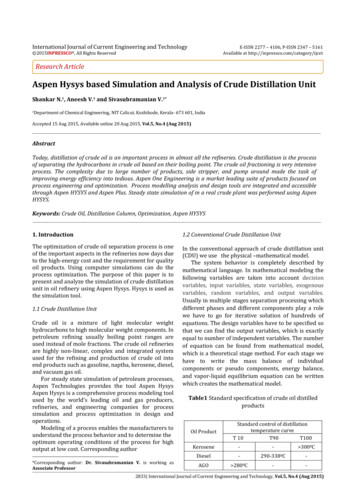
Transcription
International Journal of Current Engineering and TechnologyE-ISSN 2277 – 4106, P-ISSN 2347 – 5161Available at http://inpressco.com/category/ijcet 2015INPRESSCO , All Rights ReservedResearch ArticleAspen Hysys based Simulation and Analysis of Crude Distillation UnitShankar N.†, Aneesh V.† and Sivasubramanian V.†*†Departmentof Chemical Engineering, NIT Calicut, Kozhikode, Kerala- 673 601, IndiaAccepted 15 Aug 2015, Available online 20 Aug 2015, Vol.5, No.4 (Aug 2015)AbstractToday, distillation of crude oil is an important process in almost all the refineries. Crude distillation is the processof separating the hydrocarbons in crude oil based on their boiling point. The crude oil fractioning is very intensiveprocess. The complexity due to large number of products, side stripper, and pump around made the task ofimproving energy efficiency into tedious. Aspen One Engineering is a market leading suite of products focused onprocess engineering and optimization. Process modelling analysis and design tools are integrated and accessiblethrough Aspen HYSYS and Aspen Plus. Steady state simulation of in a real crude plant was performed using AspenHYSYS.Keywords: Crude Oil, Distillation Column, Optimization, Aspen HYSYS1. Introduction1.2 Conventional Crude Distillation Unit1 Theoptimization of crude oil separation process is oneof the important aspects in the refineries now days dueto the high-energy cost and the requirement for qualityoil products. Using computer simulations can do theprocess optimization. The purpose of this paper is topresent and analyze the simulation of crude distillationunit in oil refinery using Aspen Hysys. Hysys is used asthe simulation tool.1.1 Crude Distillation UnitCrude oil is a mixture of light molecular weighthydrocarbons to high molecular weight components. Inpetroleum refining usually boiling point ranges areused instead of mole fractions. The crude oil refineriesare highly non-linear, complex and integrated systemused for the refining and production of crude oil intoend products such as gasoline, naptha, kerosene, diesel,and vacuum gas oil.For steady state simulation of petroleum processes,Aspen Technologies provides the tool Aspen HysysAspen Hysys is a comprehensive process modeling toolused by the world’s leading oil and gas producers,refineries, and engineering companies for processsimulation and process optimization in design andoperations.Modeling of a process enables the manufacturers tounderstand the process behavior and to determine theoptimum operating conditions of the process for highoutput at low cost. Corresponding author*Corresponding author: Dr. Sivasubramanian V. is working asAssociate ProfessorIn the conventional approach of crude distillation unit(CDU) we use the physical –mathematical model.The system behavior is completely described bymathematical language. In mathematical modeling thefollowing variables are taken into account decisionvariables, input variables, state variables, exogenousvariables, random variables, and output variables.Usually in multiple stages separation processing whichdifferent phases and different components play a rolewe have to go for iterative solution of hundreds ofequations. The design variables have to be specified sothat we can find the output variables, which is exactlyequal to number of independent variables. The numberof equation can be found from mathematical model,which is a theoretical stage method. For each stage wehave to write the mass balance of individualcomponents or pseudo components, energy balance,and vapor-liquid equilibrium equation can be writtenwhich creates the mathematical model.Table1 Standard specification of crude oil distilledproductsOil ProductKeroseneStandard control of distillationtemperature curveT 10T90T100-- 3000CDiesel-290-3380C-AGO 2800C--2833 International Journal of Current Engineering and Technology, Vol.5, No.4 (Aug 2015)
Shankar N. et alAspen Hysys based Simulation and Analysis of Crude Distillation UnitFigure1 Practical configuration of a crude distillation unitFigure2 The overview of crude oil distillation unit in typical refinery processing Agbami crudeFigure (1) shows the practical configuration of a crudedistillation unit. In practical CDU operating conditionthe major requirement is that all distilled productshave to satisfy the specification given in table (1). Thetemperature distribution of each distilled productcannot be known before hand even if the CDU towertemperature and pressure distributions are wellcontrolled. This is due to the uncertain phenomenonpresent inside the CDU system.1.3 Technological knowhow of CDUFigure (2) depicts an overview of crude oil distillationunit in typical refinery processing Agbami crude. Thecrude from the submarine is directly fed to a storagetank. The crude is the preheated using hot overheadand product side stream using heat exchanger networkand is given to the desalter where all the dissolvedsalts are removed.The crude enters a drum and some light ends withwater are flashed off