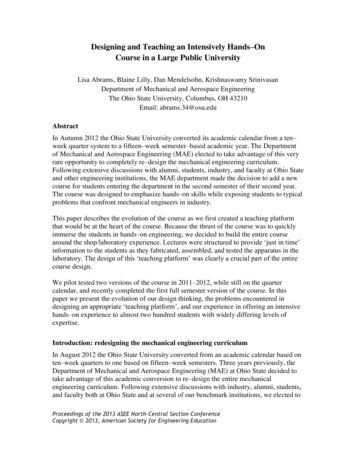
Transcription
Proceedings of the International Conference on Industrial Engineering and Operations ManagementBogota, Colombia, October 25-26, 2017Bottleneck Identification Using Time Study and SimulationModeling of Apparel Industries(Case Study on MAA Garment)Aregawi yemane1Bahir Dar institute of technology, industrial engineering, Bahir Dar, EthiopiaAregawi yemane@yahoo.comSerajul haque2Bahir Dar institute of technology, industrial engineering, Bahir Dar, Ethiopiaserajull@gmail.comIván Santelices Malfanti3Universidad delBío-Bío, DepartamentoIngeniería Industrial, Concepción, Chileisanteli@ubiobio.clAbstractThis study deals with bottleneck detection with simulation techniques and time study. Modeling andsimulation are potential tools for analyzing assembly lines such as clothing in a garment. Thus, theresearchers attempted to experiment 160 numbers of replication in the arena tool.The experiment monitors the assembly process resources without altering the actual production scheme. Inthis study, the arena software and POM dedicated to modeling and measuring the performance of the existingRonny t-shirt sewing line. The t-shirt is formed and has 12 main parts are assembled.For each activity, the researchers took 15 sampling observations using stopwatch. All the collected data arestatistically analyzed using the input analyzer in arena for statistical significance and the expressionresolution to be used for the simulation model. This simulation model has considered production resourceslike four threads over lock machines, single needle, two flat lock needles, machine operators, qualitycheckers, trimmer, batch arrival time Inter lot of pieces, sequence pieces, testing Different scenarios.Keywords: - clothing, bottle neck, study time, t-shirt, simulation models IEOM society international321
Proceedings of the International Conference on Industrial Engineering and Operations ManagementBogota, Colombia, October 25-26, 2017production line [5]. In the production of clothing,INTRODUCTIONresponsible would have been able to check whether theEthiopian clothing industries face many problems that haveassembly work will be completed in time for delivery, hownot become competitive globally. These problems include;machines and man or operators are used, if any station onthe poor performance of products in the export market,the line assembly line is late it is global. To achieve thispoor quality and inadequate supply of raw materials, lowapproach, the study of working time is the duration for eachproductivity and poor resource utilization. Because ofpart to be mounted on production lines [5] and [2]those, most of the country's textile companies are notactivities. The assembly lines are generating productionlucrative and most are in great loss [1]. Bottlenecks in thesystems to meet the humanity needs that have been growingproduction regime involve long queues, long waiting times,day by day. The goals of these systems produce productspoor performance and overall inefficiency of the system.that have high production rates in the shortest time, in aSuch a system should work under capacity. To maximizemore productive, economical and quality manner. Theresource capacity and the efficiency level of operations it ispurpose of the case study was to design the assembly chaindesirable to have appropriately programmed workstationsto achieve maximum line efficiency using the optimumand disposition in available space structures, with anmachine working time for constant cycle time [6]. Lineoptimal allocation of available resources. Work- time study,Balancing is commonly used to solve problems that havebalancing the assembly line and simulation can be appliedoccurred in the assembly line. Line balancing is a techniqueto the production line to find alternative solutions toto minimize the distance between workers and workload inincrease sewing line efficiency. A good layout design couldorder to achieve the desired flow rate [7]. This can be doneincrease the productivity by correctly balancing theby equating the amount of work at each station andassembly line [2]. Some researchers said, the simulationassigning the least number of workers to the particularmodel is used to identify bottlenecks in the production lineworkstation. A line balancing can be classified into threeand evaluate a number of suggested solutions using thecategories according to the numbers Mounted on the linearena software [3]. In addition to that the productivity ofand in accordance with the rhythm of line [8] and [7] arethe company will be improved while the company diffusesmodels;the appropriate time study of the products to be mounted onSingle line Model: - can be described as a line thatthe