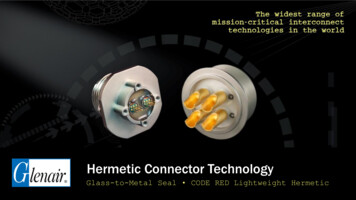
Transcription
Hermetic Connector TechnologyGlass-to-Metal Seal CODE RED Lightweight Hermetic
Hermeticity in Connectors Interconnection devices may be permanentlysealed by fusion or other means to prevent thetransmission of air, moisture and other gasesacross a bulkhead or other barrier Hermeticity is expressed as the rate of leakagevolume of helium per second in time. Mil/aerocaliber hermetics perform at 1X10-7 He/CC sec. Glass-to-metal, or CODE RED encapsulantsealing technology, is preferred for robust,durable hermetic seals between contacts, insertassemblies and connector bodies and shells.
The traditional “Gold Standard” ofHermetic Seals: Glass-to-MetalMatched SealCompression Seal
Advantages of Glass-to-Metal Sealed HermeticConnectors Compared to Legacy “Potted” Solutions High reliabilityPressure resistanceHigh operating temperatureMechanical strengthWithstands the heat of solderingEasy final assembly (i.e. welding orwire bonding) No material breakdown/aging over time
Hermetic Sealing Process: Sealing/Firing Components assembled (metalshell/contacts/glass) using carbon fixtureplates to hold them in position Assembly placed in a controlledtemperature furnace ( 1700 F) andsubjected to a gradually increasingtemperature. At the sealing temperature, the glassmelts and fills the space between the pinand the shell (chemical bond occurs) The assembly is then cooled.
Hermetic Sealing Process – Cleaning Sealed assemblies wired or rackedbased on their size and configuration. Processed for cleaning (oil removal) Descaling (multi-step process toremove oxidation) Brite-Dip process (passivation) Hydro Honed using a fine grit impactbead at low pressure, then rinsed anddried Final inspected and packed for return
Hermetic Sealing Process – Plating Typically gold plating is required Contacts cannot be plated in large batches(barrel or vibratory process) Each contact is individually wired twice, onceon each side Assembly is submersed into the platingsolution Wiring can produce an area that is discoloredwhere the wire was attached. “Wire marks”are common and are allowed for this type ofplating
Hermetic Sealing Process – Final Assembly Insulators Interfacial seals/gaskets Socket components(design dependent) Crimp removable inserts Connector hardware
Hermetic Sealing Process – Test Leak Testing 100% helium leak testing Electrical Typically IR/DWV 100% Pressure Testing In-house to 15,000 psi Several labs available for 15ksi
Hermetic Sealing Can Be Implementedfor Any Circular Connector Package Technology supports both pin and socket contact in any receptacle 15Series 80Mighty MouseThese are all standard catalog product offerings at Glenair
And For All Rectangular DesignsMIL-DTL-24308MIL-DTL-83513Again, standard catalog product offerings at Glenair
Design Features of StandardMIL-DTL-38999 HermeticsGlenair is QPL’d for both pin and socket contact typesSeries ISeries IIBayonetScoop-ProofBayonetLow-ProfileSeries IIITriple-Start Stub ACMESeries IVBreech Lock
Better than QPL glass-to-metal seal hermetic solutions,catalog hermetic specials, hybrid contact hermetics, and more233-100 IAWMIL-DTL-38999 Series IIIhermeticHermetic receptacleswith crimp contactsHermeticbulkhead feed-thrusHermetics withhigh-speed contacts
Special RF Pin-Contact Hermetics withHybrid Coax/Twinax/Signal Inserts1 x 10-7 cc/sec1 x 10-7 cc/sec9 # 16 Coax contacts and 48 #23 contacts19N17 arrangement with 2 #8 Twinax
Single-Way Hermetic Triax Connectors1 x 10-8 cc/sec, 2 milliohms
Special Hermetic Quadrax Connectors-50 C to 200 C, 1x10-7 cc/sec rated
Special Fiber Optic Hermetics1 x 10-8 cc/sec Fiber/signal combinations (no fiber-only arrangements)
Design Opportunities in Custom Glass-to-MetalSeal Hermetic Connectors Flange dimensions andmounting Length of bulkhead penetration Connector-to-panel sealing Unique contacts / insertarrangements Shell and contact materials Contact wire termination type PCB mounting design Other
