Cu toma un tiempo considerable, debido a la bajavelocidad de difusión del Cu en Al y a la baja temperatura de tratamiento térmico desolubilizado que permite utilizar el contenido de Cu.2.6.3.- Esferoidización de partículas de Si eutéctico.- El tratamiento térmico desolubilizado también tiene como objetivo esfereoidizar las fases de Si eutéctico. Lamorfología del Si eutéctico juegan un papel muy importante en las propiedadesmecánicas de las aleaciones. El Si en una aleación sin ser modificada se encuentra enforma de laminillas largas y quebradizas que representan un efecto negativo para laductilidad de las aleaciones, debido que son un punto de iniciación de grietas.14
La transformación de la morfología del Si eutéctico se puede lograr mediante untratamiento térmico de solubilizado a alta temperatura por periodos largos de tiempos.Además por modificación química, añadiendo Sr a la fundición y por la utilización losdos métodos combinados para el propósito.Las etapas con las cuales las partículas de Si eutéctico modifican su morfología son lassiguientes: Primeramente se fragmentan, luego se esferoidizan y posteriormente sehacen más gruesas. Mediante la modificación de la aleación por medio de adición deSr, se logra que las partículas de Si eutéctico sean como fibras, las cuales son másfáciles de fragmentar y esfereoidizar durante el tratamiento térmico de solubilizado, conesto se logra que el tiempo del mismo se reduzca.El tiempo necesario para la modificación de la morfología de las partículas de Sieutéctico depende de factores como la temperatura del tratamiento térmico desolubilizado además del tamaño y forma de la partículas de Si en la condición decolada.Cuando la aleación Al-Si-Cu ha sido modificada con adición de Sr, se pueden aplicartemperaturas más bajas por tiempos más largos (8-16 h), y se han llegado a obtenermuy buenos resultados [8].2.6.4.- Temple.- El propósito de templar las aleaciones Al-Si-Cu antes de hacer untratamiento térmico de envejecido, es obtener una solución sólida sobresaturada deátomos de soluto. Esto se logra mediante la disminución rápida de la temperatura detratamiento térmico de solubilizado a la temperatura ambiente o cercana a dichatemperatura. Así se logra suprimir la precipitación de fases estables típicamenteformadas durante el enfriamiento lento. Esto se debe a que el enfriamiento rápido“congela” la microestructura que posee mayor cantidad de átomos de soluto a latemperatura elevada, y a la cual no se le permitió volver a estado de equilibriotermodinámico por medio de un enfriamiento lento.Considerando el diagrama binario Al-Cu, después del temple los átomos de Cu notienen tiempo de difundirse para formar la fase θ en equilibrio, la microestructura estáconformada solo de la fase α sobresaturada, la cual tiene un exceso de átomos de Cu yfuera de un estado de equilibrio.El agua es empleada para realizar el templado, sin embargo se pueden desarrollaresfuerzos residuales causando distorsión en las piezas, para suprimir este efecto esnecesario efectuar el templado empleando agua a temperaturas superiores a latemperatura ambiente aproximadamente a 80 C [11]. Cuando es necesaria unavelocidad de temple más lenta se puede utilizar aceite, baños de sales o sustanciasorgánicas.15
2.6.5.- Envejecimiento o tratamiento térmico de precipitación.Esta etapa consiste en incrementar la temperatura de la solución sólida αsobresaturada (αss) a un valor dentro de la región bifásica (α θ), mostrada en eldiagrama de equilibrio Al-Cu Fig. 2.2. A esta temperatura la velocidad de difusión esconsiderable, debido a que αss no está en equilibrio, los átomos de Cu excedentesempiezan difundir y formar en los sitios de nucleación partículas finamentedispersas llamadas precipitados. Después de un determinado tiempo y manteniendola temperatura de la aleación se llega a la microestructura en equilibrio (α θ), [11,12].Las temperaturas típicas de envejecimiento artificial T6 para las aleaciones Al-Si-Cu,son 150 C, 170 C, 190 C, 220 C y 240 C[7], otros trabajos muestran 160 C y 200 C [8].Si el tratamiento térmico de envejecido es llevado a cabo a temperatura ambiente esdenominado envejecido natural o temperaturas más elevadas, en un intervalo de 150 Ca 240 C es llamado envejecido artificial. El propósito es obtener precipitados finos deátomos de soluto distribuidos uniformemente, lo cual le da propiedades de altaresistencia a las aleaciones.El envejecido natural es un tratamiento
suficiente endurecimiento por dispersión debido a la precipitación de fases metaestables secundarias β' y β" (Mg 2Si) de acuerdo a lo observado en el diagrama de fases del sistema binario Mg-Si [4], mostrado en la Fig. 2.3. El límite superior debe asegurar una pequeña fracción de volumen de fases que contienen Mg de origen .