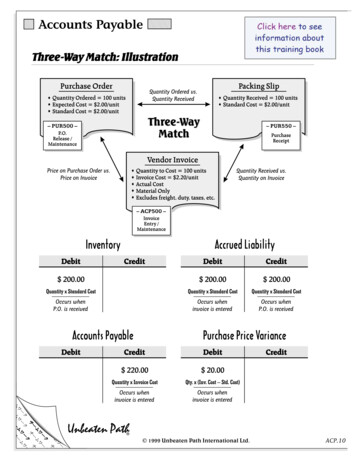
Transcription
Accounts PayableThreeWay Match: IllustrationThreeee-W 1999 Unbeaten Path International Ltd.ACP.10
InventoryInventory BPCSPInventoryBPCSPrroduct Integration Itemplanning parameters,demand and current levels ofInventory determine what shouldbe made or bought InventoryaccountsEntry fortransactions Journal Inventoryvalidation of CustomerOrder Allocations Relieve Allocations Relieve Inventory Costsposted fromother products arefed back to Inventory Requirementscode Warehouse information Item Listdescription ItemPrice Description Forecast flagshipment history User-definedgroup codes P.O.quantities areordered andreceivedCosts Purchase Price Variance Accrued liability accounts Commission Standardplanning parameters, demandand current levels of Inventorydetermine the material plan Set Inventory Shop orderbalancesallocations Issues to shop orders Receipts from shoporderscode Item Itemplanning parameters,demand and current levels ofInventory determine whatshould be made or boughtup ItemBills ofMaterial Set up ItemRoutings 1999 Unbeaten Path International Ltd.INV.2
Manufacturing Data ManagementWork Center Cost Loading Code & Cost Bucket DefinitionsCost Loading CodeNo Hours0Could be used when a work center represents an outside operation (e.g. toaccumulate overhead costs)Machine Hours1Machine hours that represent automated operations with no operatorinterventionSetup Hours2Setup or teardown timeSetup & Machine Hours3Combination of 1 & 2Run Hours4Labor / operator hoursSetup & Run Hours5Combination of 2 & 4Run & Machine Hours6Combination of 1 & 4Indirect Hours7May be used for hours not directly related to production (e.g. to accumulatehousekeeping costs)Setup, Run & Machine Hours8Combination of 1,2 & 49Could be used to accumulate a percent of a cost rate (#1–4 above) for thework center. The corresponding “% of Rate” field points to the cost rate touse for the calculation. Ordinarily used to calculate overhead as a percent oflabor rate / machine rate.PercentageCost Bucket Code ExamplesFull DescriptionShortDescriptionCostTypeRoll-Up toBucket #1Fabrication Hour LaborFab LaborL12Setup Hour LaborS/U LaborL23Run Hour Labor – “Manual”Run LaborL34Outside Processing MaterialOP Mat’lM45Raw Material & Purchased PartsMaterialM56Indirect Labor “Supervisor”IndirectO67Outside OverheadOH–OutsideO78Fixed OverheadOH–FixedO89Variable Overhead – %OH–Var–%O9Bucket # 1999 Unbeaten Path International Ltd.MDM.16
Capacity PlanningCapacity Planning PPrrocess Flow CAP.3 1999 Unbeaten Path International Ltd.
Configurable LedgerConfigurable Ledger Posting CyclePosting 1999 Unbeaten Path International Ltd.CLD.14
Cost AccountingBPCS Systems Logic for Calculating Routing CostsBPCSRouting Unbeaten Path 1999 Unbeaten Path International Ltd. CST.12
CST.13❷At the Workcenter file, the system determines the Cost Loading Codes toapply.❸Based upon the Cost Loading Codes found, the system will determine theLoad Hour fields to be used (as stated at the System Parameter level).❹The system goes to the Routing file to gather the Load Hours applicable anddetermine the Basis Code rule to be used.❺The system calculates the Standard Cost by multiplying the hours per piece(drawn from the Routing file) by the rate per piece (drawn from theWorkcenter file).❻At the Workcenter file, the system determines which Standard Cost Bucket isassigned to the rate used to calculate the Standard Cost (Step 5). The systemthen moves the calculated Standard Cost into that Cost Bucket within the CostMaster File (CMF).❼The system moves to the next applicable Rate (in the Workcenter file) andrepeats the process until all applicable rate values are satisfied. In theexample on the previous page, the next applicable rate is Rate 4. Rate 4 is apercentage (see Cost Loading Code 9) of Rate 1. The Standard Cost iscalculated as follows: 235% x 14.20 x [(5.50 1.75) / 100] 2.42Item Standard Cost Bucket 5 is assigned to Rate 4,so the calculated Standard Cost of 2.42 is transferred to Standard Cost Bucket5 within the Cost Master File (CMF).Cost Accounting For a given item, the system goes to the Routing file to determine theWorkcenter number.BPCSRoutingBPCS Systems Logic for Calculating Routing Costs 1999 Unbeaten Path International Ltd.❶
Configurable Order ManagementConfigurable Order Mgmt. BPCOrderBPCSPrroduct IntegrationSP On-Order PickedAmounts Item Details Lot Details Quantity On Hand Customer Order CustomerDetails MaterialAllocationsOrders OrderDetails NeedStatusDates PaymentAgreementDetails Planning Bills Multiple Currencies Parameters Forecast Foreign ExchangeBasis DataReservations ATP Ship-toWarehouseDetailsCalendar Shop Incentives ResupplyOrders ShippingCalendar Promotion FeaturesandOptionsDetails Promotionand DealsTrackingCalendar Customer OrderDetails 1999 Unbeaten Path International Ltd.COM.2
Master Production SchedulingOrder Policy CodesOrderPolicyItem Master FieldsOrder PolicyLotSize(X required field)IncrementalOrder Qty.Order A. DiscreteF. Least CostG. Period Order.Quantity.(variable period)Holding CostPercentageXH. Discrete Abovethe StandardLot SizeXI. IncrementalAbove StandardLot SizeXJ. Multiple of theStandard LotSizeXDefault PeriodDays*XK. Period Order.Quantity.(fixed period)X**Blank Order PolicyCode (ReorderPoint)****The system default Period Days for Order Policy G (Period Order Quantity) are defined in the SYS800Parameters Generation Program: Days for period lot sizing.**The Period Days for Order Policy K (Period Order Quantity for fixed defined period) are defined in JIT100 /SYS800 JIT Planning Period Data Maintenance.*** Item not planned by MRP. MPS.9 1999 Unbeaten Path International Ltd.
CST.13 Cost Accounting BPC S Systems Logic for Calculating R outing Costs For a given item, the system goes to the Routing file to determine the Workcenter number. At the Workcenter file, the system determines the Cost Loading Codes to apply. Based upon the Cost Loading Codes found, the system will determine the Load Hour fields to be used (as stated at the System Parameter level).