The Lightweight Hermetic ChallengeFull hermetic sealing (10-7) in a lightweight connector shell package,with low contact resistance AND mission-critical durability Glass-to-metal seal furnacetemperatures are too high forlightweight aluminum and lowresistance copper contacts Conventional epoxy pottinglacks sealing strength andmission-critical durability
Introducing CODE REDWhen the mission demands hermeticity, and you can’tafford the weight and electrical resistance of steel or Kovar
Glass-Seal Hermetics Drawbacks vs.CODE RED BenefitsGlass-to-Metal SealHermetic Drawbacks Excessive weight High contactresistance Expensiveprocess with highfallout Long lead timesand expensivetooling Code RedBenefitsLight weightLow resistancecopper ContactsHigh yieldValue stream:process canmake 80 parts in3 days usingstandard tooling
Key to CODE RED PerformanceUnlike static epoxy potting, CODE RED sealing encapsulantis a dynamic adhesive material Expansion and contraction is matched tometal connector materials Virtually immune to thermal aging Order of magnitude stronger and moredurable than conventional hard epoxy potting
CODE RED Features and Benefits Hermetic Seal 1X10-7 Light weight, corrosionresistant materials Low-resistance copperalloy contacts Extreme temperaturetolerance Meets NASA outgassing Turnkey, drop-inreplacement for glass-sealhermetics Can be used in variousproduct families and shellgeometries
CODE RED Weight Savings:MIL-DTL-38999Shell Size ss Sealed28.435.248.256.281.491.495.8153.7*CODE REDWeight Weight 1.51Aluminum2.55-2.80Stainless Steel 7.70-7.73MaterialDensity(lb/in3)0.0550.0980.284% WeightReduction52%47%47%42%40%32%28%43%% Heavier than % Heavier thanCompositeAluminum44%81%65%
Current Carrying Capacity(single pin geometry @20ºC)160140100806040200201612CONTACT SIZEInconelKovarNickel IronBeCu8CURRENT (AMPS)120
Standard MaterialsComponentMaterialFinishDynamic GlenairEncapsulant SealingN.A.ContactsBeryllium copper alloy perASTM B197 or equivalent50 microinches gold per ASTMB488 Type 3, Code C, Class1.27 over 50-100 microinchesnickel plate per SAE-AMS-QQN-290 Class 2Retaining Ring300 Series Stainless SteelPassivated per AMS 2700,method 1, type 2, class 3Epiall 1908 or E484N.A.Wire Grommet andInterfacial SealsBlended fluorosilicone/siliconeelastomer 30% silicone per ZZR-765, 70% fluorosilicone perMIL-R-25988N.A.Shell and Jam NutAluminum alloy 6061-T6 perASTM B221Electroless nickel per ASTMB733CODE REDInsulator
CODE RED Testing and Validation DWV and IRContact retentionInsert retentionHermetic seal at 30 psiIR at temperatureDWV at altitudeRandom vibration attemperature*
CODE RED Testing and ValidationConnectors utilizing Code Redpotting have gone throughgrueling qualification testing tovalidate the technologyincluding: 100 cycles of thermal shock 1000 hours of thermal aging Extreme temperatureexposure to 200 C
CODE REDMaterial and process summary CODE RED is a proprietary encapsulant sealing and applicationprocess that delivers hermetic performance on par with glasssealed solutionsCODE RED is not old school epoxy potting. CODE RED Sealingsolves all the aging, embrittlement, temperature cycling andleak problems inherent to hard epoxy solutionsCODE RED Hermetics Dynamic hermetic encapsulant with a coefficient of expansion matchedto copper contact and aluminum shell materialsProprietary (internal) connector shell package architectureProven, quality-controlled application process performed in Glenair’sCODE RED Center of Excellence
Hermetic Connector TechnologyGlass-to-Metal Seal CODE RED Lightweight Hermetic
Better than QPL glass-to-metal seal hermetic solutions, catalog hermetic specials, hybrid contact hermetics, and more 233-100 IAW MIL-DTL-38999 Series III . Design Opportunities in Custom Glass-to-Metal Seal Hermetic Connectors Flange dimensions and mounting Length of bulkhead penetration