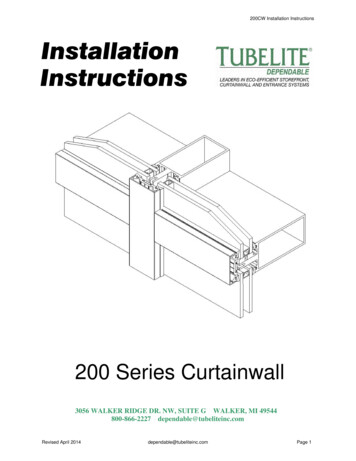
Transcription
200CW Installation InstructionsInstallationInstructions200 Series Curtainwall3056 WALKER RIDGE DR. NW, SUITE G WALKER, MI 49544800-866-2227 dependable@tubeliteinc.comRevised April 2014dependable@tubeliteinc.comPage 1
200CW Installation InstructionsTABLE OF CONTENTSGENERAL CONSTRUCTION NOTESPARTS LISTELEVATION DETAILSFRAME FABRICATIONStep 1: Determine Frame SizeDetermine Frame WidthDetermine Frame HeightStep 2: Cut Mullions to SizeStep 3: Cut Pressure Plates, Snap-on Face Covers and Fillers to LengthStep 4: Drill Weep Holes in Horizontal Pressure PlateStep 5: Mill Weep Slot in Horizontal Snap-on CoverStep 6: Drill Slots in HorizontalStep 7: Notch Sills and HeadsStep 8: Notch Horizontal in Final Bay (if necessary)Step 9: Fasten Splice Sleeves in Lower Segments of Verticals (if necessary)Step 10: Add Steel Reinforcing (if necessary)CURTAINWALL INSTALLATIONStep 11: Attach Shear BlockStep 12: Butt Sill Anchor to Side of MullionStep 13: Fasten Sill Anchor to MasonryStep 14: Slide Horizontal Onto Shear BlockStep 15: Slide Horizontal Onto Sill Anchor ClipStep 16: Seal Joints Between Verticals and HorizontalsStep 17: Install Water DamsStep 17: Install Water Dam (SSG)Step 18: Apply Sealant Around Water DamStep 19: Press Vertical Gaskets Into Vertical MembersStep 20: Press Horizontal Gaskets Into Horizontal MembersStep 21: Place Setting BlocksStep 22: Install GlassStep 23: Press Glazing Gaskets Into Vertical Pressure PlatesStep 24: Fasten Vertical Pressure Plate and Snap-on CoverStep 25: Press Glazing Gaskets Into Horizontal Pressure PlatesStep 26: Screw Horizontal Pressure Plate Into PlaceStep 27: Seal Horizontal Pressure Plate ScrewStep 28: Install Horizontal Snap-on CoverStep 29: Insert Backing RodCONNECTION AT PERIMETERReturn Leg Pressure PlateF Perimeter RunnerCORNER CONDITIONOutside 90 Degree CornerSUNSHADE ATTACHMENTRevised April 0313132333334Page 2
200CW Installation InstructionsGENERAL CONSTRUCTION NOTES1. These instructions cover typical product application, fabrication, installation and standard conditions and aregeneral in nature. They provide useful guidelines, but the final drawings may include additional details specific tothis project. Any conflict or discrepancies must be clarified prior to execution.2. Materials stored at the job site must be kept in a safe place protected from possible damage by other trades.Stack with adequate separation so materials will not rub together, and store off the ground. Cardboard or paperwrapped materials must be kept dry. Check arriving materials for quantity and keep record of where variousmaterials are stored.3. All field welding must be done in accordance with AISC guidelines. All aluminum and glass should be shieldedfrom field welding to avoid damage from weld splatter. Results will be unsightly and may be structurally unsound.Advise general contractor and other trades accordingly.4.Coordinate protection of installed work with general contractor and/or other trades.5. Coordinate sequence of other trades which affect framing installation with the general contractor (e.g. fireproofing, back up walls, partitions, ceilings, mechanical ducts, HVAC, etc.).6. General contractor should furnish and guarantee bench marks, offset lines and opening dimensions. Theseitems should be checked for accuracy before proceeding with erection. Make certain that all adjacent substrateconstruction is in accordance with the contract documents and/or approved shop drawings. If not, notify thegeneral contractor in writing before proceeding with installation because this could constitute acceptance ofadjacent substrate construction by others.7. Isolate all aluminum to be placed directly in contact with masonry or other incompatible materials with a heavycoat of zinc chromate or bituminous paint.8. Sealant selection is the responsibility of the