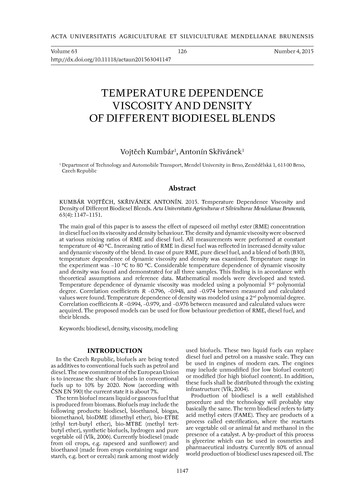
Transcription
ACTA UNIVERSITATIS AGRICULTURAE ET SILVICULTURAE MENDELIANAE BRUNENSISVolume 63126Number 4, EMPERATURE DEPENDENCEVISCOSITY AND DENSITYOF DIFFERENT BIODIESEL BLENDSVojtěch Kumbár1, Antonín Skřivánek11Department of Technology and Automobile Transport, Mendel University in Brno, Zemědělská 1, 613 00 Brno,Czech RepublicAbstractKUMBÁR VOJTĚCH, SKŘIVÁNEK ANTONÍN. 2015. Temperature Dependence Viscosity andDensity of Different Biodiesel Blends. Acta Universitatis Agriculturae et Silviculturae Mendelianae Brunensis,63(4): 1147–1151.The main goal of this paper is to assess the effect of rapeseed oil methyl ester (RME) concentrationin diesel fuel on its viscosity and density behaviour. The density and dynamic viscosity were observedat various mixing ratios of RME and diesel fuel. All measurements were performed at constanttemperature of 40 C. Increasing ratio of RME in diesel fuel was reflected in increased density valueand dynamic viscosity of the blend. In case of pure RME, pure diesel fuel, and a blend of both (B30),temperature dependence of dynamic viscosity and density was examined. Temperature range inthe experiment was 10 C to 80 C. Considerable temperature dependence of dynamic viscosityand density was found and demonstrated for all three samples. This finding is in accordance withtheoretical assumptions and reference data. Mathematical models were developed and tested.Temperature dependence of dynamic viscosity was modeled using a polynomial 3rd polynomialdegree. Correlation coefficients R 0.796, 0.948, and 0.974 between measured and calculatedvalues were found. Temperature dependence of density was modeled using a 2nd polynomial degree.Correlation coefficients R 0.994, 0.979, and 0.976 between measured and calculated values wereacquired. The proposed models can be used for flow behaviour prediction of RME, diesel fuel, andtheir blends.Keywords: biodiesel, density, viscosity, modelingINTRODUCTIONIn the Czech Republic, biofuels are being testedas additives to conventional fuels such as petrol anddiesel. The new commitment of the European Unionis to increase the share of biofuels in conventionalfuels up to 10% by 2020. Now (according withČSN EN 590) the current state it is about 7%.The term biofuel means liquid or gaseous fuel thatis produced from biomass. Biofuels may include thefollowing products: biodiesel, bioethanol, biogas,biomethanol, bioDME (dimethyl ether), bio-ETBE(ethyl tert-butyl ether), bio-MTBE (methyl tertbutyl ether), synthetic biofuels, hydrogen and purevegetable oil (Vlk, 2006). Currently biodiesel (madefrom oil crops, e.g. rapeseed and sunflower) andbioethanol (made from crops containing sugar andstarch, e.g. beet or cereals) rank among most widelyused biofuels. These two liquid fuels can replacediesel fuel and petrol on a massive scale. They canbe used in engines of modern cars. The enginesmay include unmodified (for low biofuel content)or modified (for high biofuel content). In addition,these fuels shall be distributed through the existinginfrastructure (Vlk, 2004).Production of biodiesel is a well establishedprocedure and the technology will probably staybasically the same. The term biodiesel refers to fattyacid methyl esters (FAME). They are products of aprocess called esterification, where the reactantsare vegetable oil or animal fat and methanol in thepresence of a catalyst. A by-product of this processis glycerine which can be used in cosmetics andpharmaceutical industry. Currently 80% of annualworld production of biodiesel uses rapeseed oil. The1147
1148Vojtěch Kumbár, Antonín Skřiváneksame ratio applies to the Czech Republic, as well. Inthis case, we refer to the biofuel as rapeseed methylester (Králová, 2007).From theoretical point of view, pure RME canbe used in diesel engines directly without anychemical modifications. However, the drawbacksof this approach are its worse properties comparedto diesel including viscosity, density, stability, andcetane number. As a result, it is more commonlyused in a blend with conventional diesel fuel.This article addresses issues connected with theviscosity/density of RME, diesel fuel, and blends.MATERIALS AND METHODSRME, diesel fuel, and 8 of their mutual blendswith different mixing ratios have been chosen forthe experiment. Samples with volume of 1000 mlwere used. Detailed description is given in Tab. Ibelow.I: Blends of RME and diesel used in the experimentDiesel %Viscosity measurements were performed usingthe Anton Paar DV-3P rotational viscometer. Thisdevice measures torque force required to overcomeresistance