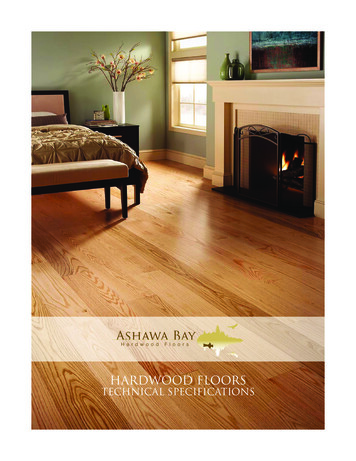
Transcription
Hardwood FloorsTechnical Specifications
Ashawa Bay Hardwood Floors Technical Specifications Unfinished Engineered Flooring General InformationUnfinished Engineered Flooring SpecificationsEngineered ConstructionEngineered Flooring Production Flow ChartEngineered Flooring Quality Control SummaryEngineered Flooring Quality Control ProgramEngineered Flooring Daily Quality Control ReportLumber Receiving and ProcessingVeneer Wear Layer ProductionEngineered Flooring ProductionEngineered Flooring PackagingPlywood Information and ProcessingPlywood Internal Bond TestingPlywood GOST StandardOven Dry MethodOven Dry Method EquipmentBond Line Test ProcedureEquilibrium Moisture ContentFlooring Bond Line Chisel TestFlooring Tongue and Groove Fit Test – Shake MethodFlooring Tongue and Groove Fit Test – Go/No GoMachine ToolingTooling DetailsSafety Data SheetFinishing ProcessCARB ComplianceStability of Wood SpeciesHardness of Wood SpeciesWarrantyRadiant Heat WarrantyGuide for Using the Oven-Dry Method for Determining the Moisture Content ofWoodInstallation Instructions: Staple or Nail DownInstallation Instructions: Glue DownInstallation Instructions: FloatingAmerican National Standard or Engineered Wood FlooringAshawa Bay Hardwood Floors9483 Ashawa Road, PO Box 398Cook, MN 55723800-788-9689
Unfinished Engineered Flooring General InformationOur Ashawa Bay Hardwood Floors unfinished engineered floors manufactured in Cook,Minnesota, at Hill Wood Products, Inc., are constructed using the following materials.Face wear layer:Standard wear layer thickness is 4.2 mm of sawn veneer, other thickness wear layers(3.2mm and 6mm) are used in custom products.Specie, grade, width, and length will vary by product and order.Domestic species:Our standard list of domestic species consists of:Red OakWhite OakR/Q Red OakR/Q White OakHard MapleCherryWalnutHickoryWe can offer many other species upon request.Plywood substrate:The standard plywood substrate is 12mm thick, Baltic birch, structural rated. Otherthicknesses are used for custom products, 9mm and 15mm are common.The adhesive is a type 1, exterior rated adhesive, conforming to NWFA standards.The plywood glue bond passes the NWFA bond line test standards.The 12mm substrate has 9 plies of birch veneer, 9mm has 7 plies, 15mm has 11 plies.Dimensions:The standard dimensions of our flooring are:Thickness 5/8” (1/2” and ¾” are options)Width 2.25” – 8” (max capability 10”)Length 2’-8’ (max capability 10’)Other dimensions, wear layer thickness, and plywood thickness are available as options.Laminating Adhesive:We use a water resistant PVA adhesive in bonding the wear layer to the plywood.The adhesive bond conforms to the NWFA bond line test standards.Ashawa Bay Hardwood Floors9483 Ashawa Road, PO Box 398Cook, MN 55723800-788-9689
Machining:We machine a standard tongue and groove along the sides of the flooring planks, as wellas end match the planks.Our standard profile is square edge and end.Microbevel edges and ends are available upon request, and are standard when prefinished.Stress relief cuts are made on the back side of each plank.Moisture Content:Our engineered flooring is manufactured to a moisture content of 6-9%.The environmental conditions before, during, and after installation should have atemperature range of 60-80 degrees F and relative humidity range of 35-50%.Packaging:Packaging3" 4" 6"2 1/4"5"7"8"2-8'32 ft230 ft226.66 ft218.66 ft221.33 ft22-10'40 ft237.5 ft233.33 ft223.33 ft226.66 ft2Installation Methods:Our engineered flooring can be installed as floating, glue down, or nail/staple downapplications. Detailed installation instructions on all methods are available.Ashawa Bay Hardwood Floors9483 Ashawa Road, PO Box 398Cook, MN 55723800-788-9689
