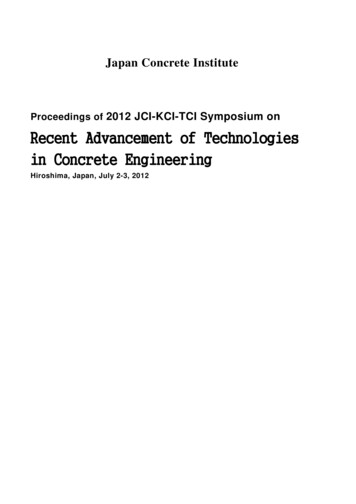
Transcription
Japan Concrete InstituteProceedings of 2012 JCI-KCI-TCI Symposium onRecent Advancement of Technologiesin Concrete EngineeringHiroshima, Japan, July 2-3, 2012
Organizing CommitteeHirozo MihashiChairman, Contact Person of JCI, Tohoku University, JapanKenro MitsuiSecretary, Takenaka Corporation, JapanTakafumi NoguchiSecretary, The University of Tokyo, JapanKoji SakaiSecretary, Kagawa University, JapanRyoichi SatoSecretary, Hiroshima University, JapanTsutomu KanazuCentral Research Institute of Electric Power Industry, JapanTetsushi KandaKajima Corporation, JapanToshiharu KishiThe University of Tokyo, JapanYasuhiro KurodaShimizu Corporation, JapanYuko OgawaHiroshima University, JapanEtsuo SakaiTokyo Institute of Technology, JapanTakumi ShimomuraNagaoka University of Technology, JapanYu-Chen OUContact Person of TCI, National Taiwan University of Science and Technology,TaiwanSoobong ShinContact Person of KCI, Inha University, KoreaSponsor:Japan Concrete Institute (JCI)Co-sponsors:Korea Concrete Institute (KCI) & Taiwan Concrete Institute (TCI)Auspices:Chugoku Electric Power Co., Inc.
Table of ContentsPrefaceControl of CrackingShrinkage Cracking Control Technology for R/C Structures byCombining SRA andExpansiveAgents in ConcreteTetsushi KANDA, Haruki MOMOSE and Fumitoshi SAKURAMOTO /JCIEvaluation of Fiber Reinforced Concrete on the Impact and Blast Resistance PerformanceGyuyong KIM, Jeongsoo NAM, Hongseop KIM and Moohan KIM /KCIResistance of Crack Opening of Highly Flowable Strain Hardening Fiber Reinforced Concrete(HF-SHFRC) under Tensile and Shear ForcesWen-Cheng LIAO (National Taiwan University) /TCIEvaluating Shrinkage Reducing Admixtures on the Early-age Cracking Behavior of CementitiousComposites Using Restrained Ring TestShih-Tang LIN, Ran HUANG and Tsai-Lung WENG /TCIShrinkage Behavior of Ultra High Performance Cementitious Composite at Early AgeSungwook KIM, Jungjun PARK and Jaeheum MOON /KCIOutline of JCI Guidelines for Control of Cracking of Mass ConcreteTsutomu KANAZU, Ryoichi SATO, Shigeyuki SOGO, Toshiharu KISHI, Takafumi NOGUCHI, ToshiakiMIZOBUCHI and Shingo MIYAZAWA /JCINew Materials and TechnologyEffects of Alkali Dosage and Curing Temperatures on Engineering Properties of Alkali-activatedSlag GeopolymerTzong-Ruey YANG, Ta-Peng CHANG, Ren-You YANG and Zih-Cian CHEN /TCIMaterial Design of Cement for Increased Waste Usage and Reduction of CO2 EmissionsEtsuo SAKAI and Eiji MARUYA /JCICrack Self-healing Concrete Introducing Semi-capsulation Effect by Granulation of IngredientsToshiharu KISHI, Tae-Ho AHN and Takao KOIDE /JCI
Applications of Synchrotron X-ray Radiation on Structural Materials Research in Nano/Micro-scaleJae-Eun OH and Paulo J. M. MONTEIRO /KCICarbon Dioxide Uptake during Concrete Life CycleYasuhiro KURODA and Toshifumi KIKUCHI /JCI“Long-term Behavior and Durability of Concrete StructuresCyclic Behavior of Reinforced Concrete Beams with Corroded Transverse ReinforcementYu-Chen OU and Hou-Heng CHEN /TCISimulation of Shrinkage Related Behavior of Concrete Structures Based on Durability MechanicsTakumi SHIMOMURA /JCIAn Analytical Study of Long-term Deformation in SRC Columns Considering Differential MoistureDistributionJin-Keun KIM and Gyeong-Hee AN /KCIRelative Humidity and Drying Shrinkage of Hardening Concrete Containing Normal- and Light-WeightCoarse Aggregates: a Comparative Experimental StudySeongcheol CHOI and Young Soo CHUNG /KCIReliability-based Design for Concrete-cover Thickness Considering the Corrosion Hazard ofReinforcing Steel Bars: Coastal Regions in TaiwanChien-Kuo CHIU and Fung-Chung TU /TCIThe Abrasion of Concrete Made of Industry By-productsWen-Chen JAU /TCI
PrefaceSince new technologies for increasing the strength and lifespan of concrete structures and for reducingproject's environmental impacts are being constantly developed, exchanging ideas and betterunderstanding of recent advancement of technologies in concrete engineering could be useful for shapingthe future of Asia we live in.In 2007, President of Korea Concrete Institute (KCI) Young-Soo Chung proposed Japan ConcreteInstitute (JCI) and Taiwan Concrete Institute (TCI) to organize Joint Symposium of these three institutesfor this purpose.The first KCI-JCI-TCI symposium was held during November 6-8, 2008 in Ilsan, Korea.symposium consisted of a one-day seminar and a technical visit.TheEighteen papers on Assessment ofExisting Concrete Structures & Recent Advancements in Concrete Technology were presented at thesymposium. The first symposium gave a form to the framework of the symposium of three institutes veryappropriately.Then the second TCI-JCI-KCI symposium was held during November 26-28, 2010 in Taipei, Taiwan.The second symposium consisted of a one-day seminar and a technical visit, too.The symposiumthemes were Sustainable Concrete Technology & New RC Structures and totally seventeen papers werepresented.The third JCI-KCI-TCI symposium on Recent Advancement of Technologies in Concrete Engineeringis held during July 1-3, 2012 in Hiroshima, Japan. As the same as the previous two symposiums, aone-day seminar and a technical visit are organized. Seventeen papers are presented on Control ofCracking, New Materials and Technology & Long-term Behavior and Durability of Concrete Structures.As usual, the organizers of symposiums were responsible for pointing out the main themes andconcrete related problems on which we should work and debate.These themes and research directionsusually change in time. Accordingly I am sure that future research cooperation of the three institutes willhave helpful and useful effects on further development of concrete technology. Furthermore it is expectedthat outcomes of the joint symposiums could contribute to stimulate the activities of Asian ConcreteFederation (ACF).Finally, I would like to express my sincere thanks to the great support of the Japan Concrete Institute,the Korea Concrete Institute, and the Taiwan Concrete Institute, which made this joint symposiumpossible. In addition, I also wish to acknowledge the auspices of the Chugoku Electric Power Co., Inc. aswell as all of members of the Organizing Committee and, in particular, the authors for their excellentcontributions.July 1 st , 2012Hirozo MihashiChairman of the Organizing Committee
rdProceedings of the 3 JCI-KCI-TCI Symposium onRecent Advancement of Technologies inConcrete EngineeringJapan Concrete Institute, July 2012Shrinkage cracking control technology for R/C structures by combiningSRA and expansive agents in concreteTetsushi. Kanda, Haruki. Momose and Fumitoshi. SakuramotoKajima Technical Research Institute, Chofu-shi, JapanABSTRACTMix proportions and building application of Crack Reducing Concrete, CRC,using expansive agent and shrinkage reducing agent, were studied for a crackrestriction measure of floor slab construction. Basic properties such ascompressive strength and fresh behavior of CRC were clarified and mixproportions applicable to real constructions were determined. Stability of freshconcrete based on the mix design was confirmed through constructions and strainbehavior of the hardened structure was monitored. It was shown that the CRC hasexcellent construction executability, and higher crack reducing capability thanks tothe introduction of chemical prestressing and subsequent development ofshrinkage reducing effects.Keywords:1 INTRODUCTIONGrowing interest in durability of buildingstructures has marked the crack controllingtechnology that plays significant role on thedurability of concrete structures. Crackingmechanisms have been quantitatively studied on thebasis of the largely accumulated research results andsome countermeasures have been proposed from theviewpoints of material science, constructiontechnology and structural engineering (AIJ 2003).However, very few technologies were proven to beeffective in a quantitative manner and used as acrack control design method.For the establishment of crack controlling designmethod in the future, a notable technology withconsiderable impact and quantitative measure is theCrack Reducing Concrete (CRC) characterized by acombined use of expansive agent and shrinkagereducing agent (SRA) (Tomita 1994, Kanda et al.2004). It has been reported that the synergetic effectof combining expansive agent and SRA is notableand it is possible to produce a concrete with very lowshrinkage, which is effective in reducing shrinkageat real structures (Tomita et al. 1986).However, CRC application in construction sitesinvolves several unknown factors such as mix designprocedure, manufacture and placement know-howand influences on the cracking mechanism ofstructures. This paper deals with these problemsquantitatively executing experiments on mix design,construction and strain behavior of real structuresand reports the practicability and shrinkage reducingeffects of CRC.2 SELECTION OF SRA MATERIALS2.1 Overview of SRA Material SelectionExperiment(1) Experimental parametersThe targeted structure was a 4-story car parkingtower with steel frames and R/C slabs. CRC wasapplied to its floor to examine crack controllability.Mix design experiment was formulated to determinethe type of SRA with parameters shown in Table 1.This study is necessary because the effect of SRA onfresh properties such as air content is significant(Tomita 1988) while the range of air content atdischarge in this construction was specified within4.5% plus or minus 1.5% pursuant to JapaneseArchitectural Standard Specification 5 ofArchitectural Institute of Japan. The fresh concretetemperature included 30 C in addition to 20 Ctaking into account temperatures of the season of theconstruction.(2) Materials used and mix proportionsFour types of SRA, all of them were alcohol typeand major in the market, were tested as shown inTable 1. Products B and C were the modifiedversions of product A for a better air entrainingcapability, while product D was by anothermanufacturer. The other materials were common to1
2.2 Results of the SRA material selectionexperimentFresh properties of all the mixes are shown inTable 4. Dosage of superplasticizer was notsignificantly different according to the type of SRAand fresh concrete temperatures while that of AEagent differs considerably to assure the targeted aircontents. A larger amount of AE agent was requiredfor Mix-A compared to other cases using differenttypes of SRA and air entraining was impossible at30 C.all the experiments: ordinary portland cement, a lowdosage lime-CSA type expansive agent, AE agentpursuant to JIS A 6204 and a superplasticizer of typeI polycarbonic acid type were used. Mix proportionsare listed in Table 2 where a part of unit watercontent was substituted with SRA. Water-binderratio of 0.45 and unit water content of 170 kg/m3were common to all the mixes and the expansiveagent of 20 kg/m3 was admixed as a part of binder.The AE agent and the superplasticizer were preparedto have an air content of 4.5% and slump of 18 cmrespectively.70FactorLevelParameterSRA type5Fresh concretetemperature2SRA 4 types andcontrol20 C, 30 CReduction rate (%)Table 1 Items for material selection60Slump loss rate(%)Air content loss rate(%)50Fresh temp. 30oC403020100Mix-N Mix-A Mix-B Mix-C Mix-DMixTable 2 Mix proportions for material selectionSRAtypeFigure 1 Changes in fresh properties with time2WaterFineUnitExpansive SRAbinderaggr.(%) *2wateragentratiocontent (kg/m3) 4517045205Mix-C4517045205Mix-D4517045205*1 Inclusive mix, *2 Included in the unit water contentCompressive strength(N/mm )MixABCDTable 3 Test itemsFreshpropertyJIS A 1128,1101PurposeChanges in aircontentandslumpCompressiveJIS A 1108Possiblestrengthreduction by thetype of SRARestrainedJIS A 6202 *1Initial expansionstrainanddryingshrinkageSpacing factor ASTM C 457Confirmfrostresistance*1 A 7-day sealed curing after mixing before drying(3) Test itemsTest items for SRA selection may be chosen areshown in Table 3. Changes in air content and slumpin the fresh state and compressive strengthdecreasing due to SRA addition were particularlyfocused on. Volume changes of hardened specimenswere compared using the standard restrain test(method B in JIS A 6202). Air void spacing factorwas measured with the linear traverse method forfear of coarsening of entrained air voids due to 234Material age (week)5Figure 2 Compressive strength by the type of SRA-4MethodExpansion-shrinkage strain (x10 )Test 0Material age (day)200Figure 3 Volume change behavior by the type ofSRASlump losses and changes in air content frommixing to an age of 60 min. are shown as adecreasing rate in Figure 1. The fresh property testsat the age of 60 min. were performed with remixingof the concrete that was left without external effectsafter the first test at mixing. This generally led to alarge slump loss but effect of SRA addition wassmall compared with the control specimen (Mix-N).2
