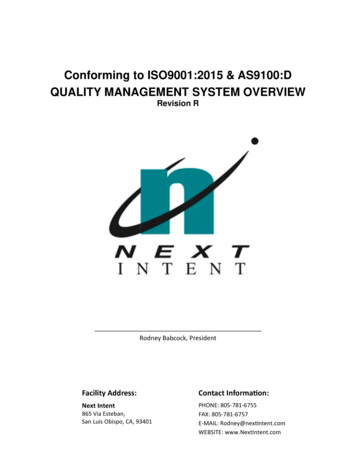
Transcription
Conforming to ISO9001:2015 & AS9100:DQUALITY MANAGEMENT SYSTEM OVERVIEWRevision RRodney Babcock, PresidentFacility Address:Contact InformaƟon:Next IntentPHONE: 805-781-6755FAX: 805-781-6757E-MAIL: Rodney@nex ntent.comWEBSITE: www.NextIntent.com865 Via Esteban,San Luis Obispo, CA, 93401
Document Title:Quality Management System OverviewRevision: RDocument Number:See last page for historyQMS OverviewProcess Owner(s): QA Manager, PresidentPage 1 of 16ApprovalRevision Date:1/17/2020StampTable of Contents:IntroducƟon 1.1 & 1.23Next Intent QMS Structure 1.13Non-Applicable Provisions 1.33NormaƟve References 24DefiniƟons 34Company Overview & Context 4.14Scope 4.35The QMS and its Processes 4.45Leadership & Commitment 5.15Quality Policy 5.25Roles Responsibility & Authority 5.35Risks & OpportuniƟes 6.15Quality ObjecƟves 6.25Planning of Changes 6.35Resources 7.16Monitoring & Measuring Resources 7.1.56OrganizaƟonal Knowledge 7.1.66Competence 7.26Awareness 7.36CommunicaƟon 7.46Documented InformaƟon 7.56OperaƟonal Planning & Control 8.17OperaƟonal Risk Management 8.1.17ConfiguraƟon Management 8.1.27Product Safety 8.1.37PrevenƟon of Counterfeit Parts 8.1.47Requirements for Products and Services 8.28Control of Externally Provided Products & Services – General 8.4.18
Document Title:Quality Management System OverviewRevision: RDocument Number:See last page for historyQMS OverviewProcess Owner(s): QA Manager, PresidentPage 2 of 16ApprovalRevision Date:1/17/2020StampControl of Externally Provided Products & Services – Type & Extent 8.4.29InformaƟon for External Providers 8.4.39Control of ProducƟon & Service Provision 8.5.19IdenƟficaƟon & Traceability 8.4.110Customer’s or Supplier’s Property 8.5.310PreservaƟon 8.5.410Release of Product 8.610Control of Non-Conforming Output 8.711Monitoring, Measurement, Analysis and EvaluaƟon11Internal Audit 9.211Management Review 9.311Improvement 10.011OrganizaƟonal Chart 5.312Roles & ResponsibiliƟes 5.313Process InteracƟons15Revision Control16Referenced Documents16
Document Title:Quality Management System OverviewRevision: RDocument Number:See last page for historyQMS OverviewProcess Owner(s): QA Manager, PresidentRevision Date:1/17/2020Page 3 of 16ApprovalStampIntroducƟon 1.1 & 1.2:Structure 1.1:Next Intent has developed a quality managementsystem (QMS) designed to comply with therequirements of AS9100:D/ISO9001 and to documentour best business prac ces, be er sa sfy therequirements and expecta ons of our customers andimprove the overall management of the company. TheQuality Manual includes this overview, StandardOpera ng Procedures (SOPs), Work Instruc ons (WIs)and forms (QAFs) for recording documented informa on(records). This overview describes the QMS, delegatesauthori es, iden fies interdepartmental rela onships,and responsibili es of the personnel responsible forperforming within the system. The overview alsoprovides the necessary references for most ac vi esused within the QMS to ensure compliance to thenecessary requirements of the standard. Together theydocument the QMS and are to be used to instruct and toguide employees and management of Next Intent whoseac ons affect product quality.Next Intent uses a mul - er document structure tocommunicate its process requirements. The structure ispyramidal with this Quality Management System Overviewat the apex and becoming more process specific towardthe base.The QMS Overview provides a descrip on of the companyand the quality management system. The StandardOpera ng Procedures (SOPs) provide high-level guidanceand support. Work instruc ons are task specific. Formsare developed in order to standardize the informa on thatis gathered and recorded as documented informa on.This Quality Manual shall also inform Next Intent’scustomers what controls have been implemented toassure product quality. Each sec on includes a generaland brief procedure outlining the QMS processes andreferences the SOPs, where applicable, that providemore detailed descrip ons.The QMS employs a process approach, which providesfor the management and con nuous improvement ofthe quality system and its processes through theapplica on of Plan-Do-Check-Act (PDCA) methodologyand a focus on risk-based-thinking with the objec ve ofpreven ng undesirable outcomes before they occur,analyzing nonconformi es that do occur, and takingac on to prevent recurrence.Non-Applicable Provisions 1.3:This QMS is complementary, and not an alterna ve, tocontractual, statutory and regulatory requirements.JusƟficaƟon:Next Intent’s management team has demonstrated itscommitment through the development of this QMS andthe promo on of its effec veness and improvement, theestablishment of a quality policy and communica ng theimportance of effec ve quality management. Our focusis upon our customers and our goal is completesa sfac on through error free work and on- medelivery.8.3 Design and Development8.5.5 Post Delivery Ac vi es8.5.1.2 Valida on and Control of Special Processes8.3 - Next Intent does not offer or perform any design ordevelopment ac vi es, we work from customer printsand purchase order requirements.8.5.5 - Next Intent does not engage in post-deliveryac vity except warranty rework/repair for nonconforming product.8.5.1.2 – Next Intent performs no special processes asdefined by the standard. All features can be directlymeasured.
Document Title:Quality Management System OverviewRevision: RDocument Number:See last page for historyQMS OverviewProcess Owner(s): QA Manager, PresidentPage 4 of 16ApprovalRevision Date:1/17/2020StampNormaƟve References 2:DefiniƟons 3:The following documents are norma vely referenced inthis QMS Manual:Terminology and defini ons specific to a process that arenot broadly understood in the manufacturing industry aredefined in the defini on sec on of any procedures or workinstruc ons that are used in the control of that process.Terminology used by the Standard, that is not part of thecommon parlance, will be clarified in context as needed. ISO 9000:2015 QMS Fundamentals & Vocabulary ISO 9001:2015 QMS Requirements AS9100:D Aerospace QMS RequirementsCompany Overview & Context 4.1:Next Intent is a contract manufacturer of precision machined components and assemblies for na onal laboratories, theaerospace, and the defense industries, with over 20 years of experience. Using advanced turning, milling, wire EDMtechnology, and skilled and experienced machinists and operators, Next Intent o en takes on manufacturing challengesthat others will not.Next Intent has determined external and internal issues that are relevant to its purpose and strategic direc on, and thataffect its ability to achieve the intended results of its quality management system. These issues may be legal, technical ormarket related, foreign or domes c. Informa on regarding these issues is monitored and reviewed regularly by NextIntent’s management which considers issues related to values, culture, knowledge, and performance, and how theyrelate to Next Intent.Interested ParƟes 4.2:Relevant interested par es are those that provide significant risk to organiza onal sustainability if their needs andexpecta ons are not met. Next Intent has determined how interested par es are relevant to the organiza on and hasdefined them and their rela onship in the chart below. We monitor and review informa on pertaining to them by usingthe established key performance indicators (KPI’s) and discussing them in the Management Review Mee ngs.Regulatory AgenciesCustomers(OSHA, DOL, EPA, DOS, Rule 41 etc.)Informed through regula ons, courtrulings, legisla on etc. Measured bynonconformi es and infrac onsMeasured by OTD, quality (NCRs), andsurveys.Governing Bodies(FAA, NASA, DOD etc.)Informed by design requirements,quality and workmanship standardsSuppliersEmployeesPeriodic evalua on based on OTD,quality (NCRs/DMRs) and surveyresponsesInformed through evalua ons andreten onCommunityStakeholders(Ac vist organiza ons)An -government & an -militaryprotests and communica ons(Owners and investors)P&L, Cash Flow, ROIFinancial InsƟtuƟons(when applicable)Profit & Loss and Cash Flow
Document Title:Quality Management System OverviewRevision: RDocument Number:See last page for historyQMS OverviewProcess Owner(s): QA Manager, PresidentPage 5 of 16ApprovalRevision Date:1/17/2020StampScope 4.3:Risks and OpportuniƟes 6.1:Next Intent has determined the boundaries and applicability of the QMS basedupon the requirements of interested par es, internal and external issues, itsproduct, services and business model, and will apply the requirements ofAS9100 as applicable.This QMS applies to all produc on facili es used by Next Intent for machiningand assembly. Non-applicable provisions have been iden fied andenumerated elsewhere in this overview.Managing risks and opportuni esconsists of minimizing the likelihoodof undesired outcomes andenhancing the opportuni es fordesirable effects.Ac ons taken to address risks andopportuni es shall be propor onateto the poten al impact. Risks maybe avoided, mi gated, transferredor accepted. Opportuni es may beexploited, enhanced, shared oraccepted. Risks, opportuni es andstrategies are evaluated for eachprocedure.Risks are managed according to SOP8.1.1-01 Opera onal RiskManagement any me ac on istaken within, or changes made to,the QMS.The QMS and its Processes 4.4:Next Intent has established and con nually improves its QMS, including theprocesses needed and their interac ons, in accordance with the AS 9100Rev. D standard.Leadership and Commitment 5.1:Top Management has developed this manual including, conducts staffmee ngs, Management Review mee ngs, adopted risk-based thinking andassured that relevant informa on is communicated to personnel.Furthermore, Top Management has demonstrated their commitment throughthe development of the Quality Manual and the Quality Policy and Objec vesdocumented in this manual.Management ensures that customer requirements are completely understoodand met. Ensuring customer sa sfac on is achieved through iden fying andmanaging the risks and opportuni es that can affect the conformity of theproducts and services that we provide. Next Intent communicates with thecustomer and takes appropriate ac on when product conformity or on- medelivery are not met.Next Intent’s management demonstrates and maintains its focus on customersa sfac on by determining and understanding customer and statutoryrequirements and by monitoring product conformity and on- me deliveryperformance and taking appropriate ac on if planned results are not met.Risks and opportuni es that can affect product conformity and delivery aredetermined and addressed.Quality Policy 5.2:Next Intent is commi ed to furnishing products and services that meetor exceed all of our customer’s needs and expecta ons.Roles, Responsibility & Authority 5.3:Next Intent’s management has assigned responsibili es for relevant roleswithin the company. An organiza onal chart and descrip on of du es isincluded at the end of this overview. Please refer to pages 12 through 14.Quality ObjecƟves 6.2:Sales Quote vs. Order Ra oProducƟon (Repeat Parts) 95% On Time Delivery 95% QualitySupplier Performance 95% Supplier OTD 95% Supplier QualityPlanning of Changes 6.3:Changes that could affect the QMSare reviewed and planned for inadvance and carried out in acontrolled manner to protect theintegrity of the QMS. These changeswill be considered during theManagement Review process wherethey will be evaluated for theirpoten al consequences, thealloca on of resources and changesin responsibili es and authority.
Document Title:Quality Management System OverviewRevision: RDocument Number:See last page for historyQMS OverviewProcess Owner(s): QA Manager, PresidentRevision Date:1/17/2020Page 6 of 16ApprovalStampResources 7.1:Monitoring & Measuring Resources 7.1.5:Next Intent’s Management has commi edto providing the necessary resources tomaintain and improve the QMS, and thecompany as a whole.Resources are provided for the preventa veand rou ne maintenance of infrastructure toprovide a safe and reasonably comfortableworkplace where the requirements of ourcustomer’s products can be met and verifiedand where raw materials, components, andfinished product are properly preserved.Qualified individuals are employed, andtrained, as necessary, to improve theirability to implement the QMS and operateand control its processes.Next Intent manages the social andpsychological aspects of the company incompliance with all applicable laws and doesnot u lize the QMS to do so. Physicalaspects of the work environment are,however, managed by the QMS inaccordance with SOP-7.1-01 Infrastructure &Environment.Necessary measurement resources are provided, and controlled andcalibrated in accordance with SOP-7.1.5-01 Monitoring & MeasuringResources – Calibra on, with traceability to NIST.OrganizaƟonal Knowledge 7.1.6:Relevant knowledge gained is documented in the form of process andpart specific work instruc ons, setup sheets and CNC programs, as isappropriate. See SOP-8.5.1-03 Produc on Informa on Filing.Knowledge gained for the administra on and improvement of theQMS will be captured during Management Review and incorporatedinto the QMS manual.Next Intent is made up of long-standing and experienced operatorsand training is provided on new or revised procedures to ensureaffected par es are constantly aware of changes.Competence 7.2:All Next Intent employees begin with certain competencies andknowledge. We endeavor to improve and increase thosecompetencies through ongoing training, as outlined in SOP-7.2-01Competence & Awareness. This results in personal growth, higherquality product and a safer work environment.Awareness 7.3:CommunicaƟon 7.4:As outlined in SOP-7.2-01 Competence & Awareness, all employees aremade aware of the quality policy, their contribu on to theeffec veness of the QMS, and the implica ons of not conforming withits requirements, during their new employee orienta on. Thisawareness is reinforced periodically during company mee ngs andother discussions.The QMS is available to all employees and they are made aware oftheir role in its con nual improvement. Quality Policy awareness isachieved through the use of posters, banners and swag.Awareness of Next Intent’s ethics policy is accomplished with QAF-117,which communicates the policy and provides for acknowledgement bythe employee. The form will be retained as documented informa on.Next Intent’s management ensures internalcommunica on occurs regarding theeffec veness of the QMS. This isaccomplished through company mee ngs,correc ve ac ons, internal audits, and othermethods including emails and personalconversa ons. Communica on includesinternal and external feedback.Next Intent communicates with regulatoryauthori es when required, and regularlywith its customers with regard toinforma on pertaining to their orders.Documented InformaƟon 7.5:Documented informa on (records) is(are) retained, controlled and preserved in accordance with SOP-7.5-01Documented Informa on and with SOP-7.5-02 Security & Protec on of Documents. Documents associated with theQMS are readily accessible on the company network for use by all employees.
Document Title:Quality Management System OverviewRevision: RDocument Number:See last page for historyQMS OverviewProcess Owner(s): QA Manager, PresidentRevision Date:1/17/2020Page 7 of 16ApprovalStampOperaƟonal Planning and Control 8.1:Opera onal Planning and Control is completed by determining the customer’s requirements during the quo ng andcontract review phases. SOP-8.1-01 Contract ReviewOpera ons, Manufacturing Engineering, Programming, and Manufacturing develop a manufacturing plan that isdocumented in the manufacturing traveler and set-up sheets, including necessary resources and those processes that areto be obtained from external providers (suppliers, vendors or subcontractors). The quality assurance plan is documentedin QAF-011 Produc on Control Sheet (PCS) for the job. Next Intent’s configura on management consists of the travelerand the customer’s design documents.Documented informa on (records) verifying the comple on of the planned processes and demonstra ng conformity tothe customer’s specifica ons shall be retained per SOP-7.5-01 Documented Informa on.The procedure for the control and preven on of foreign object debris/damage (FOD) is documented under SOP-8.5.1-04FOD Preven on, Detec on & Removal.Work transfers are controlled through proper iden fica on of conformity requirements, flowing down all customerrequirements, proper control of suppliers, and inspec on of received work. Normal work transfers to external providersare controlled per SOP-8.4.1-01 Control of Suppliers & Sub-Contractors and SOP-8.1.4-01 Preven on of Counterfeit Parts.Work transfer in the event of a disaster or emergency is controlled per SOP-8.1-02 Transfer of Work - Disaster Recovery& Business Con nuity Plan.The safety and fitness-for-use of the finished product is addressed through strict adherence to customer requirements.The product safety of the design(s) is(are) solely the responsibility of the customer. Safety in the produc on of ourcustomer’s products is addressed in SOP-8.1.3-01 Product and Produc on Safety and during New Employee Training.OperaƟonal Risk Management 8.1.1:PrevenƟon of Counterfeit Parts 8.1.4:Next Intent endeavors to manage its exposure to risk. Theprocedure for the considera on of risks is described in SOP-8.1.101 Opera onal Risk Management.Counterfeit product is any product thatmisrepresents its material, performance orcharacteris cs. Counterfeit parts include, butare not limited to: Used, refurbished, or reclaimed partsrepresented as new product. Parts manufactured from subs tutematerials/alloys. Material misrepresented as authen cproprietary material. Parts with a different surface pla ng/finishthan the required or order product. Parts that have not been fully tested by theoriginal component manufacturer (OCM),that are represented as completed product.Note: Refinished, up-screened, or updated partsidenƟfied accordingly are not consideredcounterfeit product.Next Intent strives to avoid counterfeit parts andmaterials through the procedures outlined inSOP-8.1.4-01 Preven on of Counterfeit Parts.ConfiguraƟon Management 8.1.2:Next Intent uses the produc on traveler, coordinate measuringmachine (CMM) reports, PCSs, and process cer fica ons todocument the configura on (revision) of the products produced. Ifa revision to a product is received from the customer while a job isin process, Opera ons and/or Manufacturing Engineering shallreview the changes rela ve to whether they may be incorporatedinto the product in process before upda ng the traveler, prints,and inspec on documents. Conformance to standards shall bedocumented on the traveler, PCSs, and CMM reports.Product Safety 8.1.3:The fitness for use and safety of the designs of the productproduced by Next Intent to our customer’s designs, is wholly theresponsibility of our customers. Next Intent’s responsibili es forproduct and produc on safety are outlined in SOP-8.1.3-01Product and Produc on Safety.
Document Title:Quality Management System OverviewRevision: RDocument Number:See last page for historyQMS OverviewProcess Owner(s): QA Manager, PresidentRevision Date:1/17/2020Page 8 of 16ApprovalStampRequirements for Products and Services 8.2:Communica ons with our customers is essen al to their sa sfac on. This communica on shall include: The requirements and expecta ons of the customer The services that Next Intent will and will not be providing Changes to orders Job status updates Controlling customer owned property Repor ng non-conformi es and reques ng devia ons Handling customer feedback including complaints Establishing specific requirements for con ngency plansThe requirements for products and services delivered by Next Intent to its customers shall be determined throughcommunica on with the customer during the sales and quo ng process and confirmed during contract review.During contract review, Next Intent ensures that the requirements and expecta ons are fully understood, that they arein agreement with what was communicated during quo ng, and that they can be met with the tools and technologycurrently available at Next Intent, its partners and suppliers. Opera onal risks are iden fied and considered at this mein accordance with SOP-8.1.1-01 Opera onal Risk Management.Before commi ng to supply products or services to our customers, Next Intent performs a contract review perSOP-8.1-01 Contract Review, to ensure that the requirements are understood, and that we have the ability to meet thoserequirements, stated and unstated, including delivery.Changes to purchase orders will be reviewed in the same manner as new orders.Documented informa on shall be retained as applicable.Control of Externally Provided Products and Services – General 8.4.1:Next Intent is responsible for the conformity of all externally supplied products and services that are incorporated intoour customer’s product, therefore we ensure that externally provided processes, products, and services conform to allrequirements. In order to manage risk, external providers are controlled in accordance with SOP-8.4.1-01 Control ofSuppliers & Sub-Contractors with regard to capability and performance.Some proprietary processes are controlled through documented informa on that is not available for public examina on.Next Intent shall verify the quality and fitness for use of products and services provided by external providers.Customer specified suppliers will be u lized whenever required, however Next Intent shall remain responsible for theconformity of the products and services delivered and shall verify the quality and fitness for use of these products andservices.Controls and product requirements shall be flowed down to external providers and to sub- er providers to assure that allrequirements are met.
Document Title:Quality Management System OverviewRevision: RDocument Number:See last page for historyQMS OverviewProcess Owner(s): QA Manager, PresidentPage 9 of 16ApprovalRevision Date:1/17/2020StampControl of Externally Provided Products and Services – Type & Extent of Control 8.4.2:Externally provided processes, products and services are controlled to prevent adverse effects upon Next Intent’s abilityto deliver product and services. Supplier performance is monitored through the quality of their products and services,and through their on- me delivery as noted in Sec on 6.2. External providers, their products and services are controlledthrough the provisions of SOP-8.4.1-01 Control of Suppliers & Sub-Contractors, the Purchase Order, including the Terms& Condi ons and the Quality Terms & Condi ons clauses and any relevant customer Quality Clauses.It is preferable to Next Intent that our suppliers be registered with third-party cer fica on bodies.Externally supplied product that is released for produc on, a er verifica on ac vi es, shall be iden fied by means ofrecording the PO number for the material or components on the traveler. Evidence of compliance with requirements ofmaterials and services from external providers shall be through cer ficates and/or test reports, as appropriate.Next Intent POs clearly state in QA 7, under Quality Terms & Condi ons, that Next Intent and its customers, customer’srepresenta ve, or regulatory agencies, all have the right of entry to the supplier’s facility and records for the purpose ofverifying compliance with the requirements of the purchase order.Verifica on of products and services delivered to Next Intent by external providers shall be through means of cer ficatesof conformance (COCs), inspec on reports, mechanical and/or chemical cer fica ons, and PCS sheets as appropriate.Delegated verifica on responsibili es are spelled out in the purchase order. Next Intent remains responsible for theconformity of externally provided products and services, therefore, delegated verifica on ac vi es are periodicallymonitored by Next Intent through a review of the cer fica ons provided by the supplier, receiving inspec on, third partyinspec on services, and/or first ar cle inspec on. Verifica on of purchased products and services shall be conductedaccording to the level of risk(s) iden fied by Next Intent. If our customer has iden fied raw material as a significant risk,Next Intent shall take appropriate ac on(s) to verify the accuracy of test data provided by the supplier.InformaƟon for External Providers 8.4.3:Purchases are made via the release of formal purchase orders and prints which clearly describe all of the requirements ofwhat is being purchased and the verifica on of same. Purchase orders are reviewed by QA for accuracy andcompleteness prior to release. The crea on and approval of purchase orders is controlled according to SOP-8.4.3-01Purchasing.Received products or services are then verified against requirements to ensure sa sfac on of requirements.Control of ProducƟon and Service Provision 8.5.1:Produc on is controlled, per SOP-8.5.1-01 Control of Equipment, Tools and So ware Programs, through the job traveler,which, together with the customer’s drawings, procedures, quality clauses, and other documents, allows for thecommunica on of all customer requirements, and special instruc ons, including acceptance and rejec on criteria.Suitable inspec on resources are available. Produc on processes are validated through first ar cle inspec on (FAI) inaccordance with SOP-8.5.1-02 Process Verifica on – First Ar cle Inspec on. The FAI shall be repeated if changes to thedesign or process invalidate the original results. Measuring ac vi es are then conducted at appropriate intervals tocontrol the process(es). Inspec on sampling shall be performed according to SOP-8.5.1-05 QA Levels & SamplingAll changes to the purchase order are reviewed by Opera ons and approved before releasing the change to produc on.When changes are made, no fica on will be made to everyone affected.Process informa on is filed on the server per SOP-8.5.1-03 Produc on Informa on Filing and available to produc onpersonnel. The completed traveler, produc on control sheets, CMM reports and other cer fica ons shall be retained asdocumenta on of the process verifica on.
Document Title:Quality Management System OverviewRevision: RDocument Number:See last page for historyQMS OverviewProcess Owner(s): QA Manager, PresidentRevision Date:1/17/2020Page 10 of 16ApprovalStampIdenƟficaƟon & Traceability 8.5.2:PreservaƟon 8.5.4:Next Intent controls the iden fica on and traceability ofall products through all stages of produc on from rawmaterial to shipping of the finished product in accordancewith SOP-8.5.2-01 Iden fica on & Traceability.Raw materials used in the produc on of finished productare kept segregated and iden fied at all mes.Product made of material from different lots (heatnumbers) will be processed on separate jobs to preservetraceability.Should a job be split, or otherwise separated from itstraveler, a copy of the traveler will be made and kept withthe orphan lot.The authority to accept product through employeestamps is granted and controlled by Quality Assurance inaccordance with WI-8.5.2-02.Cer ficates of Conformance (COCs), chemical and physicalanalysis cer fica ons (as applicable), etc. are required forall purchased materials and services and will be retainedwith the documented informa on for the job. Asrequired by the customer, these may be assembled alongwith test data from Next Intent into a COC packet anddelivered to the customer with the finished product.Product produced by Next Intent shall be protectedduring processing, storage, and shipping, from damage ordeteriora on and to maintain conformity torequirements.As applicable, preserva on includes iden fica on andtraceability, handling, packaging, storage, protec on fromthe elements, and protec on from FOD contamina on. Itmay also include cleaning, marking and labeling, specialhandling and storage, and stock rota on (FIFO).Preserva on also applies to the cons tuent parts of aproduct including raw materials, components andhardware.Product is to be packaged for shipping in accordance withWI-8.5.4-01 Packaging, Labeling and Shipping.The control and preven on of FOD contamina on isaddressed SOP-8.5.1-04 FOD Preven on, Detec on andRemoval.Customer’s or Supplier’s Property 8.5.3:Property supplied by customers (e.g. raw materialcas ngs, components, etc.) or external providers (e.g.tools, instruments, etc.) shall be iden fied, verified, andprotected while in the possession of Next Intent.Customer supplied raw materials shall be iden fied andpreserved according to SOP-8.5.3-01 Customer SuppliedMaterial.Customer supplied material that is lost, damaged orfound to be otherwise unfit for use as intended shall bereported to the customer and records retained regardingthe disposi on.Tooling, fixtures, facili es etc. belonging to a customer orexternal provider (supplier), provided to Next Intent foruse, shall be protected, preserved and safeguarded.The confiden al and proprietary informa on of ourcustomers and suppliers is preserved and protectedaccording to SOP-7.5-02 Security & Protec on ofDocuments.Release of Product 8.6:All product is inspected and validated, as appropriate tothe product and contractual obliga ons, prior to releaseand at appropriate stages in the manufacturing process.Records of the acceptance criteria and valida on aremaintained on the Traveler, FAIR, Produc on ControlSheets (PCS) and CMM reports and shall be retained asdocumented informa on.All inspec on records and other customer requireddocumenta on (COC packets) shall be available at theme of delivery of the product and shall be kept andpreserved in accordance with SOP-7.5-01 DocumentedInforma on.Signoffs and stamps on the traveler indicate the personperforming the inspec on(s).The release of product to the customer shall not proceedun l all the planned processes, meas
Quality Management System Overview Introduc on 1.1 & 1.2: Next Intent has developed a quality management system (QMS) designed to comply with the requirements of AS9100:D/ISO9001 and to document our best business prac ces, be er sa sfy the requirements and expecta ons of our customers and