Unfinished Engineered Flooring Specification Sheet for 5/8” thick x 2.25”, 3”, 4”,5”, 6”, 7”, 8” wide x 2-8’ length, select grade.1. Product ComponentsVeneer:Moisture Content 6-9%Type: Sawn, sanded 2 sides 80 gritThickness 4.2mmTolerance /-.01mm (.004”)Lengths 2’-8’Grade: Per orderPlywood:Moisture Content 6-9%Type 1, exterior ratedGrade: Baltic Birch or approved hardwood CP/CP or better 9 plyThickness Tolerance: 12mm /-.15mmLengths 2’-8’Glue:Type: PVA pre-catalyzed Type 1 water resistantEqualization:Difference veneer and plywood moisture: /-2%2. Dimensional TolerancesNominalToleranceLength L:Random 2’-8’Random 2’-8’Width W:2.25”, 3”, 4”, 5”, 6”, 7”, 8” 0.25 mm (.010”)Thickness T:0.619” 0.125 mm (.005”)Squareness:0.18 mm (.007”) per 25.4 mm (1”) of widthCup:Max. 0.20% across the width of a board;Edge Straightness:Max. 0.025% 0.7 mm (.028”) on 1200 mm (47.25”)Flatness:Max. 1.25% of lengthOverwood:Max. 0.38 mm (0.015”)Ashawa Bay Hardwood Floors9483 Ashawa Road, PO Box 398Cook, MN 55723800-788-9689length
3. Visual and Surface TolerancesSurface finish: Sanded 150 grit. Surface chatter/belt marks not allowedTear out/Chip out/Surface defect: Not visible from 1.5m (60”) distance viewing4. Packaging Requirements: Per Purchase orderAshawa Bay Hardwood Floors9483 Ashawa Road, PO Box 398Cook, MN 55723800-788-9689
Unfinished Engineered Flooring Specification Sheet for 11/16” thick x 2.25”, 3”, 4”,5”, 6”, 7”, 8” wide x 2-8’ length, select grade.1. Product ComponentsVeneer:Moisture Content 6-9%Type: Sawn, sanded 2 sides 80 gritThickness 6mmTolerance /-.01mm (.004”)Lengths 2’-8’Grade: Per orderPlywood:Moisture Content 6-9%Type 1, exterior ratedGrade: Baltic Birch or approved hardwood CP/CP or better 9 plyThickness Tolerance: 12mm /-.15mmLengths 2’-8’Glue:Type: PVA pre-catalyzed Type 1 water resistantEqualization:Difference veneer and plywood moisture: /-2%2. Dimensional TolerancesNominalToleranceLength L:Random 2’-8’Random 2’-8’Width W:2.25”, 3”, 4”, 5”, 6”, 7”, 8” 0.25 mm (.010”)Thickness T:0.697” 0.125 mm (.005”)Squareness:0.18 mm (.007”) per 25.4 mm (1”) of widthCup:Max. 0.20% across the width of a board;Edge Straightness:Max. 0.025% 0.7 mm (.028”) on 1200 mm (47.25”)Flatness:Max. 1.25% of lengthOverwood:Max. 0.38 mm (0.015”)Ashawa Bay Hardwood Floors9483 Ashawa Road, PO Box 398Cook, MN 55723800-788-9689length
3. Visual and Surface TolerancesSurface finish: Sanded 150 grit. Surface chatter/belt marks not allowedTear out/Chip out/Surface defect: Not visible from 1.5m (60”) distance viewing4. Packaging Requirements: Per Purchase orderAshawa Bay Hardwood Floors9483 Ashawa Road, PO Box 398Cook, MN 55723800-788-9689
Unfinished Engineered Flooring Specification Sheet for 3/4” thick x 2.25”, 3”, 4”,5”, 6”, 7”, 8” wide x 2-8’ length, select grade.1. Product ComponentsVeneer:Moisture Content 6-9%Type: Sawn, sanded 2 sides 80 gritThickness 4.2mmTolerance /-.01mm (.004”)Lengths 2’-8’Grade: Per orderPlywood:Moisture Content 6-9%Type 1, exterior ratedGrade: Baltic Birch or approved hardwood CP/CP or better 9 plyThickness Tolerance: 15mm /-.15mmLengths 2’-8’Glue:Type: PVA pre-catalyzed Type 1 water resistantEqualization:Difference veneer and plywood moisture: /-2%2. Dimensional TolerancesNominalToleranceLength L:Random 2’-8’Random 2’-8’Width W:2.25”, 3”, 4”, 5”, 6”, 7”, 8” 0.25 mm (.010”)Thickness T:0.740” 0.25 mm (.010”)Squareness:0.18 mm (.007”) per 25.4 mm (1”) of widthCup:Max. 0.20% across the width of a board;Edge Straightness:Max. 0.025% 0.7 mm (.028”) on 1200 mm (47.25”) lengthFlatness:Max. 1.25% of lengthOverwood:Max. 0.38 mm (0.015”)Ashawa Bay Hardwood Floors9483 Ashawa Road, PO Box 398Cook, MN 55723800-788-9689
3. Visual and Surface TolerancesSurface finish: Sanded 150 grit. Surface chatter/belt marks not allowedTear out/Chip out/Surface defect: Not visible from 1.5m (60”) distance viewing4. Packaging Requirements: Per Purchase orderAshawa Bay Hardwood Floors9483 Ashawa Road, PO Box 398Cook, MN 55723800-788-9689
Unfinished Engineered Flooring Specification Sheet for 1/2” thick x 2.25”, 3”, 4”,5”, 6”, 7”, 8” wide x 2-8’ length, select grade.1. Product ComponentsVeneer:Moisture Content 6-9%Type: Sawn, sanded 2 sides 80 gritThickness 3.2mmTolerance /-.01mm (.004”)Lengths 2’-8’Grade: Per orderPlywood:Moisture Content 6-9%Type 1, exterior ratedGrade: Baltic Birch or approved hardwood CP/CP or better 9 plyThickness Tolerance: 9mm /-.15mmLengths 2’-8’Glue:Type: PVA pre-catalyzed Type 1 water resistantEqualization:Difference veneer and plywood moisture: /-2%2. Dimensional TolerancesNominalToleranceLength L:Random 2’-8’Random 2’-8’Width W:2.25”, 3”, 4”, 5”, 6”, 7”, 8” 0.25 mm (.010”)Thickness T:0.475” 0.125 mm (.005”)Squareness:0.18 mm (.007”) per 25.4 mm (1”) of widthCup:Max. 0.20% across the width of a board;Edge Straightness:Max. 0.025% 0.7 mm (.028”) on 1200 mm (47.25”)Flatness:Max. 1.25% of lengthOverwood:Max. 0.38 mm (0.015”)Ashawa Bay Hardwood Floors9483 Ashawa Road, PO Box 398Cook, MN 55723800-788-9689length
3. Visual and Surface TolerancesSurface finish: Sanded 150 grit. Surface chatter/belt marks not allowedTear out/Chip out/Surface defect: Not visible from 1.5m (60”) distance viewing4. Packaging Requirements: Per Purchase orderAshawa Bay Hardwood Floors9483 Ashawa Road, PO Box 398Cook, MN 55723800-788-9689
Engineered ConstructionAshawa Bay engineered floors are constructed with high quality materials and made tolast. Some features of our flooring are:- CARB compliant (formaldehyde free) adhesive and plywood- Northern hardwood wear layers for consistent color and tight grain patterns- Manufactured in a humidity controlled environment for stability- Lifetime structural warranty- Available widths 2-1/4” to 10”- Available lengths 2’ – 10’- Available thickness ½”, 5/8”, ¾”4.2mm (3/16”) thick hardwoodwear layer sawn from lumber.Precision machined tongue andgroove on edges and ends.Baltic Birch plywood, 9 plies,structural rated, CARBcompliant, exterior ratedadhesive.Ashawa Bay Hardwood Floors9483 Ashawa Road, PO Box 398Cook, MN 55723800-788-9689
Engineered Flooring Production Flow ChartLumber is received fromsuppliers into warehouse.Plywood is received fromsuppliers into warehouse.Lumber processing center.Plywood processing center.Lumber is ripped to widthSurfaced to thicknessTrimmed to length and defectedPlywood is sanded to thicknessPlywood is scoredRipped to widthLumber blanks are sawn into wearlayersWear layers are sanded to thicknessWear layers are sorted, defected,graded, and staged for flooringproductionEngineered flooring processing center.Adhesive is applied to plywoodWear layers and plywood are laminated inpressFlooring blanks are sanded to thicknessTongue and grooves are machined onedgesTrimmed to length and end matchedPackaged and shrink wrappedPalletized for shipmentAshawa Bay Hardwood Floors9483 Ashawa Road, PO Box 398Cook, MN 55723800-788-9689
Processing CenterLumber receivingPlywood ReceivingLumber processingPlywood processingVeneer ProcessingFlooring laminatingFlooring machiningFlooring packagingDimensionMeasurementXXXXXPO d LineChisel Test TestAshawa Bay engineered flooring quality control summary listVisualInspectionXXXXXXXXXAdhesiveFit TestStress Test Application Rate T&GXX
