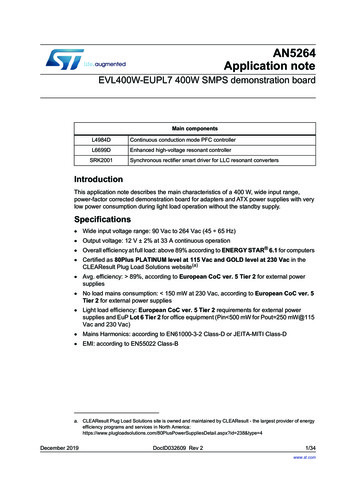
Transcription
AN5264Application noteEVL400W-EUPL7 400W SMPS demonstration boardMain componentsL4984DContinuous conduction mode PFC controllerL6699DEnhanced high-voltage resonant controllerSRK2001Synchronous rectifier smart driver for LLC resonant convertersIntroductionThis application note describes the main characteristics of a 400 W, wide input range,power-factor corrected demonstration board for adapters and ATX power supplies with verylow power consumption during light load operation without the standby supply.Specifications Wide input voltage range: 90 Vac to 264 Vac (45 65 Hz) Output voltage: 12 V 2% at 33 A continuous operation Overall efficiency at full load: above 89% according to ENERGY STAR 6.1 for computers Certified as 80Plus PLATINUM level at 115 Vac and GOLD level at 230 Vac in theCLEAResult Plug Load Solutions website(a) Avg. efficiency: 89%, according to European CoC ver. 5 Tier 2 for external powersupplies No load mains consumption: 150 mW at 230 Vac, according to European CoC ver. 5Tier 2 for external power supplies Light load efficiency: European CoC ver. 5 Tier 2 requirements for external powersupplies and EuP Lot 6 Tier 2 for office equipment (Pin 500 mW for Pout 250 mW@115Vac and 230 Vac) Mains Harmonics: according to EN61000-3-2 Class-D or JEITA-MITI Class-D EMI: according to EN55022 Class-Ba. CLEAResult Plug Load Solutions site is owned and maintained by CLEAResult - the largest provider of energyefficiency programs and services in North werSuppliesDetail.aspx?id 238&type 4December 2019DocID032609 Rev 21/34www.st.com34
ContentsAN5264Contents1Circuit description . . . . . . . . . . . . . . . . . . . . . . . . . . . . . . . . . . . . . . . . . . . 32Efficiency and no load consumption measurements . . . . . . . . . . . . . . 53Eco design requirement verification power supplies . . . . . . . . . . . . . . 84Harmonics content measurement . . . . . . . . . . . . . . . . . . . . . . . . . . . . . 105Functional check . . . . . . . . . . . . . . . . . . . . . . . . . . . . . . . . . . . . . . . . . . . 115.1Resonant stage waveforms . . . . . . . . . . . . . . . . . . . . . . . . . . . . . . . . . . . 115.2Startup . . . . . . . . . . . . . . . . . . . . . . . . . . . . . . . . . . . . . . . . . . . . . . . . . . . 125.3Dynamic load response . . . . . . . . . . . . . . . . . . . . . . . . . . . . . . . . . . . . . . 145.4Mains dips at half load . . . . . . . . . . . . . . . . . . . . . . . . . . . . . . . . . . . . . . . 155.5Burst mode operation at light load . . . . . . . . . . . . . . . . . . . . . . . . . . . . . . 155.6Overcurrent and short-circuit protection . . . . . . . . . . . . . . . . . . . . . . . . . . 166Thermal map . . . . . . . . . . . . . . . . . . . . . . . . . . . . . . . . . . . . . . . . . . . . . . 187Conducted emission pre-compliance test . . . . . . . . . . . . . . . . . . . . . . 198PFC coil specification . . . . . . . . . . . . . . . . . . . . . . . . . . . . . . . . . . . . . . . 208.19Electrical characteristics . . . . . . . . . . . . . . . . . . . . . . . . . . . . . . . . . . . . . . 20Transformer specification . . . . . . . . . . . . . . . . . . . . . . . . . . . . . . . . . . . 229.1Electrical characteristics . . . . . . . . . . . . . . . . . . . . . . . . . . . . . . . . . . . . . . 2210Motherboard and daughterboard layout . . . . . . . . . . . . . . . . . . . . . . . . 2411Support material . . . . . . . . . . . . . . . . . . . . . . . . . . . . . . . . . . . . . . . . . . . 3212Revision history . . . . . . . . . . . . . . . . . . . . . . . . . . . . . . . . . . . . . . . . . . . 332/34DocID032609 Rev 2
AN52641Circuit descriptionCircuit descriptionThe application architecture is made up of two stages: a front-end PFC pre-regulator basedon a CCM (continuous conduction mode) boost PFC controller, using the L4984, and adownstream LLC resonant half-bridge converter, designed around the L6699, providing a 12V regulated output voltage, dedicated to supplying ATX or similar applications requiring tomeet the most stringent efficiency and standby regulations.The main focus of this demonstration board is the light-load efficiency, achieved through theburst mode function of both PFC and LLC controllers and the self-adaptive deadtime of theL6699, modulated by the internal logic according to the half-bridge node transition times,which allows the maximization of the transformer magnetizing inductance, reducing theprimary current at light load operation.An active high voltage start-up circuitry based on a depletion MOSFET provides a very faststart-up time and minimizes the residual consumption during normal operation to anegligible level.The very high efficiency during normal load operation and the very small Heat Sink used atsecondary side is obtained by using synchronous rectification, based on the SRK2001.Figure 1. EVL400W-EUPL7: 400W SMPS demonstration boardDocID032609 Rev 23/3434
& Q) ; ) )86( & Q & Q / 927& 8-,1*5 5 & Q) ; ;, / 5(6,6725 0 18 // ''(' 29(5 ,& 7,0(5 *1' *' 9&& 5 ,& 0,& / ',19 &203 &6 3)& 2. 08/7 9)) ' 1 0 ' 1 0 %' ' ;% 6 B ( 7 6,1.a& Q) X) 9& & X) 9,6(1B % -3; / /65 & Q) ; 5 N Q)& 5 6 257('& Q)4 00%7 N5 ' // & 8; 3)& &' -3 1 0 /9* 5 N& Q)9%227 9* 5 N-3 0 /( ( '(5 3 5 N ' &66 ,& / ''(/ 1& 287 9&& &) 5)0,1 5 53)& 6723 *1' /9* 67% ,6(1 /,1( ',6 5 5 & Q& X) 95 N& Q) ; / 927& 8-,1**'B3)& 4 %66 & S5 0 & S)& Q)9 & 0 /( 675,3 ',5(&7/ 62/'(5(' 21 %27 6,'(6 0% '%5 N5 N 5 0 5 5& Q a- 0.'61 9DF 3 1 ( 57 5 0 5 0 5 0 5 N& Q)& Q)& X)5 N& Q)& Q & S)5 '9287B3)& 5 0 5 0 5 0 & Q & Q & X)5 .' // 5 55 N5 & Q) ; 5 1 0 ' 9 // &5 .5 N5 55 1 0 5 1 0 -3; 5 55 55 . & Q -3; 8 9 & & Q)' // 4 %66 5 5' / 43 B X ' 1 0 5 5' // & 8-,1* 5 & X) 9' // & 5 & ' 6 - & ' 1 0 ' // &5 1 0 5 5 5 55 54 1 0 ' 6736 & X) 9&5 5 5 1 0 5 54 1 0 5 N 5 N4 5 5 4 67) 1 0 5 5 ' & 57 17& 5 6 6 ( 7 6,1.9&& *1' ,& &9 /223 ,& &2//(&725 ,& (0,77(5 1 & 9* 287 1 & 9 & -3; 5677 6 )3 5 5 & S 9' // & 5 5' // & 5 5 5 N-3; & X) 95 55 5 5 N& S) 95 54 67) 10 14 67) 10 1& Q) 9& Q) 9& 1 0 & Q 5 N'5 9 N5 '5 & ' 60 - & 5 5 & 1 0 -3 5 1 0 -3 1 0 & X)5 N 76: ) ' 5 5 N& Q 5 N5 N5 5 N& X) Q 5 N 5 1 0 & 1 0 8-,1* 7 /3 6 ( 7 6,1. 9&& ,& 6) &9 /223 *1' ,& ,& 6) ,& &2//(&725 ,& (0,77(5 N 9'5 5 N* & X)5 55 5 ,& 65. (1 *' 352* 9&& *1' '96 696 *' 696 '96 6 ( 7 6,1. 65& & X) 9 & X) 9& X)5 5& Q)5 55 5 '5 * 4 67/ 1 ) 9S *1' 9P 2XW 9FF ,& 76& &,/7 4 1 0 5 1 0 / X P5 8-,1* 5 5 1 0 4 1 0 5 59287& X) 9& 1 0 5 1 0 & Q)& X)3&% 5HY (9/ : (83/ 5 1 0 5 1 0 ' 1 0 (9/65. 63) * 4 67/ 1 ) 5 55 & X) 9,& 760 ,'79&& *1' &&B287 &9B287 && 9B5() && &9 & X) 565& & X)& X)5 ,O GLVHJQR q GL SURSULHWj 67 FKH VL ULVHUYD L GLULWWL VDQFLWL GDOOH OHJJL7KH GUDZLQJ LV SURSHUW\ RI 67 WKDW UHVHUYHV WKH ULJKWV HQDFWHG IURP WKH ODZV 6KHHW' 60 - & RI- ) 6721 0 - ) 6721 0 % 5 5 5HY - ) 6721 0 - ) 6721 0 9 3&% 5(9 5 . 3&% 5(9 670LFURHOHFWURQLFV SSOLFDWLRQ /DE 2II /LQH 3RZHU 6XSSO\ %8 ,QGXVWULDO 0XOWLVHJPHQW 6HFWRU ,06 7XHVGD\ 0DUFK 'RFXPHQW 1XPEHU(9/ : (83/ 0% '%V6L]H 'DWH7LWOH 5HYLVLRQ 5HYLVLRQ 5HYLVLRQ & X) 5 55 4 67/ 1 ) 9 Q & & X) 95 N& X) 90 /( 675,3 ',5(&7/ 62/'(5(' 21 %27 6,'(6 0% '% 4 67/ 1 ) * & Q 5 N' ' ' ' 6 6 6 ,& (0,77(5 ' ' ' ' 6 6 6 ' ' ' ' 6 6 6 5& Q) & ' ' ' ' 6 6 6 N-3 % 1 0 &9 /223% 9 & 3&% 5(9 & 35,0 5 &21752//(5 ' 8* 7(5 %2 5' 67) 1 0 0 /( ( '(5 3 -3 % 0 /( 675,3 ',5(&7/ 62/'(5(' 21 %27 6,'(6 0% '% & 5 0 5 N5 N& Q)5 1 0 ,& &2//(&725 &7/9 ,/ 7/ / &21752/ %2 5' 5 0 5 .' 91 0 5 0 5 . 5 .5 N & 1 0 &% 5 1 0 4 1 0 5 1 0 % 9 % 109287B3)& 1 & 1 & /9* ,6(1B3)& *'B3)& 8; 3)& &' *1'*1' ,6(1B % & &'&% DocID032609 Rev 24/34AN5264Circuit descriptionFigure 2. Circuit diagram
AN5264Efficiency and no load consumption measurementsTable 1 shows the overall efficiency measurements at the nominal mains voltages. At 115Vac the full load efficiency is 89.8% and at 230 Vac it is 93.1%.Table 1. Overall efficiency measurements230 V-50 HzTest115 V-60 W][%][V][A][W][W][%]No ------100mW 36.7250mW 54.810% load 20% load 5% load eff.12.108.33100.82 108.2093.212.108.33100.79 109.3092.250% load eff.12.1416.50200.31 212.9094.112.1416.55200.92 217.8092.275% load eff.12.2225.00305.50 325.8093.812.2225.00305.50 335.7091.0100% load eff.12.3133.00406.23 436.3093.112.3133.00406.23 452.3089.8Avg. eff. 25%, 50%,75%, 100%93.591.3Figure 3. Efficiency measurementĨĨŝĐŝĞŶĐLJ ŵĞĂƐƵƌĞŵĞŶƚϵϲ͘Ϭ ϵϰ͘Ϭ ϵϮ͘Ϭ ĨĨŝĐŝĞŶĐLJ й 2Efficiency and no load consumption measurementsϵϬ͘Ϭ ϴϴ͘Ϭ ϮϯϬ s Ͳ ϱϬ ,njϴϲ͘Ϭ ϭϭϱ s Ͳ ϲϬ ,njϴϰ͘Ϭ ϴϮ͘Ϭ ϴϬ͘Ϭ йϵϬйϭϬϬйWŽƵƚͬWŽƵƚ͕ŵĂdžAt 100 mW load the efficiency is 36.7% at 115 Vac and 37.8% at 230 Vac. No loadconsumption at 115 V is around 121 mW and around 136 mW at 230 V. At 250 mW load theDocID032609 Rev 25/3434
Efficiency and no load consumption measurementsAN5264efficiency is 54.8% at 115 Vac and 56.1% at 230 Vac. Also at no load, the boardperformance is superior for a 400 W power supply: no load consumption at nominal mainsvoltage is lower than 150 mW.Measurement results at light load are reported in Table 2 and plotted in Figure 4. Efficiencyis better than 50% even with 250 mW output power.It should be highlighted that the measurements do not take into account the powerdissipation on the Cx discharge resistor, as it is not present here since different solutionscan be adopted to discharge Cx capacitors: a single resistor or a device enabling/disablingthe connection of the discharge resistor. In the case of a single resistor an additional powerloss due to the resistor should be considered.Table 2. Light load efficiency230 V-50 HzTest115 V-60 2609 Rev 2
AN5264Efficiency and no load consumption measurementsFigure 4. Light load efficiency diagram ŝŐŚƚ ůŽĂĚ ĞĨĨŝĐŝĞŶĐLJ ŝĐŝĞŶĐLJϲϬ͘ϬϱϬ͘ϬϮϯϬ s Ͳ ϱϬ ,njϰϬ͘Ϭϭϭϱ s Ͳ ϲϬ �Ϯ͘ϱϯϯ͘ϱϰϰ͘ϱϱϱ͘ϱWŽƵƚ t The measurements reported here following have been done according to therecommendation of this measurement procedure:1. Because the current flowing through the circuit under measurement is relatively small,the current measurement circuit is connected to the demonstration board side and thevoltage measurement input is connected to the AC source side. In this way the currentabsorbed by the voltage circuit is not considered in the measured consumptionamount.2. During any efficiency measurement remove any oscilloscope probe from the board.3. For any load measurement we apply a warm time of 20 minutes by each different load.Loads have been applied increasing the output power from minimum to maximum.4. Because of the input current shape during light load condition, the input powermeasurement could be critical or not reliable using a power meter in the usual way. Toovercome the issues, all light measurements have been done by measuring the activeenergy consumption of the demonstration board under test and then calculating thepower as the energy divided by the integration time. The integration time has been setas 36 seconds, as a compromise between a reliable measurement and a reasonabletime measurement time. The energy is measured in mWh, then the result in mW issimply calculated by dividing the instrument reading (in mWh) by 100. The instrumentused was Yokogawa, WT210 Power Meter.DocID032609 Rev 27/3434
Eco design requirement verification power supplies3AN5264Eco design requirement verification power suppliesIn the following tables the comparison between the regulation requirements for Eco designand the EVL400W-EUPL7 test results are reported: note that the design overcomes therequirements with margin.Table 3. ENERGY STAR requirements for computers ver. 6.1ENERGY STAR requirementsfor computers ver. 6.1:Test resultsLimits115 Vac - 60 Hz230 Vac - 50 HzEfficiency @ 20 % load91.392.3 82%Efficiency @ 50 % load92.294.1 85%Efficiency @ 100 % load89.893.1 82%Power factor0.990.97 0.9StatusPassTable 4. EuP Lot 6 tier 2 requirements for household and office equipmentTest resultsEuP Lot 6 Tier 2Limitsrequirements:115 Vac - 60 Hz230 Vac - 50 HzAvg. efficiency measured at25%, 50%, 75%, 100%91.393.5 87%Efficiency @ 250 mW load54.856.1 50%Efficiency @ 100 mW load36.737.8 33%StatusPassTable 5. European CoC ver. 5 tier 2 requirements for external power suppliesEuropean CoC ver. 5Tier 2 requirements forexternal power supplies:8/34Test resultsLimits115 Vac - 60 Hz230 Vac - 50 HzAvg. efficiency measured at25%, 50%, 75%, 100%91.393.5 89%Efficiency @ 10% load86.386.9 79%No load input power [W]0.1210.136 0.15 WDocID032609 Rev 2StatusPass
AN5264Eco design requirement verification power suppliesTable 6. 80Plus-Efficiency levelTest results80Plus-PLATINUMLimitsinternal nonredundantLimitsinternal nonredundant@ 115Vac@ 230VacPLATINUMGOLD115 Vac -230 Vac -60 Hz50 HzEfficiency @ 20% load90.41%91.33% 90% 90%Efficiency @ 50% load92.02%94.08% 92% 92%Efficiency @ 100% load89.41%93.52% 89% 89%Power factor @ 50%Load0.980.96 0.95 0.9DocID032609 Rev 2StatusPass9/3434
Harmonics content measurement4AN5264Harmonics content measurementThe board has been tested according to the European Standard EN61000-3-2 Class-D andJapanese standard JEITA-MITI Class-D, at both the nominal input voltage mains. Asreported in the following Figure 5 and Figure 6, the circuit is able to reduce the harmonicswell below the limits of both regulations. On the bottom side of the diagrams the totalharmonic distortion and power factor have been measured too. The values in all conditionsgive a clear idea about the correct functionality of the PFC.Figure 5. European Standard EN61000-3-2Class-D0HDVXUHG YDOXH-(,7 0,7, &ODVV ' OLPLWV DUP RQLF&XUUHQW @ DUPRQLF &XUUHQW @0HDVXUHG YDOXHFigure 6. JEITA-MITI at 100 Vac - 50 Hz, full load -(,7 0,7, &ODVV ' OLPLWV DUPRQLF 2UGHU Q@THD 16.8% - PF 0.9987 DUPRQLF 2UGHU Q@THD 3.38% - PF 0.9994Figure 7. Mains voltage and current waveforms Figure 8. Mains voltage and current waveformsat 230 V - 50 Hz - full loadat 100 V - 50 Hz - full loadTHD 17.1% - PF 0.998810/34THD 4.01% - PF 0.9995DocID032609 Rev 2
AN5264Functional check5Functional check5.1Resonant stage waveformsFigure 9. 115 Vac -60 Hz - full loadFigure 10. 115 Vac - 60 Hz - full load - voltage onthe resonant capCH1: ISEN LLCCH1:ISEN LLCCH2: LVGCH2: LVGCH3: HVGCH3: HVGCH4: HBCH4: C RESFigure 11. 115 Vac - 60 Hz - half loadFigure 12. 115 Vac - 60 Hz - half load - voltageon the resonant capCH1: ISEN LLCCH1:ISEN LLCCH2: LVGCH2: LVGCH3: HVGCH3: HVGCH4: HBCH4: C RESFigure 13 and Figure 14 show the waveforms during full load operation. It is possible to notethe measurement of the edges and the relevant deadtime.DocID032609 Rev 211/3434
Functional checkAN5264Figure 13. HB transition at full load - rising edgeFigure 14. HB transition at full load - fallingedgeCH1: ISEN LLCCH1: ISEN LLCCH2: LVGCH2: LVGCH3: HVGCH3: HVGCH4: HBCH4: HB5.2StartupThe waveforms relevant to the board startup at 115 Vac and full load have been capturedfocusing in Figure 15 on the PFC startup and in Figure 16 on the LLC startup. Note that theoutput voltage reaches the nominal value approximately 700 msec after plug-in.Figure 15. PFC startup at 115 Vac full loadFigure 16. LLC startup at 115 Vac full loadCH1: GD L4984CH1: CSSCH2: VOUT 12VCH2: ISENCH3: VCC L4984CH3: LVGCH4: BULK VOLTAGECH4: HBNote in Figure 17 that the start-up frequency has been set close to the smooth startfrequency during the initial 50 us.12/34DocID032609 Rev 2
AN5264Functional checkFigure 17. Safe-start at 115 Vac/60 Hz - full loadFsmooth start 167 kHzCH1: CF; CH2: ISEN; CH4: HBIn Figure 18 and Figure 19, the main L6699 pin signal has been measured during normaloperation at full load. Referring to Figure 18 we can note the signals:Figure 18. L6699 pin signals - 1Figure 19. L6699 control pin signals - 2CH1: DIS (it is at GND); CH2: LINECH1: RFMIN; CH2: STBYCH3: DELAY (it is at GND);CH3: CSS; CH4: CFCH4: ISEN ISEN pin (#6) matches the instantaneous current flowing in the transformer primary side.The L6699 integrates the anti-capacitive mode protection on pin #6; therefore it needs tosense the instantaneous value of the current to check the correct phase between thevoltage and current in the resonant tank. LINE pin (#7) divider has been dimensioned to start up the L6699 once the PFC outputvoltage has reached the rated value, in order to have correct converter sequencing, withPFC starting first and LLC starting later in order to optimize the design of the LLCconverter and prevent capacitive mode operation that may occur because of operation attoo low input voltage. DELAY pin (#2) is zero, as it must be during normal operation, because it works duringthe overcurrent protection operation. DIS pin (#8) is used for open loop protection and therefore, even in this case, its voltageis at ground level.DocID032609 Rev 213/3434
Functional checkAN5264In Figure 19 the pins dedicated to the control part of the L6699 are reported: RFmin pin (#4) is a 2 V (typ.) reference voltage of the oscillator; the switching frequencyis proportional to the current flowing out from the pin. CSS pin (#1) voltage is the same value as pin #4 because it is connected to the latter viaa resistor (R37), determining the soft-start frequency. A capacitor (C24) is also connectedbetween the CSS pin and ground, to set the soft-start time. At the beginning of L6699operation the voltage on the CSS pin is at ground level because C18 is discharged, thenthe CSS pin (#1) voltage increases according to the time constant till the RFmin voltagelevel is reached. STBY pin (#5) senses the optocoupler voltage; once the voltage decreases to 1.25 V, bothgate drivers stop switching and the circuit works in burst mode. CF pin (#3) is the controller oscillator; its ramp speed is proportional to the current flowingout from the RFmin pin (#4). The CF signal must be clean and undistorted to obtaincorrect symmetry by the half-bridge current, and therefore care must be taken in thelayout of the PCB.5.3Dynamic load responseThe EVL400W-EUPL7 has been connected to a dynamic load to measure the outputvoltage variations. The load changed every 400 ms from open load to 20 A load and viceversa, at 800 ma/μs. The response of the output voltage is shown with a ripple of about 600mV pkpk at 115 Vac-60 Hz.Figure 20. Dynamic load response: open load to 20 A and vice versa. 115 Vac-60 HzCH1: STBY; CH2: EAO; CH3: VOUT; CH4: IOUT14/34DocID032609 Rev 2
AN5264Functional checkFigure 21. Detail - open load to 20A loadCH1: STBY; CH2: EAO; CH3: VOUT; CH4: IOUT5.4Figure 22. Detail - 20A load to open loadCH1: STBY; CH2: EAO; CH3: VOUT; CH4: IOUTMains dips at half loadIn this test the EVL400W-EUPL7 has been checked against a 0 % mains dip (single linecycle, according to IEC61000-4-11) at both nominal voltages while operating at half load(16.5 A). The output voltages of the board and of the PFC are shown.Figure 23. Single cycle 100% mains dip at 115Vac - 60 Hz - half load (16.5 A)CH1: Vac; CH2: VPFC; CH3: VOUT5.5Figure 24. Single cycle 100% mains dip at 230Vac - 50 Hz - half load (16.5 A)CH1: Vac; CH2: VPFC; CH3: VOUTBurst mode operation at light loadIn Figure 25 some burst mode pulses are captured during 250 mW load operation. Theburst pulses are very narrow and their period is quite long, therefore the resulting equivalentswitching frequency is very low, ensuring high efficiency. The resulting output voltage rippleduring burst mode operation is about 100 mV peak-to-peak.DocID032609 Rev 215/3434
Functional checkAN5264Figure 25. Pout 250 mW, BM operationFigure 26. Detail of the BM pulseCH1: VOUT (AC COUPLED)CH1: ISEN; CH2: STBYCH2: STBY; CH3: LVG; CH4: HBCH3: LVG; CH4: HBIn Figure 26 the detail of the burst is reported: the first initial pulse is shorter than thefollowing ones avoiding the typical high current peak at half-bridge operation restarting, dueto the recharging or the resonant capacitor. The operating frequency of the half-bridgeduring burst mode is around 62 kHz.5.6Overcurrent and short-circuit protectionThe L6699 is equipped with a current sensing input (pin 6, ISEN) and a dedicatedovercurrent management system. In the case of overload, the voltage on the pin surpassesan internal threshold (0.8 V) that triggers a protection sequence. An internal switch is turnedon for 5 μs and discharges the soft-start capacitor. This quickly increases the oscillatorfrequency and thereby limits energy transfer. Under output short-circuit conditions, thisoperation results in a peak primary current that periodically oscillates below the maximumvalue allowed by the sense resistor.The converter runs under this condition for a time set by the capacitor on pin DELAY (pin 2).During this condition, the DELAY capacitor is charged by a 350 μA current from pin DELAY,generated by an internal current generator, and is slowly discharged by the external parallelresistor. If overload lasts, the voltage on the pin rises and when it reaches 2 V the soft-startcapacitor is completely discharged, so that the switching frequency is pushed to itsmaximum value, and the 350 μA current source is forced continuously on. As the voltage onthe pin exceeds 3.5 V, the IC stops switching and the internal generator is turned off, so thatthe voltage on the pin decays because of the external resistor. The IC is soft-restarted asthe voltage drops below 0.3 V. In this way, under short-circuit conditions, the converterworks intermittently with very low input average power. This procedure allows the converterto handle an overload condition for a time lasting less than a set value, avoiding ICshutdown in the case of short overload or peak power transients. On the other hand, in thecase of dead short, a second comparator referenced to 1.5 V immediately disablesswitching and activates a restart procedure.16/34DocID032609 Rev 2
AN5264Functional checkFigure 27. Short-circuit at 115 Vac/60 Hz - fullloadFigure 28. Short-circuit - zoom at 115 Vac/60Hz full loadCH1: ISEN; CH2: DELAYCH1: ISEN; CH2: DELAYCH3: CSS; CH4: HBCH3: CSS; CH4: HBIn Figure 27 a dead short-circuit event has been captured. In this case the overcurrentprotection is triggered by the second comparator referenced at 1.5 V which stops switchingby the L6699 and discharging of the soft-start capacitor; at the same time the capacitorconnected to the DELAY pin (#2) begins charging up to 3.5 V (typ.). Once the voltage on theDELAY pin reaches 3.5 V, the L6699 stops charging the delay capacitor and the L6699operation is resumed once the DELAY pin (#2) voltage decays to 0.3 V (typ.) by the parallelresistor, via a soft-start cycle. In Figure 28 details of peak current with short-circuit occurringis shown.If the short-circuit condition is removed, the converter restarts operation, otherwise, if theshort is still there, the converter operation results in an intermittent operation (Hiccup mode)with a narrow operating duty cycle of the converter, in order to prevent overheating of powercomponents, as can be noted in Figure 29.Figure 29. Short-circuit at 115 Vac/60 Hz - fullload Hiccup modeCH1: ISEN; CH2: DELAYCH3: CSS; CH4: HBDocID032609 Rev 217/3434
Thermal map6AN5264Thermal mapIn order to check the design reliability, a thermal mapping by means of an IR camera wasdone. Below, the thermal measurements of the board, component side, at nominal inputvoltage are shown. Some pointers, visible on the images, have been placed across keycomponents or components showing high temperature. The ambient temperature duringboth measurements was 25 C; a 7 cm diameter cooling fan was used during thermalmeasurement. It was placed at about 5 cm from the edge of the board below with respect tothe images. The air flow produced by the fan was 1,2 m/s at 15 cm away in central position.Figure 30. Thermal map at 90 Vac - 60 Hz - fullloadFigure 31. Thermal map at 230 Vac - 50 Hz - fullloadTable 7. Thermal maps reference points fig. 30 at 90 Vac - 60 Hz - full loadPointRef.DescriptionTemp. ( C)1L2Resonant transf. - secondary69.5 ºC2T1Common mode choke111.8 ºC3L4PFC inductor80.4 ºCTable 8. Thermal maps reference points fig. 31 at 230 Vac - 50 Hz - full load18/34PointRef.1T12SRK20013R3DescriptionTemp. ( C)Resonant transf. - secondary70.9 ºCSynchronous rectifier board60.4 ºCNTC 1R0-S23760.0 ºCDocID032609 Rev 2
