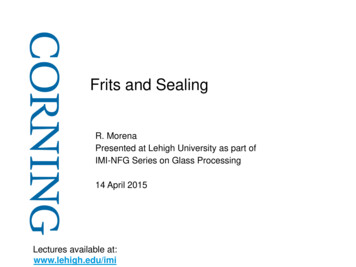
Transcription
Frits and SealingR. MorenaPresented at Lehigh University as part ofIMI-NFG Series on Glass Processing14 April 2015Lectures available at:www.lehigh.edu/imi
Powdered glasses (frits) Sealing Frits – Coatingsglazes –glaze (with opacifiers, colorants)ceramicporcelain enamel ground coat cover coatmetal.Science & Technology 2015 Corning Incorporated2.
Starting point Frits – finely powdered glasses that when re-heated will sinter,soften, and flow to form a seal or a coating(heat)At start:unconsolidated frit powderAt finish:strong, hermetic sealor impervious coating.Science & Technology 2015 Corning Incorporated3.
Overview Brief introduction, frits vs bulk glasses Selection criteria for design of frit composition Processing of frits.Science & Technology 2015 Corning Incorporated4.
Bulk glass vs frit behavior By definition, glass is a thermodynamically unstable structure. Converting a bulk glass to a fine powder only increases itsinstability. Relatively few bulk glasses are stable as frits, but will crystallize toat least some extentBULK GLASSPROPERTIES?FRITPROPERTIES.Science & Technology 2015 Corning Incorporated5.
SnO-ZnO-P2O5 systemStable low temperature fritswith good aqueous durability.Science & Technology 2015 Corning Incorporated6.
Classifications of frits Vitreous – remains glassy throughout sealing cycle; will softenand flow if re-heated Devitrifying – initially glassy, but at some point during sealingcycle will crystallize to form a hard, rigid bond. If reheated, will notflow and soften. Typically, vitreous frits are desired where seals are subjected torepeat thermal cycling; devitrifying frits are preferred forapplications in which the seal will be exposed to high operatingtemperatures.Science & Technology 2015 Corning Incorporated7.
Selection criteria for design of fritcomposition Maximum permissible sealing temperature CTE of materials to be bonded (CTE compatibility) Use temperature of sealed assembly Other – durability, strength, hermeticity, required lifetime,IR absorbance.Science & Technology 2015 Corning Incorporated8.
Frit-sealing:SOFC (solid oxide fuel cells)Frit sealRequirements:Max. sealing temp: 900 CTE: 110-120Service temp: 750ºOther: alkali-free, hermeticduring extended (10Y) servicetime in H2 environment.Science & Technology 2015 Corning Incorporated9.
Frit-sealing: OLED devicesFrit sealRequirements:Max. sealing temp: 450 CTE: 30-35Service temp: RTOther: hermetic during5Y lifetime; laser-sealablesince temp duringsealing must be 100º1mm from seal edge.Science & Technology 2015 Corning Incorporated10.
Frit-sealing: Micro-reactors for chemicalsynthesisMicro-reactorsRequirements:Max. sealing temp: 800 CTE: 35-40Service temp: -50º to 50ºOther: high chemical durability(acids and bases).Science & Technology 2015 Corning Incorporated11.
Sealing temperature
For a frit, flow is everything – main determinantof sealing temperatureStraight 109 PSlt. Rounding 108 PRounding107 PFlowed104-105 PPuddled 103 P.Science & Technology 2015 Corning Incorporated13.
For a frit, flow is everythingOptimum viscosityrange for sealingStraight 109 PSlt. Rounding 108 PRounding107 PFlowed104-105 PPuddled 103 P.Science & Technology 2015 Corning Incorporated14.
Selection criterion: Flow For strongest seal, seal temperature should correspond tothe softening range of the fritSoftening range viscosity of several 80CTE frits for 700º se aling9.59just right atsealing templog(viscosity, P)8.5too stiff atsealing temp8too fluid atsealing temp7.576.5Ca-Zn-silicateV-borate6Sr,Ca alumino re, degC.Science & Technology 2015 Corning Incorporated15.
Flow evaluationFrit AFrit B.Science & Technology 2015 Corning Incorporated16.
9.59.59.09.0Log (Viscosity, P)Log (Viscosity, P)Viscosity curves in softening 090Temperature (ºC)Frit Aafter firing @ 900º-1hr1100700725750775Temperature (ºC)Frit Bafter firing @ 800º-1hr.Science & Technology 2015 Corning Incorporated17.
Temperature interval between Tg and Tx (onset)is best comparative predictor of flow.Science & Technology 2015 Corning Incorporated18.
Tg is highly composition sensitive450Tg for SnO-ZnO-P2O5 frits at 33% P2O53503002500102030408Tg (oC)40050SnO/ZnO molar ratio at 33% P2O5.Science & Technology 2015 Corning Incorporated19.
Expansion compatibility
Expansion compatibility Mismatch stresses from CTE differences can result in seal failureeither during sealing, or in subsequent service. Measurement of mismatchButt sealInverse sandwich sealExpansion mismatch (δ) T (αf – αg)residual stress,residual strain.Science & Technology 2015 Corning Incorporated21.
Selection criterion:Expansion compatibility: microreactor frit Perfect expansion match between a frit and a substrate is unlikely(different curvatures to expansion curve)200butt seal, BM-5 friton EAGLE glassCTE Mismatch, ppm15010050Frit inTension00100200300400500600700800900Frit inCompression-50-100Temperature, C.Science & Technology 2015 Corning Incorporated22.
Expansion compatibilityK-borosilicate frits fired on EAGLETG at 800deg160frit cracked140Mismatch, ppm12010080604020(frit in e, degC.Science & Technology 2015 Corning Incorporated23.