Engineered Flooring Quality Control ProgramQuality control procedures are applied throughout the entire manufacturing process. Thefollowing is an outline of the quality control tests, measurements and other procedures.Lumber Receiving: Lumber shipments are received into the factory and inspected foracceptance. Visual inspection of overall quality of lumber: overall appearance and quality,defects, checking, stain.Frequency: each shipment received. Comparison with purchase order specifications: specie, grade, length, width.Frequency: each shipment received. Moisture content testing.Frequency: each shipment received.Specifications: MC acceptable range 6-9%, if the lumber is within this range itis cleared for processing. If the moisture content is not within the range, then thelumber is removed from production and conditioned to the acceptable range ofmoisture content.Tools and methods: A moisture meter is used to verify moisture content, if outsideof the acceptable range, then the oven dry moisture content testing procedure andequipment are applied.Lumber processing: As lumber is processed, each individual board is visually inspectedto determine the best yield possible. Each board is cut to size, surfaced, and defected pergrading rules of the flooring. Veneer blanks are the process output. Visual inspection of quality of rough lumberFrequency: continuous, every board is inspected, 100% Dimension measurement of length, width and thicknessFrequency: beginning of a production run and 1 time/hour of production.Tools and methods: micrometers are used to physically measure the width andthickness of lumber blanks after ripping trimming and surfacing.Specifications: internal specifications for target thickness, length, and width. Visual inspection and sorting of veneer blanksFrequency: 100% of veneer blanks are inspected and sorted for gradeSpecifications: internal grade rulesAshawa Bay Hardwood Floors9483 Ashawa Road, PO Box 398Cook, MN 55723800-788-9689
Plywood Receiving: Plywood shipments are received into the factory and inspected foracceptance. Visual inspection of overall quality of plywood: overall appearance and quality.Frequency: each shipment received. Comparison with purchase order specifications: specie, grade, length, width.Frequency: each shipment received. Moisture content testing.Frequency: each shipment received.Specifications: MC acceptable range 6-10%, if the plywood is within this rangeit is cleared for processing. If it is outside of acceptable range it is returned to thesupplier.Tools and methods: A moisture meter is used to verify the moisture content, if theresults are outside of the normal range, then the oven dry moisture content testingprocedure and equipment are applied.Plywood Processing: Plywood is sanded, scored, and ripped to width for engineeredflooring production. Visual inspection of overall quality, defects, voidsFrequency: continuous, every sheet of plywood is inspected, 100% Thickness measurement after sandingFrequency: at the start of each production run and 1 time/hour of production.Tools and methods: micrometers are used to physically measure the thickness ofthe plywood.Specifications: internal specifications for target thickness. Stress test prior to laminatingFrequency: continuous, every strip of plywood is inspected, 100%Tools and methods: an internally developed test method is followed.Specifications: pass/fail, if the plywood cracks or deflects beyond specifications itis removed from production and destroyed. Strips that pass the stress test aresuitable for flooring production.Ashawa Bay Hardwood Floors9483 Ashawa Road, PO Box 398Cook, MN 55723800-788-9689