erector, installer and/or glazing contractor and must be approvedby the sealant manufacturer with regard to application and compatibility for its intended use. All sealants must beused in strict accordance with the manufacturer’s instructions and applied only by trained personnel to surfaces thathave been properly prepared.9. Sealant must be compatible with all materials with which they have contact, including other sealant surfaces.Consult sealant manufacturer for recommendations relative to shelf life, compatibility, cleaning of substrate,priming, tooling adhesion, etc.10. Drainage gutters and weep holes must be kept clean at all times. Tubelite will not accept responsibility forimproper drainage as a result of clogged gutters and weep holes.11. This product requires clearances at head, sill and jambs to allow for thermal expansion and contraction. Referto final distribution drawings for joint sizes. Joints smaller than ¼” may be subject to failure. Consult your sealantsupplier.12. All materials are to be installed plumb, level and true with regard to established bench marks and columncenter lines established by the general contractor and checked by the erector, installer and/or glazing contractor.13. Cleaning of exposed aluminum surfaces should be done per AAMA recommendations.14. Due to varying perimeter conditions and job performance requirements, anchor fasteners are not specified inthese instructions. For anchor fastening, refer to the shop drawings or consult the fastener supplier.15. Check tubeliteinc.com for any updates on installation instructions.Revised April 2014dependable@tubeliteinc.comPage 3
200CW Installation InstructionsEXTRUSIONSShapeBack member forcaptured 1" glassE1180:E2053:E1199:E1025:E2297:2" x 2 1/2"2" x 3 5/8"2" x 4"2" x 4 1/2"2" x 6"Back member forcaptured 1/4" glassE1046:E1495:E0977:E1584:2" x 2 1/2"2" x 4"2" x 4 1/2"2" x 6"Open-back perimeterRevised April 2014Part No.DescriptionE3284: 2" x 4"E3285: 2" x 6"Back member forsilicone glazed 1" glassE3127: 2" x 4"E3126: 2" x 4 1/2"E3125: 2" x 6"2" screw applied hornE3270: 1" glassE2012: 1/4" glass2" x 4 1/2" tubeE14511 3/4" x 4 1/2" slicktubeE00414" x 1" F anchorperimeter runnerE31622 1/2" x 1" F anchorperimeter runnerE1094dependable@tubeliteinc.comPage 4
200CW Installation InstructionsEXTRUSIONSShapeSnap coverE0968:E0992:E2606:E1214:E0978:E3642:E1587:2" x 1/2"2 x 3/4"2" x 1"2" x 1 1/2"2" x 2"2" x 3"4" x 3/4"O.S. corner adapterE2101I.S. corner adapterE2100Pocket reducer for1/4" glazingE4TB69Pocket reducer for 3/8"- 1/2" glazingE4TB80Glass pocket - closureplate for 1" glassE3192Return legpressure plateRevised April 2014Part No.Descriptiondependable@tubeliteinc.comE1062Page 5
200CW Installation InstructionsACCESSORIESShapeDescriptionPart No.Insulated pressure plateM1061Temporary glazing clipP1193Return legpressure plateM1202Back member spliceP1625A: For E1180P1625B: For E1199, E1495P1625C: For E0977, E1025P1625D: For E1584, E2297P1625E: For E2053P1625F: For E3125P1625G: For E3126P1625H: For E3127P914Insulator for M1061Temporary glazing clip(use withE3125/3126/3127)Setting block for 1"glassP946:P947:Snap cover spliceP1626A: 1/2"P1626B: 3/4"Fixed glazing gasketPTB28:PTB31:EPDMSilicone1/8"3/16"Silicone glazing spacerP1690Water dam for 1"glazed systemP945Water dam for siliconeglazed verticalsP1629Locking lugShear blockRevised April 2014P1108dependable@tubeliteinc.comP1265: .3125" hole diameterP1266: .375"P1267: .4375"P1320A: 4" back memberP1320B: 6"P1320C: 4 1/2"P1320D: 2 1/2"P1320F: 3 5/8"P1320K: 4" open back memberP1320L: 6" open back memberPage 6