the drum.The high volatile product like LPG is initiallyobtained. The removed light ends are directly fed to theflash zone of the main column of the CDU. The crude isagain heated. Distillate products from the main columnare removed from selected trays. These are calledDraw off trays. From the tower top of the atmosphericcolumn, full range naphtha (both light and heavy) willleave as a vapor. Eventually, the vapor will becondensed and separated in a phase separator. Theseparated naphtha product will be partially sent forreflux and the balance sent as reflux stream from theoverhead drum. From the atmospheric column theproducts like kerosene and diesel are also obtained.The bottom products of the atmospheric column isheated and is given to the vacuum column .The vacuumcolumn as the name suggests operates at vacuum2834 International Journal of Current Engineering and Technology, Vol.5, No.4 (Aug 2015)
Shankar N. et alAspen Hysys based Simulation and Analysis of Crude Distillation Unittemperature, where the products like light vacuumgasoil (LVGO) and high vacuum gasoil (HVGO) areobtained.2. Input data and characterization of crude oilThe simulation of the typical crude distillation unitusing Hysys is the objective of the work. The feed of491.5 tons/hr of the crude enters into the preflashcolumn. The number of theoretical stages in thecolumn is specified as 13.Thecoloumn pressure wasaround 2-3 atm. The mass flow of three pre flashcolumn product is given in table (2).Table 2 Mass flow of preflash column productProductMass flow (ton/hr)Light Products3.5Light Naptha1.2Bottom product370.95The second step is the characterization of crude oil andinput data. Refineries usually have multiplicity of crudeoils. Refineries go for blending of crude oils due tooperational and feed availability.The input variables are usually crude oil propertiesand manipulated variables of CDU such as reflux ratio,product flow rates etc. Crude feeds are usually not ofone origin but mix that can vary from 2 to 10 differentcrude types. Usually using ASPEN does the crude oilblending. Simulation package can be used tocharacterize petroleum fluids if data from laboratory isavailable, also ready to use characterized crudedatabase are available. The partial simulation of thecrude distillation unit in fig (2) is depicted in fig (3)and fig (4) respectively.The bottom of the pre flash column was pre heated to362.4 0C in a furnace before entering the atmosphericcolumn. The mass flow of atmospheric column is givenin table (3).Table 3 Mass flow of atmospheric columnProductMass flow (ton/hr)Heavy Naptha45.45Kerosene43.18Atmospheric Residue176.76Figure 3 The simulation of typical crude distillationunitThe residue of the atmospheric column is given to thevacuum column where it undergoes distillation undervacuum temperature. The mass flow rate of vacuumcolumn is given in table (4).Table 4 Mass flow of vacuum columnProductLVGOVGOMass flow (ton/hr)173.86118.30HVGO37.653. Simulation of crude distillation unitThe first step for a successful simulation is correctchoice of the thermodynamic method that will be usedin the calculations of the state variables and thephysical properties. The Peng-Robinson equation ofstate is normally accepted for the compounds in thecrude distillation unit process stream. The number oftheoretical stages of an existing column is estimated, asthe product of real number of stages and columnefficiency .The equation is applicable to all calculationof all fluid properties in natural gas processes.Figure 4 The simulation of typical crude distillationunit4. Steady State SimulationThe true boiling point data (ASTM D86) for theproducts like light naphtha, kerosene were available.The initial condition for simulation is set as in realenvironment. Figure (5) depicts the simulation andexperimental result of the kerosene distillate.2835 International Journal of Current Engineering and Technology, Vol.5, No.4 (Aug 2015)
Shankar N. et alAspen Hysys based Simulation and Analysis of Crude Distillation Unit4. Advantages of using AspenConventional Design ProcedureFigure5 Simulated and experimental ASTM D86 curvesof KeroseneFigure (6) depicts the Simulated and experimentalASTM D86 curves of Light gas oil (LGO).Hysysover1. Aspen Hysys is powerful tool for steady statemodeling. Theoretically it’s very difficult to find theenergy balance and mass balance across the crudedistillation unit.2. The process can be easily understood whilesimulation using Hysys.3. Aspen Hysys can be used for both steady state andynamic simulation of complex crude oil distillationsystem.4. Aspen Hysys the flexibility contributed through thedesign combined with un parallel accuracy androbustness leads to the more realistic model.5. The single model concept of Aspen Hysys increasesthe Individual Engineers efficiency and efficiency of anorganization6. Aspen Hysys is having its unique feature of its strongthermodynamic foundationConclusionFigure6 Simulated and experimental ASTM D86 curvesof Light gas oil (LGO)Figure (7) depicts the true boiling point curve of theatmospheric crude. The maximum difference betweenthe experimental and simulation results were around10 0 C.Simulation software is one of the best tools for a crudeoil refinery. This can be used during the conceptualdesign as well during the entire life span of theequipment’s. Aspen Hysys enables the simulation ofvery complex crude distillation systems in an easymanner. The goal is achieved by using Aspen, whichprovide capability to design the entire processaccurately.For the analysis of the crude distillation unitsimulated and experimental curves of kerosene, lightgas oil and true boiling point curve of atmosphericresidue is taken into account.The simulation software can be used fordebottlenecking, performance and process studies.The optimization can be done very easily, togetherwith the advanced process control tools, make itprofitable in the operation in real time. The goal isachieved by using Aspen, which provide capability todesign the entire process accurately.ReferencesFigure7 Simulated and experimental TBP curves ofatmospheric residueRaja Kumar More, Vijaya Kumar Bulasara, RamgopalUppaluri, Vikas R. Banjara, (2010) Optimization of crudedistillation system using aspen plus: Effect of binary feedselection on grass root design, Chemical EngineeringResearch and Design 88 ,pp. 121-13Akbar Mohammadi Doust, Farhad Shahraki and Jafar Sadeghi,(2012) Simulation, control and sensitivity analysis of crudeoil distillation unit Journal of Petroleum and GasEngineering Vol. 3(6), pp. 99-11Lekan T. Popoola, Alfred A. Susu (2014) Application ofArtificial Neural Networks Based Monte Carlo Simulationin the Expert System Design and Control of Crude OilDistillation Column of a Nigerian Refinery, Advances inChemical Engineering and Science, 2014, 4, pp.266-2Popoola, L.T., Babagana, G. and Susu, A.A. (2013) ExpertSystem Design and Control of Crude Oil Distillation Column2836 International Journal of Current Engineering and Technology, Vol.5, No.4 (Aug 2015)
Shankar N. et alAspen Hysys based Simulation and Analysis of Crude Distillation Unitof a Nigerian Refinery using Artificial Neural NetworkModel. International Journal of Research and Reviews inApplied Sciences, 15, pp.337-34Mohd.KamaruddinAbd Hamid Hysys: An Introduction toChemical Engineering Simulation Ones D. S. D. and PujadoP. R., (2006). Handbook of Petroleum Processing, Springer,NetherlandLeo Chau-KuangLiau, Thomas Chung-Kuang Yang MingTeTsai (2004), Expert system of a crude oil distillation unitfor process optimization using neural networks ,ExpertSystems with Applications 26 (2004), pp.247–2LekanTaofeekPopoola, Gutti Babagana, Alfred Akpoveta Susu(2013), A Review of an Expert System Design for Crude OilDistillation Column Using the Neural Networks Model andProcess Optimization and Control Using Genetic AlgorithmFramework, Advances in Chemical Engineering and Science,2013, 3, pp.164-1Aspen Engineering Suite 2004.1 Aspen Plus 2004.1, GettingStarted Modeling Petroleum ProcesseWarren.L. McCabe, Julian C .Smith, Peter Harriot (2009)Unitoperations in chemical engineering Aspen TechnologyAspen Plus user guide volume 1 anMichael E Hanyak (2007)Chemical Process Simulation andAspen tech Hysys Software Version 2006 Bucknelluniversity Lewisburg PA 17837 December 15 2N. Kozarev, F. Keil, S. Stoyanov, (2010) Computer AidedSteady State Control of Crude Oil Distillation, Journal of theUniversity of Chemical Technology and Metallurgy, 45(4),pp.401-4J. Haydary, T. Pavlik (2009),Steady-State and DynamicSimulation of Crude Oil Distillation using ASPEN Plus andASPEN Dynamics, Petroleum and Coal, 51(2), pp.100-1E.O.Okeke, A.A. Osakwe-Akofe (2003)Optimization of aRefinery Crude Distillation Unit in the Context of TotalEnergy Requirement, NNPC R&D Division, Port Harcourt,NigE.I. Santana, R.J. Zemp, (2001) Thermodynamic Analysis of aCrude-Oil Fractionating Process, 4th Mercosur Congress onProcess Systems Engineering, 21, pp.523-5Kermanshah Refinery (2009). Operating data of DistillationuniSea, J. W., Oh, M., & Lee, T. H. (2000). Design optimization ofcrude oil distillation, Chemical Engineering Technology,23(2), pp.157 – 16Luyben WL (2006). Distillation Design and Control UsingAspeW. Heather, Refining Crude Oil, The New Zealand Re- finingCompany Ltd., Ruakaka, 20Lluvia M. Ochoa-Estopier, Megan Jobson, Robin Smith (2013),Operational optimization of crude oil distillation systemsusing artificial neural networks Elsevier Computers &Chemical Engineering ,Volume 59, pp.178–18Mizoguchi, A., Martin, T. E., &Hrymak, A. N. (1995).Operations optimization and control design for apetroleum distillation process, The Canadian Journal ofChemical Engineering, 73, pp. 896–9072837 International Journal of Current Engineering and Technology, Vol.5, No.4 (Aug 2015)
Aspen Hysys is a comprehensive process modeling tool used by the world's leading oil and gas producers, refineries, and engineering companies for process simulation and process optimization in design and operations. Modeling of a process enables the manufacturers to understand the process behavior and to determine the .