production line, the minimum queue length on thecombines a single model. This line produces many units ofmachines, the minimum production cost and high-qualityan unchanged product. The tasks performed at each stationproducts to establish an improved clothing industryare the same for all units. Products with strong demand areIncrease the productivity of the specific model.destined for this line [9].Work-time study, Assembly line balancing can be appliedMixed model line: - Mixed model line is producing moreto apparel or clothing production line to find alternativethan one model. They are made simultaneously on the samesolutions to increase the efficiency of the sewing line of theline. Once a model is running at a station, other productsgarment section. In this paper, they try to show how a goodare made in other seasons. Therefore, each station islayout can be designed and productivity can be increasedequipped to perform various operations necessary toby appropriate assembly line balancing (Mominul, et al.,produce any model that moves through it. Many consumer2014). Some of the optimization layout design studies fromproducts are assembled in Mixed Model [3].balancing lines using simulation models and differentBatchline: - This line produces every batch model.approaches will be studied in this type of problemTypically,the workstations are set to produce the requireddiscussed in the literature. The line balancing is thequantityofthe first model then stations are rebuilt toassignment process of tasks or workstations so that theproduceanothermodel. The products are often assembledworkstations have roughly the same time requirements.inbatchesrequiredwhen the average. It is cheaper to use aThis results in minimizing stop times along the line andmountingchaintoproducevarious batch products to buildhigh use of labor and equipment and minimizing the cycleaseparatelineforeachmodel.The research will take placetime of the production line.inthefieldappliedamixedmodelline. Simulation is oneCycle time is the maximum time allowed for eachofthetoolsthathavebeenwidelyusedin various sectorsworkstation in the production of clothing items, clothingandmanufacturingorganizations.Usingavalid simulationcomponents or parts are collected in a finished outputmodelgivesnumerousbenefitsandbenefitsin creatingwhich is the final product of the subassembly process. Andbettermanufacturinginordertoimprovesystemthe process has a different number of oidentifyoperators, and installation components. Therefore, a goodbottlenecks in the production line and evaluate a fewbalance line increases the efficiency of the sewing section IEOM society international322
Proceedings of the International Conference on Industrial Engineering and Operations ManagementBogota, Colombia, October 25-26, 2017proposed solutions [9]. Systems simulation modelingachievedinashortperiodoftime.objectives are producing products that have high productionrates in the shortest time in a more productive, economicaland agreed manner. An assembly line garment was selectedand simulated using Arena simulation and statisticalmethods to solve the balanced problem [6] have been used.Most Ethiopian textile factories could have been low inproductivity and therefore less competitive in the worldmarket due to delays in delivering products to customers.The major problems facing businesses are not optimallayout design; less resource utilization is used for differentproducts, inappropriate line balancing. Therefore, becauseof those problems the company has failed to meet its dailyFigure 1: sewing lineplan. In this case, the actual production of the sewingThe objectives of the studysection is about 550-680 t-shirt per day with an average ofto identify the bottlenecks of the garment line using650 t-shirt its lane is 900 t-shirts per day. Overall, there is atime study and simulation analyses of the apparelvariation between its plan and target. The issues faced inindustry.the case of study are; improper assembly balance andTo develop a simulation model of the sewing sectioninsufficient time standard for each product of the companyof the apparel industry.generally did not use an optimal resource to achieve itsTo assess performance of the existing sewing line.goal. This study demonstrates that enough time is needed toTo estimate the standard time of the products.balance line patterns and model development to increaseTo analyze the causes and effects of the productionline efficiency. In the ronny t-shirt manufacturing modelareas of the sewing section for not meeting their goal.there is a high WIP in some operations such as shoulderMETHODOLOGYattach, sleeve attach and back top stitch and zero waitingThis study needs a lot of data like man power, machinetime