AN52647Conducted emission pre-compliance testConducted emission pre-compliance testA pre-compliance test (testing environment not compliant) on conducted emission has beenperformed. The following images are the average and the quasi peak measurements ofconducted emission at full load and at the nominal mains voltages. The measurements havebeen taken with the ground AC input and the negative pole output of the board groundedand compared with the EN55022-ClassB limits. The converter is fed by AC line through anisolation transformer and the LISN. see Figure 33.Figure 32. EMI at 115 Vac - 60 Hz - full loadFigure 33. EMI at 230 Vac - 50 Hz - full loadDocID032609 Rev 219/3434
PFC coil specificationAN52648PFC coil specification8.1Electrical characteristics Converter topology: Boost, Continuous Conduction Mode Core type: QP3038-25H, MB4 or equivalent Min. operating frequency: 40 kHz Typical operating frequency: 70 kHz Primary inductance: 370 μH 10% at 1 kHz-0.25 V Supplier: YUJING TECHNOLOGY, PN: 11999-115H4001D/CFigure 34. Transformer pin-outTable 9. PFC coil winding dataZENTECH: WK5235, 502A, F 20KHz V 1.0V AT R (mΩ)L1230.1Ø*70c*1p(LITZ)Y48 0.5370 uH 10%160 max.L2410.3Ø*1p6 0.5--DocID032609 Rev 2
AN5264PFC coil specificationFigure 35. PFC coil mechanical aspectManufacturer YUJING TECHNOLOGY Inductor P/N: 1999-115H4001D/CDocID032609 Rev 221/3434
Transformer specificationAN52649Transformer specification9.1Electrical characteristics Converter topology: half-bridge, LLC resonant Core type: LP3925H-3C94 or equivalent Min. operating frequency: 65 kHz Typical operating frequency: 70 kHz Primary inductance: 720 μH 10% at 1 kHz-0.25 V Leakage inductance: 95 μH 10% at 1 kHz-0.25 VFigure 36. Transformer pin-outTable 10. Transformer winding dataZENTECH: WK5235, 502A, F 100KHz V 1.0 V AT 25ºCNo.StartFinishWireColorTurnsInductanceDCR (mΩ)L1420.1Ø*60c*1p(LITZ)Y33 0.5720uH 10%110 max.L2760.3Ø*1pY2 0.5--L39, 1011, 120.1Ø*250c*2p(LITZ)Y2 0.5--L413, 1415, 160.1Ø*250c*2p(LITZ)Y2 0.5--LK420.1Ø*60c*1p(LITZ)Y33 0.522/34DocID032609 Rev 295uH 10% @ Secondary Short
AN5264Transformer specificationFigure 37. Transformer overall drawingManufacturer YUJING TECHNOLOGY Transformer P/N: 1999-204H4002D/CDocID032609 Rev 223/3434
Motherboard and daughterboard layout10AN5264Motherboard and daughterboard layoutFigure 38. Motherboard top and bottom view24/34DocID032609 Rev 2
AN5264Motherboard and daughterboard layoutFigure 39. Control daughterboard top and bottom viewFigure 40. SR board top and bottom viewDocID032609 Rev 225/3434
Motherboard and daughterboard layoutAN5264Table 11. Bill of material - 1D15XB60HSingle phase bridge rectifierSHINDENGENC1220nF-X2X2 - film cap - R46 series, class X2, 310 Vac,110ºCKEMETC2, C3, C112n2-Y1Y1 safety cap. DE1E3KX222MMURATAC10N.M.C4, C5, C6470nF-X2X2 - film cap - R46 series, class X2, 310 Vac,110ºCKEMETC7470nF-X2X2 - film cap - R46 series, class X2, 275 Vac,110ºCKEMETC81000p-500V500 Vac CERCAP - 1206VISHAYC9330uF - 450VAluminum ELCAP - 330uF - 450V 20% LLG2W331MELA45
AN5264 Circuit description 34 1 Circuit description The application architecture is made up of two stages: a front-end PFC pre-regulator based on a CCM (continuous conduction mode) boost PFC controller, using the L4984, and a downstream LLC resonant half-bridge converter, designed around the L6699, providing a 12