CTE compatibility: use of fillers Fillers are added to adjust CTE of base fit Types of fillers– Additive – depend on Rule of Mixtures– Inversion depend on volume change associated with phasetransformation to adjust CTE difficult to retain hermeticity because of localizedmicrocracking PbTiO3, [Co,Mg]2·P2O7.Science & Technology 2015 Corning Incorporated24.
Effect of filler additions Will adjust CTE, α α1K1V1 α2K2V2 (for additive fillers)K1V1 K2V2 Will affect flow, and raise viscosity (and most likely, sealingtemperature)V-phosphate frit with different filler loadings fired at 380 -1h.Science & Technology 2015 Corning Incorporated25.
Possible additive-fillers β-eucryptite, LAS glass-ceramic, Li2O.Al2O3.2SiO2(intrinsic) CTE -10x10-7/degC Stuffed β-quartz, ZnAS glass-ceramic, CTE 0x10-7/degC β-spodumene, LiZnMgAS, CTE 10x10-7/degC ZWP, Zr2(WO4)(PO4)2, CTE -30x10-7/degC Leucite, K2O·Al2O3·2SiO2, CTE 200x10-7/degC (Stabilized) ZrO2, CTE 110x10-7/degC.Science & Technology 2015 Corning Incorporated26.
Additive filler – β-eucryptiteFigure 1 - Effect of beta-eucryptite filler level on CTE of OLED fritCTE of frit as function ofblendβ-eucryptite level (wt basis)80100:07090:10-7 oCTE (10 / C)6085:155080:2075:254070:3030(data measured in cooling on bars first fired to 400o-1hr in N2)205075100125150175200225250Temperature (oC).Science & Technology 2015 Corning Incorporated27.
Expansion compatibility with display glass700(onset of cracking?)600Expansion Mismatch, ppm50040025% filler(badly cracked at RT)30030% filler20035% filler100(frit in tension,1737 in (frit in compression,1737 in tension)(samples fired in situ;measurements made during cooling)-200Temperature, deg C.Science & Technology 2015 Corning Incorporated28.
Inversion filler - (Co,Mg)2·P2O70.8(CoP2O7)-0.2(MgP2O7).Science & Technology 2015 Corning Incorporated29.
Inversion filler in fritExpansion Mismatch in Frit, ppm500400mismatch for butt seal,frit blend on fused silica(estimated mismatchcurve, no filler)300200(frit in 100(frit in compression)-200-300Temperature, oC.Science & Technology 2015 Corning Incorporated30.
Service temperature
Service temperature Considerations––––Frit viscosity (should be 1010 P for dimensional stability)Stable chemistry and microstructure needed for long survival timesNo reaction with substrateSoft vs hard seal –stress relief during cooling vs. dimensionalstability.Science & Technology 2015 Corning Incorporated32.
Frit microstructure may change at high servicetemperaturesAs-fired (850º-1hr)Frit AFrit BFrit CAfter aging (167hrs at 725º).Science & Technology 2015 Corning Incorporated33.
High temp frit coating for Pt(must withstand exposure at 1200deg)Frit 6253, fired 1300-hr.Science & Technology 2015 Corning Incorporated34.
Coating for SiC furnace tubes77607702Thermal aging samples (120hrs @1500 ).Science & Technology 2015 Corning Incorporated35.
Other criteria
Selection criterion: aqueous durability (frits forinsulating windows).Science & Technology 2015 Corning Incorporated37.
Near-IR Absorbance.Science & Technology 2015 Corning Incorporated38.
Selection criterion: compressive surface layerfor strengthNa & K diffusion profiles for frit on 2318 (fired 650o-30min)10.014.09.0Na2OWt. % K2O7.012.06.0approx. surface ofsubstrate glass5.011.04.010.03.0Wt. % Distance from frit surface into substrate glass (um).Science & Technology 2015 Corning Incorporated39.
Processing of frits
Frit pastes Although frits may be applied by a variety of techniques (screenprinting, doctor-blading, nozzle dispensing, etc), they are alwaysapplied as a paste or ink rather than as a powder. Paste frit powder solvent binders dispersants surfactants The paste is designed to exhibit a specific rheology needed for thedispensing method.Science & Technology 2015 Corning Incorporated41.
Changes in frit paste with temperatureDispensedpasteAfter organicburn-out(300-325o)After frit softeningand flow (500-600o).42Science & Technology 2015 Corning Incorporated42.
Furnace sealingTemperatureFrit flow and sealingBinder burn-out43Elapsed TimeScience & Technology. 2015 Corning Incorporated43.
Processing comparisonTemperatureLaser sealing(after organicsburn-out)Frit flow and sealingFurnace-sealingOrganicsburn-out44Elapsed TimeScience & Technology. 2015 Corning Incorporated44.
Laser-sealing process is very fast(cooling cycle once laser passes)Cooling550500Temperature, e,s.45Science & Technology 2015 Corning Incorporated45.
Close-up look at laser-sealingNear-IR laser, 5-50mm/secSubstrate glass is transparentto Near-IR, so all laser energyreaches bottom of fritLaser energy penetratesseveral microns into fritHeat is transmittedto top surface of frit600o.46Science & Technology 2015 Corning Incorporated46.
Acknowledgements I wish to acknowledge the contributions of my many colleagues atCorning Incorporated whose assistance, hard work, and ideaswent into the development of the materials in this presentation.Science & Technology 2015 Corning Incorporated47.
Frit-sealing: OLED devices Frit seal Requirements: Max. sealing temp: 450 CTE: 30-35 Service temp: RT Other: hermetic during 5Y lifetime; laser-sealable since temp during sealing must be 100º 1mm from seal edge