200CW Installation InstructionsACCESSORIESShapeRevised April 2014DescriptionPart No.Sill anchorP1318A: 4" back memberP1318B: 6"P1318C: 4 1/2"P1318D: 2 1/2"P1318F: 3 5/8"P1318K: 4" open back memberP1318L: 6" open back memberHead 43K:F anchorP2078A: For E1215P2078B: E1180P2078C: E2053P2078D: E1199P2078E: E1025P2078F: E2297P2078G: E3127P2078H: E3126P2078J: E3125T anchorP2079A: For E1215P2079B: E1180P2079C: E2053P2079D: E1199P2079E: E1025P2079F: E2297P2079G: E3127P2079H: E3126P2079J: E31254" back member6"4 1/2"2 1/2"3 5/8"4" open back member6" open back memberPipe sleeve spacerfor 3/8" diameter boltP2028#10 UNC x 5/8"type B hex washerheadS357#14-14 x 1/2" typeB hex headS139#10 x 1/2" type BPhillips truss headS191#14-14 x 1/2" typeB hex headS270dependable@tubeliteinc.comPage 7
200CW Installation InstructionsELEVATION DETAILSRevised April 2014dependable@tubeliteinc.comPage 8
200CW Installation InstructionsELEVATION DETAILSRevised April 2014dependable@tubeliteinc.comPage 9
200CW Installation InstructionsFRAME FABRICATIONStep 1: Determine Frame SizeDetermine Width Check that the opening issquare and plumb at both ends.Units must be installed in a truerectangle. Measure the width of theopening at the top, middleand bottom. Select the smallestdimension measured. Todetermine the frame widthto be used, subtract aminimum of 1” from thesmallest measured width, toallow a minimum of 1/2” ateach jamb for shimmingand caulking. Allow a larger clearance ifnecessary to accommodatebuilding tolerances, anout-of-square opening,anticipated thermalexpansion within the unitand/or according to projectneeds.Revised April 20141/2" min.dependable@tubeliteinc.com1/2" min.Page 10
200CW Installation InstructionsDetermine Height Measure the height of theopening in several placesalong the entire length of theopening. To determine the frameheight to be used, select thesmallest dimension measuredand subtract 1” to allow aminimum of 1/2" at sill andhead for shimming andcaulking. Allow a larger clearance ifnecessary to accommodatebuilding tolerances, anout-of-square opening,anticipated thermal expansionwithin the unit and/oraccording to project needs.1/2" min.1/2" min.Step 2: Cut Mullions to Size Verticals should be frame height found in Step #1 (rough opening height minusclearances). Vertical framing members run through as shown in the elevation overview. Cut horizontal framing members to the daylight opening (the distance betweenverticals) minus 1/16" total.Revised April 2014dependable@tubeliteinc.comPage 11
200CW Installation InstructionsStep 3: Cut Pressure Plates, Snap-on Face Covers and Snap-in Fillers to Length Cut vertical pressure plates and face covers to the same length as thecorresponding vertical. Cut horizontal pressure plates to a minimum of daylight opening minus 3/8" (3/16" offeach side) and a maximum of DLO minus 1/8" (1/16" off each side). Cut horizontal face covers and snap-in fillers for roll-over horizontals to the samelength as the corresponding horizontals (daylight opening). To splice vertical pressure plates and face covers, allow a 3/8" gap for the splicejoints. The splice in a vertical pressure plate should be 2" below the splice in themullion, and the splice in a vertical snap-on cover should be 2" below the splice in thepressure plate as shown in Figure 1.Splice sleeveBack memberFace coversplice (2"lower thanpressureplatesplice)Pressure plate splice (2" lower thansplice of back member)Figure 1: Splice face covers and pressure plates as necessary.Revised April 2014dependable@tubeliteinc.comPage 12
200CW Installation InstructionsStep 4: Drill Weep Holes inHorizontal Pressure Plate Drill three weep holes in thehorizontal pressure plate: twohalfway between the center andthe end of the pressure plate andone at the center of the pressureplate, as shown in Figure 2. Drill all weep holes 5/16" abovethe groove which marks thecenter line of the pressure plate. Pressure plate is pre-punchedwith holes for fasteners. Drilladditional holes as required toensure end holes are a minimumof 2” and maximum of 4” from thevertical and then assume a 10”center to center spacing for theremainder.Weep holes2" min. 4" max.Center lineFigure 2: Install three weep holes in thehorizontal pressure plate.Step 5: Mill WeepSlot in HorizontalSnap-on Cover Mill a weep slota maximum of 1"from the end of thecover. The weepslots are to be 1/4"wide x 1/2" long asshown in Figure 3.1/2" x 1/4"weep slot3/16"1" max.Figure 3: Mill a weep slot in the horizontal snap-on cover.Revised April 2014dependable@tubeliteinc.comPage 13