Engineered Flooring Processing: Veneer wear layers and plywood are laminated intoflooring blanks, sanded, machined with tongue and groove on edges, end matched, andpackaged for shipping. Moisture content testing of flooringFrequency: 1 time/day of productionTools and methods: Oven dry moisture content testing procedure and equipment.Specifications: MC acceptable range 6-9%, if the batch of wear layers arewithin this range it is cleared for processing. If it is outside of acceptable range itis conditioned to within the acceptable range Visual inspection of adhesive application rateFrequency: continuous as the adhesive is applied to plywood, 1 time every hourafter the press operation.Tools and methods: Inspection for 100% adhesive coverage before pressing,squeeze out around the perimeter of the glue line after pressing. Bond strength testing after pressingFrequency: 1 time/day of productionTools and methods: chisel testSpecifications: pass/fail based on the chisel test results, failure results inproduction stoppage and machinery adjustment. Visual inspection for flatness after pressingFrequency: at the start of every production run and 1 time every hourTools and methods: visual inspectionSpecifications: if flooring is not flat it is measured for acceptance to internaltolerances, if out of tolerance the product is removed from production. Thickness after sandingFrequency: at the start of every production run and 1 time/hour of productionTools and methods: micrometers are used for accurate measurement of flooringthicknessSpecifications: internal targets and tolerances exist, if outside of tolerance thensander adjustments are made.Ashawa Bay Hardwood Floors9483 Ashawa Road, PO Box 398Cook, MN 55723800-788-9689
Width after machining tongue and groove on edgesFrequency: at the start of every production run, 1 time/hour of productionTools and methods: micrometers are used to measure the exact width of theflooringSpecifications: internal targets and tolerances exist, if outside of tolerance thenmachine adjustments are made. Edge tongue and groove fit after machiningFrequency: at the start of every production run, 1 time/hour of productionTools and methods: manual fit test, shake test, go/no go gauges Final fit and quality lay upFrequency: at the start of a production run, and1 time every hour of productionTools and methods: 10 – 20 square feet of flooring is placed on a flat table andput together as if being installed. The fit, squareness of ends, straightness ofedges, over wood, under wood, conformance to grade, and overall quality arevisually inspected.Specifications: results are compared to internal standards for the particular gradeof flooring being produced. Bond line testFrequency: each production runTools and methods: random samples are taken daily and tested per the bond linetest procedures.Specifications: Pass/fail. Visual packaging inspectionFrequency: continuous, every package is inspected after shrink wrapping, 100%.Tools and methods: visual inspection to insure the packages are properlypackaged and sealed prior to palletizing for shipment.Specifications: internal standards for package appearance and protection.Ashawa Bay Hardwood Floors9483 Ashawa Road, PO Box 398Cook, MN 55723800-788-9689
DateEngineered Flooring Daily Quality Control oThe tests below are to be done once per hour. Initial by test signifies test passed.Width8:30Lot #ThicknessResults1:3010:309:30Chisel Test (Pass/Fail)PO #Oven TestInitials2:303:30InitialsTemperature% RHTimeBuilding Humidification &Temperature ReadingsSpeciesChisel Test (Pass/Fail)4:30Oven TestWidthThicknessPO #TimeResultsInitialsFITThicknessWidthSquareness