Table 4 Fresh properties in material selectionFresh concrete temperature 20 CFresh concret temperature 30 CMixMix-NMix-AMix-BMix-CMix-D*1)Super- *2)AEAge (min)plasticizer agent 103060*1 weight ratio to binderSlump (cm) Air content Fresh(%)concretetemp. ( 721.6Spacing factor( m)300Slump (cm) Air content Fresh(%)concretetemp. ( .52.031.822.031.817.53.031.662.231.831.931.5*2 unit: 1A 0.003% of binder weightIn spite of this tendency, decreasing rate of aircontent was small in the control specimen andsignificant in SRA added specimens depending onthe type of SRA. Among SRA added mixes, aircontent was most stable in Mix-C. Changes incompressive strength with age, at a fresh concretetemperature of 20 C, are shown in Figure 2 wherethe addition of SRA leads to the compressivestrength reduction at most 10% without regard to thetype of SRA.Restrained strain test results are shown in Figure3, where the initial expansion of SRA addedspecimen was twice as large as that of the controlspecimen and the drying shrinkage of SRA addedspecimen was 40% as small as that of the controlspecimen. The reduction of drying shrinkage at anSRA dosage of 5 kg/m3 was approximately 30%according to a literature (Tomita 1988) wherebysynergetic effect with expansive agent is significant.350*1)Super- *2)AEAge (min)plasticizer agent 5103060o20 CFigure 5 Floor plan of the test building and strainmeasurement pointsResults of spacing factor measurement are shownin Figure 4. At a fresh concrete temperature of 20 C,each case except for Mix-N and Mix-D satisfies aspacing factor of 250 m or less that is preferable fora better frost resistance (Kasai 1995), while Mix-Dstill shows a spacing factor of approximately 300 mthat is slightly greater than 250 m and almost equalto that of the control specimen (Mix-N). The effectof SRA addition on the coarsening of entrained airvoid may be small as a whole.The above results imply that the product A within appropriate air entrainment may cause problemsduring construction at high temperatures in thesummer. No particular difference in properties wasfound between other SRA added specimens butoverall estimation resulted in the use of product C inthe construction experiment.o30 C3 CONSTRUCTION EXPERIMENTS2503.1 Execution plan200150100500Mix-N Mix-A Mix-B Mix-C Mix-DMixFigure 4 Spacing factor by the type of SRA(1) Concrete construction planThe plan view of the applied car-parking tower isshown in Figure 5. CRC was used for floor slabsfrom the second to fourth floor for 960 m2 per floor.Placement for each floor was performed every threedays using concrete pump for a necessary amount of140 m3 per floor. Floor surface was finished directlywith a trowel for three times and was subsequentlywet-cured with water spraying intensively. Slabthickness was 140 mm with a doubled reinforcingbar of D10@200 and designed as a one-way slab forthe span direction using flat deck plate.(2) Mix proportion of concrete and production planThe CRC used for the construction was designedto have a slump of 18cm and specified compressive3
12Control range (18 2.5cm)10At dischargeAfter mixing8642017 17.5 18 18.5 19 19.5 20 20.5Slump (cm)Figure 7 Variation of slump14At dischargeAfter mixing12Control range(4.5 1.5%)10Frequency(3) Measurement planStrain behavior of structural concrete wasmeasured at a unit area of the 3rd floor slab. Acontrol steel bar with a strain gauge was embeddedthree points of the floor slab and strains of threedirections were traced continuously and subjected toa rosette analysis. In this study, all-in-one behaviorof the control steel bars and concrete was assumed,hence the thermal strain can be separated bymeasuring the concrete temperatures (Momose et al.2003).As shown in Figure 6, slab specimens were preparedas an internally restrained model where concrete wasplaced at the same time as that of the floor concreteand strain behavior responsible solely by the internalrestraint was monitored. In addition, slightlyrestrained specimen with a reinforcement ratio of0.1%, capable of stabilizing expansion and ofrepresenting free volume changes, was subjected tostrain measurement. Stability of properties wasconfirmed through the execution of fresh propertytests and specimen sampling for compressivestrength test.Concrete placement was performed in a threedays at the beginning of September when 28agitating trucks per day successfully completed theplacement for the floor of one story. Compaction andtroweling of slab surface were executed in the sameway as in the normal concrete though the CRCtemperatures at discharge exceeded 30 C.Results of the fresh property test, variations ofslump and air content, for every 4 trucks are shownin Figures 7 and 8. Variations at discharge aredistributed within the control limit of 18 2.5cm and4.5 1.5%. Both slump and air content values aftermixing were set higher taking into accountsubsequent transportation time of 30 minutes. Itappears that variation of air content, which was theprimary concern, was fully controlled thanks to thefrequent fresh property tests and resulting finedosage control of AE agent and anti-foaming agent.Compressive strength of specimen, cured in water onsite and performed at an independent organization,was greater than approximately 35 N/mm2 and easilysatisfied the spcified value of 27 N/mm2.Frequencystrength of 27N/mm2 and the mix proportion wasdetermined after a trial mixing as shown in Table 5.The original mix proportion of the manufacturingplant capable of satisfying the specification is alsoshown but the water-binder ratio was reduced from0.58 to 0.54 taking into account possible decrease incompressive strength and scatter of air content. Inaddition to AE agent, anti-foaming agent was used torestrict entrapped air during transportation. The antifoaming agent was a polyoxialkylene type and dosed0.0025% of the binder mass.During manufacturing of CRC, the expansive agentwas introduced from the storage tank on the groundby a dedicated pump and SRA was introduced to thewater-measuring tank by hand. Mixing time wasextended from standard 30 seconds to 45.864202.533.5 4 4.5 5Air content(%)5.5Figure 8 Variation of air contentFig.6 Model specimen (internally restrained)Table 5 Mix proportion of concrete for constructionMixOriginalCRCWaterbinderratio (%)5854Unitwater(kg/m3)180180Fine aggr.Content(%)4746Expansiveagent(kg/m3)203.2 Results of the construction testSRA(kg/m3)5Superplasticizer(l/m3)0.781.083.3 Results of strain measurementNo cracking was found in the concrete slabs of960 m2 at each floor until the age of four monthsthough concrete of each floor slab was placed at onetime without any crack-inducing grooves.Strain behavior was examined with total strain andnet strain: the total strain is considered to representthe real concrete behavior after compensating the4
Principal strain of structure ( )150100500-50ThermalstrainN1 (Net strain)N2 (Net strain)N3 (Net strain)N1 (Total strain)N2 (Total strain)N3 (Total strain)-100-150-200010 20 30 40 50 60 70 80Effective material age (day)Figure 9 Changes in strain of the structureMaximum principal net strain ( )400200350300Slightly restrainedspecimen250Elastic comp. strain200 creep strainInternally restrained150specimen1005000Concreteof the structure (N2)10 20 30 40 50 60 70 80Effective material age (day)Figure 10 Effect of restraint on straintemperature dependency of strain gauge and the netstrain is a result of eliminating thermal strain fromthe total strain.Thermal strain was calculated on the basis of alinear expansion coefficient of 10.3x10-6/degwhich was obtained as a least-square linearregression of incremental strains associated withtemperature changes of every 6 hours in the slightlyrestrained specimens. The linear expansioncoefficient involves some effects of material age andwater content because data acquisition wasperformed at an age form 11 to 91days whenhydration reactions of cement and expansive agentwere supposed to become stable.Strain behavior of floor concrete is shown in Figure9. Effective material age according to CEB-FIP90and maximum principal strain are represented in thehorizontal and vertical axes. Both in the total and thenet strain, the maximum principal strain behavedsimilarly at points N1, N2 and N3 and difference bymeasuring point was small, though the measurementat the point N1 became impossible after 32 days bysome errors. Approximately 100 of the initialexpansion strain remained until the age of 75 days inthe net strain while the total strain showed anexpansion of 100 to 150 at early ages andsubsequent shrinkage of 200 at the age of 75 days.The difference can be attributed to a fluctuation inthe concrete floor temperature of approximately 20degree between that at the placement and that at theage of 75 days.Difference in strain behavior with the differencein degree of restraint is shown in Figure 10 wherethe strains of the internally restrained specimen andthe floor concrete were 100 and 300 smaller thanthat of the slightly restrained specimens. The strainshown in this figure are the net strain and showingthat drying proceeds slower than that in Figure 3because surface area is relatively small compared toits volume.The principal strains of the concrete floor andtheir directions are shown in Figure 11. Maximumstrain ranged from 80 to 150 and minimum strainranged from 25 to 80 showing the small differenceFigure 11 Strain distributionin strain between the maximum and the minimum.4 DISCUSSIONThe restrained stress c predominant to concretecracking is briefly discussed in this section while theestimationmethodinvolvesconsiderableassumptions and the result should not be decisive.However, taking into account the lack in such astudy dealing with the restrained stress of full-scalefloor elements, this discussion could be of somecontributions to this field.In this discussion, strain of the restrained body isestimated from the net strain of the floor slab andusing the balance of forces c is calculated. Unlikebuilding walls that is restrained by the footing beams,the floor slabs of the targeted building could exhibita thermal behavior in conjunction with the restraintssuch as internal reinforcing steel and steel beamsunder the same ambient temperatures. In addition,the difference in linear expansion coefficient of thefloor slab and the restraints is so small that thethermal stress in the restrained concrete floor is ofminor concern. Hence the net strain can be used forthe estimation of c.For simplicity, the floor slab is treated as auniaxial member. The balance of forces betweenconcrete and the restraints is given by equation (1) c A c d Ed Ad s Es As r Er A r 0(1)where : restrained stress, : elastic strain, E:Young’s modulus, A: sectional area and subscripts c,d, s and r denote concrete, deck plate, steel beam andreinforcing bar respectively. Strains d, s and rshould be known to obtain c using equation (1).These strains were not measured in this study but canbe substituted with a strain of concrete floor at thelongitudinal direction of N1 and N3 points that areclose to a steel beam, and strains d, s and r areassumed to be equal. It was reported that straindistribution of the two dimensional member can besimplified as a one dimensional member withoutsignificant errors (Imamoto 2003). The input values5
and the result of this estimation are shown in Tables6 and 7. When strains at N2 and N3 are averaged,it was estimated that a compressive stress of c 0.84N/mm2 was created at the maximumexpansion as a chemical prestressing and it remainedfor 0.49N/mm2 at the age of 75 days. This shows astress relaxation of approximately -0.3N/mm2 wastaken place due to drying shrinkage.Table 6 Numerical data for stress estimationDimensionsCrosssectionalarea (mm2)Concrete7600x140mm1058034Deck teel usofsteelItemTable 7 Estimation of restrained stress of concreteTime/PointAtmaximumexpansionAt 75-dayInput valuePointN2N3MeanN2N3MeanStrain s and r( )110104107655862Estimated valueStress c(N/mm2)0.870.820.840.510.460.49This compressive stress, even under subsequentdrying shrinkage strain development, can beexpected to contribute to a long-term crackingcontrol. When applying JSCE formula to thisbuilding condition, the shrinkage strain is estimatedto have developed 70% of the ultimate dryingshrinkage strain. If we assume that the dryingshrinkage of floor concrete develops more than halfof the ultimate value, the compressive stress due tochemical prestressing will be nearly cancelled in along term. If otherwise assumed that the crackingstrength is a 70% of the splitting strength (AIJ 2003),at least a tensile stress of 1.5N/mm2 remains at thetension side as a margin and the risk of cracking inthe floor slab is supposed to be small. Floor slabsrestrained both steel beams and deck plate arenormally inescapable from cracking while use ofCRC resulted in a successful cracking control.5 CONCLUSIONSPractical solutions necessary for the constructionof Crack Reducing Concrete have been studiedthrough the experiments of mix design, trialconstruction and strain behavior of a real structure.Major findings are as follows.(1) Stable air entraining was performed duringconstruction thanks to the selection of lower alcoholtype shrinkage reducing agent leading to asatisfactory construction results.(2) No cracking was found in the concrete slabs of960 m2 at each floor until the age of four monthsthough the concrete of each floor slab was placedwithout any crack-inducing grooves.(3) Risk of long-term cracking of the structure issupposed to be low thanks to an introduced chemicalprestressing of 0.8N/mm2 estimated with anapproximate calculation.ACKNOWLEDGEMENTAuthors express their sincere thanks to thoseinvolved in this study at Denki Kagaku Kogyo ltd.and Asahi Denka Kogyo ltd. for their generouscooperation.REFERENCES[1] AIJ. 2003. Shrinkage cracking of concretestructures – Mechanisms and state-of-the-Art oftechnical measures. Tokyo: ArchitecturalInstitute of Japan.[2] Imamoto, K. 2003. Shrinkage behavior ofvarious types of concrete walls. Journal ofStructural and Construction Engineering(Japan). 568: 15-20.[3] JSCE. 2002. Standard specifications for designand construction of concrete structures –Verification for structural performance. Chapter3, Japan Society of Civil Engineers: 30-34.[4] Kanda, T., et al. 2004. Experimentalinvestigation of anti-cracking effects in concreteslab applying Expansive agent and shrinkagereducing agent, JCI annual proceedings (Japan).26(1): 501-506.[5] Kasai, Y. 1995. The Concrete. Tokyo: GijyutsuShoin.[6] Momose, H. et al. Shrinkage behavior of real RCstructure using low-heat portland cement andexpansive agent. JCI Symposium on HighPerformance Structures using ExpansiveConcrete, 2003. Tokyo: Japan Concrete Institute:21-26.[7] Tomita, R. 1986. Shrinkage reducing effect ofsome chemical admixtures on RC buildingstructures. Concrete Engineering (Japan). 24(5):14-21.[8] Tomita, R. 1988. Shrinkage reducing agent.Concrete Engineering (Japan). 26(3): 55-60.[9] Tomita, R. 1994. Super low shrinkage concrete.Concrete Engineering (Japan). 32(7): 105-109.6
Proceedings of the 3rd JCI-KCI-TCI Symposium onRecent Advancement of Technologies inConcrete EngineeringJapan Concrete Institute, July 2012EVALUATION OF FIBER REINFORCED CONCRETE ON THEIMPACT AND BLAST RESISTANCE PERFORMANCEGyuyong Kim, Jeongsoo Nam, Hongseop Kim and Moohan KimDepartment of Architectural Engineering, Chungnam National University, KoreaABSTRACTRecently, projectiles or fragments generate localized effect characterized bypenetration or perforation, spall scabbing, as well as more widespread crackpropagation. The military and related research institutes began work on the projectto reduce the blast damage. Therefore, in this study, we present results from anexperimental study on the impact and blast resistance of fiber reinforced concretewith fiber types by high velocity steel projectile test and emulsion explosiveexplosion test. In the present work, the effectiveness of fiber reinforcement on theimpact and blast resistance performance of concrete specimen has beeninvestigated. Tensile and bending strengths of fiber reinforced concrete specimenswere higher than of plain specimens, and the fiber reinforced concrete decrease inrear side spall was also higher. Fiber reinforced concrete has higher impact andblast resistance than plain specimen.Keywords: impact resistance, blast resistance, fiber reinforcement, shock damage,fractur
In 2007, President of Korea Concrete Institute (KCI) Young-Soo Chung proposed Japan Concrete Institute (JCI) and Taiwan Concrete Institute (TCI) to organize Joint Symposium of these three institutes for this purpose. The first KCI-JCI-TCI symposium was held during November 6-8, 2008 in Ilsan, Korea. The