200CW Installation InstructionsStep 6: Drill Slotsin Horizontal Drill two slots in thefront of thehorizontal backmember betweenthe reglet and theglass supporttongue. The slots are .281"x .201" in diameterand centered 3/8"from the end of thehorizontal member,on the V-shapedgroove in theextrusion, as shownin Figure 4.281" x .201" slots3/8"Figure 4: Drill slots in the horizontal member.Step 7: Mill Sills andHeads Mill sills and heads toclear anchor clips. Thisstep is only necessaryfor installations that usetubular back membersfor heads and sills, notfor open-back perimetermembers. The notch must notdamage the verticalwalls of the tube, butshould remove the topor bottom of the tubefrom wall to wall, to adepth of 3 1/16" fromthe end of the sill orhead as shown in Figure5.Revised April 20143 1/16"Width as required by head/sill anchor, leaving 1/8" oneach sideFigure 5: Notch the sills, shown, and heads, similar, to fit in theanchor clips.dependable@tubeliteinc.comPage 14
200CW Installation InstructionsStep 8: Mill Horizontal in Final Bay (if necessary) The tubular horizontals for the last bay to be installed may need to be milled on bothends, as the masonry may prevent movement of the jamb to get the frame clips intothe horizontals. Mill the sill, head and intermediate horizontals in the final bay as shown in Figure 6,or attempt to spread the vertical mullions apart.9/16"3/4"1/8"1 3/4"1/4"1/8"Figure 6: Notch the horizontals in the last bay so they can slide over the frame clips.Revised April 2014dependable@tubeliteinc.comPage 15
200CW Installation InstructionsStep 9: Fasten Splice Sleeves in Lower Segments of Verticals (if necessary) Consult the approved shop drawings to see what size of 1/4-20 flat-head fasteners(minimum 3/4") to use when fastening the splice sleeves to the lower segments of theverticals. Drill and countersink four holes on both sides of the verticals (eight holes pervertical), in the locations shown on the approved shop drawings. The diameter of theholes should be appropriate for the fasteners. Slide a splice sleeve into the end of the vertical mullion where holes were just drilledas shown below. The splice sleeve is 10" long. Half its length should be inside themullion, and half should project out the end of the mullion.1/4" steel angledead load clip(not by Tubelite)Splice sleeve1" insulatedglassOutline ofpressureplateSealant.040aluminumspliceRevised April 2014Splicedependable@tubeliteinc.comHard splicePage 16
200CW Installation InstructionsStep 10: Add SteelReinforcement (ifnecessary)Steel Refer to approvedshop drawings todetermine whether theapplication requiressteel reinforcement. If reinforcement isrequired, cut steel to 6”less than the frameheight. Slide the steel into thevertical mullion from oneend, recessing it 3” infrom the end of thevertical. Drill pilot holes throughthe steel and the verticalmullion at the center ofeach horizontal, andanchor the steel to thevertical using fastenersof an appropriate size(not by Tubelite) asshown at right.Revised April 2014Fastenerdependable@tubeliteinc.comPage 17
200CW Installation InstructionsCURTAINWALL INSTALLATIONStep 11: Attach Shear Block Drill .201" diameter holes into the side of the vertical back member as shown inFigure 7. Attach an intermediate shear block for the corresponding vertical back memberusing S139 fasteners. For dimensions, examine the table below. Dimensions also apply to where the head and sill anchors meet the vertical.However, the drilled holes must be 1" from the top and bottom of the mullion.Dim.BDim. AS139Figure 7: Attach shear block to the vertical back member.ClipDim. ADim. BUse With ExtrusionGlassTube depthP1320A2.250"0.886"E1199, E1495, E32831", 1/4"4"P1320B4.218"0.897"E1584, E22971", 1/4"6"P1320C2.250"1.136"E0977, E10251", 1/4"4 1/2"P1320D0.750"0.886"E1046, E11801"2 1/2"P1320F1.875"0.886"E20531"3 32851"6"Revised April 2014dependable@tubeliteinc.comPage 18
200CW Installation InstructionsStep 12: Butt SillAnchor to Side ofMullion Position an endvertical back member inan opening in themasonry. Leave a gapfor sealant between themasonry and thevertical. Fasten sillanchor to vertical usingS139 fasteners. Headanchor is similar. Place a shim (not byTubelite) under the sillanchor, and butt the sillanchor against the sideof the mullion, as shownin Figure 8.S139Figure 8: Butt the sill anchor against the side of the mullion.Step 13: Fasten SillAnchor to Masonry Using the hole in the sillanchor clip as a guide,drill a hole into themasonry for the anchorbolt. Place a locking lug onthe anchor clip and awasher over the lockinglug as shown in Figure 9.Then fasten the anchorclip to the masonry withthe anchor bolt (not byTubelite) shown in theshop drawings. Headanchor is similar.Anchor bolt(not byTubelite)LockinglugFigure 9: Place a locking lug on the anchor clip and awasher over the locking lug, then fasten an anchor bolt (notby Tubelite) to the masonry.Revised April 2014dependable@tubeliteinc.comPage 19
200CW Installation InstructionsStep 14: SlideHorizontal OntoShear Block Seal the perimeterof the shear block tothe mullion. Seal the ends ofthe horizontal thatwill attach to thevertical. Slide the end of thehorizontal onto theframe clip, andfasten the horizontalto the frame clipusing two S270fasteners, as shownin Figure 10. Seal fastenerheads.Seal perimeterof shear blockSeal ends ofhorizontalS270Cap sealFigure 10: Slide the end of the horizontal onto the shear block andfasten using two S270 fasteners.Step 15: Slide HorizontalOnto Sill Anchor Clip Seal the perimeter of thesill anchor to the mullion. Seal the ends of thehorizontal that will attachto the vertical. Slide the end of the sillonto the sill anchor clip,and place shims under thesill as necessary to makeit level, and to create asealant gap. Slide the end of thehorizontal onto the frameclip, and fasten thehorizontal to the frame clipusing two S270 fasteners,as shown in Figure 11. Seal fastener heads. For perimeter anchoringand connection details, goto page 30.Revised April 2014Seal perimeterof sill anchorSeal ends ofhorizontalS270Cap sealFigure 11: Slide the end of the horizontal onto the sill anchor andfasten using two S270 fasteners.dependable@tubeliteinc.comPage 20
200CW Installation InstructionsStep 16: SealJointsBetweenVerticals andHorizontals Seal the jointsbetweenverticals andhorizontals, asshown in Figure12. Tool thesealant into thevoids, andclean offexcess sealant.SealantFigure 12: Seal the joints between verticals and horizontals.PTI 707 butyl sealantor equivalentStep 17: InstallWater Dams Wherever ahorizontal meetsa vertical, applya bead of butylsealant acrossthe verticalmember, asshown in Figure13. Insert a waterdam into the gapbetween thehorizontal andvertical memberswhere the sealantwas just applied.Revised April 2014PTI 707 butylsealant orequivalentWater damFigure 13: After sealing the gap between the horizontal andvertical, insert a water dam into the gap.dependable@tubeliteinc.comPage 21
200CW Installation InstructionsStep 17: Install Water Dam (SSG) Wherever a horizontal meets an SSG vertical, apply a bead of butyl sealant acrossthe vertical member, as shown in Figure 14. Insert a water dam into the gap between the horizontal and vertical members wherethe sealant was just applied.PTI 707butylsealant orequivalentPTI 707 butylsealant orequivalentWater dam(P1629)Figure 14: After applying sealant to the gap between the horizontal and vertical, insert a waterdam into the gap.Revised April 2014dependable@tubeliteinc.comPage 22
200CW Installation InstructionsStep 18: ApplySealant AroundWater Dam Apply a bead ofbutyl sealant aroundthe perimeter of eachwater dam. Also applysealant across thefront of the water damstretching across thetongue of the verticalmember, as shown inFigure 15. Tool the sealant intoall voids and tool toensure the sealant willnot contact the edgeof the glass. Infiltrated water mustalso be able to passfreely around theglass and out theweep hole.Step 19: Press VerticalGaskets Into VerticalMembersWaterflowPTI 707 butylsealant orequivalentFigure 15: Apply a bead of sealant around the perimeter of eachwater dam.GasketGasket Seal the heads of theS270 fasteners on thehorizontal member. Press the verticalgaskets into their regletson the vertical member,as shown in Figure 16.Press the ends of thegaskets into the sealantaround the water dams.Figure 16: Press the vertical gaskets into theirreglets on the vertical member.Revised April 2014dependable@tubeliteinc.comPage 23
200CW Installation InstructionsStep 20: Press Horizontal Gaskets Into Horizontal Members Apply butyl sealant where the vertical gaskets will meet the horizontal gaskets asshown in Figure 17. Press horizontal gaskets into their reglets on the horizontal back members asshown in Figure 18. Press the ends into the sealant.PTI 707butylsealant orequivalentFigure 17: Apply butyl sealant where the vertical gaskets will meet the horizontal gaskets.GasketGasketFigure 18: Press the horizontal gaskets into their reglets on the horizontal member.Revised April 2014dependable@tubeliteinc.comPage 24
200CW Installation InstructionsStep 21: Place SettingBlocks Place setting blocks atthe quarter points of eachlight (two setting blocksper light) or as required byshop drawings, as shownin Figure 19. Use P946 for 1" glassand P948 for 1/4" glass.Setting blockFigure 19: Place setting blocks at the quarter point ofthe light or as required by shop drawings.Revised April 2014dependable@tubeliteinc.comPage 25
200CW Installation InstructionsStep 22:Install Glass Glass size iscalculated asdaylightopening 1"horizontallyand vertically. Place glasson settingblocks, asshown inFigure 20.GlassGlassFigure 20: Place glass on setting blocks.Step 23: PressGlazing GasketsInto VerticalPressure Plate Press glazinggaskets (PTB28)into the reglets ofthe verticalpressure plate, asshown in Figure21.Figure 21: Press glazing gaskets into the reglets of the vertical pressureplate.Revised April 2014dependable@tubeliteinc.comPage 26
200CW Installation InstructionsStep 24: FastenVertical PressurePlate and Snap-onCover Fasten the verticalpressure plate to themullion as shown inFigure 22 with anS357 fastener andglazing gaskets(PTB28). Torque of 30-40in.-lbs. should beused to fasten thepressure plate. Install the verticalsnap-on cover asshown in Figure 22.S357PressureplateSnap-on coverFigure 22: Place the vertical pressure plate and snap-on cover.Step 25: PressGlazingGaskets IntoHorizontalPressure Plate Press glazinggaskets(PTB28) into thereglets of thehorizontalpressure plate. Butter theends of thegaskets in thehorizontalpressure platewith butylsealant asshown in Figure23.Revised April 2014Gasket(PTB28)PTI 707 butylsealant orequivalentFigure 23: Butter the ends of the gaskets in the horizontal pressure platewith butyl sealant.dependable@tubeliteinc.comPage 27
200CW Installation InstructionsStep 26: FastenHorizontal PressurePlate Into Place Fasten thehorizontal pressureplate in place with anS357 fastener asshown in Figure 24. Torque of 30-40in.-lbs. should beused to fasten on thepressure plate. Seal the jointbetween thehorizontal pressureplate and the verticalsnap-on cover, andtool the sealant intothe void, as shown inFigure 25.S357Figure 24: Fasten the horizontal pressure plate into place.SealantFigure 25: Seal the joint between the horizontal pressure plate and vertical snap-on cover.Revised April 2014dependable@tubeliteinc.comPage 28
200CW Installation InstructionsStep 27: SealHorizontalPressure PlateFastener Seal the head ofthe fastenerholding thehorizontal pressureplate, as shown inFigure 26.SealantFigure 26: Seal the head of the fastener holding the horizontalpressure plate.Step 28: InstallHorizontalSnap-on Cover Install thehorizontalsnap-on coveras shown inFigure 27.Figure 27: Install the horizontal snap-on cover.Revised April 2014dependable@tubeliteinc.comPage 29
200CW Installation InstructionsStep 29: Seal thePerimeterSealant Insert a backer rodinto the gapbetween the frameand the buildingsubstrate on the top,sides and bottom ofthe installation asshown in Figure 28. Apply sealant to fillthe void. Tool the sealantsmooth.BackerrodSealantBuilding substrateFigure 28: Insert a backer rod into the gapbetween the frame and the building substrate.Revised April 2014dependable@tubeliteinc.comPage 30
200CW Installation InstructionsCONNECTION AT PERIMETERReturn Leg Pressure Plate pressureplateS357SnapcoverAssembly Install glazing gaskets (PTB28) in the reglets of the vertical mullion. Install the glass. Attach glazing gasket to pressure plate. Install the return leg pressure plate to the vertical mullion using S357 fasteners. Install the snap cover to the pressure plate.Revised April 2014dependable@tubeliteinc.comPage 31
200CW Installation InstructionsF Perimeter Runner OptionDow Corning 995sealant orequivalentBackmemberGlassF perimeterrunnerGlazing gasket(PTB28)Dow Corning 995sealant orequivalentPressure plateS357Snap coverAssembly Install an F perimeter runner in the frame opening. Install glazing gaskets (PTB28) in the reglets of thevertical mullion. Apply structural sealant in corner between F perimeterrunner, vertical mullion and glazing gasket, as well aswhere the F perimeter runner will meet the pressureplate. Install the vertical mullion next to the F perimeterrunner. Install the glass. Attach glazing gaskets to pressure plate. Install the pressure plate to the vertical mullion usingS357 fasteners. Install the snap cover to the pressure plate.Revised April 2014dependable@tubeliteinc.comPage 32
200CW Installation InstructionsCORNER CONDITIONSOutside 90 Degree CornerGlassDow Corning 995sealant orequivalentBack memberOS adapterSpacerCorning 9#10 x 1 1/8"Type B (not byTubelite)Dow Corning 995 sealant or equivalentGlassDow Corning 995sealant orequivalentAssembly Attach an OS adapter (E2101) to theback member. Attach a pair of modified spacers(PTB75) to the OS adapter. Apply structural sealant beside thespacers. Set the glass. Apply structural sealant between glass.Revised April 2014dependable@tubeliteinc.comPage 33
200CW Installation InstructionsSUNSHADE ATTACHMENTBack memberS424Sunshadeattachmentbracket (P3908)Assembly Pre-drill holes at least 3/4" deep into the tongue of the back member where the S424 fasteners will go. Attach sunshade attachment brackets (P3908) to vertical mullion using eight S424 fasteners.Revised April 2014dependable@tubeliteinc.comPage 34
200CW Installation InstructionsSUNSHADE ATTACHMENTSunshadeattachmentbracket (P3908)BackmemberNotched facecover (E0992)SunshadeoutriggerS365SealantAssembly Notch a face cover (E0992) to fit around the sunshade attachment brackets, then install the face coverto the vertical. Seal perimeter of notch when face cover is installed. Using eight S365 fasteners, attach the sunshade outrigger to the sunshade attachment brackets.Revised April 2014dependable@tubeliteinc.comPage 35
Step 5: Mill Weep Slot in Horizontal Snap-on Cover Step 6: Drill Slots in Horizontal Step 7: Notch Sills and Heads Step 8: Notch Horizontal in Final Bay (if necessary) . glazed system P945 Water dam for silicone glazed verticals P1629 P1265: .3125" hole diameter P1266: .375" P1267: .4375" Locking lug Shear block P1320A: 4" back member P1320B: 6"