Lumber Receiving and ProcessingWhen lumber is received, it is inspectedvisually for compliance in width, length, gradeand overall appearance compared to thepurchase order specifications.Moisture content verification: samples are cutrandomly from each unit of lumber and themoisture content is determined by the ovendry method.If the moisture content is within an acceptablerange 6-9%, the unit proceeds to be processed.As the lumber is processed each individual boardis visually inspected prior to processing.The lumber is then ripped, trimmed, and surfacedto desired size. Defects are cut from the boards.The lumber blanks are againvisually inspected and thenstacked by grade and size, readyto process into wear layers.Ashawa Bay Hardwood Floors9483 Ashawa Road, PO Box 398Cook, MN 55723800-788-9689
Veneer Wear Layer ProductionAshawa Bay floors manufactures hardwood veneer wear layers using framesawtechnology to achieve high yields and accurate thickness of the wear layers. The sawnveneers have a desirable look of a sawn plank and not the “plywood” look of rotaryproduced veneer products. The wear layers are sanded to tight tolerances and sorted pergrade prior to entering flooring production.Prepped lumber blanks areloaded into the infeed of the theframesaws for processing intoveneer wear layers.Veneer wear layers exit theframesaw, ready to sand tothickness tolerance.Veneer wear layers areinspected for quality, grade, andmeasured for thickness beforebeing stacked for flooringproduction.Ashawa Bay Hardwood Floors9483 Ashawa Road, PO Box 398Cook, MN 55723800-788-9689
Engineered Flooring ProductionAshawa Bay engineered flooring is produced using state of the art equipment along withtight quality control measures that results in a high quality flooring product.After laminating, each flooringplank is sanded to tighttolerances.Flooring planks flow throughthe machining process wherethe edges are machined with thetongue and groove, and the endsare trimmed square and endmatched with a tongue andgroove.Through each stage of theprocess the flooring width andthickness are measured withvery precise calipers to makesure the product is being madeto final tolerances.Ashawa Bay Hardwood Floors9483 Ashawa Road, PO Box 398Cook, MN 55723800-788-9689
Engineered Flooring Packaging - UnfinishedAshawa Bay engineered floors are packaged after production and prepared for shipping.The flooring is bundled per internal specifications of the proper number of pieces andsquare footage per package. The bundles are then end capped for protection fromshipping damage, and then shrink wrapped in plastic to protect the flooring frommoisture. The shrink wrapped bundles are then palletized for shipment.Bundles of flooring are endcapped with cardboard fordamage prevention.The flooring bundles are shrinkwrapped in plastic and labeled.The wrapped bundles arepalletized, edge protected,banded, and stretch wrapped inplastic for shipping.Ashawa Bay Hardwood Floors9483 Ashawa Road, PO Box 398Cook, MN 55723800-788-9689
Plywood Information and ProcessingAshawa Bay floors uses only structural rated Baltic Birch plywood in the construction ofour engineered flooring. Baltic Birch is recognized as the premium plywood substrate inengineered flooring due to the strength properties, lack of voids, exterior rated adhesive,and dimensional stability. The plywood suppliers produce the plywood to GOSTstandards and it is CARB compliant. We test the plywood for moisture content when itarrives at our factory and before we process it.Baltic Birch plywood arrivesinto our factory packaged incrates.Each individual sheet ofplywood is sanded to exactthickness tolerance prior to usein flooring manufacture.Each sheet of plywood is scoredwith grooves along the backside to relieve any internalstresses that may exist andallow the flooring to lay flat.Ashawa Bay Hardwood Floors9483 Ashawa Road, PO Box 398Cook, MN 55723800-788-9689
Plywood Internal Bond TestingThe internal bond (IB) test is a tensile test which a sample is loaded into a tensile testmachine and it is pulled apart. The resulting information is the number of pounds persquare inch are required to pull the sample apart. We use this test method whenanalyzing plywood options for use as substrate in the construction of engineered flooring.When compared to other plywood options used in the engineered flooring industry, BalticBirch plywood greatly out performs the others in IB strength. This is important since itmeasures the amount of stress a substrate can withstand prior to failure. The higher theIB strength, the lower the chance of substrate failure.This control chart illustratestypical IB values for BalticBirch plywood substrate.The average is 278pounds/square inch.The average IB values forcomparison of substrates:China hardwood import 127Aspen USA 140Baltic Birch 278Ashawa Bay Hardwood Floors9483 Ashawa Road, PO Box 398Cook, MN 55723800-788-9689
INTERGOVERNMENTAL STANDARDGOST 3916.1-96Plywood with faces in hardwood veneer for general use.Contents DESCRIPTION - GENERAL USE PLYWOOD CLASSIFICATION AND DIMENSIONS TECHNICAL REQUIREMENTS RULES OF ACCEPTANCE CONTROL METHODS TRANSPORTATION AND STORAGE PRODUCERS GUARANTEE Table: DESCRIPTION AND LIMITATIONS OF PLYWOOD DEFECTSSPECIFICATIONSIntroduction date: 01-01-19981. DESCRIPTION - GENERAL USE PLYWOODThis standard covers general use plywood with hardwood face veneer.This standard is not applicable to specialty or decorative plywood.Minimal requirements relating to the formaldehyde emission of plywood are covered in 4.3 and 6.8.3. CLASSIFICATION AND DIMENSIONS3.1. Plywood is subdivided into grades based on the following: appearance of face veneers, glue bond, the degree of moistureresistance of the bond, and if sanded or not.3.1.1. The plywood is subdivided into 5 grades, based on the appearance of the face veneers: E (elite), I, II, III and IV.Descriptions of the face grades of the plywood are specified in Supplement A.3.1.2. The degree of moisture resistance of the plywood bond is specified by the following marks: FSF - water proof plywood (WBP) FK - water resistant plywood (MR)3.1.3. The sanding if the plywood is specified as follows: Not sanded (NS) Sanded one side (S1) Sanded two sides (S2)3.2. Dimensions.3.2.1. The dimensions and the number of plies in the plywood sheets must correspond to tables 1 and 2.Table 1. Dimensions (millimeters)Lengt(width) of the plywood 440,25002700,2745,3050,3600,3660Min(Max)Tolerance in mm /- 3,0 /- 4,0 /- 4,0 /- 6,0Note: Production of plywood is allowed in other dimensions corresponding with the terms of a contract.Table 2. Thickness (millimeters)UnsandedNominalSanded Plywood Sanded PlywoodPlywoodthicknessof Number of Variance(mm)Min/Max (mm)3,0 mm3-ply 0,3/-0,4 0,4/-0,34,0 mm3-ply 0,3/-0,5 0,8/-0,46,5 mm5-ply 0,4/-0,5 0,9/-0,49,0 mm7-ply 0,4/-0,6 1,0/-0,512,0 mm9-ply 0,5/-0,70,6 1,1/-0,615,0 mm11-ply 0,6/-0,8 1,2/-0,718,0 mm13-ply 0,7/-0,9 1,3/-0,821,0 mm15-ply 0,8/-1,0 1,4/-0,9UnsandedPlywoodThicknessVariance(mm)1,01,5
24,0 mm27,0 mm30,0 mm17-ply19-ply21-ply 0,9/-1,1 1,0/-1,2 1,1/-1,31,0 1,5/-1,0 1,6/-1,1 1,7/-1,22,0Note: Production of plywood is allowed in other thickness and construction (number of plies) corresponding with the terms ofa contract. The minimum and maximum variances may be determined by the following formula.Sanded Plywood - maximum/minimum tolerance:1. Maximum: Thick * 0.03 mm 0.2 mm (12 mm*0.03 mm 0.2 mm) 12 mm 0.5 mm2. Minimum: Thick * 0.03 mm 0.4 mm (12 mm*0.03 mm 0.4 mm) 12 mm - 0.7 mmUnsanded Plywood - maximum/minimum tolerance:1. Maximum: Thick * 0.03 mm 0.8 mm (12 mm*0.03 mm 0.8 mm) 12 mm 1.1 mm2. Minimum: Thick * 0.03 mm 0.4 mm (12 mm*0.03 mm 0.3 mm) 12 mm - 0.6 mm3.2.2. Plywood panels must be cut at a right angle. Deviation must not exceed 2 mm per 1 lineal