of rotating cylinder or disk immersed inthe measured material sample. The rotating cylinderor spindle is connected via spring to motor sharotating at defined speed. Rotation of the sha ismeasured electronically and provides accurateinformation about the position of the sha , hencethe spindle (see Fig. 1). The dynamic viscosityvalue in [mPa·s] is then acquired using internalcalculation algorithm. For constant viscosity liquids,the resistance against motion increases with the sizeof spindle. Measurement range for determination ofmaterial rheological properties can be adjusted byselecting the appropriate combination of spindleand rotation speed. To obtain relevant results, it isnecessary to know essential rheological propertiesof given sample. Obviously, it is necessary tocorrectly classify the material prior any testing takesplace (Kumbár and Sabaliauskas, 2013).Standard spindle labeled LCT was used in theexperiment. The spindle is most appropriate for1: Schematic of device geometryliquids featuring very low viscosity. On the rotationalviscometer the number of spindle revolutions wasset to 100 per minute and the sampling frequencywas set to 1 Hz.The temperature dependence of viscosity wasmeasured using the following procedure: 200 ml ofthe measured sample cooled to 10 C was placedinto a beaker. This beaker with the sample wasthen placed into working vessel of the rotationalviscometer. Then, the measuring spindle (LCT)and a calibrated temperature sensor Pt 100 wereimmersed as well. A er that the actual dynamicviscosity measurement began. The sample wasfurther heated up to 80 C. Presented procedureis in accordance with the references (Kumbár andPolcar, 2012; Kumbár and Dostál, 2014).Using a simple conversion, we can calculate thekinematic viscosity from the dynamic viscositymeasured. The kinematic viscosity is the ratio ofdynamic viscosity and density of measured sample: [mm2·s 1; mPa·s, g·cm 3], (1)where .kinematic viscosity, .dynamic viscosity, and .density.Density measurements were performed usingMohr scales. Sample temperature was 40 C. Thisvalue represents a comparative temperature fordistilled liquids according to the ISO 8217 standard.A mathematical model was created using theStatistica 10 so ware. Accuracy (suitability) offitted functions was determined by the correlationcoefficient R; the degree of significance (p 0.05).RESULTS AND DISCUSSIONExamination of RME concentration in dieselfuel revealed that with increasing concentration,the density of blend increase dependence is almost
1149Temperature Dependence Viscosity and Density of Different Biodiesel Blendslinear. This result was expected in accordancewith the references (Alptekin and Canakci, 2008;Ramírez-Verduzco et al., 2011). Then, a mathematicalmodel was constructed. In the model, the followinglinear regression formula was used (Kumbár andVotava, 2014):y a1 · x a0.(2)A er substitution, the formula reads as follows: 0.0005 · c 0.7855 [g·cm 3],The influence of the RME concentration indiesel fuel with respect to dynamic viscosity wasmonitored. Once again it was proven that withincreasing RME concentration, the dynamicviscosity dependence is nearly linear, as statedin (Borges et al., 2011) and (Joshi and Pegg, 2007).The general formula has been used (2). A ersubstitution, the relationship is as follows: 0.005 ·c 1.3659 [mPa·s],(3)where .density andc .volume concentration.Very high correlation coefficient R 0.999 wasacquired. For pure diesel fuel, the density was0.785 g·cm 3 and for pure RME (B100), it was0.835 g·cm 3. Density values of blend samples arelisted in Tab. II below.(4)where .dynamic viscosity andc .volume concentration.The correlation coefficient value in this group wasas high as R 0.996. For pure diesel fuel, the dynamicviscosity was 1.352 mPa·s. For pure RME (B100), thevalue was 1.881 mPa·s. Dynamic viscosity values ofblend samples are listed in Tab. II below.II: Density and viscosity values of various blends of diesel fuel and RMENo.Diesel FuelRMETemperatureDensityDynamic ViscositymPa·sml%ml% 1.8812: Effect of RME concentration in diesel fuel on its flow behaviour 3
1150Vojtěch Kumbár, Antonín SkřivánekValues of density and dynamic viscosity providedsource data for charts shown in Fig. 2. Individualvalues of the equation coefficients are included inthe corresponding figures.For three samples (pure diesel fuel, pure RMEB100 and B30 blend) temperature dependence ofdynamic viscosity and density was monitored. Asexpected and in accordance with the references(Maggi, 2006; Knothe and Steidley, 2007; Yuanet al., 2009), higher temperature was connectedto decrease of dynamic viscosity and density ofsamples, see Fig. 3 and Fig. 4. For the individualcharts, mathematical models were constructedusing 3rd polynomial degree (5) for the temperaturedependence of dynamic viscosity and using2nd polynomial degree (6) for the temperaturedependence of the density. The general relationshipswere as follows:y a3 · x3 a2 · x2 a1 · x a0andy a2 · x2 a1 · x a0.3: Dependence of temperature and dynamic viscosity4: Dependence of temperature and density(5)(6)
Temperature Dependence Viscosity and Density of Different Biodiesel BlendsIndividual values of the equation coefficients areincluded in the corresponding figures.The R correlation coefficient showed high valuesin range from 0.796 to 0.974 (for 3rd polynomial1151degree) and in range from 0.976 to 0.994 (for 2ndpolynomial degree).CONCLUSIONRapeseed oil methyl ester (RME) concentration in diesel fuel may affect its flow behaviour, i.e.dynamical viscosity and density. Several different blends of RME and diesel fuel were used for theexperiment. All the samples were heated to comparative temperature of 40 C (according to theISO 8217 Standard). With increasing ratio of RME in diesel fuel, the density and dynamic viscosity ofblends increased. The increase in density and dynamic viscosity were mathematically modeled usinga linear function. The R correlation coefficient reached very high values of 0.999 (for density) and0.996 (for dynamic viscosity).For pure RME (B100), pure diesel fuel, and diesel fuel blend (B30), dependence of temperature anddynamic viscosity/density was monitored in range from 10 C to 80 C. Resulting dependenceof temperature and dynamic viscosity/density was confirmed based on the assumptions andreferences. For these measurements, mathematical models were constructed using functions withthe lowest number of degrees of freedom. Dependence of temperature and dynamic viscosity wasmodeled using 3rd polynomial degree. Dependence of temperature and density was modeled using2nd polynomial degree. The R correlation coefficient reached very high values of 0.796, 0.948, 0.974(for 3rd polynomial degree) and values of 0.994, 0.979, 0.976 (for 2nd polynomial degree).Presented mathematical models can be used to predict the flow behaviour (density, dynamic viscosity,temperature/viscosity/density dependences) of RME, diesel fuel, and their blends.AcknowledgementThe research has been supported by the project No. TP 4/2014, financed by Internal Grant Agencyof Mendel University in Brno, Faculty of Agronomy.REFERENCESALPTEKIN, E., CANAKCI, M. 2008. Determinationof the Density and the Viscosities of BiodieselDiesel Fuel Blends. Renewable energy, 33: 2623–2630.BORGES, M. E., DÍAZ, L., GAVÍN, J., BRITO, A.2011. Estimation of the Content of Fatty AcidMethyl Esters (FAME) in Biodiesel Simplex fromDynamic Viscosity Measurements. Fuel ProcessingTechnology, 92: 597–599.CZSO. 1993. Automotive fuels. – Diesel. – Requirementsand test methods. ČSN EN 590.JOSHI, R. M., PEGG, M. J. 2007. Flow Properties ofBiodiesel Fuel Blends at Low Temperatures. Fuel,86: 143–251.KNOTHE, G., STEIDLEY, K. R. 2007. KinematicViscosity of Biodiesel Components (Fatty AcidAlkyl Esters) and Related Compounds at LowTemperatures. Fuel, 86: 2560–2567.KRÁLOVÁ, T. 2007. Bio bio biodiesel. Euro, 49: 58–59.KUMBÁR, V., POLCAR, A. 2012. Flow behaviourof petrol, bio-ethanol and their blends. ActaUniversitatis Agriculturae et Silviculturae MendelianaeBrunensis, LX(6): 211–216.KUMBÁR, V., SABALIAUSKAS, A. 2013. Lowtemperature behaviour of the engine oil. ActaUniversitatis Agriculturae et Silviculturae MendelianaeBrunensis, LXI(6): 1763–1767.KUMBÁR, V., DOSTÁL, P. 2014. Temperaturedependence density and kinematic viscosityof petrol, bioethanol and their blends. PakistanJournal of Agricultural Sciences, 51(1): 175–179.KUMBÁR, V., VOTAVA, J. 2014. Differences inengine oil degradation in spark-ignition andcompression-ignitionengine.Eksploatacjai Niezawodnosc – Maintenance and Reliability, 16(4):622–628.MAGGI, C. P. 2006. Advantages of KinematicViscosity Measurement in Used Oil Analysis.Practicing Oil Analysis Magazine, 5: 38–52.RAMÍREZ-VERDUZCO, L. F. et al. 2011. Predictionof the Density and Viscosity in Biodiesel Blends atVarious Temperatures. Fuel, 90: 1751–1761.VLK, F. 2004. Alternative au
kinematic viscosity from the dynamic viscosity measured. The kinematic viscosity is the ratio of dynamic viscosity and density of measured sample: [mm2·s 1; mPa·s, g·cm 3], (1) where .kinematic viscosity, .dynamic viscosity, and .density. Density measurements were performed using Mohr scales. Sample temperature was 40 C. This