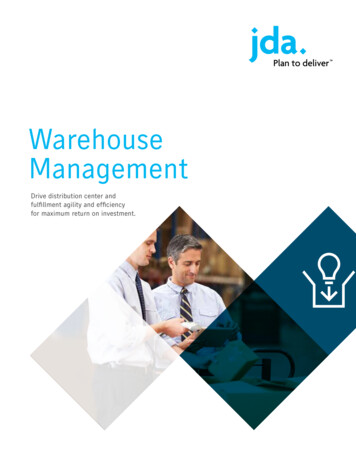
Transcription
WarehouseManagementDrive distribution center andfulfillment agility and efficiencyfor maximum return on investment.
Part of JDA’s Intelligent FulfillmentTM solution, JDA Warehouse Management isa comprehensive, real-time warehouse and distribution center managementsystem that skillfully handles real-world disruptions to help drive improvedperformance and competitive edge. JDA Warehouse Management helpsmanufacturers, retailers and distributors thrive in an ever-changing, hyperconnected omni-channel world by providing the power to quickly adapt tochanges, and optimize and execute the right inventory, at the right location, atthe right time. Users are empowered with more flexibility, real-timeresponsiveness and the ability to easily manage complex warehouse operations.Why does JDA WarehouseManagement enablecustomers to achieve thebest results?Industry LeadershipJDA has been enabling companies to optimize theirdistribution networks for more than 35 years. JDAprovides the most comprehensive task optimizationtechnology, including the industry’s only embedded3D mapping — out-of-the-box. Our vision andcapabilities integrate and synchronize operationsfrom the retail store shelf back through extendedsupply networks.JDA’s Warehouse Management technology andservices provide a comprehensive, RFID-enabledsolution for distribution and inventory managementcovering: Labor management Inbound operations Inventory management Work order processing Outbound operations Asset managementOptimizing Supply Chain ROIBy optimizing every move in the distribution center(DC), operations run more smoothly, accurately andefficiently. Nothing is left to chance or to the whimsof individual workers. Workflow and throughputoperate as a well-oiled machine. This maximizes thevalue of the DC and produces the greatest return onyour supply chain investment.The User Experience: RevisionedIn keeping with JDA’s customer-centered vision,the JDA Warehouse Management user experienceis an ongoing strategy for solving key industryproblems and interacting with technology in a newway, focused on user empowerment and efficiency.It provides a “control tower” for each role, allowingusers to handle the most pressing issues in real timewhile keeping an eye on their day-to-day business —resulting in maximum user productivity.Role-Based Mobility: Extending UserAdvantageThoughtfully created and prioritized based onextensive customer feedback, JDA WarehouseManagement extends the solution’s use throughmobile roles. Now users can flexibly respond tobusiness demands both in and outside the facilitywithout being locked down to a workstation or RFdevice.
The Flexibility to Bolster Omni-ChannelFulfillment Strategiesconsistency and control over what tasks are assignedand how they are carried out.As an integral part of our Intelligent Fulfillmentsolution, JDA Warehouse Management is focused onmeeting the demands of omni-channel fulfillment.The solution thoroughly handles fast-pacedprocessing of small, direct-to-consumer orders. Italso provides enhanced support for more flexiblestore distribution capabilities.JDA is a long-time leader in labor and workforcemanagement, transforming your workplace into aself-accountable, performance-focused culture. Thistransformation is accomplished through a proven,step-by-step methodology that incorporates culturealtering change management and strategic projectmanagement programs.Complex Operations Supported MoreEasily With Smart ConfigurationThe transformed business is enabled bytechnology for:Experience faster time to value with quickerimplementations, increased agility, simplifiedprocess changes and better onboarding. Userfriendly, prescriptive workflows allow users tomanage complexity without losing any richness,making them more self-sufficient. Your company’sspecific business needs are met without thecustomizations that make upgrades painful andcostly.Workforce Planning and SchedulingTo ensure just the right number of workers with theright skills are available exactly when needed tofulfill order demand.Labor ManagementLabor represents 50-75 percent of non-inventorycosts in most distribution centers, so optimizingeach and every task is critical to achieving agile,efficient and lean operations. This requiresSchedule OptimizationThe ability to quickly assign and reassign workersto priority work areas and functions based on orderflows, deadlines, skills and cost considerations.Task OptimizationMaking sure all tasks are assigned and executed inthe proper sequence while balancing workflows andorder priorities to maximize efficiency and quality ofservice.Learning ManagementA blended learning capability with classroomand online courses ensures that workers receiveproper training and certifications for their jobs. Jobperformance can be compared to training receivedto evaluate the effectiveness of training programs.JDA WAREHOUSE MANAGEMENT CUSTOMERSHAVE ACHIEVED SUBSTANTIAL ROI: Fulfillment cost reductions of 10-50% Inventory storage and handling cost reductions of10-35% Throughput increases of 10-40% Inventory visibility and accuracy near 100% Inventory reductions of 5-25% Credit reductions of 75-95% Dock-to-stock time reductions of 25-50% Receiving dwell-time reductions of 25-50%
Compliance and MeasurementMeasuring performance and ensuring compliancewith regulations and work rules is central toworkforce management. This includes trackingindirect time, attendance, quality and safety, as wellas calculating incentive rewards.Inbound Transportation Management — Real-timeoptimization of: Inbound shipment planning and scheduling Load consolidation and routing Carrier selection, tendering and management Round-trip coordination with outbound shipmentsVisibility and AnalyticsReal-time visibility into performance across theenterprise enables immediate reaction to events,analysis of trends, and the ability to quickly discoverthe root cause of problems.Only JDA has this broad spectrum of workforcemanagement capabilities and services to optimizeevery move within the DC and across the enterprise.Warehouse ManagementInbound OperationsEfficient inbound operations start with knowingwhat is being shipped from suppliers and whenit will arrive. JDA offers supplier collaborationtechnology to provide visibility into supplierproduction and shipments through a Web portaland EDI ASN information. Inbound shipments canalso be synchronized and controlled through JDAtransportation solutions.Optimized OperationsOnce you have visibility into inbound shipments,there are many tasks that should be optimized tostreamline inbound operations. JDA’s WarehouseManagement solution provides optimizationcapabilities.Appointment SchedulingIntegrates Web-based communications with agraphical dock calendar for: Inbound and outbound appointment scheduling Standing appointment management Exception management Vendor and carrier compliance ASN, PO and pack list management Receiving documentation, including global trademanagement
Yard and Dock ManagementCheck-in to check-out management of yardequipment, inventory movements, dock doors andpersonnel, including: Gate check-in and check-out Yard and dock location assignments Inventory and asset tracking System-directed movements via wireless devicesInbound ServicesSystem-directed work assignments for: Vendor/carrier compliance statistical sampling QA workflow controlDuty ManagementA complete solution for managing bondedwarehouses, including: Compliance with excise and customs legislationCross-DockingHot receipt functionality to prioritize inboundinventory with outbound orders, reducing handling,storage and costs while improving service. Detailed audit trails for customs controls and audit Real-time demand assessment and prioritization Evaluation and breakdown Put-to-store synchronization Disassembly/de-kitting Integration with dock scheduling Clean/rework/repackageReceiving and PutawayOptimized receipt and stowage, including:Reverse Logistics/Returns ProcessingSystem-directed work assignments for: Putaway or return to vendor Dispose or destroy Receipt check-in by paper, RF or RFID Detailed SKU attribute capture and verification Cart/container optimization System-directed putaway based on cube, weight,dimensions, nesting and stacking, commonality,location availability, zoning and product demand Operator-managed overrides and exceptions Optimized task interleavingRetail Store ProcessingInbound processing for retail distribution, including: Store distribution flow-through processing Put-to-store Merge-in-transit“In just five months, operator productivity has grown by 25 percentwhile increased employee motivation has reduced staff turnover.In addition, new starters are trained faster and with best-practiceoperating methods that enable them to be productive from day one.”Diane SmithSupply Chain ManagerThe Works
Inventory ManagementEffective inventory management requires visibilityand control from suppliers’ production all the waythrough to the end user. JDA provides this realtime visibility and control to optimize the tracking,movement, handling, storage, and if necessary,recall of all types of raw materials, work-in-processand finished goods inventory. Key functions include:Supplier CollaborationVisibility into supplier production, packaging,QA processing and shipments, with exceptionmanagement.SlottingImproves productivity by synchronizing productplacement to order demand. Key features include:Inventory ControlTracks inventory based on many SKU attributes,including: Lot number/expiration dates, with variable aging Catch-weights and volumes Nested serial numbers Country of origin Temperature-controlled requirements Nesting and stacking limitationsSpecial HandlingEnforces rules for handling, storage and trackingof SKUs that require environmental or HAZMATsegregation, procedures and certifications. Balances pick velocity with travel distances,ergonomics and equipment constraints for optimalworkload efficiency and safetyQA/RecallProvides ancestry and destination tracking by lot,SKU and item/serial number for inventory at rest or inmotion across the supply network. It enables: Compares the cost of re-slotting to the economicbenefits achieved to compute the true ROI of theslotting plan Lot and item-level visibility and control across thenetwork Integrates with replenishment activities todynamically re-slot, minimizing disruption and cost Redirect shipments and ASNs Real-time, multi-level QA holds Centralized recallReplenishmentSupports multiple strategies to tailor replenishmentto product, location, environment and slotting needs.Replenishment can be triggered by: Quantity or top-off On-demand/emergencyCycle CountingSystem-directed work provides 99 percentaccuracy, virtually eliminating the need for traditionalcycle counting. However, multiple cycle countingprocedures are supported, interleaved with dailyactivities. Slotting or other fulfillment plansEnterprise VisibilityReal-time visibility into inventory across theenterprise and extended supply networks throughdashboards with detailed drill-down analysiscapabilities and user-configurable reporting enablesimproved decision making, reduced inventory levelsand better support for demand-driven fulfillmentstrategies.
Work Order ProcessingA lot more goes on in distribution centers today thansimple pick, pack and ship. Through postponementstrategies, customer service requirements andstore-ready processing, DCs are becoming limitedproduction centers, requiring skills, equipment,work orders and management practices not seenin traditional warehouses. Work Order Processingin these DCs can be more akin to manufacturingprocesses than traditional distribution functions.JDA’s Work Order Processing solution assigns,sequences and directs tasks to ensure timely,consistent and accurate completion of work orderproduction. In many ways it can be thought of as amanufacturing execution system for the DC.Work Order Processing is highly configurable,providing the flexibility you need to tailor processingto your initial needs, as well as to ever-changingfuture requirements. System-directed work ensuresefficiency and throughput even within the chaos ofmultiple, changing customer requirements — puttingyou in control.WORK ORDER PROCESSING FUNCTIONALITYINCLUDES: Work order assignment, sequencing and execution Raw material control, including backflushing Multi-level bills of material Postponement strategies Value-added services Work cell planning and scheduling Light manufacturing/assembly Kitting/de-kitting Store-ready containers/pallets
Outbound OperationsFrom pre-pack to proof of delivery, JDA optimizesevery step of outbound operations to ensureaccuracy, timeliness, efficiency, compliance andoptimal customer service. The breadth of capabilitiesinclude:Task Management and InterleavingJDA’s unique 3D mapping of facilities enables themost efficient task assignments for all work, withintegrated voice or RF-directed interleaving oftasks. Tasks are assigned and interleaved basedon proximity, priority and permissions to maximizeefficiency and service while ensuring safetyand adherence to work rules and certificationrequirements.Multiple Pick MethodsA virtually unlimited number of pick methods can bedeployed simultaneously. Methods supported outof-the-box include multiple versions of: batch, wave,zone, and cluster picking supporting LIFO, FIFO,LEFO and FEFO inventory turn strategies.Retail In-Store and Dark-Store Picking andProcessing of E-Commerce OrdersIncludes in-store picking and dark-store capabilitiesfor effectively managing retail e-commercefulfillment operations, helping to enhance shoppers’omni-channel experience and facilitate the buyanywhere, fulfill anywhere and return anywheremodel that retail customers expect.Packing and ShippingSystem-directed packing, cartonization, QAverification, staging, and pack-and-hold managementenables accurate, timel
Warehouse Management Inbound Operations Efficient inbound operations start with knowing what is being shipped from suppliers and when it will arrive. JDA offers supplier collaboration production and shipments through a Web portal and EDI ASN information. Inbound shipments can also be synchronized and controlled through JDA transportation solutions. “In just five months, operator productivity .File Size: 487KBPage Count: 12