meter.3.2.3. Deviation from square edges can not exceed 2mm per 1 lineal meter.3.3. Making if plywood must include: Name of product Woos species of the face and core veneers Glue Bond marks Veneer grades for face and core Formaldehyde emission classification Type of surface treatment Dimensions Applicable GOST standardBelow is an example of markings in plywood. Birch plywood with core plies of birch veneer, water resistant, with acombination of face and core veneers I/III, with an emission class of E1, sanded in both sides, in 2440 mm long, 1220 mmwideand9mmthickismarked:Birch plywood/birch, FK, I/III, E1, S2, 2440*1220*9 GOST 3916.1-964.TECHNICAL REQUIREMENTS4.1. Characteristics4.1.1. To produce face veneers for plywood, the following species can be used for the face veneer: birch, alder, maple, elm,beech, asp, poplar, lime. For core veneers, in addition to the ones just mentioned, the following can be used: pine, spruce, fir,larch and esthespeciesoftheplywood.The plywood can be made of one or more than one species of wood, therefore it is either "homogeneous" or "combined".If the number of veneer plies is even, the direction of fibers (grain) of the two middle plies must be parallel.Veneers, located symmetrically within the thickness of plywood, must be the same species and thickness.The thickness of the veneer used for the faces must not exceed 3,5 mm. And for the thickness if core veneers must nit exceed 4mm.4.1.2. Wood and manufacturing defects exceeding limits stated in Table 3, are not allowed in face veneers.4.1.3. Wood and manufacturing defects, exceeding the limits stated in Table 3, are allowed in core veneers, as long as they donot influence its integrity and dimensions. The requirements for quality and dimensions are specified in this standard.4.1.4. The maximum amount of wood and manufacturing defects allowed in face veneers is indicated in Table 4.4.1.5. The combination of face veneer grades is indicated in GOST 30427.4.1.6. The face veneer of E grade can consist of 2 components with one splice joint in the middle of the panel. This appliesonly to widths up to 1525 mm.If the width is over 1525 mm, the face veneer if E grade can consist of 3 components of equal width. The face veneer of I andII grades can be made from an unlimited number of veneer components.For grades E, I, II veneer joints must be parallel to plywood edges. Veneers must be matched for color.4.1.7. Plugs must be even with the surface, firmly bonded, must match the color of the face of the panel. The grain must alsobe parallel to the direction of the wood fibers (grain) on face veneer. For grades I and II the plugs must match the color of thewood.Putty fills or reapirs must match the color of the wood of a given grade. In addition, they must provide easy gluing, retain itscolor during plywood treatment and not crack while bending.4.2. Strength and mechanical indices are stated in Table 5.4.3. Formaldehyde content in plywood, depending in emission class, must meet the limits stated in Table 6.4.4. The plywood is measured in either square meters or cubic meters. The volume of one panel is determined with a precisionof up to 0.00001 m3. The volume of a few panels is determined with the precision of up to 0.5 m3. The squareness of a panel ismeasured with the precision of up to 0.01 m2. The squareness of a few panels in measured with a precision of up to 0.5 m2.4.5. The marking is
Ashawa Bay Hardwood Floors 9483 Ashawa Road, PO Box 398 Cook, MN 55723 800-788-9689 Unfinished Engineered Flooring General Information Our Ashawa Bay Hardwood Floors unfinished engineered floors manufactured in Cook, Minnesota, at Hill Wood Products, Inc., are constructed using the following materials. Face wear layer: