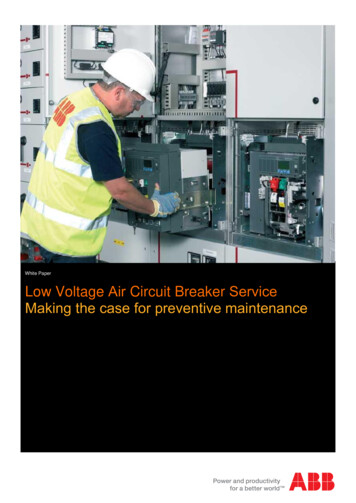
Transcription
White PaperLow Voltage Air Circuit Breaker ServiceMaking the case for preventive maintenance
Low voltage air circuit breaker serviceMaking the case for preventive maintenanceThe Case for MaintenanceEquipment intensive businesses understand that theuptime and reliability of their assets are vital tobusiness success. Owners and facility managementteams are increasingly concerned with their abilitiesto keep their equipment working at peakperformances. This leaves them with the task ofmanaging the myriad of maintenance challenges,which include extending equipment life cycles,maintaining and improving efficiencies, decreasingunscheduled downtime, planning for the unexpectedfailures – and all this while decreasing maintenancecosts.The National Fire Protection Association standards,NFPA 70B: Recommended Practice for ElectricalEquipment Maintenance, aptly states that ‘Electricalequipment deterioration is normal, but equipmentfailure is not inevitable. As soon as new equipmentis installed, a process of normal deteriorationbegins. Unchecked, the deterioration process cancause malfunction or an electrical failure.Aneffective Electrical Preventive Maintenance programidentifies and recognizes these factors and providesmeasures for coping with them.’ It goes on tohighlight that ‘without an Electrical PreventiveMaintenance program, the management assumes agreatly increased risk of a serious electrical failure.’It is essential to have a properly implementedpreventive maintenance program for electricalequipment.Maintenance for your Switchgear and BreakersElectrical switchgear are made up of ponents, which are often forgotten afterinstallation. Studies show that the rate of electricalcomponent failures is three times higher in facilitiesthat do not perform preventive maintenance (sourceIEEE).It has also been found that if a circuit breaker is nottested and maintained according to themanufacturer’s instructions, the failure rate could bevery high.An IEEE study shows that failureprobability could reach 50% in five years. Further inthe study, it was found that 73% of all circuit breakerfailures are disruptive to plant operations, andrequire the technical teams’ emergency, round-the-Page 2clock efforts to rectify. All of the above can begreatly reduced if preventive maintenance isperformed.The following are the most common causes ofswitchgear malfunction – Failure of components, including the circuitbreakers Loose connections Insulation deterioration Ingress of moisture, dust and other foreignobjects Accelerated deterioration from specialelectrical loading conditions and harshenvironmental conditionsThe circuit breaker is essentially a mechanicalsystem with numerous moving parts.Its lifeexpectancy is dependent on the wear and tear of allits components, including the frame, main contacts,jaw type contacts, auxiliary contacts, operatingmechanisms, electrical and mechanical accessories,trip unit, and lubricating products.The aforementioned causes can be detected andcorrected during maintenance actions. When leftuncorrected, the breaker can fail to open under faultconditions.Potential consequences of inactioninclude devastating equipment damages, fires,personnel safety hazards, and production downtimewhich could result in lost revenue and corporatereputation.Standards such as the NFPA, IEEE, NEMA, IEChave extensively documented requirements formaintenance of electrical equipment. These studiesaddress the frequencies of maintenance andtechnicians’ skill sets for maintenance actions.Comprehensive instructions on how maintenanceactions can be carried out can also be obtained fromequipment eMaintenance program will reduce accidents,improve personnel safety, and minimize costlybreakdowns and shutdowns of productionequipment. Impending troubles can be identified,and corrected before they become major problemsand require more expensive and time consumingsolutions. (NFPA 70B)
Maintenance StrategiesThe following diagram illustrates the maintenancestrategies commonly used for electrical equipment –those that are required. Monitoring systems detectabnormal conditions on measurable indicators suchastemperatureschangesandequipmentperformance efficiencies.Built-in diagnosticfeatures use algorithms to predict and communicatethe health status of each sensitive component,thereby allowing facility and maintenance personnelto make timely decisions on maintenance actionsand requirements.AdvantagesDisadvantagesCorrective Maintenance Low cost Less staff required formanagementCorrective Maintenance, also known as run-tofailure, assumes that all failures are age-related andinevitable. As the name suggests, no maintenanceactions are carried out on the equipment. Uponfailure, corrective actions such as repairs orreplacements are made. This maintenance strategyshould only be applied to equipment with negligiblefailure consequences.Preventive Maintenance is the systematicinspection, detection, correction, and prevention ofincipient failures, before they become actualfailures. This can be further divided into plannedand predictive maintenance. Objectives include thefollowing – Maintain original equipment functionalities Reduce unplanned downtime Optimize useful lifetime of equipment Decrease long-term maintenance costsScheduled Maintenance is the form of preventivemaintenance where the equipment is shut downregularly. This enables maintenance personnel totest and inspect the multiple components in thesystem, and carry out the necessary actions to keepthe system running with all the intendedfunctionalities and performance levels. Increased cost due tounplanned downtime ofequipment Increased labor cost,especially if overtime isneeded Cost involved with repair orreplacement of equipment Possible secondaryequipment or processdamage from equipmentfailure Inefficient use of staffresourcesPreventive Maintenance More labor intensive Cost effective in manycompared with Correctivecapital-intensive processesMaintenance Planned maintenanceinterval can take into account Includes performance ofunneeded maintenanceplant scheduleswhen compared with Increased component lifePredictive Maintenancecycle Reduced equipment orprocess failure Estimated 8% to 18% costsavings over correctivemaintenance programPredictive Maintenance Increased componentoperational life/availability Allows for preemptivecorrective actions Decrease in equipment andprocess downtime. Decrease in costs for partsand labor Improved worker andenvironmental safety Energy savings Estimated 8% to 12% costsavings over preventivemaintenance Increased investment indiagnostic equipment Increased investment in stafftraining Savings potential not readilyseen by managementPredictive Maintenance, another form of preventivemaintenance, is also known as condition-basedmaintenance.It is a systematic approach todetermine the need for actions to be taken beforefailure. This limits maintenance activities only toPage 3
CostsMaintenance costs, especially the indirect costs, arenot always evident or easily justified. IEEE STD 902states: ‘In planning an electrical preventivemaintenance program, consideration must be givento the costs of safety, the costs associated withdirect losses due to equipment damage, and theindirect costs associated with downtime or lost orinefficient production.’Due to the different natures of various maintenancestrategies, their overall costs also differ.Thefollowing diagram illustrates the total costs that areassociated with maintenance.* Indirect emergency costs have not been includedin this table** Ordinary maintenance refers to maintenancedone by non-ABB personnel, but in accordance withABB Installation and Maintenance ManualPage 4FrequenciesIn normal operational conditions, manufacturerstandards recommend minimum maintenanceactivities to be carried out on products at intervals ofa specified number of operations, or at least once ayear, whichever comes first. These frequencies canvary depending on the criticality of the application,the loading of the equipment, and the environment itis installed in. It is the responsibility of the user tocheck with the manufacturers for the appropriateintervals for their equipment, and thereafter planaccordingly.Where predictive maintenancestrategies are employed, maintenance intervals canalso be adjusted, depending on current breakerconditions.For circuit breakers, maintenance actions involvevisual inspection, general cleaning, lubrication of themechanical parts where required, checking forcontact wear and alignment, and inspection of arcchutes especially after opening in a fault condition.Maintenance frequencies depend largely on theenvironmental conditions of the surrounding area.Environments with dust, lint, moisture, or otherforeign matter indicate the need for higherfrequencies. Special note should also be taken forinstallations where vibrations are present. Criticalityof the application is also a major factor in decidingmaintenance intervals.In addition to these planned interventions, thefollowing are some situations where circuit breakersshould temporarily be taken out of service forfunctionality checks – Fault due to short circuit condition:Before resetting the breaker, it, along withthe circuit and equipment, should be testedand inspected, by a qualified person, toensure a short circuit condition does notexist in the system and that it is safe toreset the breaker. Resetting the breakerwhen the short circuit condition still exists isa critical situation that can cause burninjuries resulting from explosions ofelectrical equipment. After a high level fault has occurred inequipment that is properly rated andinstalled:It is not always clear what damage hasoccurred within the equipment. The circuitbreaker may appear virtually clean while itsinternal condition is unknown. Qualifiedpersonnel should be engaged to inspect the
systemandverifycircuitbreakerfunctionalities and integritiesWhen the circuit breaker has not beenoperated for extended periods of time:The circuit breaker should be manuallyopened and closed to check that themechanism works properlyUnknown failures or tripping of the system:Equipment must be checked for short circuitconditions. If the breaker cannot interrupt asecond fault, it will fail and may destroy itsenclosure and create a hazard for anyoneworking near the equipment.ConclusionIn order to protect equipment and people, properpreventive maintenance must be performed.Several standards and guides exist to assist userswith electrical equipment maintenance.Whenovercurrent protection devices are properly operatedand maintained, equipment damage, arc flashhazards and unplanned outages are greatlyreduced.Page 5
Maintenance for Low Voltage Air Circuit BreakersABB solutions, skills, advantagesChoosing ABB SolutionsInvesting in failure prevention, rather than living withits consequences, is a primary concern for manybusinesses. Successful prevention of failure canpositively influence a company’s long termcompetitiveness.Over the years, ABB Low Voltage Service hasdeveloped people and software to become a onestop solution for the maintenance of ABB electricalequipment. With this infrastructure in place, theteam partners with our customers to maximizeequipment performance throughout their life cycles.With ABB as a service provider, the customer canbe confident that its equipment is maintained byskilled and certified technicians who use genuine,quality parts.ABB declines all liability for damages to persons orproperty caused by failure to comply withmaintenance instructions detailed in the installationand service manuals.Preventive Maintenance ProgramPreventive Maintenance Program, or PMP, is asystematic and functional means of maintaining aspecific breaker. It is a scheduled maintenanceprogram developed by ABB. Based on studies andexisting statistics, it is designed to preserve thebreakers’ original integrities and functionalities sothat failure probabilities will be reduced. Steps takenat pre-determined times of the life cycle includepartial and complete overhauls of the ACB, cleaningand lubrication of moving parts, replacement of wornparts etc.The following figure illustrates such a typicalschedule –ABB Field Service EngineersABB has an extensive network of qualified fieldservice engineers. In accordance with local andinternational standards on skilled personnel, theseengineers have undergone intense, theoretical andhands-on training conducted by the ABB factory.The certification levels are administered through aformal system, which ensures that all the knowledgeand expertise of all certified engineers remaincurrent.Equipped with specific technical know-how andaccess to all the manufacturer’s resources on ourequipment, ABB engineers are qualified to handle awide range of issues that can arise.Apart from routine maintenance work, services bythe technical team also include customer eplacement of components, and otheradvanced engineering solutions.Companies who choose to have their services doneby the ABB team of engineers can be assured ofquality services that comply with manufacturers’requirements.Page 6The results of maintenance according to theschedule include extended circuit breaker life,increased plant reliability and personnel safety,increased production reliability, and relatively lowersmaintenance costs in the long run.All interventions are carried out by engineers andtechnicians certified by ABB.Please refer to www.abb.com or contact your localABB representative for more information.
Life Expectancy Analysis Program, also known asLEAP, is a proprietary diagnostic tool developed byABB. It periodically assesses the conditions ofbreakers on the plant. Using data pertaining tooperating conditions, the algorithms, which are builtinto LEAP, determines the he
NFPA 70B: Recommended Practice for Electrical Equipment Maintenance, aptly states that ‘Electrical equipment deterioration is normal, but equipment failure is not inevitable. As soon as new equipment is installed, a process of normal deterioration begins. Unchecked, the deterioration process can