provided in some operations such as quality checkers,capacity, sequence of jobs, inter arrival of parts fortrimming and sleeve hemming in those operations theassembling, processing time at each machine, efficiency,resources that assigned have below 50% utilization.quality product outputs (number of defects, rework,MAA Garment and textile Factory (Kebire enterprise) is anormal) such data are used for model the production line.private company formed and registered in April 2001Therefore; the researchers had used primary data andaccording to the Federal Commercial Democratic Law ofsecondary data (documented data), and the researchers usedEthiopia. MAA Garment Factory started its business instop watch for recording some necessary information likeJune 2004 in the northern part of Ethiopia, Tigray, Mekelleprocessing time for new products transfer time from onewholly owned kebire Enterprises plc. It is the diamond tipstation to the next one. The researchers had tried to find thein combination with expatriates in Turkey, Pakistan and thecauses why the company did not achieve its goals is due toPhilippines, with the production of fully-equipped set-upsdifferent material shortage like the inputs for differentwith the most reputable machines and equipment fromsections, cotton, yarn, fabric cloth or improper linerenowned manufacturers in the world such as Juki, Myers,balancing. So, this can be solved due to approaches likeand Cie, local dynamic locals. MAA Garments is emergingproper line balancing, time study and simulationas one of the leading clothing manufacturers not only inapproaches.Ethiopia but also in the rest of the world. The company'srecognition has reached its peak since its inception andSimulation methodology has eight phases (onur, et al.,revealed energy-producing goods in the clothing industry.2002).The incorporation of methods and solutions for theStep 1: Define the Problem Which Study and Whyproduction system allowed faster mixing in theBusiness Reason?international market, and although the main objective wasStep 2: design the model that study (s) that will provideto export garments internationally, the company has beenanswerstowho?committed to meeting the needs of the market national. ItStep 3: Designing the Conceptual Model Which strategyintends to incorporate and improve infrastructures, whilemodel (continuous, discrete, mixed) will be used and atmaintaining concern with environmental and socialwhat level of detail?responsibilities, so that the company's ultimate goals are IEOM society international323
Proceedings of the International Conference on Industrial Engineering and Operations ManagementBogota, Colombia, October 25-26, 2017Step 4: Formulate inputs, hypothesis, and process definitionwhich study hypothesis is based on and what productionfactors and process definition will guide the model?Step 5: Build, verify, and validate the model is the modelproperly built (check)? Is the correct model built(validation)?Step 6: Experimenting with the ModelWhat Do Think of Modeling?Step 7: Document and Present the Precious ExperienceResults What is the Basis for Future Work?Step 8: Define the Lifecycle Model Can the model providelong-term benefits, throughout or throughout training,Figure 2: root cause analysisprogramming, system redesign, and system launch?DATA COLLECTION AND ANALYSISThe standard methodology used for this thesis is a generallyaccepted computer simulation model. A garment (sewingsection) assembly plant producing a ronny t-shirt style witha total number of parts namely; shoulder attach, rib tacking,neck rib attaches, piping tack, piping attach, sleeve attach,back top stitch, bottom hemming, trimming, qualitychecking to be assembled in the production process line ofsewing section was selected for the model.Activity identification in the sewing section, processmapping how to understand how the product (entities)using built in area input analyzer, simulation modeldevelopment and identification of replication numbers withthe methodologies used.A total number of 12 activities were identified for a ronnymodel t-shirt production assembly line. Since, the modelinput based on the literature review and the actualperformance of the production lines the following variableswhich used in the measuring of efficiency and effectivenessof the garment process is collecting.ROOT CAUSE OF THE VARIATION INACTUAL OUTPUT AND TARGET OR PLANOUTPUTThe researchers have taken a discussion with theproduction managers o
proper line balancing, time study and simulation approaches. Simulation methodology has eight phases (onur, et al., 2002). Step 1: Define the Problem Which Study and Why Business Reason? Step 2: design the model that study (s) that will provide answers to who? Step 3: